- お役立ち記事
- A must-see for quality assurance department managers! Effective practices for quality improvement and cost reduction using Six Sigma
月間76,176名の
製造業ご担当者様が閲覧しています*
*2025年3月31日現在のGoogle Analyticsのデータより
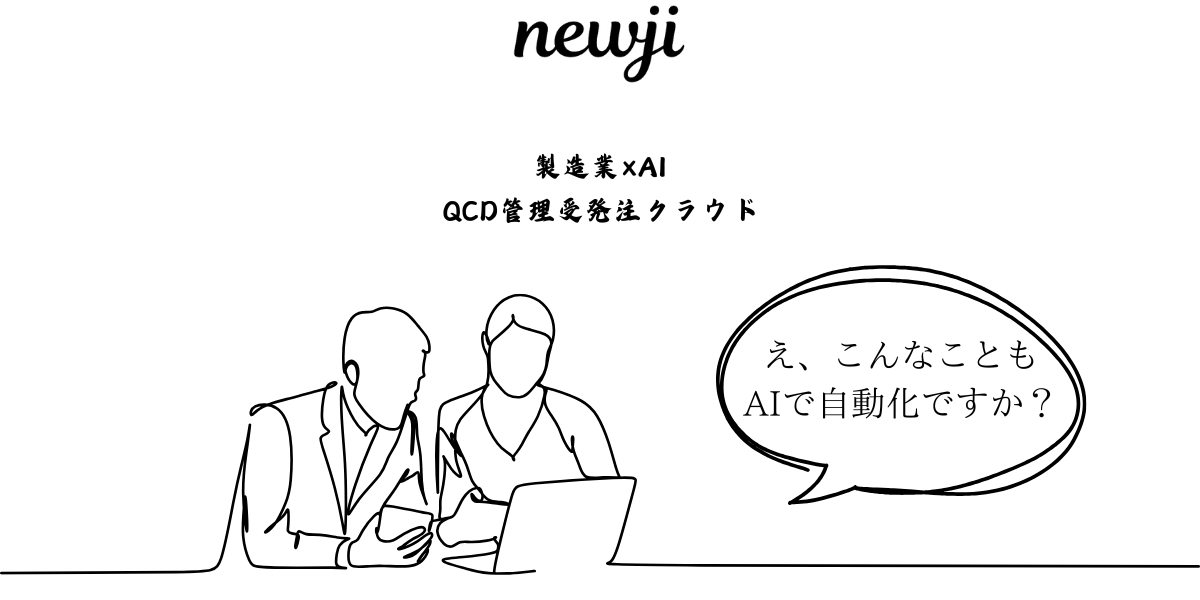
A must-see for quality assurance department managers! Effective practices for quality improvement and cost reduction using Six Sigma
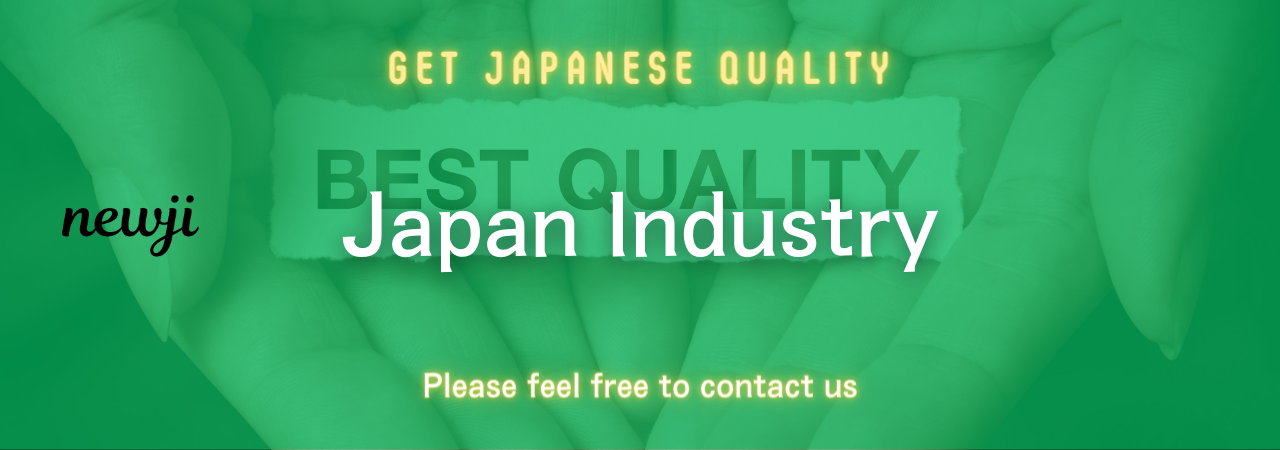
目次
Understanding Six Sigma
Six Sigma is a set of techniques and tools used for process improvement, developed by Motorola in 1986.
It aims to improve the quality of output by identifying and removing the causes of defects and minimizing variability in manufacturing and business processes.
The methodology focuses on improving process quality and efficiency, reducing costs, and enhancing customer satisfaction.
Six Sigma applies a data-driven approach and relies on statistical analysis to make informed decisions.
It is named after a statistical concept, where sigma (σ) represents a standard deviation.
In a Six Sigma process, variations are managed so tightly that no more than 3.4 defects occur per million opportunities.
The Principles of Six Sigma
Six Sigma is built on five key principles, often abbreviated as DMAIC (Define, Measure, Analyze, Improve, and Control).
1. **Define**: Clearly define the problem and set improvement goals.
This stage is about understanding what needs to be improved and setting objectives to meet those requirements.
2. **Measure**: Collect data and establish baselines to identify the current performance of the process.
This involves measuring the critical outputs and inputs.
3. **Analyze**: Analyze the data to identify root causes of defects and areas of improvement.
The focus is on understanding the relationship between variables and finding areas where changes can lead to significant improvements.
4. **Improve**: Implement solutions to eliminate defects and enhance process performance.
Once improvements are identified, they are tested, and changes are applied to see practical outcomes.
5. **Control**: Monitor the processes to ensure that improvements are sustained and establish controls to prevent recurrence of defects.
This final step ensures that gains are maintained over time, and adjustments can be made if issues arise.
Quality Improvement through Six Sigma
Implementing Six Sigma can significantly enhance the quality of a company’s products and services.
By employing this methodology, organizations can minimize errors and defects, which leads to higher customer satisfaction.
Reducing Errors
With Six Sigma, the focus is placed on reducing variation and getting processes under control.
This minimizes errors and defects, ensuring that products or services meet set standards consistently.
When errors are minimized, the cost associated with rework, waste, and customer complaints decreases.
Enhancing Process Efficiency
Six Sigma improves the efficiency of processes by identifying and eliminating wasteful practices.
Streamlining operations leads to faster turnaround times and increased productivity, crucial factors in maintaining competitive advantage.
Cost Reduction with Six Sigma
In addition to quality improvement, Six Sigma offers effective strategies for cost reduction.
By focusing on systematic data analysis and reducing defects, an organization can save money and optimize resources.
Optimizing Resource Use
Waste reduction is a core principle of Six Sigma.
By implementing changes based on analysis, companies use their materials, labor, and time more effectively.
This optimization ensures resources are spent only on value-adding activities.
Decrease in Operational Costs
As errors and defects are minimized, there is a reduction in the costs related to repairs, returns, and warranty claims.
By ensuring high-quality output from the beginning, companies spend less on rectifying issues.
Practical Implementation of Six Sigma
For quality assurance managers, applying Six Sigma can be a transformative strategy.
Here are some steps to effectively implement Six Sigma within an organization.
Training and Development
Invest in training employees in Six Sigma methodologies.
This includes having designated Six Sigma champions like Green Belts and Black Belts who lead projects and ensure adherence to processes.
Training empowers employees to be change agents, increasing their value to the company.
Choosing the Right Projects
Identify projects that align with business objectives and have the potential for significant impact.
These projects should target processes with high defect rates, customer dissatisfaction, or considerable room for improvement.
Data Collection and Analysis
Gather accurate data to understand current process performance and establish benchmarks.
Analyze data comprehensively to identify trends or patterns and use it to develop informed improvement strategies.
Continuous Monitoring
Once improvements are implemented, continuously monitor the processes to ensure they are being followed correctly.
Regular audits and performance reviews will help in sustaining the gains made by the Six Sigma projects.
The Benefits of Six Sigma in Quality Assurance
Implementing Six Sigma brings various benefits to a quality assurance department and the organization as a whole.
Improved Customer Satisfaction
With fewer defects and higher quality products, customer satisfaction levels rise.
Happy customers are more likely to return, recommend your company, and help grow sales.
Increased Profit Margins
By reducing waste and improving efficiency, companies experience cost savings and better profit margins.
Six Sigma also reduces capital spent on curing defects, thereby retaining more earnings.
Enhanced Competitive Edge
Businesses that actively use Six Sigma maintain a competitive edge by consistently delivering quality.
This strategic advantage allows them to stay ahead in their industries.
In conclusion, Six Sigma is a powerful methodology that, when implemented correctly, can lead to significant quality improvement and cost reduction.
By following its principles, quality assurance departments can drive success and ensure that their organizations remain competitive and profitable.
資料ダウンロード
QCD管理受発注クラウド「newji」は、受発注部門で必要なQCD管理全てを備えた、現場特化型兼クラウド型の今世紀最高の受発注管理システムとなります。
ユーザー登録
受発注業務の効率化だけでなく、システムを導入することで、コスト削減や製品・資材のステータス可視化のほか、属人化していた受発注情報の共有化による内部不正防止や統制にも役立ちます。
NEWJI DX
製造業に特化したデジタルトランスフォーメーション(DX)の実現を目指す請負開発型のコンサルティングサービスです。AI、iPaaS、および先端の技術を駆使して、製造プロセスの効率化、業務効率化、チームワーク強化、コスト削減、品質向上を実現します。このサービスは、製造業の課題を深く理解し、それに対する最適なデジタルソリューションを提供することで、企業が持続的な成長とイノベーションを達成できるようサポートします。
製造業ニュース解説
製造業、主に購買・調達部門にお勤めの方々に向けた情報を配信しております。
新任の方やベテランの方、管理職を対象とした幅広いコンテンツをご用意しております。
お問い合わせ
コストダウンが利益に直結する術だと理解していても、なかなか前に進めることができない状況。そんな時は、newjiのコストダウン自動化機能で大きく利益貢献しよう!
(β版非公開)