- お役立ち記事
- A must-see for quality assurance department managers! How to achieve data-driven quality improvement using seven new QC tools
A must-see for quality assurance department managers! How to achieve data-driven quality improvement using seven new QC tools
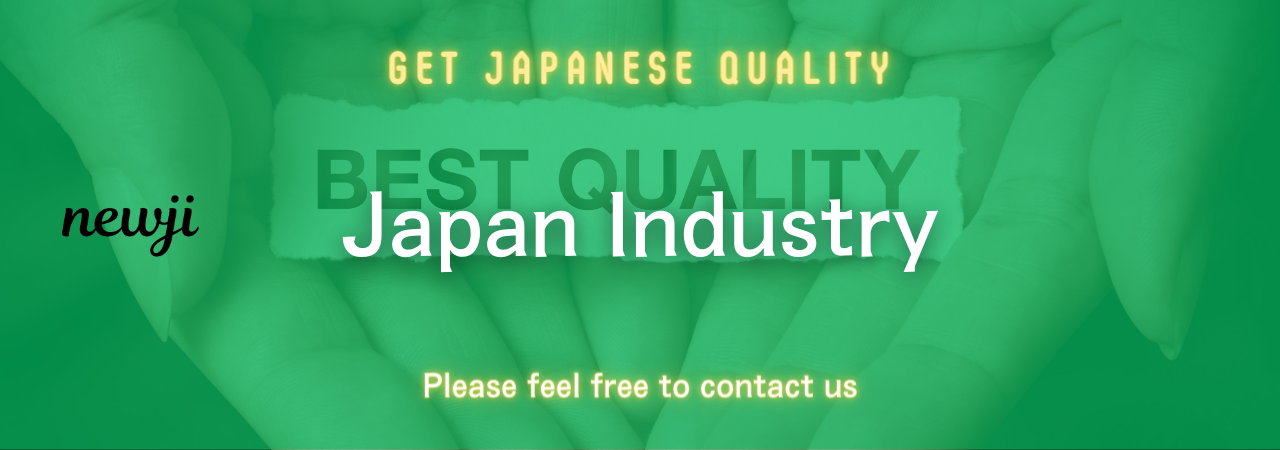
目次
Introduction to Data-Driven Quality Improvement
In today’s competitive business environment, quality assurance has become more important than ever.
Ensuring high quality in products and services is essential for maintaining customer satisfaction and staying ahead of competitors.
The rapidly evolving field of data analytics provides a vast array of tools to help achieve these quality objectives.
Among those tools are the seven new QC (Quality Control) tools that are helping managers revolutionize quality improvement efforts.
These tools are designed to utilize data effectively, leading to more informed decision-making and enhanced quality control processes.
The Seven New QC Tools
Developed to go beyond traditional quality control methods, these seven new QC tools assist in tackling complex quality issues with a more holistic and data-driven approach.
They are valuable assets for any quality assurance department aiming to refine their processes.
Let’s delve into each tool and explore how they contribute to quality improvement.
Affinity Diagram
The affinity diagram is a brainstorming tool that organizes a large number of ideas into their natural relationships.
This tool is useful for Quality Assurance managers who need to bring together diverse thoughts from different stakeholders.
By clustering similar ideas, the affinity diagram helps identify patterns, common themes, and potential areas for improvement.
Interrelationship Digraph
An interrelationship digraph helps visualize the cause-and-effect relationships within a complex system.
It assists in identifying key factors that influence quality.
For quality assurance managers, this tool is essential for understanding which aspects of a process or product are causing specific quality issues.
By identifying these critical factors, managers can target their improvement efforts more effectively.
Tree Diagram
The tree diagram is a hierarchical tool that breaks down broad objectives into manageable tasks.
It’s particularly beneficial in quality planning and project management.
For example, ensuring a product meets quality standards might be a main goal.
By using a tree diagram, managers can identify sub-tasks such as material selection, process refinement, and final testing that are necessary to achieve that goal.
Matrix Diagram
A matrix diagram is a powerful tool for examining relationships between different variables.
In quality assurance, it can help you visualize and prioritize the relationships between different attributes of a product or process.
This aids in identifying critical areas that require quality improvement efforts and allocating resources effectively.
Process Decision Program Chart (PDPC)
PDPC is used for contingency planning.
It anticipates potential problems and helps develop strategies to counteract them.
Quality assurance managers can use PDPC to prepare for unexpected issues in quality processes, ensuring that there are robust plans in place to maintain quality standards even in adverse situations.
Activity Network Diagram
The activity network diagram is a project management tool that assists in scheduling and sequencing tasks.
For quality improvement projects, it ensures that all critical tasks are completed in a timely manner.
By optimizing the sequence of activities, managers can reduce delays and improve the efficiency of quality control operations.
Prioritization Matrix
Prioritization matrices help determine the order in which tasks should be undertaken based on their importance.
It is particularly useful in deciding where to focus quality improvement efforts when resources are limited.
By prioritizing tasks with the greatest impact on quality, managers can ensure that their efforts yield significant results.
Implementing Data-Driven Strategies
Implementing these seven QC tools effectively requires a strategic approach that incorporates data analysis into the quality assurance process.
Data-driven quality improvement involves collecting and analyzing relevant data to inform decisions and track progress.
It requires collaboration across departments, from production and R&D to customer service and marketing.
Collecting Quality Data
The first step in a data-driven strategy is to identify the types of data that are critical for quality improvement.
This could include customer feedback, production metrics, or defect rates.
Once identified, set up systems for regularly collecting and reviewing this data.
This might involve automated data collection tools or manual processes, depending on your specific needs.
Analyzing Data for Insights
Once data is collected, the next step is transforming it into actionable insights.
Use statistical analysis or data visualization tools to identify trends, outliers, and patterns.
The insights gained will guide the use of the seven QC tools.
For example, you might discover that a particular process consistently results in defects.
Armed with this knowledge, you can utilize an interrelationship digraph to dive deeper into the cause and effect.
Driving Continuous Improvement
Continuous improvement is a core principle of effective quality management.
By consistently applying the insights gained from data analysis, you can drive ongoing enhancements to products, services, and processes.
Regularly revisiting the QC tools and reassessing the data ensures that improvements are implemented and sustained over time.
Benefits of a Data-Driven Quality Approach
By adopting a data-driven approach to quality improvement using the seven new QC tools, organizations can realize several benefits.
These include enhancing customer satisfaction by consistently delivering high-quality products and services.
Additionally, streamlined processes and reduced waste mean significant cost savings for the business.
It also fosters a culture of continuous improvement, encouraging employees to proactively seek ways to enhance quality.
Conclusion
Quality assurance departments face the challenging task of maintaining and improving product and service standards.
By leveraging data effectively through the use of the seven new QC tools, these departments can achieve data-driven quality improvement.
This approach not only enhances process efficiencies but also builds a robust foundation for sustained competitive advantage.
Managers should embrace these tools and strategies to ensure their organizations remain leaders in quality assurance.
資料ダウンロード
QCD調達購買管理クラウド「newji」は、調達購買部門で必要なQCD管理全てを備えた、現場特化型兼クラウド型の今世紀最高の購買管理システムとなります。
ユーザー登録
調達購買業務の効率化だけでなく、システムを導入することで、コスト削減や製品・資材のステータス可視化のほか、属人化していた購買情報の共有化による内部不正防止や統制にも役立ちます。
NEWJI DX
製造業に特化したデジタルトランスフォーメーション(DX)の実現を目指す請負開発型のコンサルティングサービスです。AI、iPaaS、および先端の技術を駆使して、製造プロセスの効率化、業務効率化、チームワーク強化、コスト削減、品質向上を実現します。このサービスは、製造業の課題を深く理解し、それに対する最適なデジタルソリューションを提供することで、企業が持続的な成長とイノベーションを達成できるようサポートします。
オンライン講座
製造業、主に購買・調達部門にお勤めの方々に向けた情報を配信しております。
新任の方やベテランの方、管理職を対象とした幅広いコンテンツをご用意しております。
お問い合わせ
コストダウンが利益に直結する術だと理解していても、なかなか前に進めることができない状況。そんな時は、newjiのコストダウン自動化機能で大きく利益貢献しよう!
(Β版非公開)