- お役立ち記事
- A must-see for quality assurance department managers! How to achieve data-driven quality improvement using seven new QC tools
A must-see for quality assurance department managers! How to achieve data-driven quality improvement using seven new QC tools
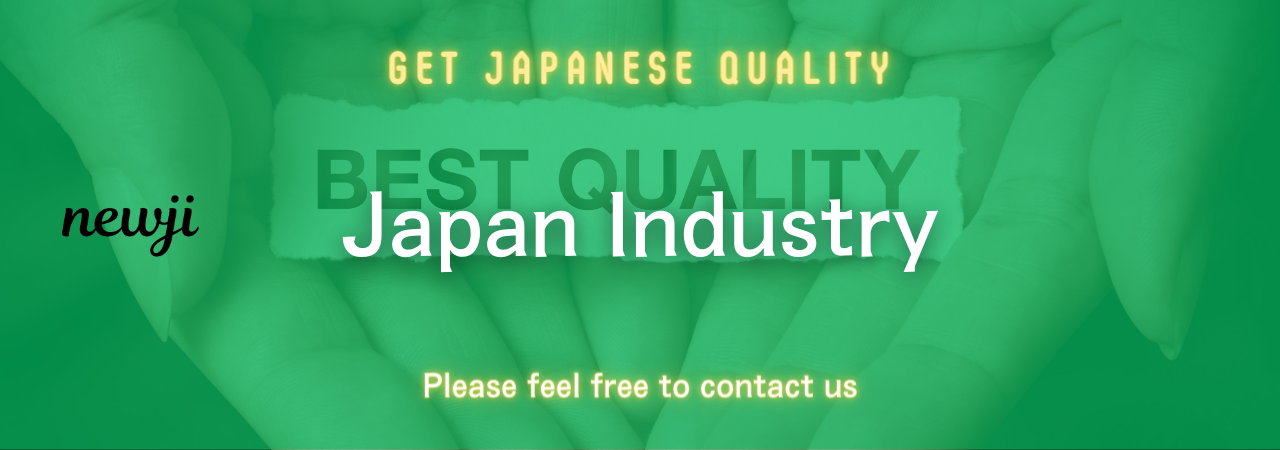
目次
Understanding the Importance of Quality Assurance
Quality assurance is a critical aspect of any manufacturing or service industry.
It ensures that products and services meet specific requirements and standards, which helps to enhance customer satisfaction and loyalty.
For quality assurance department managers, achieving data-driven quality improvement is not just a goal but a necessity.
Incorporating data analytics into quality processes allows for better decision-making, minimizes errors, and enhances the overall efficiency.
The journey to achieving quality improvement through data requires a strategic approach.
This is where the seven new Quality Control (QC) tools come into play.
These tools help in analyzing processes, identifying areas of improvement, and implementing changes effectively.
Introducing the Seven New QC Tools
Quality improvement has evolved along with industry requirements and technological advancements.
The seven new QC tools were developed to handle more complex and data-intensive processes than traditional quality tools.
These tools include:
1. **Affinity Diagram**
2. **Interrelationship Digraph**
3. **Tree Diagram**
4. **Prioritization Matrix**
5. **Matrix Diagram**
6. **Process Decision Program Chart (PDPC)**
7. **Activity Network Diagram**
These tools are designed to address specific quality-related challenges and provide structured methods for process analysis and improvement.
How Each QC Tool Contributes to Data-Driven Quality Improvement
Affinity Diagram
The Affinity Diagram is used to organize a large number of ideas into their natural relationships.
This is particularly useful when data collected from customers or processes is overwhelming and needs simplification.
By grouping similar ideas, the Affinity Diagram reveals natural patterns and themes, making data interpretation easier and more comprehensible.
Interrelationship Digraph
This tool helps in visualizing the cause-and-effect relationships among different issues.
An Interrelationship Digraph is useful in complex scenarios where issues do not fit a simple sequence, allowing managers to understand the interactions and dependencies among various factors.
This understanding is crucial to identify the root cause of quality issues and address them effectively.
Tree Diagram
A Tree Diagram breaks down broad goals into specific, actionable steps.
It is a powerful tool for planning and executing quality improvement strategies.
In a data-driven approach, a Tree Diagram helps in systematically analyzing data and identifying the sequence of actions required to meet quality objectives.
Prioritization Matrix
The Prioritization Matrix assists in ranking items based on their importance.
It takes subjective judgments and weights them against data-driven criteria to rank issues or tasks.
By using this matrix, quality managers can identify which quality improvement actions will have the most significant impact on overall quality.
Matrix Diagram
A Matrix Diagram displays the relationships between two or more groups of information.
It is useful for identifying potential problems and opportunities in quality processes.
This tool helps quality assurance teams to visualize correlations and dependencies, which facilitates more data-driven decision-making.
Process Decision Program Chart (PDPC)
The PDPC helps in anticipating potential issues in a quality improvement plan and preparing countermeasures in advance.
By mapping out every detail, the PDPC minimizes surprises and ensures a prepared response to potential setbacks.
This is essential in data-driven environments where the ability to predict outcomes can significantly impact quality improvement efforts.
Activity Network Diagram
Also known as the arrow diagram, this tool is useful for scheduling and managing complex projects.
The Activity Network Diagram helps identify the longest sequence of dependent activities to optimize resource allocation and timing.
For quality assurance managers, this ensures processes are accomplished efficiently, minimizing delays and enhancing product quality.
Implementing Data-Driven Quality Improvement
Incorporating the seven new QC tools effectively requires a systematic approach and a culture that values data-driven decisions.
Quality assurance managers should start with a thorough assessment of current quality processes and identify specific areas where data can add value.
Training teams on how to utilize these tools is crucial.
Ensure all team members understand how to collect, analyze, and interpret data using these QC tools.
Continuous monitoring and feedback loops are essential to refine processes and ensure sustainable quality improvement.
Establish clear metrics for measuring success.
Implement these tools with defined goals and objectives in mind, and regularly review the data to assess progress.
Challenges and Solutions in Adopting a Data-Driven Approach
Adopting a data-driven approach to quality improvement is not without challenges.
These can include resistance to change, lack of data skills among staff, and data management difficulties.
However, these challenges can be overcome through proper change management strategies, training, and leveraging technology for data management.
Investing in training programs can bridge the data skills gap, ensuring that all team members have the necessary skills to make data-driven decisions.
Similarly, adopting robust data management software can help streamline data collection, analysis, and storage, simplifying the entire process.
Looking forward, remaining adaptable and continuing to refine quality processes in response to new data and insights will ensure sustained success.
Conclusion
The integration of the seven new QC tools into quality assurance processes supports a data-driven approach to quality improvement.
By organizing ideas, understanding relationships, planning steps, prioritizing actions, visualizing relationships, preparing for challenges, and optimizing schedules, these tools provide comprehensive support for quality managers.
As the industry continues to pivot towards data-centric operations, the role of these QC tools and data-driven strategies becomes increasingly vital in achieving excellence in quality standards.
資料ダウンロード
QCD調達購買管理クラウド「newji」は、調達購買部門で必要なQCD管理全てを備えた、現場特化型兼クラウド型の今世紀最高の購買管理システムとなります。
ユーザー登録
調達購買業務の効率化だけでなく、システムを導入することで、コスト削減や製品・資材のステータス可視化のほか、属人化していた購買情報の共有化による内部不正防止や統制にも役立ちます。
NEWJI DX
製造業に特化したデジタルトランスフォーメーション(DX)の実現を目指す請負開発型のコンサルティングサービスです。AI、iPaaS、および先端の技術を駆使して、製造プロセスの効率化、業務効率化、チームワーク強化、コスト削減、品質向上を実現します。このサービスは、製造業の課題を深く理解し、それに対する最適なデジタルソリューションを提供することで、企業が持続的な成長とイノベーションを達成できるようサポートします。
オンライン講座
製造業、主に購買・調達部門にお勤めの方々に向けた情報を配信しております。
新任の方やベテランの方、管理職を対象とした幅広いコンテンツをご用意しております。
お問い合わせ
コストダウンが利益に直結する術だと理解していても、なかなか前に進めることができない状況。そんな時は、newjiのコストダウン自動化機能で大きく利益貢献しよう!
(Β版非公開)