- お役立ち記事
- A must-see for quality assurance department managers! How to implement APQP to improve the quality of product development
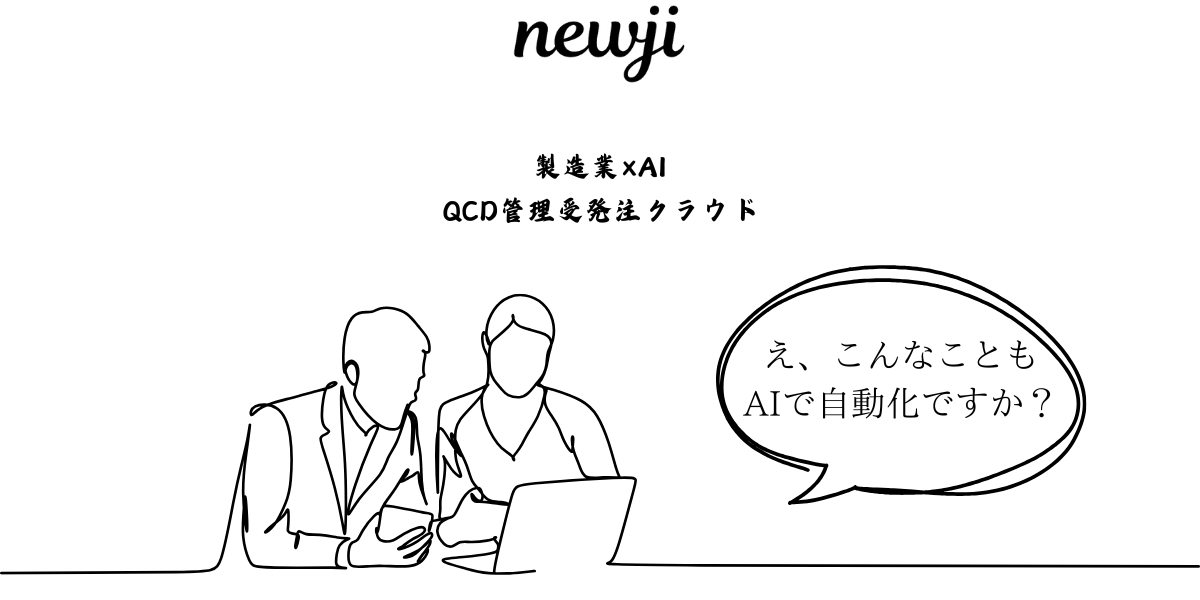
A must-see for quality assurance department managers! How to implement APQP to improve the quality of product development
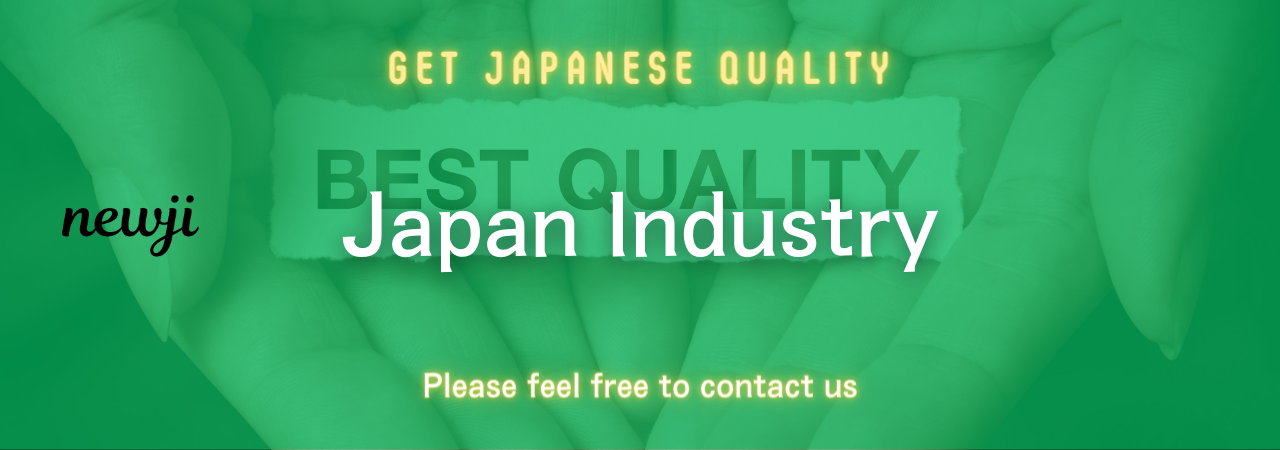
目次
Understanding APQP: What It Is and Why It’s Important
Advanced Product Quality Planning (APQP) is a framework that helps organizations in the manufacturing sector to ensure the quality of their products from the initial concept through production.
Originally developed by the automotive industry, APQP has been widely adopted across various sectors to enhance product quality and reliability.
It focuses on anticipating potential issues in the product development process and mitigating them before they become real problems.
Implementing APQP means that quality assurance isn’t just a phase in the production cycle but is ingrained in every step, resulting in more efficient processes and higher quality outcomes.
Core Elements of APQP
APQP is structured around five key phases: Plan and Define Program, Product Design and Development Verification, Process Design and Development Verification, Product and Process Validation, and Feedback Assessment and Corrective Action.
Each of these phases addresses specific areas of product and process development, ensuring that every aspect is planned, scrutinized, and optimized for quality.
APQP begins with clear planning and defining, focusing on customer needs, regulatory requirements, and core processes.
This phase is essential for understanding what the customer requires and what the final product should achieve.
Moving forward, the focus shifts to design and development.
Here, the objective is to identify potential risks in the design stage of the product.
Various tools like FMEA (Failure Mode and Effects Analysis) are used to evaluate potential points of failure and develop improvements.
The next phase emphasizes process design and verification.
It ensures that manufacturing processes are capable of producing the product efficiently and consistently.
This involves rigorous testing and criteria-setting to ensure repeatability and durability in production.
The product and process validation phase involves prototype testing, pilot runs, and more to validate that both the product and the manufacturing processes meet the quality standards defined earlier.
Finally, feedback assessment and corrective action is a continuous phase aimed at addressing any remaining or emerging issues through customer feedback and process evaluation.
Implementing APQP in Your Organization
The successful implementation of APQP requires a strategic and structured approach.
Quality assurance managers must start by setting a clear vision and objectives aligned with APQP principles.
This vision should be communicated effectively across teams to ensure collaborative efforts toward common goals.
Next, it’s vital to conduct comprehensive training sessions for all staff members involved in the product development and manufacturing processes.
Understanding the importance of each phase within APQP and how their roles contribute to overall quality is essential for successful implementation.
Establishing strong cross-functional teams is another crucial step.
These teams should consist of members from engineering, quality assurance, production, and supply chain departments to ensure a comprehensive approach to product development and quality assurance.
Additionally, a robust system for documentation and data tracking should be put in place.
This allows for effective monitoring and evaluation of each phase, ensuring that processes are transparent, repeatable, and continuously improved.
Engaging with suppliers early in the process is equally important to align expectations and foster a collaborative relationship.
Reliable suppliers contribute to the smooth running of the product development cycle and adherence to quality standards.
Benefits of Implementing APQP
Integrating APQP into your product development cycle offers numerous benefits that significantly enhance the quality and reliability of your products.
Firstly, it ensures that customer requirements are consistently met or exceeded, which translates into higher customer satisfaction and loyalty.
This is achieved by involving customers early in the planning phase to understand their needs precisely.
APQP also promotes the identification and mitigation of risks early in the product development process.
This proactive approach reduces the likelihood of defects, recalls, and warranty costs, which can be detrimental to the company’s reputation and financial health.
By fostering an environment of continuous improvement and feedback, APQP helps organizations adapt to changes and improve their processes over time.
This results in more efficient processes, reduced waste, and optimized resource utilization.
Furthermore, APQP enhances collaboration and communication among departments, leading to a more cohesive and coordinated approach to problem-solving and innovation.
Challenges and Considerations in APQP Implementation
While APQP offers a structured approach to quality planning, implementing it can be challenging, especially for organizations new to the process.
One common obstacle is the resistance to change, especially if employees are accustomed to existing workflows and practices.
To overcome this, management must demonstrate leadership and commitment, providing clear examples of the benefits through case studies or pilot projects.
Another challenge lies in effectively coordinating cross-functional teams, which requires clear communication and the establishment of clear roles and responsibilities.
Employing digital tools that facilitate collaboration and project management can significantly aid in this area.
Finally, monitoring and evaluating progress consistently can be resource-intensive, necessitating investments in proper training and tools to ensure effective implementation.
Organizations must recognize that APQP is not a one-time setup but a continuous journey requiring ongoing commitment to uphold high-quality standards.
Conclusion
For quality assurance department managers, implementing APQP is a powerful way to enhance product quality and customer satisfaction.
By integrating APQP into the product development lifecycle, organizations can better predict, plan for, and respond to potential quality issues.
Despite the challenges of initially adopting APQP, its long-term benefits in reducing risks and building more resilient processes make it a worthwhile investment.
In today’s competitive market, maintaining high standards of quality not only helps retain existing customers but also attracts new ones, ultimately leading to a stronger market position.
APQP, when applied effectively, becomes a cornerstone of your organization’s reputation for excellence and innovation in product development.
資料ダウンロード
QCD調達購買管理クラウド「newji」は、調達購買部門で必要なQCD管理全てを備えた、現場特化型兼クラウド型の今世紀最高の購買管理システムとなります。
ユーザー登録
調達購買業務の効率化だけでなく、システムを導入することで、コスト削減や製品・資材のステータス可視化のほか、属人化していた購買情報の共有化による内部不正防止や統制にも役立ちます。
NEWJI DX
製造業に特化したデジタルトランスフォーメーション(DX)の実現を目指す請負開発型のコンサルティングサービスです。AI、iPaaS、および先端の技術を駆使して、製造プロセスの効率化、業務効率化、チームワーク強化、コスト削減、品質向上を実現します。このサービスは、製造業の課題を深く理解し、それに対する最適なデジタルソリューションを提供することで、企業が持続的な成長とイノベーションを達成できるようサポートします。
オンライン講座
製造業、主に購買・調達部門にお勤めの方々に向けた情報を配信しております。
新任の方やベテランの方、管理職を対象とした幅広いコンテンツをご用意しております。
お問い合わせ
コストダウンが利益に直結する術だと理解していても、なかなか前に進めることができない状況。そんな時は、newjiのコストダウン自動化機能で大きく利益貢献しよう!
(Β版非公開)