- お役立ち記事
- A must-see for quality control department leaders in the auto parts manufacturing industry! Improving accuracy of quality evaluation using Rockwell hardness test
A must-see for quality control department leaders in the auto parts manufacturing industry! Improving accuracy of quality evaluation using Rockwell hardness test
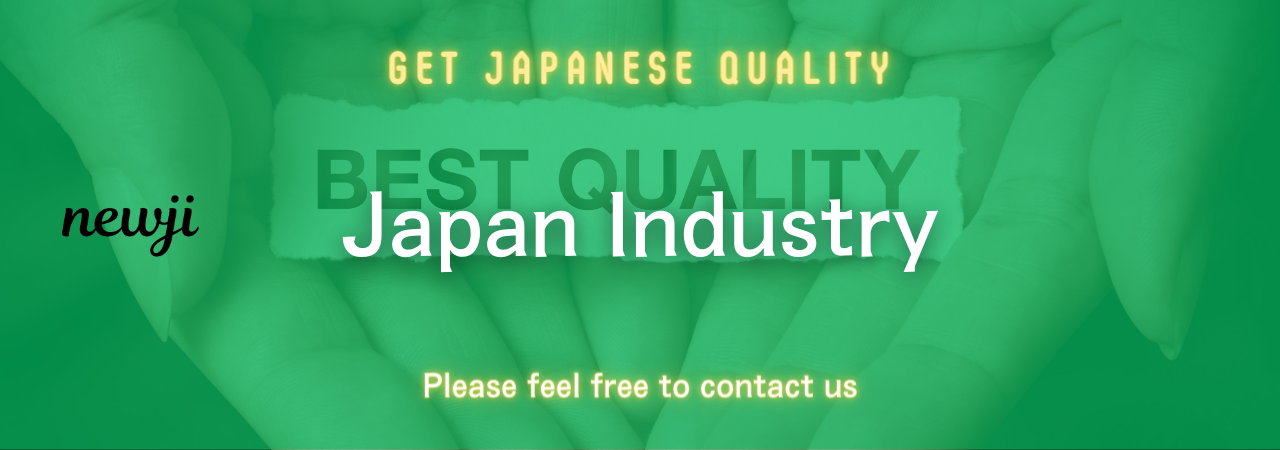
目次
Understanding the Importance of Quality Control in Auto Parts Manufacturing
Quality control is a critical aspect of the auto parts manufacturing industry.
Ensuring that each part meets specific standards is essential for the safety and performance of vehicles.
The quality control department is responsible for maintaining these standards, and one of the key methods used is the Rockwell hardness test.
What is the Rockwell Hardness Test?
The Rockwell hardness test is a method used to measure the hardness of materials.
It involves applying a specific amount of force to a material using a hard indenter.
The depth of penetration is then measured, which determines the material’s hardness level.
This test is widely used in the auto parts industry because it provides accurate and reliable data about a material’s durability and strength.
The Role of the Rockwell Hardness Test in Quality Evaluation
In the context of auto parts manufacturing, the Rockwell hardness test plays a significant role in quality evaluation.
Hardness is a critical property for many automotive components, particularly those that must withstand high wear and friction, such as gears, bearings, and shafts.
By using the Rockwell hardness test, manufacturers can ensure these parts meet required specifications before they are fitted into vehicles.
Enhancing Accuracy in Quality Control
The accuracy of the Rockwell hardness test is integral to maintaining the quality of automotive parts.
For quality control department leaders, improving the precision of this test is of utmost importance.
The following strategies can be implemented to enhance accuracy:
1. **Calibration and Maintenance of Equipment**: Ensuring that the testing machines are regularly calibrated and maintained is crucial.
Any discrepancies in equipment can lead to inaccurate results, potentially affecting the quality of auto parts.
2. **Staff Training**: Regularly training staff to ensure they are up-to-date with the latest testing procedures is essential.
Experienced and well-trained personnel can help maintain consistency and accuracy in testing.
3. **Controlled Testing Environment**: Conducting tests in a controlled environment helps eliminate external factors that might affect the results.
This includes maintaining a consistent temperature and humidity level in the testing area.
The Benefits of Using the Rockwell Hardness Test
The Rockwell hardness test offers several benefits that make it a preferred choice in the auto parts industry:
1. Quick and Efficient
Compared to other hardness testing methods, the Rockwell hardness test is quick and efficient.
It provides immediate results, allowing for faster decision-making in quality control processes.
2. Non-destructive Testing
One of the significant advantages of the Rockwell hardness test is that it is non-destructive.
Parts do not need to be altered or damaged in any way, which is crucial when dealing with expensive or delicate components.
3. Versatile and Adaptable
The Rockwell hardness test can be applied to a wide range of materials, from metals to plastics.
Its versatility makes it highly adaptable to different testing needs within the auto parts manufacturing industry.
Best Practices for Implementing the Rockwell Hardness Test
For leaders in the quality control departments, implementing best practices for the Rockwell hardness test will ensure optimal results:
Developing Protocols
Establish clear protocols for conducting the Rockwell hardness test.
Documentation should include detailed instructions and criteria for passing or failing components based on hardness results.
Continuous Improvement
Regularly review and update testing practices and protocols as technology and standards evolve.
Continuous improvement is key to maintaining high-quality production.
Inter-departmental Collaboration
Encourage collaboration between departments, such as engineering and production, to ensure that the Rockwell hardness test aligns with overall quality objectives and production goals.
This collaborative approach can help identify any issues early and develop solutions effectively.
Conclusion
For leaders in the quality control departments of auto parts manufacturing, the Rockwell hardness test is an indispensable tool.
By understanding its role and employing strategies to enhance its accuracy, the quality of automotive components can be significantly improved.
Ultimately, this leads to safer and more reliable vehicles, boosting consumer trust and satisfaction in the automotive industry.
資料ダウンロード
QCD調達購買管理クラウド「newji」は、調達購買部門で必要なQCD管理全てを備えた、現場特化型兼クラウド型の今世紀最高の購買管理システムとなります。
ユーザー登録
調達購買業務の効率化だけでなく、システムを導入することで、コスト削減や製品・資材のステータス可視化のほか、属人化していた購買情報の共有化による内部不正防止や統制にも役立ちます。
NEWJI DX
製造業に特化したデジタルトランスフォーメーション(DX)の実現を目指す請負開発型のコンサルティングサービスです。AI、iPaaS、および先端の技術を駆使して、製造プロセスの効率化、業務効率化、チームワーク強化、コスト削減、品質向上を実現します。このサービスは、製造業の課題を深く理解し、それに対する最適なデジタルソリューションを提供することで、企業が持続的な成長とイノベーションを達成できるようサポートします。
オンライン講座
製造業、主に購買・調達部門にお勤めの方々に向けた情報を配信しております。
新任の方やベテランの方、管理職を対象とした幅広いコンテンツをご用意しております。
お問い合わせ
コストダウンが利益に直結する術だと理解していても、なかなか前に進めることができない状況。そんな時は、newjiのコストダウン自動化機能で大きく利益貢献しよう!
(Β版非公開)