- お役立ち記事
- A must-see for quality managers in the chemical manufacturing industry! How to optimize reaction processes with real-time monitoring
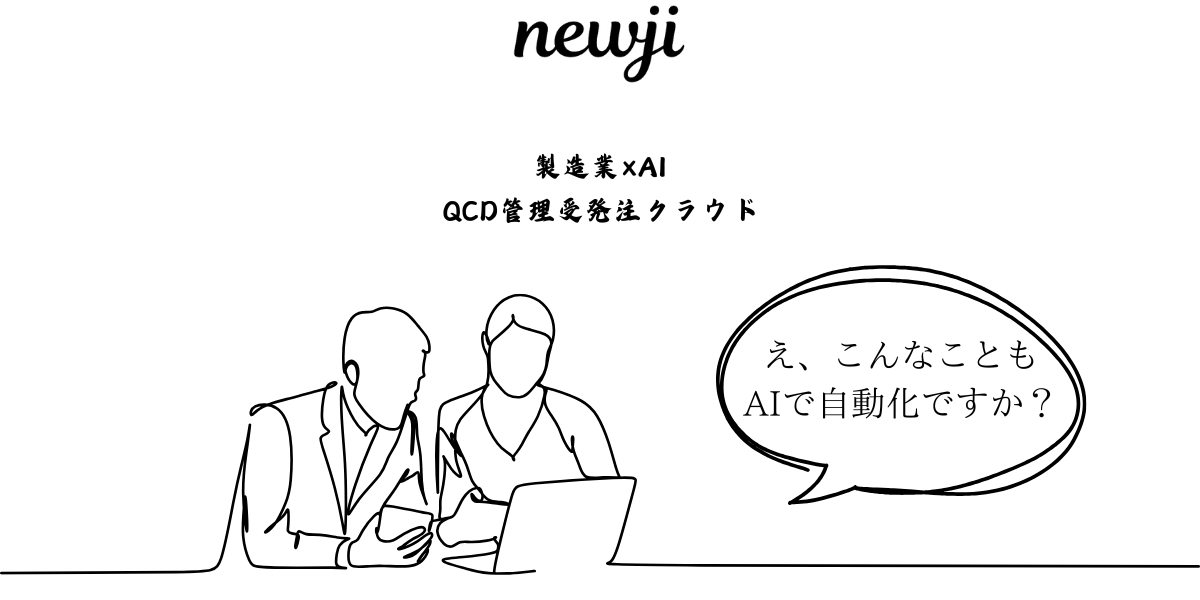
A must-see for quality managers in the chemical manufacturing industry! How to optimize reaction processes with real-time monitoring
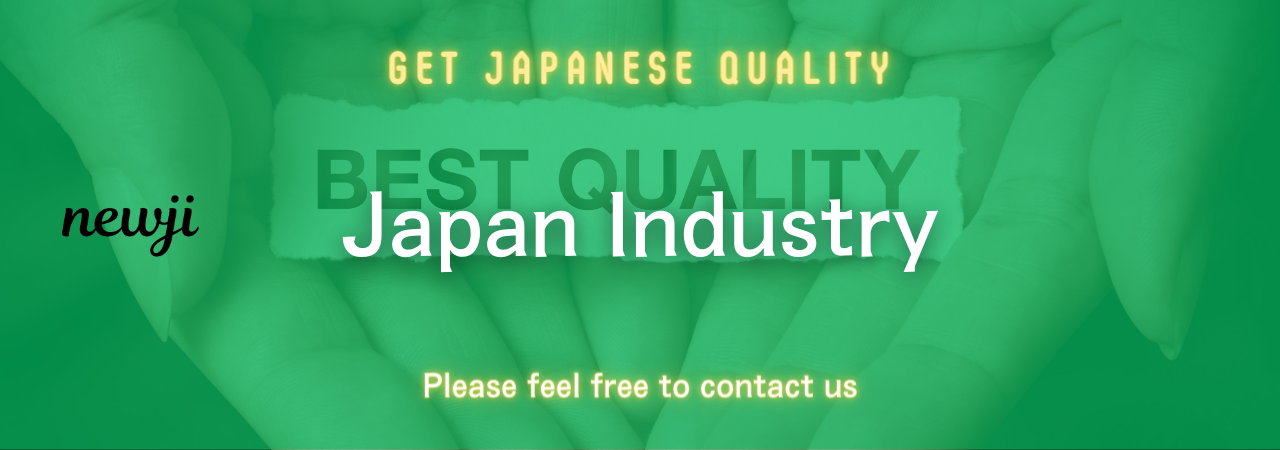
目次
Understanding Reaction Processes in Chemical Manufacturing
In the world of chemical manufacturing, reaction processes are the backbone of production.
These processes involve the transformation of raw materials into valuable products through chemical reactions.
To ensure the high quality and efficiency of these reactions, quality managers must have a firm understanding of the underlying principles and challenges associated with these processes.
Chemical reactions can be complex, often involving multiple steps and various variables.
Each reaction step can influence the overall outcome, making it crucial for quality managers to monitor and control these processes diligently.
Optimizing reaction processes not only leads to improved product quality but also enhances productivity and reduces costs.
Challenges in Chemical Reaction Monitoring
Monitoring chemical reactions in real-time is a challenging task due to the dynamic and intricate nature of these processes.
Chemical reactions can be affected by numerous factors such as temperature, pressure, pH levels, and the presence of contaminants.
Any deviation from the optimal conditions can result in subpar product quality or even hazardous outcomes.
Traditional methods of monitoring often involve manual sampling and laboratory analysis, which can be time-consuming and prone to errors.
These methods also lack the ability to provide immediate feedback, making it difficult to make on-the-fly adjustments to the reaction parameters.
As the demand for higher quality and more efficient production rises, there is an increasing need for advanced monitoring techniques.
The Importance of Real-Time Monitoring
Real-time monitoring of reaction processes provides a solution to the challenges faced in chemical manufacturing.
By using advanced technologies, such as process analytical technology (PAT), manufacturers can gain immediate insights into the reaction conditions and outcomes.
Real-time monitoring allows quality managers to detect potential issues early in the process.
This proactive approach enables swift adjustments to maintain optimal reaction conditions, reducing the risk of defects and waste.
It also facilitates the fine-tuning of reaction parameters, leading to higher yields and more consistent product quality.
Technologies for Real-Time Monitoring
There are several technologies that play a crucial role in enabling real-time monitoring of chemical reactions.
These include spectroscopy, chromatography, and other sensor-based solutions that provide continuous data on reaction progress and conditions.
Spectroscopic methods, such as infrared (IR) and Raman spectroscopy, offer non-invasive ways to monitor reaction components in real-time.
These techniques allow for the identification and quantification of different chemical species, providing a comprehensive understanding of the reaction dynamics.
Chromatography, another powerful tool, helps in separating and analyzing the individual components of a reaction mixture.
When combined with real-time data analysis, chromatography can deliver immediate insights into the efficiency and progression of a reaction.
Additionally, sensors play a pivotal role in measuring critical parameters such as temperature, pressure, and pH levels.
These sensors provide continuous feedback, ensuring that the reaction environment remains within the desired range for optimal performance.
Benefits of Implementing Real-Time Monitoring
The implementation of real-time monitoring in chemical manufacturing offers numerous benefits that go beyond improving product quality.
By optimizing reaction processes, companies can achieve significant cost savings and operational efficiencies.
Real-time monitoring reduces the need for manual intervention and laboratory testing, freeing up valuable resources and minimizing production downtime.
It also enhances safety by providing immediate alerts for any deviations from standard operating conditions, allowing for quick corrective actions.
Furthermore, the insights gained from real-time data can foster innovation, leading to the development of new products and processes.
By understanding reaction mechanisms in greater detail, manufacturers can create more sustainable and efficient production methods.
Steps to Optimize Reaction Processes
To effectively optimize reaction processes using real-time monitoring, quality managers should follow a strategic approach:
1. **Identify Key Parameters:** Determine the critical parameters that influence reaction outcomes, such as temperature, pressure, concentration, and reaction time.
2. **Integrate Monitoring Technologies:** Select and integrate suitable real-time monitoring technologies that align with your process requirements and objectives.
3. **Establish Baseline Conditions:** Develop a baseline of optimal conditions for each reaction by conducting controlled experiments and utilizing historical data.
4. **Continuously Monitor and Adjust:** Implement continuous monitoring to gather real-time data and make informed adjustments to maintain optimal reaction conditions.
5. **Analyze Data for Insights:** Use advanced data analytics to extract actionable insights, identify trends, and refine reaction processes for improved efficiency.
Conclusion
For quality managers in the chemical manufacturing industry, optimizing reaction processes through real-time monitoring is a crucial step toward achieving excellence.
The challenges of monitoring complex chemical reactions can be effectively addressed with modern technologies, leading to superior product quality, reduced costs, and enhanced operational efficiency.
By embracing real-time monitoring solutions, quality managers can not only ensure compliance with stringent industry standards but also drive innovation and sustainability in production processes.
The advantages extend beyond immediate gains, offering a pathway to long-term competitiveness and success in the ever-evolving market landscape.
資料ダウンロード
QCD調達購買管理クラウド「newji」は、調達購買部門で必要なQCD管理全てを備えた、現場特化型兼クラウド型の今世紀最高の購買管理システムとなります。
ユーザー登録
調達購買業務の効率化だけでなく、システムを導入することで、コスト削減や製品・資材のステータス可視化のほか、属人化していた購買情報の共有化による内部不正防止や統制にも役立ちます。
NEWJI DX
製造業に特化したデジタルトランスフォーメーション(DX)の実現を目指す請負開発型のコンサルティングサービスです。AI、iPaaS、および先端の技術を駆使して、製造プロセスの効率化、業務効率化、チームワーク強化、コスト削減、品質向上を実現します。このサービスは、製造業の課題を深く理解し、それに対する最適なデジタルソリューションを提供することで、企業が持続的な成長とイノベーションを達成できるようサポートします。
オンライン講座
製造業、主に購買・調達部門にお勤めの方々に向けた情報を配信しております。
新任の方やベテランの方、管理職を対象とした幅広いコンテンツをご用意しております。
お問い合わせ
コストダウンが利益に直結する術だと理解していても、なかなか前に進めることができない状況。そんな時は、newjiのコストダウン自動化機能で大きく利益貢献しよう!
(Β版非公開)