- お役立ち記事
- A must-see for the equipment maintenance department! Improving device reliability and predicting lifespan using Weibull analysis
月間77,185名の
製造業ご担当者様が閲覧しています*
*2025年2月28日現在のGoogle Analyticsのデータより
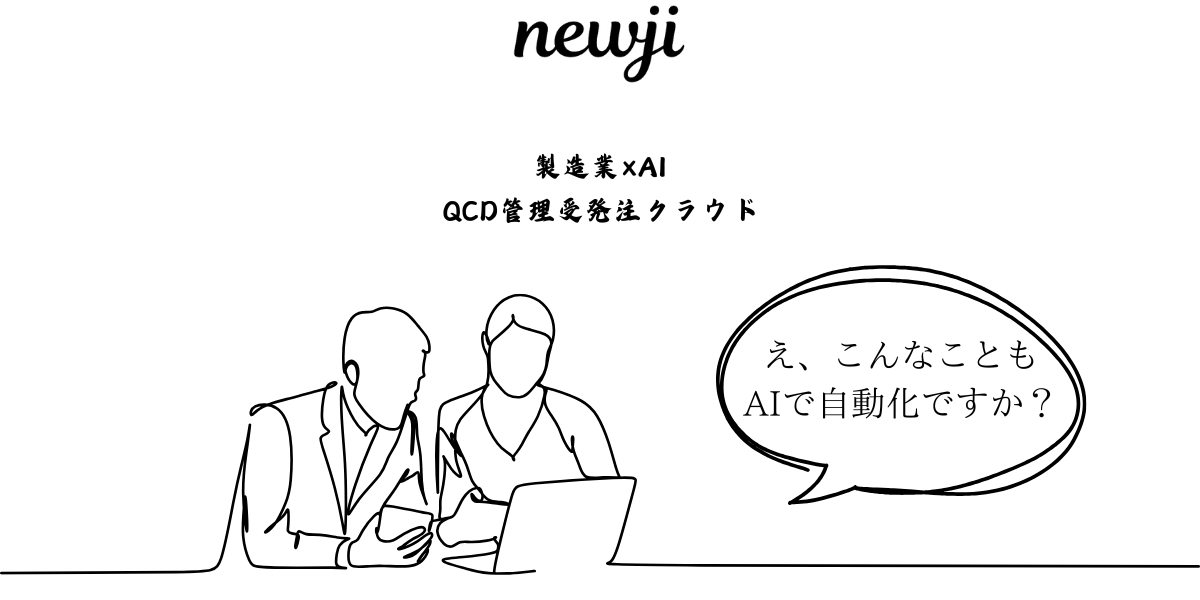
A must-see for the equipment maintenance department! Improving device reliability and predicting lifespan using Weibull analysis
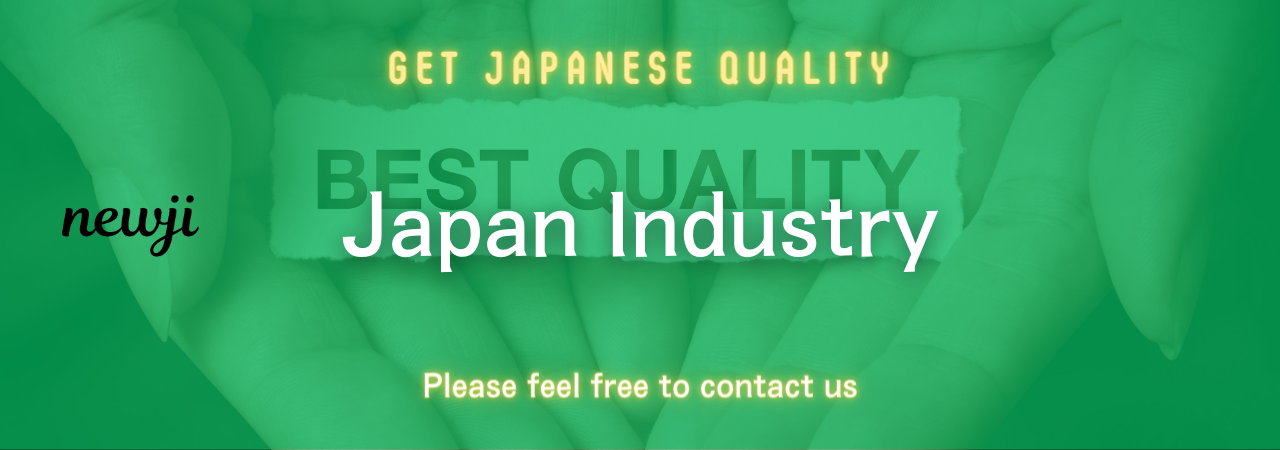
Weibull analysis, a statistical method named after the Swedish engineer Waloddi Weibull, is a powerful tool used to improve equipment reliability and predict the lifespan of devices.
By analyzing failure data, it helps maintenance departments make informed decisions about maintenance schedules and devise strategies to extend the life of machinery.
In this article, we will explore how Weibull analysis works and how it can benefit the equipment maintenance department in optimizing operations.
目次
Understanding Weibull Analysis
Weibull analysis uses a probability distribution to model the life data of products and systems.
It helps in understanding the rate at which items fail over time and allows the prediction of future failures.
This analysis is essential for maintenance departments as it enables them to assess the reliability of equipment and take preemptive actions to prevent unexpected downtimes.
The Weibull distribution has three parameters:
1. **Shape parameter (Beta, β):** Indicates the failure pattern of the equipment.
– If β < 1, the failure rate decreases over time, typically due to initial defects and early-life failures.
- If β = 1, it indicates a constant failure rate, similar to an exponential distribution, pointing towards random failure causes.
- If β > 1, the failure rate increases over time, often signifying wear-out failures.
2. **Scale parameter (Eta, η):** Denotes the characteristic life, where approximately 63.2% of units are expected to fail.
This value is crucial for estimating the lifespan of equipment under normal operating conditions.
3. **Location parameter (Gamma, γ):** Used for specific analyses to adjust the starting point on the time axis, often set to zero for simplification.
Benefits of Weibull Analysis
Improving Reliability
A key advantage of Weibull analysis is its capacity to improve the reliability of equipment.
By analyzing historical failure data, the maintenance team can detect patterns and understand the underlying causes of equipment failures.
This knowledge enables the implementation of preventive measures, such as improved design, material selection, or enhanced maintenance practices, to address the root causes and reduce the likelihood of recurrence.
Predicting Equipment Lifespan
Predicting the lifespan of equipment is essential for effective resource planning and budgeting.
Weibull analysis helps maintenance departments forecast when equipment is likely to fail, allowing for a proactive approach to maintenance.
By accurately estimating the remaining useful life of machinery, organizations can schedule repairs or replacements at optimal times, avoiding costly breakdowns and minimizing production interruptions.
Optimizing Maintenance Schedules
With the insights gained from Weibull analysis, maintenance schedules can be optimized to ensure better utilization of resources and minimize unnecessary maintenance activities.
Instead of relying on arbitrary time-based schedules, Weibull analysis advocates for condition-based or reliability-centered maintenance strategies.
This approach ensures that maintenance efforts are focused on equipment that truly needs attention, thereby reducing maintenance costs and improving operational efficiency.
Implementing Weibull Analysis in Maintenance Strategies
Data Collection
To effectively carry out Weibull analysis, it is vital to gather accurate and comprehensive failure data.
This data should include failure times, causes, and operating conditions.
The quality and quantity of data significantly impact the reliability of the analysis, so it’s crucial to maintain detailed records of equipment performance and failures over time.
Data Analysis
Once the data is collected, specialized software or statistical tools can be used to conduct Weibull analysis.
The results provide insights into equipment performance, allowing for informed decision-making.
Visualization tools, such as Weibull probability plots, are often used to interpret the data and communicate findings effectively to the maintenance team and management.
Integration into Maintenance Plans
Integrating Weibull analysis into maintenance strategies requires collaboration between different departments, including engineering, operations, and management.
By aligning maintenance schedules with the insights from Weibull analysis, organizations can strengthen their asset management practices, enhance reliability, and extend the life of their equipment.
Challenges and Considerations
Despite its numerous benefits, Weibull analysis also presents challenges that organizations must consider.
Data Accuracy
The accuracy of Weibull analysis heavily depends on the quality of failure data.
Incomplete or inaccurate records can lead to misleading conclusions.
Therefore, rigorous data collection and quality assurance practices are essential for obtaining reliable results.
Complexity and Expertise
Weibull analysis involves statistical calculations that may require expertise in reliability engineering or statistics.
Organizations may need to invest in training or hire experts to perform the analysis correctly and interpret the results effectively.
Dynamic Operating Conditions
Equipment operating conditions can change over time due to various factors, such as operator changes, environmental variations, or production demands.
Weibull analysis may need regular updates to account for these dynamic factors and ensure its ongoing relevance.
In conclusion, Weibull analysis is a valuable tool for maintenance departments seeking to enhance equipment reliability and predict lifespan.
By leveraging historical failure data, organizations can proactively optimize maintenance practices, reduce costs, and extend equipment life.
While challenges exist, the benefits provided by Weibull analysis make it a must-see approach for any maintenance department looking to improve their operations and asset management strategies.
資料ダウンロード
QCD管理受発注クラウド「newji」は、受発注部門で必要なQCD管理全てを備えた、現場特化型兼クラウド型の今世紀最高の受発注管理システムとなります。
ユーザー登録
受発注業務の効率化だけでなく、システムを導入することで、コスト削減や製品・資材のステータス可視化のほか、属人化していた受発注情報の共有化による内部不正防止や統制にも役立ちます。
NEWJI DX
製造業に特化したデジタルトランスフォーメーション(DX)の実現を目指す請負開発型のコンサルティングサービスです。AI、iPaaS、および先端の技術を駆使して、製造プロセスの効率化、業務効率化、チームワーク強化、コスト削減、品質向上を実現します。このサービスは、製造業の課題を深く理解し、それに対する最適なデジタルソリューションを提供することで、企業が持続的な成長とイノベーションを達成できるようサポートします。
製造業ニュース解説
製造業、主に購買・調達部門にお勤めの方々に向けた情報を配信しております。
新任の方やベテランの方、管理職を対象とした幅広いコンテンツをご用意しております。
お問い合わせ
コストダウンが利益に直結する術だと理解していても、なかなか前に進めることができない状況。そんな時は、newjiのコストダウン自動化機能で大きく利益貢献しよう!
(β版非公開)