- お役立ち記事
- A must-see for the general affairs department! How to obtain ISO9001 certification and promote internal standardization
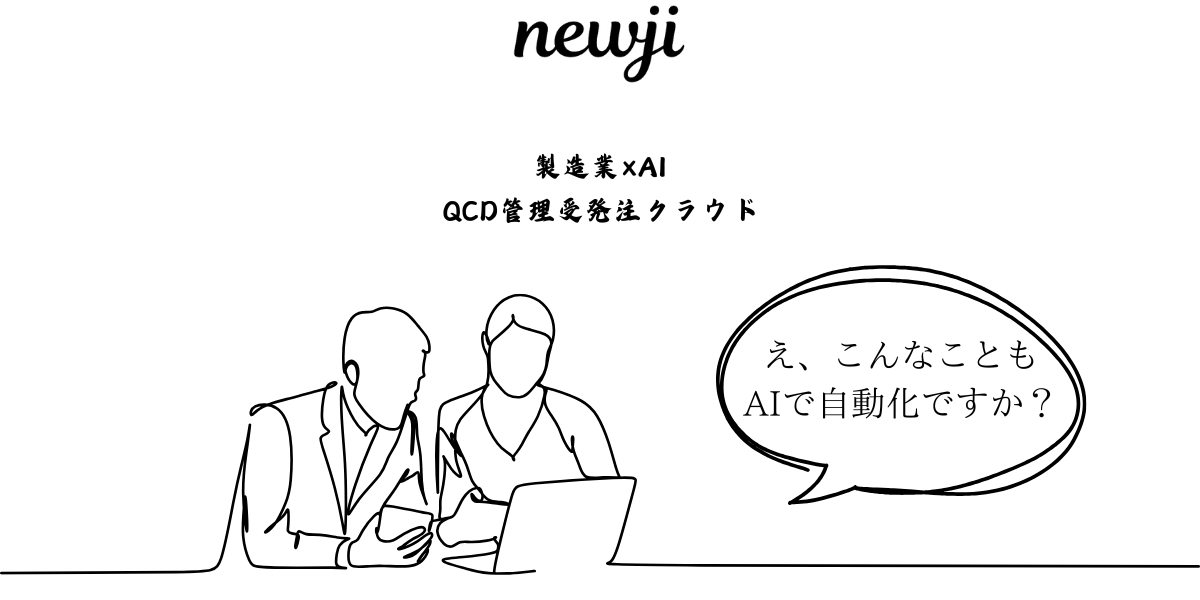
A must-see for the general affairs department! How to obtain ISO9001 certification and promote internal standardization
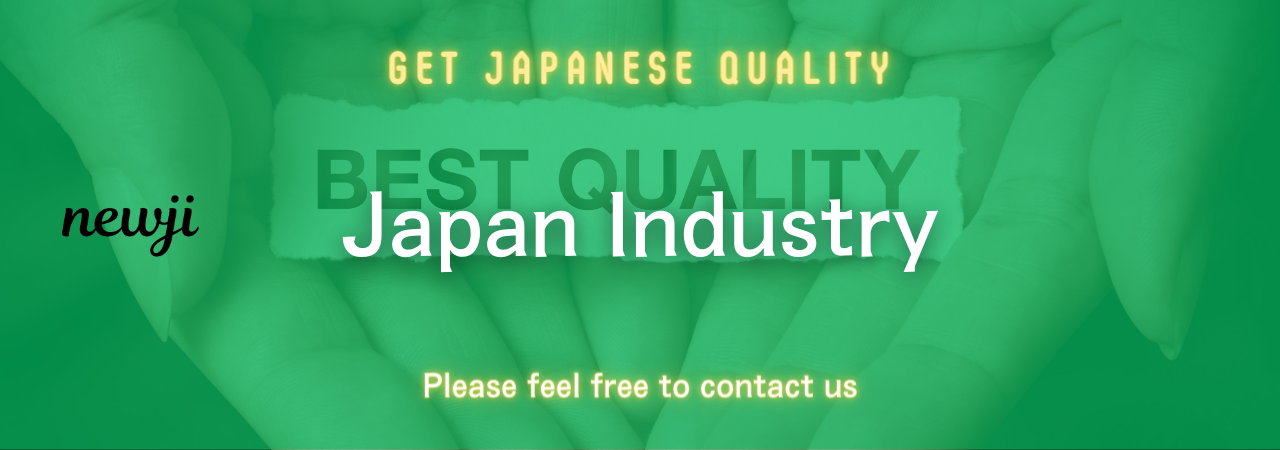
目次
Understanding ISO9001 Certification
ISO9001 is an internationally recognized standard for quality management systems (QMS).
It provides a framework that companies can use to ensure they consistently meet customer and regulatory requirements.
Achieving ISO9001 certification demonstrates a commitment to quality and customer satisfaction, which can enhance an organization’s reputation and open up new business opportunities.
What is ISO9001 Certification?
ISO9001 certification is part of the ISO 9000 family of standards, which focuses on quality management.
It is not specific to any industry and can be applied to organizations of any size or type.
The certification process involves a series of audits conducted by an external certification body to assess whether an organization meets the standard’s stringent requirements.
Benefits of ISO9001 Certification
There are numerous benefits to obtaining ISO9001 certification.
These include improved customer satisfaction, increased efficiency, and greater employee engagement.
When a company commits to the best quality practices, it can foster a culture of continuous improvement.
Another notable benefit is the potential for increased market share as the certification is often a requirement for tenders and contracts.
It also helps build customer trust, as clients are assured that an organization’s processes are reliable and consistent.
Steps to Obtain ISO9001 Certification
1. Understand the Requirements
The first step to obtaining ISO9001 certification is to thoroughly understand its requirements.
These are outlined in the ISO9001 standard document, which can be purchased from the International Organization for Standardization’s website.
The standard encompasses seven key principles, including customer focus, leadership, engagement of people, and process approach.
2. Conduct a Gap Analysis
Before implementing any changes, perform a gap analysis to identify areas where your current practices diverge from ISO9001 requirements.
This analysis helps pinpoint specific processes or procedures that need enhancement or development.
3. Develop a Plan
Based on the findings from the gap analysis, develop a comprehensive plan to address any shortcomings.
This plan should include clear objectives, timelines, and resources required for implementation.
It’s crucial to have management buy-in at this stage to ensure adequate support and participation.
4. Implement the QMS
Implementation involves setting up the processes and procedures required by ISO9001.
This includes defining roles and responsibilities, establishing quality objectives, and ensuring all staff members are trained in the new protocols.
Documentation is a key component of a QMS.
It should cover all aspects of the system, including process maps, quality manuals, and work instructions.
Ensure that the documentation is accessible and easily understandable for all employees.
5. Conduct Internal Audits
Before applying for certification, conduct internal audits to evaluate the effectiveness of the implemented QMS.
Internal audits help verify that systems are functioning as intended and identify any areas that need further improvement.
Use trained, impartial auditors to perform these audits and encourage a culture of open communication.
The findings from the internal audit should be documented and reviewed, prompting corrective actions where necessary.
6. Management Review
Management review is an important step in the ISO9001 certification process.
During this review, assess the QMS performance, ensure it aligns with business goals, and consider any potential changes.
Top management must demonstrate its commitment to the QMS by being actively involved in the review process.
7. Apply for Certification
Once the QMS is stable, apply for certification through a recognized external certification body.
The certification process will include a thorough audit of your systems, processes, and documentation.
The audit is conducted in two stages.
Stage 1 evaluates your documentation and readiness for an external audit, while Stage 2 is the actual on-site audit assessing implementation.
8. Address Non-Conformities
After the audit, the certification body will report any non-conformities found.
You will need to address these issues and demonstrate corrective actions have been taken before receiving certification.
Promoting Internal Standardization
Achieving ISO9001 is not the end; maintenance and continual improvement are vital to reaping its long-term benefits.
Continuous Improvement
Foster a culture of continuous improvement by regularly reviewing and analyzing processes.
Encourage employees to provide feedback and suggest improvements.
This proactive approach not only maintains compliance but also drives organizational efficiency and innovation.
Employee Training
Ongoing training is essential for maintaining ISO9001 standards.
Ensure all employees, especially new hires, are well-acquainted with the QMS procedures.
Regular training sessions can keep everyone updated on any changes and reinforce the importance of adhering to the standards.
Monitor and Measure
Implement metrics and key performance indicators (KPIs) to monitor the effectiveness of your QMS.
Regular data analysis can identify trends and areas for improvement, allowing the organization to make informed decisions.
Management Commitment
Leadership plays a critical role in promoting and sustaining internal standardization.
Management should actively participate in QMS activities, provide necessary resources, and recognize achievements in quality performance to motivate employees.
In conclusion, obtaining ISO9001 certification and promoting internal standardization is an ongoing journey.
It requires commitment, proper planning, and a culture that prioritizes quality.
The efforts made towards achieving these goals can significantly enhance an organization’s reputation and operational efficiency, leading to long-term success.
資料ダウンロード
QCD調達購買管理クラウド「newji」は、調達購買部門で必要なQCD管理全てを備えた、現場特化型兼クラウド型の今世紀最高の購買管理システムとなります。
ユーザー登録
調達購買業務の効率化だけでなく、システムを導入することで、コスト削減や製品・資材のステータス可視化のほか、属人化していた購買情報の共有化による内部不正防止や統制にも役立ちます。
NEWJI DX
製造業に特化したデジタルトランスフォーメーション(DX)の実現を目指す請負開発型のコンサルティングサービスです。AI、iPaaS、および先端の技術を駆使して、製造プロセスの効率化、業務効率化、チームワーク強化、コスト削減、品質向上を実現します。このサービスは、製造業の課題を深く理解し、それに対する最適なデジタルソリューションを提供することで、企業が持続的な成長とイノベーションを達成できるようサポートします。
オンライン講座
製造業、主に購買・調達部門にお勤めの方々に向けた情報を配信しております。
新任の方やベテランの方、管理職を対象とした幅広いコンテンツをご用意しております。
お問い合わせ
コストダウンが利益に直結する術だと理解していても、なかなか前に進めることができない状況。そんな時は、newjiのコストダウン自動化機能で大きく利益貢献しよう!
(Β版非公開)