- お役立ち記事
- A must-see for the purchasing department! Initiatives to ensure traceability of procured items
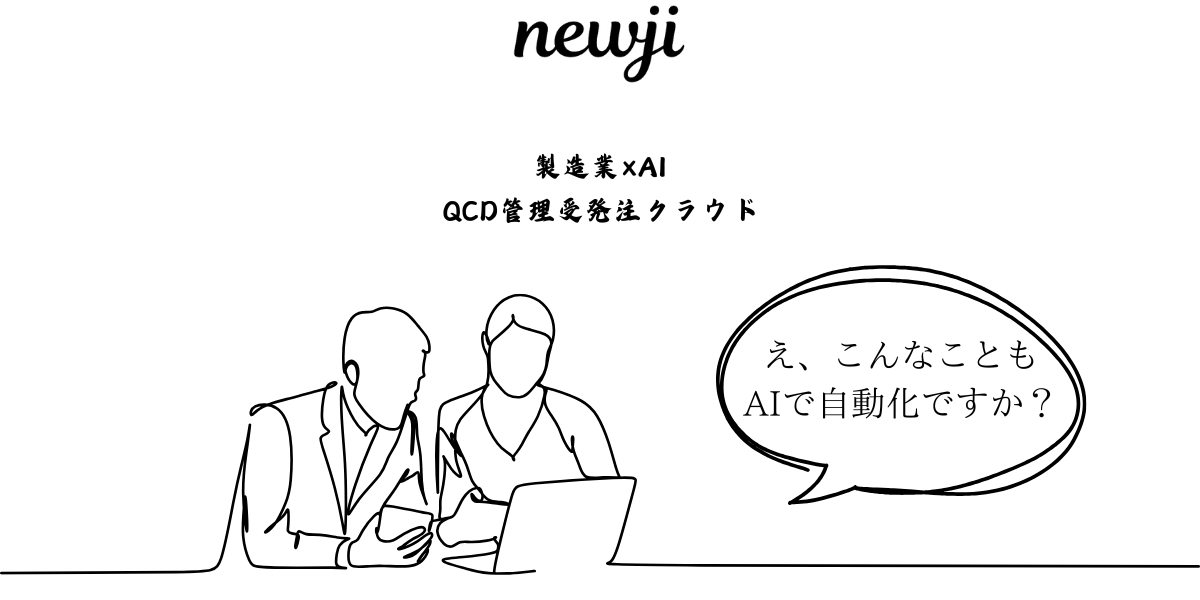
A must-see for the purchasing department! Initiatives to ensure traceability of procured items
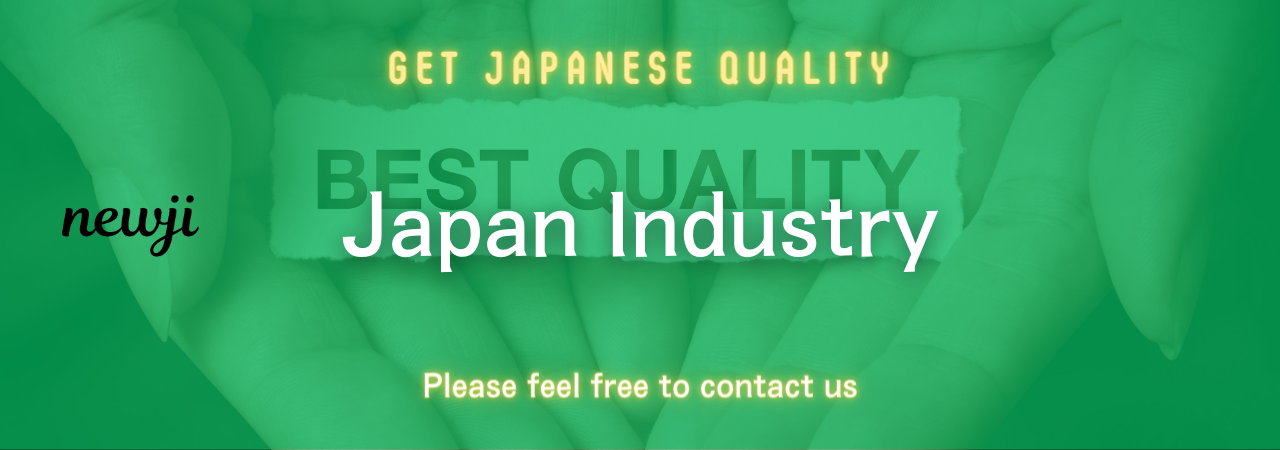
目次
Understanding Traceability in Procurement
Traceability is a crucial aspect of procurement that ensures all procured items can be tracked throughout the supply chain.
This traceability provides information about the origins, journey, and handling of products.
For purchasing departments, maintaining traceability means being able to manage and mitigate risks, work efficiently, and guarantee quality assurance.
The Importance of Traceability
Traceability allows companies to monitor their supply chains closely.
This capability is essential for compliance with legal and industry standards.
By ensuring that procurement processes are traceable, a company can safeguard against potential disruptions or issues that may arise from uncertain or unknown supply chain practices.
Additionally, traceability supports accountability.
Should there be a problem with a product, whether it’s a quality issue or an incident of non-compliance, traceability allows for quick identification and response.
It helps pinpoint which part of the supply chain is responsible, thus streamlining the process of addressing issues.
Traceability also plays a vital role in building trust with customers and stakeholders.
When a company can demonstrate comprehensive traceability practices, it enhances credibility, showing commitment to quality and transparency.
Steps to Ensure Traceability
Implementing effective traceability involves several key steps.
These initiatives are designed to provide a thorough framework for tracking and managing the movement of procured items.
Developing a Traceability System
The first step in ensuring traceability is developing a robust traceability system.
This system should be capable of recording and storing detailed information about each item in the supply chain.
This includes details like the origin of materials, manufacturing processes, and logistics data.
Many companies choose to invest in software solutions that facilitate traceability.
These systems can automatically record and organize data, making it accessible and actionable.
Technology such as blockchain can also be employed for maintaining immutable records of transactions, further enhancing reliability.
Standardizing Documentation
Standardizing documentation processes across suppliers is another important step.
Consistency in documentation ensures that information regarding procured items is accurate and comparable.
Companies should establish clear guidelines and expectations for the documents and data suppliers are required to provide.
Working closely with suppliers to align these standards often involves collaborative efforts to streamline processes.
Creating standard operating procedures for recording and sharing traceability data can significantly reduce errors and discrepancies.
Supplier Collaboration and Training
Collaborating with suppliers is essential for maintaining traceability throughout the supply chain.
Establishing strong relationships with suppliers enables open communication and cooperation.
Providing training and support to suppliers can help them understand the importance of traceability and how to comply with the company’s requirements.
Effective communication and collaboration ensure that suppliers maintain the same commitment to traceability as the purchasing department.
Auditing and Continuous Improvement
Regular audits are necessary to verify traceability measures and implement improvements where necessary.
These audits help ensure that every link in the supply chain upholds the traceability standards set by the company.
Purchasing departments should perform periodic reviews and assessments to identify areas requiring enhancement.
Continuous improvement initiatives can include revising processes and incorporating new technologies that support traceability.
Feedback from these audits can be used to refine training programs for suppliers and improve overall collaboration.
Benefits of Enhanced Traceability
For purchasing departments, investing time and resources into traceability provides several advantages.
Risk Mitigation
Enhanced traceability helps in identifying and addressing risks promptly.
By understanding the flow of materials and components, purchasing departments can quickly spot potential hazards and implement corrective actions before they escalate into larger issues.
Being able to react swiftly to risks ensures that the integrity of the supply chain is not compromised, maintaining the company’s reputation and avoiding costly disruptions.
Improved Quality Control
Traceability directly contributes to better quality control.
With detailed records of each product’s history, companies can conduct thorough quality checks and verify that standards are adhered to at every stage.
If a defect is discovered, traceability facilitates quick action, reducing the impact on production schedules and minimizing financial losses.
It also aids in continuous quality improvement by providing insights into recurring problems and potential areas for process enhancement.
Regulatory Compliance
Adhering to regulatory requirements is crucial for any business, especially those operating in highly regulated industries.
Traceability systems can help meet compliance mandates by maintaining well-documented trails of product history.
These records not only satisfy legal requisites but also aid internal compliance efforts, making audits simpler and more efficient.
Conclusion
Ensuring the traceability of procured items is a vital responsibility of the purchasing department.
By implementing strategic initiatives, departments can achieve comprehensive traceability, leading to greater efficiency, risk management, and quality assurance.
Investing in technology, standardizing processes, fostering supplier collaboration, and committing to continuous improvement are essential steps toward building a robust traceability system.
As industries evolve, maintaining traceability will continue to be a significant competitive advantage, fostering trust and solidifying market positions.
Through diligence and ongoing efforts, purchasing departments can not only meet but exceed expectations and become pivotal players in their company’s success.
資料ダウンロード
QCD調達購買管理クラウド「newji」は、調達購買部門で必要なQCD管理全てを備えた、現場特化型兼クラウド型の今世紀最高の購買管理システムとなります。
ユーザー登録
調達購買業務の効率化だけでなく、システムを導入することで、コスト削減や製品・資材のステータス可視化のほか、属人化していた購買情報の共有化による内部不正防止や統制にも役立ちます。
NEWJI DX
製造業に特化したデジタルトランスフォーメーション(DX)の実現を目指す請負開発型のコンサルティングサービスです。AI、iPaaS、および先端の技術を駆使して、製造プロセスの効率化、業務効率化、チームワーク強化、コスト削減、品質向上を実現します。このサービスは、製造業の課題を深く理解し、それに対する最適なデジタルソリューションを提供することで、企業が持続的な成長とイノベーションを達成できるようサポートします。
オンライン講座
製造業、主に購買・調達部門にお勤めの方々に向けた情報を配信しております。
新任の方やベテランの方、管理職を対象とした幅広いコンテンツをご用意しております。
お問い合わせ
コストダウンが利益に直結する術だと理解していても、なかなか前に進めることができない状況。そんな時は、newjiのコストダウン自動化機能で大きく利益貢献しよう!
(Β版非公開)