- お役立ち記事
- A new approach to cost reduction and procurement efficiency brought about by “common parts”
A new approach to cost reduction and procurement efficiency brought about by “common parts”
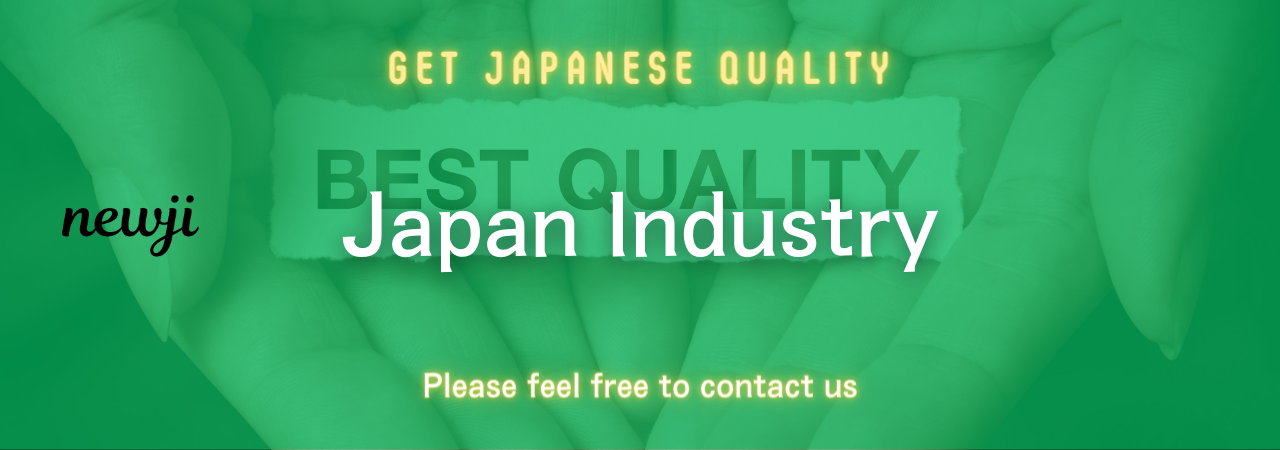
目次
Understanding Common Parts
In the world of manufacturing and production, companies are constantly seeking ways to reduce costs and improve efficiency.
One method that has gained significant attention is the use of “common parts.”
But what exactly are common parts?
Common parts are standardized components used across multiple products or product lines.
By incorporating these interchangeable parts, companies can streamline their production processes and cut down on expenses.
The use of common parts is nothing new, but its importance has grown in recent years as companies strive to stay competitive in an ever-evolving market.
By leveraging common parts, manufacturers can address issues related to supply chain disruptions, fluctuating material costs, and demands for faster turnaround times.
The Benefits of Using Common Parts
There are numerous advantages to adopting common parts in manufacturing and procurement.
Let’s explore some of these benefits and understand how they contribute to cost reduction and increased efficiency.
Cost Reduction
One of the primary benefits of using common parts is cost reduction.
By standardizing components, companies can achieve economies of scale, as purchasing larger quantities of a single part generally reduces the per-unit cost.
Additionally, bulk orders can lead to more favorable pricing negotiations with suppliers.
Moreover, the use of common parts helps minimize inventory costs.
Instead of maintaining separate inventories for distinct parts, a single inventory of common parts suffices for multiple products.
This reduction in inventory variety leads to decreased storage requirements, better stock management, and lower carrying costs.
Procurement Efficiency
Implementing common parts can significantly improve procurement efficiency.
When companies rely on a smaller set of standardized components, the procurement process becomes more streamlined.
Fewer unique parts mean reduced time spent on identifying and sourcing components.
This translates into a more agile and responsive supply chain that can adapt to market changes more quickly.
Additionally, the use of common parts may lead to longer-term relationships with suppliers, allowing for more effective collaboration and communication.
Working closely with suppliers can result in better quality, shorter lead times, and more innovative solutions to address potential production challenges.
Improved Product Quality and Consistency
Standardized parts support higher levels of quality and consistency across products.
By using common parts, companies reduce variability in the production process, which consequently leads to a more consistent output.
This consistency is crucial for maintaining brand reputation and customer satisfaction.
Furthermore, standardized parts are often subjected to more rigorous quality control measures.
By using well-tested and proven components, manufacturers can ensure that their products meet the desired standards of quality and reliability.
Simplified Training and Maintenance
The use of common parts simplifies training processes for assembly line workers and technicians.
Since employees only need to familiarize themselves with a limited set of components, they can quickly learn and execute their tasks with precision.
This results in higher productivity and decreases the likelihood of human errors that can arise from working with numerous unique parts.
Additionally, maintenance becomes more efficient with common parts.
Technicians can easily identify and replace components, reducing downtimes and ensuring smoother production operations.
This ease of maintenance extends not only to manufacturing but also to after-sales services, where repairs and replacements can be carried out with minimal hassle.
Challenges in Implementing Common Parts
While the advantages of common parts are clear, transitioning to their use may present some challenges.
Understanding these challenges is crucial for companies aiming to optimize their production and procurement strategies.
Design Constraints and Innovation Limitations
One potential downside of using common parts is the limitation it may impose on design and innovation.
Relying on standardized components can constrain the creative freedom of product designers and engineers, potentially stifling innovation.
It’s essential for companies to balance standardization with the need for unique features that differentiate their products in the market.
Initial Investment and Coordination
Implementing a common parts strategy may necessitate an initial investment in redesigning products and production lines.
Companies need to carefully plan and coordinate the transition to ensure seamless integration of new components while maintaining existing production levels.
The collaboration required across multiple departments—such as design, engineering, procurement, and production—can pose an organizational challenge.
Clear communication and project management are vital to successfully implement a common parts strategy.
Market Perception
In some cases, the use of common parts may affect how consumers perceive a product’s uniqueness or premium quality.
Companies must effectively communicate the benefits of standardized components, such as reliability and cost-effectiveness, to mitigate potential negative perceptions.
Strategies for Successful Implementation
To successfully reap the benefits of common parts, companies should consider the following strategies:
Thorough Analysis and Planning
A comprehensive analysis of current products, processes, and supply chains is crucial before adopting common parts.
Understanding where common parts can effectively replace unique components and conducting a cost-benefit analysis will guide the decision-making process.
Collaboration with Stakeholders
Engaging stakeholders throughout the organization is essential for developing a cohesive strategy.
This collaboration should involve departments such as design, engineering, procurement, production, and marketing.
Continuous Evaluation and Improvement
Once common parts have been integrated, companies should continuously evaluate the performance and effectiveness of their strategy.
Regularly reviewing cost savings, efficiency gains, and market feedback will help identify areas for improvement and adaptation to evolving trends.
By understanding and addressing these challenges, companies can successfully implement a common parts strategy and enjoy the numerous advantages it offers.
In doing so, they position themselves for long-term success in an increasingly competitive and dynamic marketplace.
資料ダウンロード
QCD調達購買管理クラウド「newji」は、調達購買部門で必要なQCD管理全てを備えた、現場特化型兼クラウド型の今世紀最高の購買管理システムとなります。
ユーザー登録
調達購買業務の効率化だけでなく、システムを導入することで、コスト削減や製品・資材のステータス可視化のほか、属人化していた購買情報の共有化による内部不正防止や統制にも役立ちます。
NEWJI DX
製造業に特化したデジタルトランスフォーメーション(DX)の実現を目指す請負開発型のコンサルティングサービスです。AI、iPaaS、および先端の技術を駆使して、製造プロセスの効率化、業務効率化、チームワーク強化、コスト削減、品質向上を実現します。このサービスは、製造業の課題を深く理解し、それに対する最適なデジタルソリューションを提供することで、企業が持続的な成長とイノベーションを達成できるようサポートします。
オンライン講座
製造業、主に購買・調達部門にお勤めの方々に向けた情報を配信しております。
新任の方やベテランの方、管理職を対象とした幅広いコンテンツをご用意しております。
お問い合わせ
コストダウンが利益に直結する術だと理解していても、なかなか前に進めることができない状況。そんな時は、newjiのコストダウン自動化機能で大きく利益貢献しよう!
(Β版非公開)