- お役立ち記事
- A new contract model to help purchasing departments maintain material supply stability
A new contract model to help purchasing departments maintain material supply stability
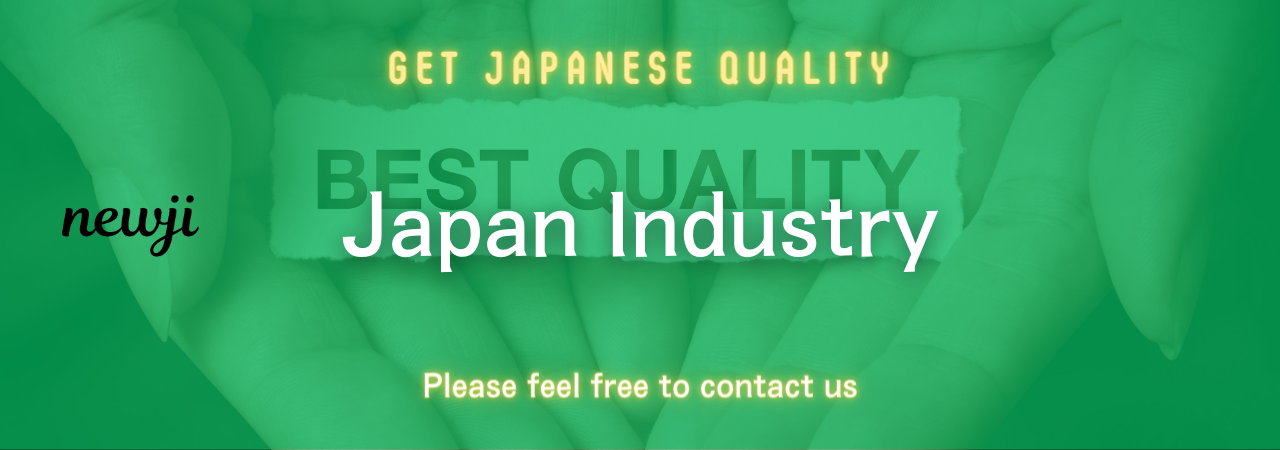
目次
Understanding the New Contract Model
In today’s fast-paced business environment, maintaining a stable supply of materials can be a daunting task for purchasing departments.
To address this issue, a new contract model has been introduced that aims to ensure stability and smooth operations.
This innovative model offers a structured approach, focusing on building strong relationships between buyers and suppliers.
Why Is Supply Stability Important?
Supply stability is crucial for businesses because it prevents disruptions in production and helps maintain customer satisfaction.
When materials are delivered on time and in the right quantity, companies can meet their production schedules without any hiccups.
This reduces downtime and loss of revenue, allowing businesses to operate efficiently and effectively.
The Basics of the New Contract Model
The new contract model places emphasis on clear communication and collaboration between the purchasing department and suppliers.
It involves setting explicit terms and conditions that benefit both parties.
This includes defined delivery schedules, agreed-upon pricing, and quality standards that suppliers must adhere to.
Building Strong Supplier Relationships
One of the key features of the new contract model is its focus on developing and maintaining strong supplier relationships.
By fostering open communication and trust, purchasing departments can work more closely with their suppliers.
This collaboration enables better forecasting of material needs and a more accurate understanding of market conditions.
Flexibility and Adaptability
The contract model is designed to be flexible and adaptable, accommodating fluctuations in demand and supply.
This adaptability is achieved by incorporating clauses that allow for adjustments in quantities and delivery schedules as needed.
Such flexibility helps companies respond to unforeseen changes without disrupting their production lines.
Ensuring Quality and Reliability
Quality assurance is another critical aspect of the new contract model.
The purchasing department sets clear quality standards that suppliers must meet consistently.
Regular audits and performance evaluations help ensure that these standards are maintained, providing reliable and high-quality materials.
Benefits for Purchasing Departments
This contract model offers several advantages to purchasing departments.
Firstly, it reduces the risk of supply chain disruptions.
With clear agreements in place, suppliers are more likely to meet their obligations, minimizing the chances of a breakdown in the supply chain.
Additionally, the model provides cost stability.
Pre-agreed pricing helps protect against market volatility, aiding in budget planning and financial forecasting.
The model also encourages strategic partnerships, allowing purchasing departments to leverage supplier expertise and innovation.
Implementing the New Contract Model
For a successful implementation, businesses need to invest time in training their purchasing teams.
Comprehensive training ensures that team members understand the intricacies of the contract model and how to apply it effectively.
Regular workshops and updates on industry best practices can enhance the team’s capabilities.
Challenges and Considerations
While the new contract model has numerous benefits, it also presents challenges that must be addressed.
One challenge is ensuring that all stakeholders buy into the new approach.
This requires effective communication and demonstrating the long-term benefits of the model.
Another consideration is the need for robust data management systems.
Having real-time access to data allows for better decision-making and more efficient contract management.
Companies must invest in technology that supports data collection and analysis.
Measuring Success
To gauge the effectiveness of the new contract model, companies should establish key performance indicators (KPIs).
These KPIs can include metrics like on-time delivery rates, material quality scores, and supplier performance evaluations.
Regularly reviewing these metrics helps in identifying areas for improvement and ensuring the model continues to deliver the desired outcomes.
The Future of Supply Stability
As industries evolve, the need for stable and reliable material supply will continue to be a priority.
The new contract model provides a framework that purchasing departments can leverage to ensure supply stability.
By adapting to market changes and fostering strong supplier relationships, businesses can position themselves for long-term success.
This forward-thinking approach ultimately benefits companies by fostering innovation, reducing costs, and enhancing competitiveness.
It is clear that the new contract model is not just a trend but a step towards creating a more resilient and efficient supply chain.
資料ダウンロード
QCD調達購買管理クラウド「newji」は、調達購買部門で必要なQCD管理全てを備えた、現場特化型兼クラウド型の今世紀最高の購買管理システムとなります。
ユーザー登録
調達購買業務の効率化だけでなく、システムを導入することで、コスト削減や製品・資材のステータス可視化のほか、属人化していた購買情報の共有化による内部不正防止や統制にも役立ちます。
NEWJI DX
製造業に特化したデジタルトランスフォーメーション(DX)の実現を目指す請負開発型のコンサルティングサービスです。AI、iPaaS、および先端の技術を駆使して、製造プロセスの効率化、業務効率化、チームワーク強化、コスト削減、品質向上を実現します。このサービスは、製造業の課題を深く理解し、それに対する最適なデジタルソリューションを提供することで、企業が持続的な成長とイノベーションを達成できるようサポートします。
オンライン講座
製造業、主に購買・調達部門にお勤めの方々に向けた情報を配信しております。
新任の方やベテランの方、管理職を対象とした幅広いコンテンツをご用意しております。
お問い合わせ
コストダウンが利益に直結する術だと理解していても、なかなか前に進めることができない状況。そんな時は、newjiのコストダウン自動化機能で大きく利益貢献しよう!
(Β版非公開)