- お役立ち記事
- A new perspective for solving logistics issues faced by purchasing departments in manufacturing industries
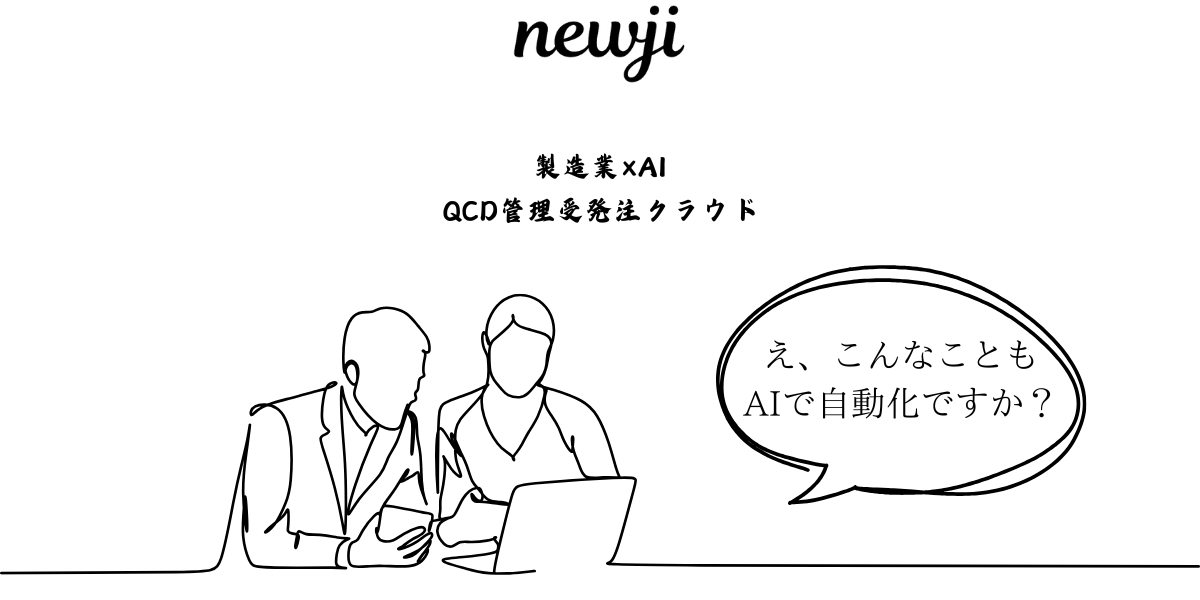
A new perspective for solving logistics issues faced by purchasing departments in manufacturing industries
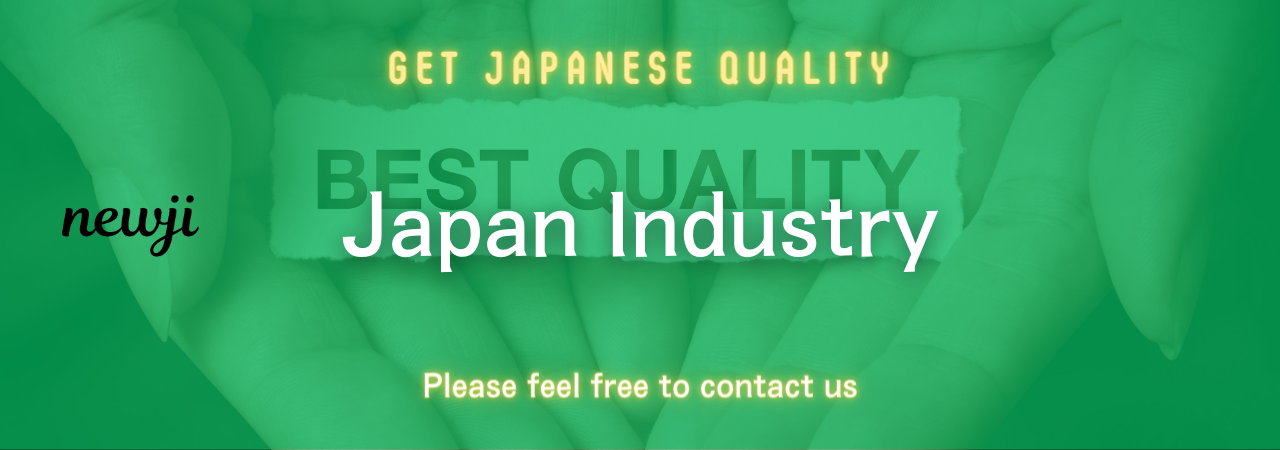
目次
Understanding the Logistics Challenges in Manufacturing
In the modern manufacturing industry, logistics operations have become more complex and integral to the success of a company.
Purchasing departments face numerous challenges as they strive to maintain a seamless flow of materials and products.
In order to solve these logistics issues, it’s essential to understand the key challenges that they face.
One of the primary challenges is the unpredictability of supply and demand.
With global supply chains, unexpected disruptions can occur, leading to delays in production and delivery.
Moreover, changes in consumer demand can impact inventory levels, creating a need for more agile logistics solutions.
Another significant issue is cost management.
Transportation, warehousing, and inventory carrying costs can quickly mount and strain budgets.
Purchasing departments must work to identify cost-saving measures without compromising the quality or timeliness of deliveries.
Complex regulatory environments present additional hurdles.
Compliance with international trade laws, environmental regulations, and safety standards requires diligent oversight.
Failure to comply can result in fines and interruptions, further complicating logistics operations.
Innovative Solutions for Logistics Optimization
To tackle these logistics challenges, manufacturing industries are turning to innovative solutions.
One effective approach is the implementation of advanced technologies such as Artificial Intelligence (AI) and the Internet of Things (IoT).
These technologies enable real-time tracking and data analysis, providing critical insights into supply chain performance.
AI-driven predictive analytics can forecast demand with greater accuracy, helping to avoid shortages or overproduction.
IoT devices can monitor the condition of goods in transit and provide alerts for any potential disruptions.
This enhances visibility and allows purchasing departments to respond quickly to changing situations.
Additionally, blockchain technology offers a transparent and secure method for tracking transactions and verifying the authenticity of goods.
By utilizing blockchain, purchasing departments can reduce the risk of fraud and ensure that supply chains remain efficient and reliable.
Another innovative solution is the integration of automated systems in warehouses.
Automation streamlines operations, reduces labor costs, and minimizes human error.
Automated guided vehicles (AGVs) and robotics can handle repetitive tasks, leaving human workers free to focus on more complex problem-solving.
Enhancing Collaboration and Supplier Relationships
Developing strong collaborations and relationships with suppliers is a crucial step in resolving logistics issues.
Effective communication and collaboration lead to better forecasting and planning, ensuring that all parties are aligned in their objectives.
Supplier relationship management (SRM) software can facilitate these interactions by providing a centralized platform for data sharing.
This ensures that purchasing departments have access to the latest information, helping them make informed decisions.
Furthermore, establishing partnerships with reliable logistics providers is essential.
These providers bring expertise in transportation and warehousing, alleviating some of the pressure on purchasing departments.
Building long-term relationships with suppliers and logistics partners can also lead to more favorable terms and conditions.
Such partnerships can result in shared risk management, reduced costs, and improved service levels, all of which contribute to a more robust logistics operation.
Sustainable Logistics Practices
With growing environmental concerns, manufacturing industries are increasingly prioritizing sustainability in their logistics operations.
Purchasing departments can implement eco-friendly practices to minimize their carbon footprint and promote sustainability.
One way to achieve this is through optimizing transportation routes to reduce fuel consumption.
Utilizing transportation management systems (TMS) can optimize delivery schedules and routes, therefore reducing emissions.
In addition, promoting the use of energy-efficient vehicles and exploring alternative energy sources can contribute to greener logistics.
Purchasing departments can encourage suppliers to adopt similar practices, creating a sustainable supply chain from end to end.
Moreover, investing in sustainable packaging solutions can also make a significant impact.
By reducing packaging waste and using recyclable materials, companies can not only save costs but also foster a positive environmental image.
The Role of Training and Skills Development
To successfully navigate logistics challenges, continuous training and skills development are crucial for purchasing department personnel.
As technologies evolve, employees must regularly update their skills to leverage new tools and methodologies effectively.
Training programs can focus on the latest innovations in supply chain management, data analysis, and regulatory compliance.
By equipping employees with cutting-edge skills, manufacturing companies can enhance their logistics capabilities.
Developing a culture of continuous improvement also encourages employees to identify and implement efficiency gains in their daily operations.
This proactive approach leads to a more dynamic and adaptive logistics function that can readily respond to future challenges.
Conclusion
Addressing logistics challenges in the manufacturing industry requires a multifaceted approach.
By embracing technology, fostering collaboration, prioritizing sustainability, and investing in skills development, purchasing departments can overcome obstacles and improve logistics efficiency.
Implementing these strategies will not only solve current logistics issues but also prepare manufacturing industries for future challenges.
Ultimately, a well-optimized logistics operation supports continued growth and competitiveness in an ever-evolving global market.
資料ダウンロード
QCD調達購買管理クラウド「newji」は、調達購買部門で必要なQCD管理全てを備えた、現場特化型兼クラウド型の今世紀最高の購買管理システムとなります。
ユーザー登録
調達購買業務の効率化だけでなく、システムを導入することで、コスト削減や製品・資材のステータス可視化のほか、属人化していた購買情報の共有化による内部不正防止や統制にも役立ちます。
NEWJI DX
製造業に特化したデジタルトランスフォーメーション(DX)の実現を目指す請負開発型のコンサルティングサービスです。AI、iPaaS、および先端の技術を駆使して、製造プロセスの効率化、業務効率化、チームワーク強化、コスト削減、品質向上を実現します。このサービスは、製造業の課題を深く理解し、それに対する最適なデジタルソリューションを提供することで、企業が持続的な成長とイノベーションを達成できるようサポートします。
オンライン講座
製造業、主に購買・調達部門にお勤めの方々に向けた情報を配信しております。
新任の方やベテランの方、管理職を対象とした幅広いコンテンツをご用意しております。
お問い合わせ
コストダウンが利益に直結する術だと理解していても、なかなか前に進めることができない状況。そんな時は、newjiのコストダウン自動化機能で大きく利益貢献しよう!
(Β版非公開)