- お役立ち記事
- A new risk assessment method for purchasing departments to prevent supply chain disruptions
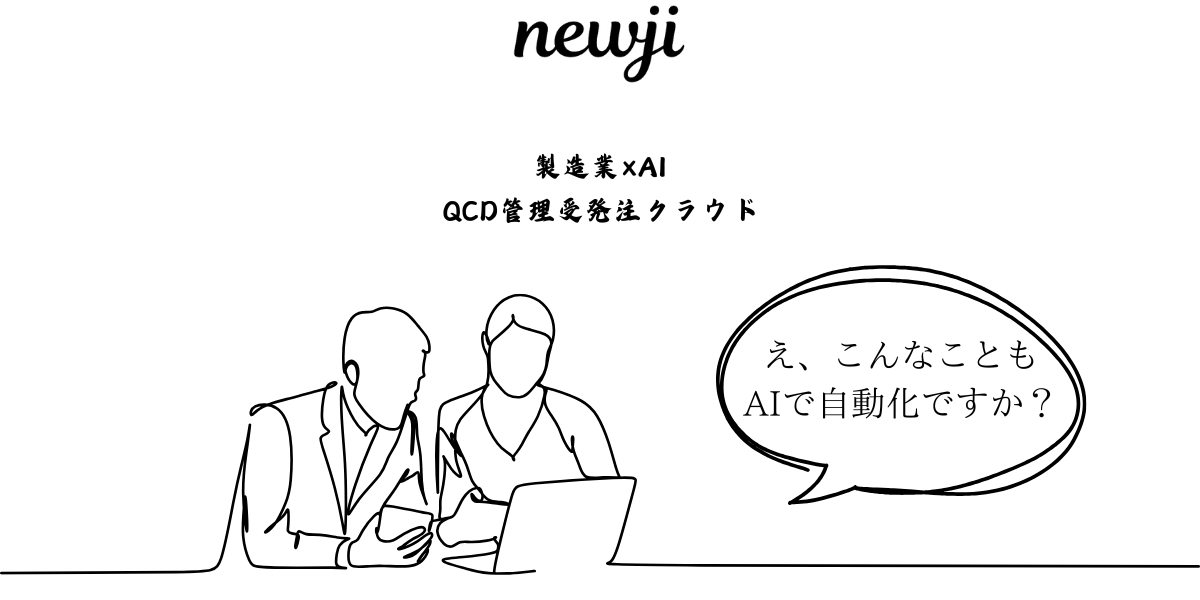
A new risk assessment method for purchasing departments to prevent supply chain disruptions
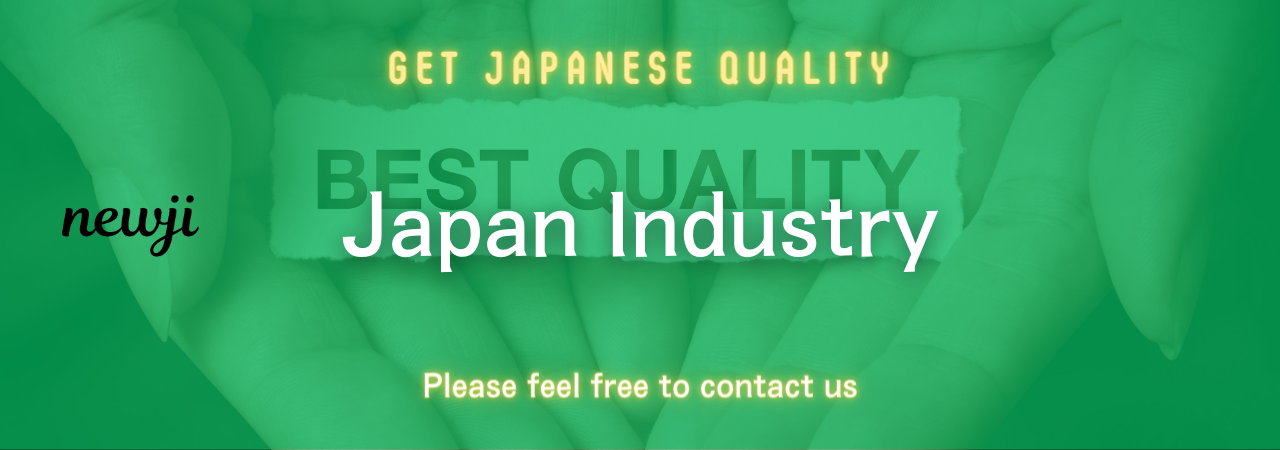
目次
Understanding the Importance of Risk Assessment in Purchasing
In an increasingly complex global market, the purchasing department of any business plays a vital role in maintaining operations smoothly.
Ensuring minimally disrupted supply chains is crucial in preventing costly downtime and maintaining overall productivity.
A modern, thorough risk assessment method is fundamental in achieving this goal.
The purchasing department must anticipate potential risks and strategize accordingly to avoid supply chain disruptions.
These risks can range from logistical issues, supplier reliability, political instability, and even natural disasters.
A comprehensive risk assessment empowers the company to respond effectively to these challenges.
The Need for a New Risk Assessment Method
Existing risk assessment methods are often outdated, with many failing to adapt to the rapid changes and trends within global markets.
An updated approach can ensure more effective identification, analysis, and mitigation of potential risks.
Consequently, purchasing departments need a fresh, dynamic method that aligns with the current global economic environment.
The new risk assessment method should be proactive rather than reactive, allowing purchasing teams to predict potential disruptions before they become critical issues.
This proactive model ensures a business’s resilience against future challenges, helping to maintain uninterrupted operations.
Identifying Key Risks
An effective risk assessment method starts by identifying potential risks.
First, companies must understand their supply chain structure and pinpoint areas most susceptible to disruption.
Key risks include those arising from supplier issues, transportation problems, local or global economic changes, and sudden shifts in consumer demand.
Supplier risks involve evaluating the reliability and stability of suppliers.
This includes considering factors like financial stability, geopolitical location, and track record for meeting deadlines.
Suppliers should be vetted to ensure they have contingency plans for possible disruptions.
Transportation risks include potential delays caused by logistical setbacks, such as port congestions or transportation strikes.
Effective risk assessment involves mapping out alternative routes and having backup plans in place.
This reduces dependence on a single transportation path, offering flexibility and reducing potential delays.
Tools and Technologies for Better Risk Assessment
Incorporating technology into risk assessment is crucial for modern purchasing departments.
Advancements in digital tools and data analytics offer new ways to monitor and predict risks, providing real-time insights that inform better decision-making.
Utilizing software platforms can automate risk assessment processes, quickly and efficiently analyzing large volumes of data from multiple sources.
Predictive analytics, powered by artificial intelligence and machine learning, can forecast potential supply chain disruptions by identifying patterns and trends.
These insights enable purchasing departments to adjust strategies in advance, minimizing potential risks before they materialize.
Implementing the New Method
Once a new risk assessment method is established, the next crucial step is implementation.
Purchasing departments must integrate the new approach into their processes, ensuring that staff is trained and ready to utilize new tools effectively.
This includes facilitating workshops and training sessions to familiarize stakeholders with new technologies and methodologies.
Regular reviews and updates are essential, as supply chain environments are continually evolving.
Purchasing departments should consistently refine their risk assessment methods to reflect any shifts in the market or within their own operations.
Creating a Culture of Preparedness
Beyond technical skills and digital tools, a culture of preparedness within the purchasing department is invaluable.
Encouraging proactive behavior and fostering open communication channels can heighten responsiveness to potential risks.
Establishing cross-departmental collaboration ensures that knowledge and strategies are shared throughout the organization, enhancing overall resilience.
Part of this culture involves conducting regular risk assessment drills.
Simulating various risk scenarios helps the purchasing department and other relevant teams remain prepared for potential disruptions.
These exercises familiarize staff with contingency plans, ensuring a swift, coordinated response when real threats arise.
Conclusion
In today’s ever-changing global market, a robust and dynamic risk assessment method is essential for purchasing departments to maintain seamless operations and prevent supply chain disruptions.
By leveraging advanced technologies, identifying key risks, and fostering a culture of preparedness, businesses can safeguard their supply chains effectively.
Implementing an updated risk assessment method ensures that purchasing departments stay ahead in identifying and managing potential threats, contributing significantly to the overall resilience and success of the organization.
資料ダウンロード
QCD調達購買管理クラウド「newji」は、調達購買部門で必要なQCD管理全てを備えた、現場特化型兼クラウド型の今世紀最高の購買管理システムとなります。
ユーザー登録
調達購買業務の効率化だけでなく、システムを導入することで、コスト削減や製品・資材のステータス可視化のほか、属人化していた購買情報の共有化による内部不正防止や統制にも役立ちます。
NEWJI DX
製造業に特化したデジタルトランスフォーメーション(DX)の実現を目指す請負開発型のコンサルティングサービスです。AI、iPaaS、および先端の技術を駆使して、製造プロセスの効率化、業務効率化、チームワーク強化、コスト削減、品質向上を実現します。このサービスは、製造業の課題を深く理解し、それに対する最適なデジタルソリューションを提供することで、企業が持続的な成長とイノベーションを達成できるようサポートします。
オンライン講座
製造業、主に購買・調達部門にお勤めの方々に向けた情報を配信しております。
新任の方やベテランの方、管理職を対象とした幅広いコンテンツをご用意しております。
お問い合わせ
コストダウンが利益に直結する術だと理解していても、なかなか前に進めることができない状況。そんな時は、newjiのコストダウン自動化機能で大きく利益貢献しよう!
(Β版非公開)