- お役立ち記事
- A New Start in a New Factory: Transforming for the Future
A New Start in a New Factory: Transforming for the Future
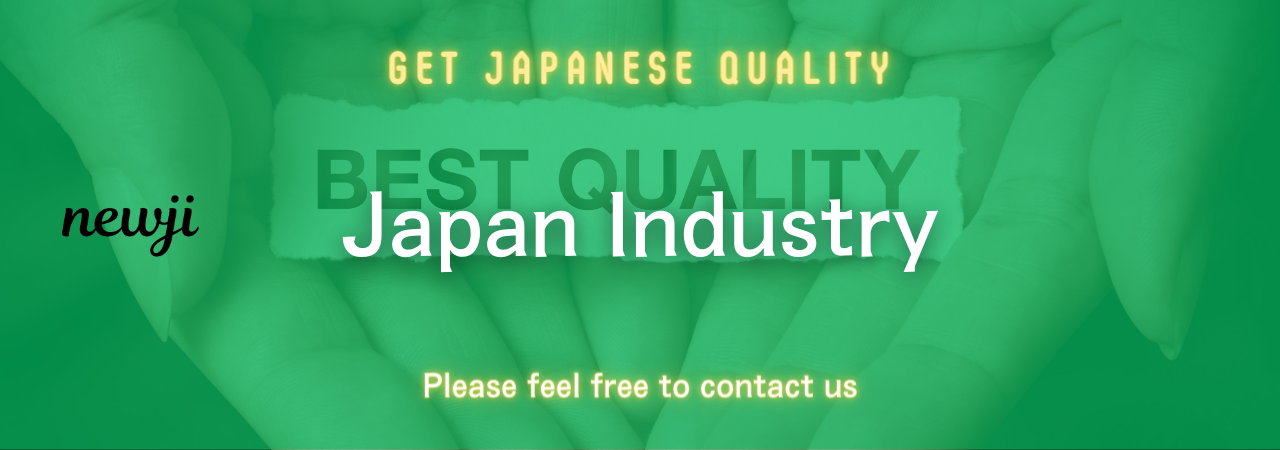
When a factory opens its doors for the first time, it marks the beginning of a new chapter for the business and its employees.
The transformation process can be both exciting and challenging.
In this article, we will explore the journey of a factory moving into a new facility and the steps involved in making this transition successful.
We will cover everything from planning and preparation to execution and employee adaptation.
目次
Planning for the Big Move
Setting Clear Goals
The first step in any successful factory relocation is to set clear and achievable goals.
Establish what the new facility aims to accomplish compared to the old.
This could include improving manufacturing efficiency, increasing production capacity, or adopting new technologies.
By setting measurable objectives, the company can track its progress and ensure the move meets its strategic needs.
Assessing the Current Situation
Before making any drastic changes, assess the current operations.
Identify what is working well and what aspects need improvement.
This will help in making informed decisions about the new factory’s design, layout, and equipment needs.
Conducting a SWOT analysis (Strengths, Weaknesses, Opportunities, Threats) can provide valuable insights.
Involving the Right Team
Relocating a factory involves numerous tasks, requiring the expertise of a diverse team.
Involve key stakeholders from various departments, such as production, engineering, logistics, and human resources.
Creating a project team with clear roles and responsibilities ensures that no crucial aspect is overlooked.
Designing the New Facility
Optimizing Layout
One of the main advantages of moving into a new factory is the opportunity to design a more efficient layout.
Consider lean manufacturing principles to minimize waste and streamline processes.
Positioning machinery and workstations in a logical flow can significantly enhance productivity.
Investing in Technology
A new facility provides the perfect opportunity to invest in state-of-the-art technology.
From advanced machinery to automation and AI-driven solutions, the right technology can revolutionize operations.
Ensure the new factory is equipped to integrate these advancements seamlessly.
Sustainability Matters
In today’s world, sustainability is a significant consideration.
Design the new factory with eco-friendly practices in mind.
This can include energy-efficient lighting and machinery, as well as waste reduction initiatives.
Not only does this benefit the environment, but it can also result in cost savings.
Executing the Move
Detailed Timeline
A well-planned timeline is crucial for a smooth transition.
Break down the move into manageable phases, from machinery disassembly to transportation and reassembly.
Ensure clear communication of deadlines and responsibilities.
This structured approach minimizes disruptions and ensures a seamless operation.
Minimizing Downtime
One of the primary concerns during relocation is minimizing production downtime.
Implement a phased move strategy where parts of the operation continue while others relocate.
Consider building a buffer stock to meet customer demands during this transition period.
Ensuring Safety
Safety should always be a top priority.
Clearly mark hazard areas and ensure the new factory complies with all safety regulations.
Conduct comprehensive safety training for all employees, focusing on the new layout and machinery.
Adapting to the New Environment
Employee Training
Even the best-designed factory would face challenges without a well-trained workforce.
Provide extensive training on new machinery and processes.
Offer ongoing support to help employees adapt to the changes and feel confident in their roles.
Building a Positive Culture
A new factory can symbolize a fresh start for company culture as well.
Foster an environment that encourages collaboration and innovation.
Recognize and reward employees’ contributions to build a motivated and engaged team.
Feedback Mechanisms
An open feedback loop is crucial for continued improvement.
Encourage employees to share their experiences and suggestions.
Regularly review feedback and implement changes where feasible.
This shows that employees’ voices are valued and can lead to better operational strategies.
Looking Ahead
Continuous Improvement
The move to a new factory marks the beginning, not the end, of a journey.
Embrace a culture of continuous improvement.
Regularly review processes and implement enhancements to stay competitive in the market.
Monitoring Progress
Consistently monitor the progress against the initial goals set for the move.
Use key performance indicators (KPIs) to gauge success.
Adjust strategies as needed to ensure the new facility continues to meet or exceed expectations.
Future Expansion
Always keep future growth in mind.
Design the new factory with scalability in mind, allowing for easy expansion as the business grows.
This forward-thinking approach ensures the facility can adapt to future demands.
In conclusion, moving to a new factory is a monumental task that requires careful planning and execution.
By setting clear goals, optimizing the new facility, and ensuring seamless execution, a business can turn this challenge into an opportunity for growth and innovation.
Most importantly, involving and supporting employees throughout this transition ensures smooth adaptation and long-term success.
資料ダウンロード
QCD調達購買管理クラウド「newji」は、調達購買部門で必要なQCD管理全てを備えた、現場特化型兼クラウド型の今世紀最高の購買管理システムとなります。
ユーザー登録
調達購買業務の効率化だけでなく、システムを導入することで、コスト削減や製品・資材のステータス可視化のほか、属人化していた購買情報の共有化による内部不正防止や統制にも役立ちます。
NEWJI DX
製造業に特化したデジタルトランスフォーメーション(DX)の実現を目指す請負開発型のコンサルティングサービスです。AI、iPaaS、および先端の技術を駆使して、製造プロセスの効率化、業務効率化、チームワーク強化、コスト削減、品質向上を実現します。このサービスは、製造業の課題を深く理解し、それに対する最適なデジタルソリューションを提供することで、企業が持続的な成長とイノベーションを達成できるようサポートします。
オンライン講座
製造業、主に購買・調達部門にお勤めの方々に向けた情報を配信しております。
新任の方やベテランの方、管理職を対象とした幅広いコンテンツをご用意しております。
お問い合わせ
コストダウンが利益に直結する術だと理解していても、なかなか前に進めることができない状況。そんな時は、newjiのコストダウン自動化機能で大きく利益貢献しよう!
(Β版非公開)