- お役立ち記事
- A new way for purchasing departments to evaluate the safety of outsourcing companies and manage suppliers
月間76,176名の
製造業ご担当者様が閲覧しています*
*2025年3月31日現在のGoogle Analyticsのデータより
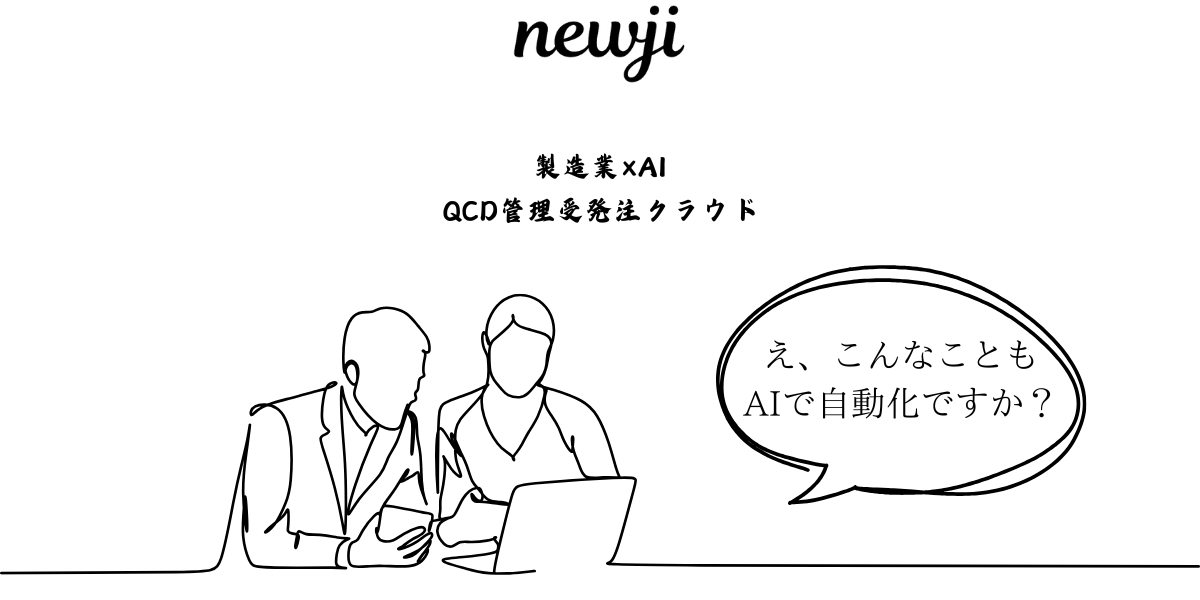
A new way for purchasing departments to evaluate the safety of outsourcing companies and manage suppliers
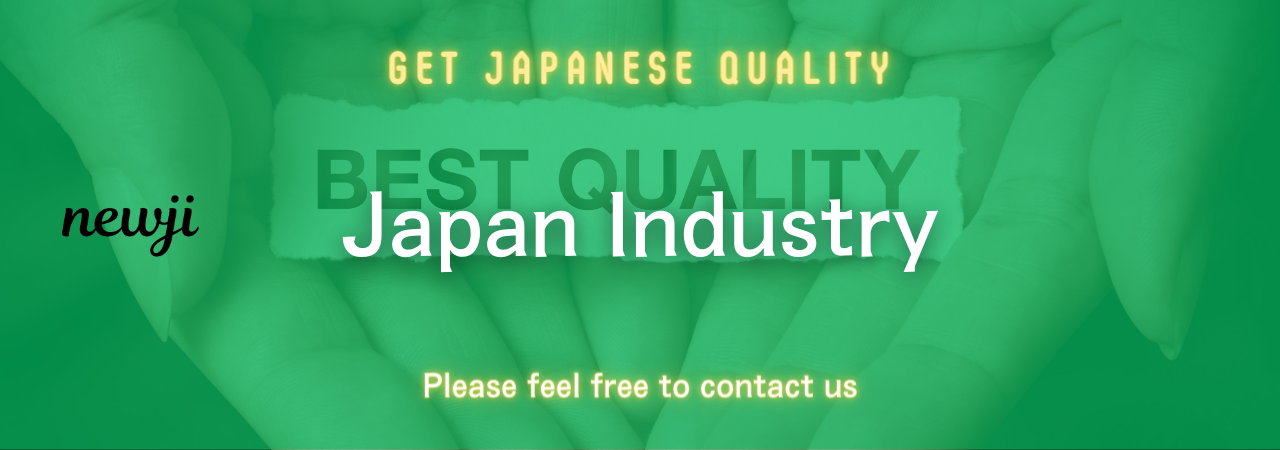
目次
Understanding the Importance of Supplier Safety Evaluation
In today’s fast-paced business environment, outsourcing has become a crucial strategy for many companies looking to reduce costs and improve efficiency.
However, one major challenge that purchasing departments face is evaluating the safety of outsourcing companies.
Ensuring supplier safety is vital as it helps mitigate risks such as data breaches, compliance violations, and financial losses.
By carefully assessing the safety of potential outsourcing partners, companies can build strong, sustainable relationships that support long-term success.
Steps to Evaluate the Safety of Outsourcing Companies
Step 1: Define Safety Criteria
The first step in evaluating the safety of outsourcing companies is to define clear safety criteria.
This involves identifying all the potential risks associated with outsourcing operations, such as cybersecurity threats, regulatory compliance issues, and quality control challenges.
Once these risks are identified, the purchasing department can establish criteria to measure each aspect.
For example, cybersecurity criteria might include the company’s data protection policies, availability of security training for employees, and recent audits or certifications.
Step 2: Conduct Thorough Research
Once safety criteria are established, it is essential to conduct thorough research on potential outsourcing partners.
This research should cover the company’s reputation in the industry, track record of safety incidents, and feedback from other clients.
A good starting point is to check online reviews, news articles, and published reports to gather unbiased opinions.
Furthermore, reaching out to professional networks and industry associations for recommendations or warnings can provide valuable insights into the reliability of a supplier.
Step 3: Request Detailed Safety Documentation
When considering an outsourcing company, request detailed safety documentation to verify their safety practices.
This includes documents like safety protocols, accident logs, and emergency response plans.
Reviewing these documents can provide insights into the company’s commitment to safety and their ability to manage risks effectively.
It may also highlight areas where improvements are needed, allowing the purchasing department to proactively address potential issues.
Step 4: Evaluate Financial Stability
Financial stability is a critical aspect of supplier safety.
An unstable financial situation might lead to disrupted services and compromised safety standards.
Therefore, evaluating the financial health of potential outsourcing companies is essential.
This can involve reviewing financial statements, credit ratings, and recent business developments to ensure the supplier can sustain operations and adhere to safety commitments.
Ongoing Safety Management and Monitoring
Maintain Regular Communication
After selecting a safe outsourcing company, maintaining regular communication is key to ongoing safety management.
Establishing open communication channels allows for timely updates on any changes in safety practices or potential risks.
Regular meetings, both virtual and in-person, can help strengthen the partnership and ensure that safety remains a top priority.
Conduct Regular Audits
Regular audits of the outsourcing company’s operations are essential for verifying compliance with safety standards.
Scheduled audits should review compliance with industry regulations, inspection of facilities, and assessment of potential risks.
Unscheduled audits can also be beneficial, as they provide a more accurate picture of daily operations and potential safety lapses.
Establish a Performance Feedback System
Establishing a performance feedback system with suppliers can drive continuous improvement in safety practices.
Providing constructive feedback on safety performance encourages the outsourcing company to address weak points promptly.
Moreover, recognizing outstanding safety achievements can create a culture of excellence and motivate suppliers to maintain high safety standards.
Leveraging Technology for Enhanced Safety Management
Implement Supplier Management Software
Technology can significantly simplify the process of evaluating and managing supplier safety.
Supplier management software offers a centralized platform to store, track, and analyze supplier data, streamlining assessments and audits.
This software can automate tracking of certification renewals, performance metrics, and flag potential safety concerns, providing purchasing departments with timely insights.
Use Data Analytics for Risk Assessment
Data analytics tools can enhance risk assessment by identifying patterns in supplier safety performance and predicting potential areas of concern.
By analyzing historical data, purchasing departments can make informed decisions and take proactive measures to mitigate risks before they escalate.
Embrace Cybersecurity Solutions
Cybersecurity is an integral aspect of supplier safety, especially as more operations are digitized.
Leveraging advanced cybersecurity solutions such as firewalls, encryption, and two-factor authentication can protect sensitive data from unauthorized access.
Furthermore, encouraging suppliers to invest in robust cybersecurity measures reinforces a company’s commitment to safety.
Conclusion
Evaluating and managing the safety of outsourcing companies is crucial for purchasing departments to ensure that their operations remain secure and efficient.
By following a structured approach that includes defining safety criteria, conducting thorough research, and leveraging technology, companies can mitigate risks and foster long-lasting supplier relationships.
Continual safety management through regular audits and feedback systems will promote a culture of safety and ensure that outsourcing partners align with the company’s safety expectations.
Ultimately, these efforts help safeguard the company’s reputation and contribute to sustainable business growth.
資料ダウンロード
QCD管理受発注クラウド「newji」は、受発注部門で必要なQCD管理全てを備えた、現場特化型兼クラウド型の今世紀最高の受発注管理システムとなります。
ユーザー登録
受発注業務の効率化だけでなく、システムを導入することで、コスト削減や製品・資材のステータス可視化のほか、属人化していた受発注情報の共有化による内部不正防止や統制にも役立ちます。
NEWJI DX
製造業に特化したデジタルトランスフォーメーション(DX)の実現を目指す請負開発型のコンサルティングサービスです。AI、iPaaS、および先端の技術を駆使して、製造プロセスの効率化、業務効率化、チームワーク強化、コスト削減、品質向上を実現します。このサービスは、製造業の課題を深く理解し、それに対する最適なデジタルソリューションを提供することで、企業が持続的な成長とイノベーションを達成できるようサポートします。
製造業ニュース解説
製造業、主に購買・調達部門にお勤めの方々に向けた情報を配信しております。
新任の方やベテランの方、管理職を対象とした幅広いコンテンツをご用意しております。
お問い合わせ
コストダウンが利益に直結する術だと理解していても、なかなか前に進めることができない状況。そんな時は、newjiのコストダウン自動化機能で大きく利益貢献しよう!
(β版非公開)