- お役立ち記事
- A Practical Guide for SMEs to Succeed in Micro Hole Machining
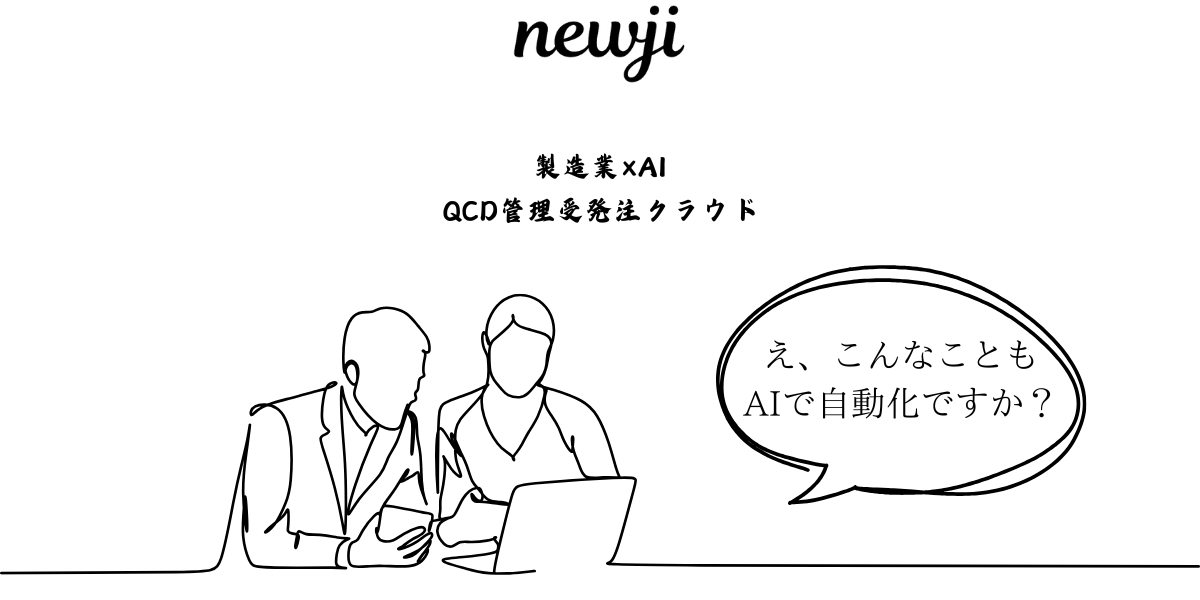
A Practical Guide for SMEs to Succeed in Micro Hole Machining
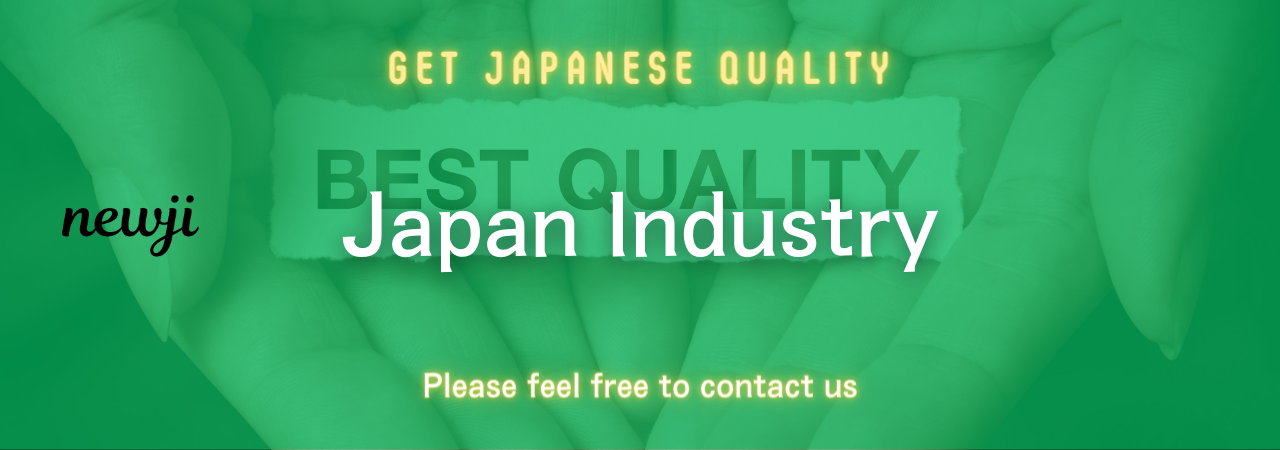
Micro hole machining is a specialized manufacturing process that involves creating extremely small holes in various materials.
These holes can be smaller than 1 millimeter in diameter and are used in numerous industries, from electronics to aerospace.
For small and medium-sized enterprises (SMEs), mastering this process can offer a competitive advantage.
This guide aims to provide practical insights into how SMEs can succeed in micro hole machining.
目次
Understanding Micro Hole Machining
Micro hole machining involves several advanced techniques, each suited to different materials and applications.
Some of the most common methods include laser drilling, electrical discharge machining (EDM), and mechanical drilling.
Each technique has its own set of advantages and drawbacks, making it crucial to select the one that best matches your specific requirements.
Laser Drilling
Laser drilling utilizes a focused laser beam to create precise holes.
This method is highly efficient for hard and brittle materials like ceramics and certain metals.
The main advantage is the high precision and speed it offers, making it suitable for mass production.
However, it can be expensive due to the cost of laser machinery and maintenance.
Electrical Discharge Machining (EDM)
EDM uses electrical discharges or sparks to erode material, forming holes.
It is particularly effective for hard metals and alloys that are difficult to machine using traditional methods.
The accuracy of EDM is unparalleled, but it is a slower process compared to laser drilling.
It’s essential to consider the trade-offs between speed and precision when using EDM.
Mechanical Drilling
Mechanical drilling employs miniature drills and reamers to create fine holes.
This is the most traditional method and is generally less expensive than laser or EDM.
However, it may not achieve the same level of precision and is not suitable for extremely hard materials.
Proper tooling and equipment maintenance are vital to achieving the best results with mechanical drilling.
Choosing the Right Equipment
Selecting the appropriate machinery is a critical step for any SMEs looking to venture into micro hole machining.
Make sure to consider factors like the type of material you’ll be working with, the required hole size, and the volume of production.
It’s also important to look at the initial investment costs and ongoing maintenance requirements.
Laser Drilling Machines
When opting for laser drilling, you’ll need a high-quality laser machine capable of producing concentrated beams.
These machines often come with advanced control systems for precise operation.
While the upfront cost can be high, the efficiency and quality of output may justify the investment for large-scale operations.
EDM Machines
EDM machines are specialized pieces of equipment that use electrical discharges to create holes.
Features to look for include automated controls, high-speed capabilities, and user-friendly interfaces.
Although EDM machines can be costly, they offer exceptional precision, making them ideal for specialized applications.
Mechanical Drills
Mechanical drilling machines are more conventional and generally easier to operate.
They require high-quality drill bits and reamers tailored for micro machining.
Regular maintenance and calibration are key to extending the life of these machines and ensuring high-quality output.
Material Considerations
Different materials respond differently to various micro hole machining techniques.
Understanding the properties of the material you’re working with is crucial to selecting the most effective method.
Metals
Metals like stainless steel, titanium, and aluminum are common in industrial applications.
Laser drilling and EDM are generally more effective for these materials due to their hardness and durability.
Mechanical drilling can also be used, but it may require specialized drill bits to achieve the desired results.
Ceramics
Ceramic materials are brittle and require a delicate approach.
Laser drilling is often the best choice for ceramics, as it minimizes the risk of cracking.
Mechanical drilling is generally not recommended due to the high likelihood of material damage.
Polymers
Polymers are softer and more flexible than metals and ceramics.
Mechanical drilling can be effective, but care must be taken to avoid deformation.
Laser drilling can also be used, but the heat generated may cause melting or warping.
It’s essential to carefully control the drilling parameters when working with polymers.
Quality Control Measures
Ensuring the quality of micro hole machining is vital for maintaining customer satisfaction and meeting industry standards.
Implementing rigorous quality control measures can help identify and rectify issues early in the production process.
Inspection Techniques
Quality inspection for micro holes involves various techniques like optical microscopy, scanning electron microscopy (SEM), and laser profilometry.
These methods provide detailed insights into hole dimensions, surface quality, and any potential defects.
Automated Inspection Systems
Automated inspection systems can significantly improve the accuracy and efficiency of quality control.
These systems use advanced imaging and laser technologies to perform real-time inspections, ensuring each hole meets the required specifications.
Skilled Workforce
A skilled workforce is essential for the successful implementation of micro hole machining.
Specialized training programs and certifications can help employees stay updated on the latest techniques and equipment.
Training Programs
Investing in comprehensive training programs ensures that your team is skilled in operating and maintaining advanced machinery.
These programs can be conducted in-house or through specialized training institutes.
Certifications
Certifications from recognized industry bodies can enhance the credibility of your workforce and your business.
These certifications often involve rigorous testing and provide a benchmark for skill levels in micro hole machining.
Cost Management
Managing costs is crucial for SMEs to remain competitive.
From equipment purchase to operational expenses, every aspect should be carefully budgeted and monitored.
Initial Investment
The initial cost can be substantial, especially when purchasing high-end machinery.
However, the long-term benefits in terms of efficiency and quality often outweigh the initial expenditure.
Operational Costs
Operational costs include maintenance, tooling, and labor.
Regular maintenance can help reduce downtime and extend the lifespan of your equipment, thereby lowering overall costs.
Micro hole machining offers numerous opportunities for SMEs in various industries.
By understanding the different techniques, choosing the right equipment, and implementing robust quality control measures, SMEs can position themselves for success.
Investing in a skilled workforce and managing costs effectively can further enhance competitiveness and ensure long-term sustainability.
資料ダウンロード
QCD調達購買管理クラウド「newji」は、調達購買部門で必要なQCD管理全てを備えた、現場特化型兼クラウド型の今世紀最高の購買管理システムとなります。
ユーザー登録
調達購買業務の効率化だけでなく、システムを導入することで、コスト削減や製品・資材のステータス可視化のほか、属人化していた購買情報の共有化による内部不正防止や統制にも役立ちます。
NEWJI DX
製造業に特化したデジタルトランスフォーメーション(DX)の実現を目指す請負開発型のコンサルティングサービスです。AI、iPaaS、および先端の技術を駆使して、製造プロセスの効率化、業務効率化、チームワーク強化、コスト削減、品質向上を実現します。このサービスは、製造業の課題を深く理解し、それに対する最適なデジタルソリューションを提供することで、企業が持続的な成長とイノベーションを達成できるようサポートします。
オンライン講座
製造業、主に購買・調達部門にお勤めの方々に向けた情報を配信しております。
新任の方やベテランの方、管理職を対象とした幅広いコンテンツをご用意しております。
お問い合わせ
コストダウンが利益に直結する術だと理解していても、なかなか前に進めることができない状況。そんな時は、newjiのコストダウン自動化機能で大きく利益貢献しよう!
(Β版非公開)