- お役立ち記事
- A Practical Guide to Burr Prevention for SMEs
月間76,176名の
製造業ご担当者様が閲覧しています*
*2025年3月31日現在のGoogle Analyticsのデータより
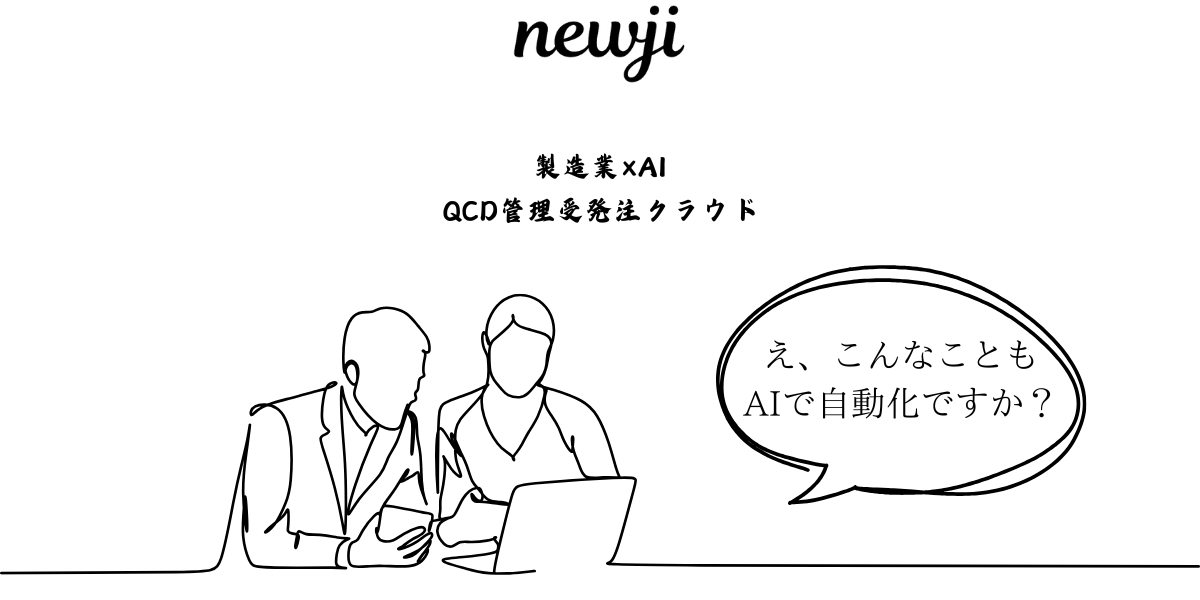
A Practical Guide to Burr Prevention for SMEs
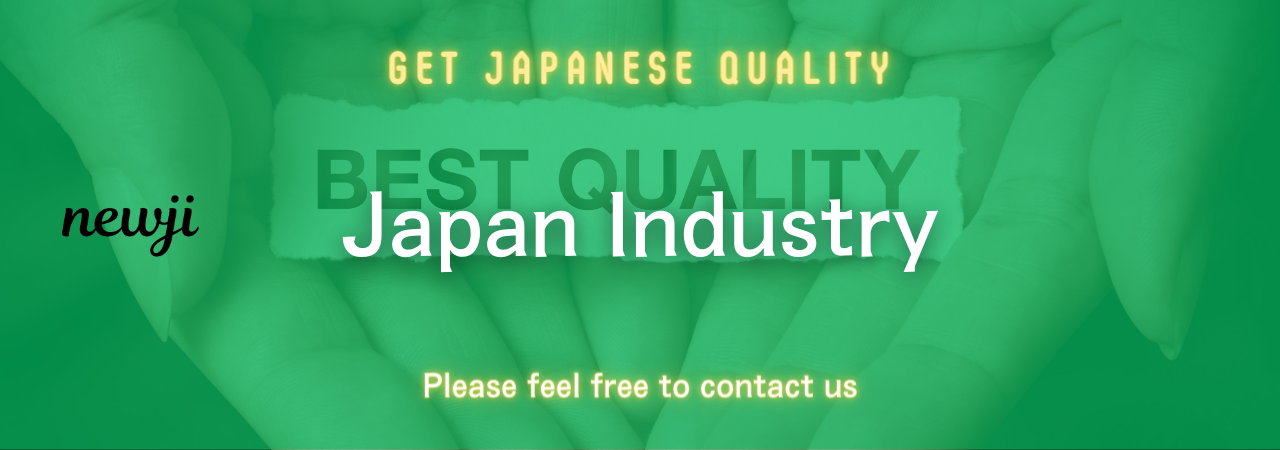
目次
Understanding Burrs in Manufacturing
In the world of manufacturing, burrs are unwanted rough edges or protrusions formed during the machining process.
They can occur in various shapes, often appearing as sharp fragments or thin splinters on metal, plastic, or other materials.
For small and medium-sized enterprises (SMEs), understanding burrs and their implications is vital for maintaining product quality and ensuring operational efficiency.
Burrs can originate from multiple machining activities, such as drilling, milling, or stamping.
When these processes are not precisely controlled, the edges of the workpiece might develop unwanted burrs.
These imperfections not only impact the aesthetic appeal of the product but can also influence its functionality and safety.
Why Burr Prevention Matters
For SMEs, preventing burrs is critical for several reasons.
First and foremost, burrs can lead to product defects that might compromise the quality and performance of the final product.
Customers expect high-quality items, and any rough or unsightly edges can lead to dissatisfaction, complaints, or returns, ultimately impacting your brand reputation.
Moreover, burrs can affect the assembly process, leading to misalignments and fitting issues.
Parts may not slot or fit together as intended, causing delays in production as employees attempt to rectify these issues.
Additionally, burrs pose safety hazards to workers.
Sharp edges or tiny metal splinters can cause injuries if not properly handled, leading to potential health risks and liability concerns.
Costs Associated with Burrs
The financial implications for SMEs dealing with burrs are notable.
Dealing with defective parts often requires additional time and resources—not just in terms of scrap or rework costs, but also in terms of labor and productivity losses.
Moreover, if an SME has a recurring issue with burrs, it might need to invest in additional quality control measures or more expensive equipment to mitigate the problem.
If burrs cause customer dissatisfaction, there could be substantial costs associated with recalls, repairs, or return shipments.
Plus, this can damage the business’s reputation, which is an asset that takes years to build but can be quickly tarnished by quality issues.
Effective Burr Prevention Techniques
To effectively prevent burrs in your manufacturing processes, consider implementing comprehensive strategies and using the right tools and technologies.
Choosing the Right Tools and Equipment
Using high-quality tools that are specifically designed for the materials you’re working with is a crucial first step in burr prevention.
Ensure that tools are sharp and well-maintained, as dull tools are more likely to produce burrs.
Investing in advanced machinery that offers precision and better control can also minimize burr formation.
Machines that provide accurate feeds and speeds appropriate for particular materials will reduce the risk of burrs forming.
Optimizing Machining Processes
Review and refine your machining processes to identify where burrs are most likely to occur.
Adjust the speeds, feeds, and depths of cuts to minimize edge stress and reduce burr formation.
Experiment with different cutting tools and angles to see which combination results in the least amount of burr.
Also, consider implementing deburring processes directly on your production line, such as using brushes, magnetic systems, or chemical deburring methods to remove burrs as parts are manufactured.
This step ensures a smoother flow of parts through the production process with immediate quality checks.
Employee Training and Consciousness
Educate your staff about the causes and consequences of burrs and provide training on the best practices for preventing and addressing them.
A skilled workforce familiar with burr management techniques can significantly reduce the presence of burrs on the production line.
Empower your employees to identify potential burr issues and encourage them to propose improvements or flag repetitive problems that may suggest process redesigns or modifications.
Design Considerations to Minimize Burrs
The design stage offers a crucial opportunity to address potential burr issues even before production begins.
Material Selection
Choosing the right material that is easier to machine can naturally reduce burr formation.
Soft metals or composites might create fewer burrs compared to harder materials that are resistant to cutting.
Design for Manufacturability
Incorporate design elements that make it easier to machine parts without causing burrs.
This might mean adjusting the shape of corners or angles, adding fillets, or optimizing the sequence of manufacturing steps to lessen burr creation.
Consulting with engineers and designers who can anticipate these issues and work in tandem with the production team is an advantageous strategy for reducing burrs.
Regular Maintenance and Quality Control
Routine maintenance of tools and machinery is essential for burr prevention.
Ensure that equipment is in proper working order, regularly scheduled for maintenance checks, and promptly repaired if needed.
Incorporate robust quality control checks throughout the manufacturing process to catch burrs early on.
Utilizing techniques such as visual inspections, surface finish checks, and automated sensors can help identify and eliminate burrs before they reach the customer.
Conclusion
For SMEs looking to maintain quality and efficiency in their manufacturing processes, burr prevention should be a strategic priority.
By investing in the right tools and technologies, training employees, and integrating burr prevention into the design and production process, businesses can save time and reduce costs associated with defective products.
Adopting a comprehensive approach to burr prevention not only safeguards operational efficiency but also ensures customer satisfaction and enhances the enterprise’s reputation in the industry.
資料ダウンロード
QCD管理受発注クラウド「newji」は、受発注部門で必要なQCD管理全てを備えた、現場特化型兼クラウド型の今世紀最高の受発注管理システムとなります。
ユーザー登録
受発注業務の効率化だけでなく、システムを導入することで、コスト削減や製品・資材のステータス可視化のほか、属人化していた受発注情報の共有化による内部不正防止や統制にも役立ちます。
NEWJI DX
製造業に特化したデジタルトランスフォーメーション(DX)の実現を目指す請負開発型のコンサルティングサービスです。AI、iPaaS、および先端の技術を駆使して、製造プロセスの効率化、業務効率化、チームワーク強化、コスト削減、品質向上を実現します。このサービスは、製造業の課題を深く理解し、それに対する最適なデジタルソリューションを提供することで、企業が持続的な成長とイノベーションを達成できるようサポートします。
製造業ニュース解説
製造業、主に購買・調達部門にお勤めの方々に向けた情報を配信しております。
新任の方やベテランの方、管理職を対象とした幅広いコンテンツをご用意しております。
お問い合わせ
コストダウンが利益に直結する術だと理解していても、なかなか前に進めることができない状況。そんな時は、newjiのコストダウン自動化機能で大きく利益貢献しよう!
(β版非公開)