- お役立ち記事
- A practical guide to quality function deployment (QFD) essential for quality departments
月間76,176名の
製造業ご担当者様が閲覧しています*
*2025年3月31日現在のGoogle Analyticsのデータより
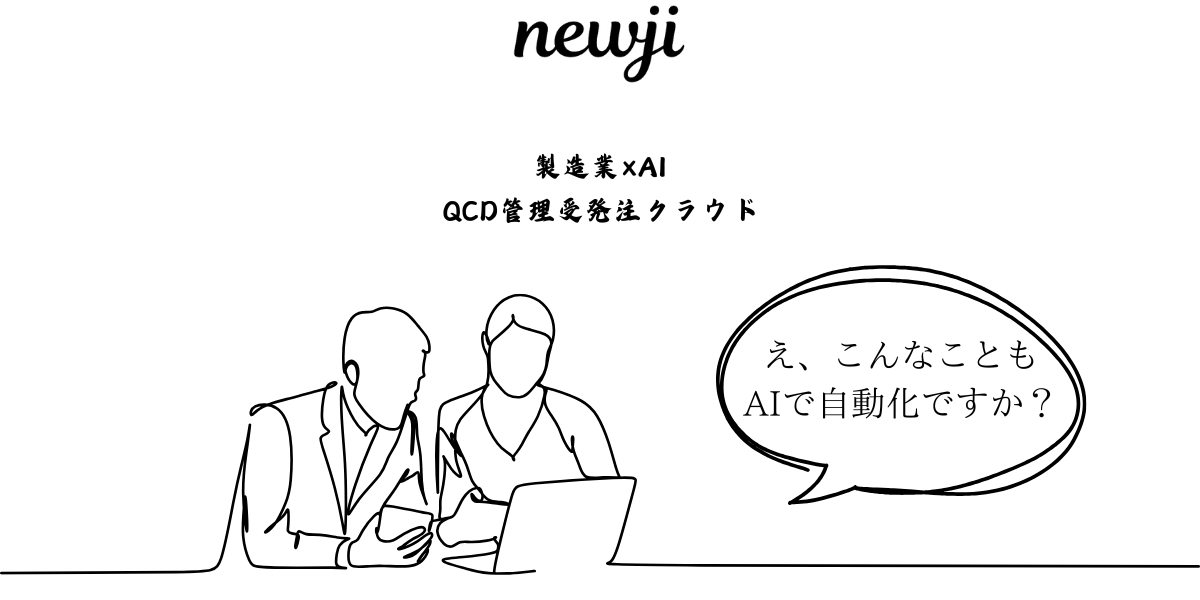
A practical guide to quality function deployment (QFD) essential for quality departments
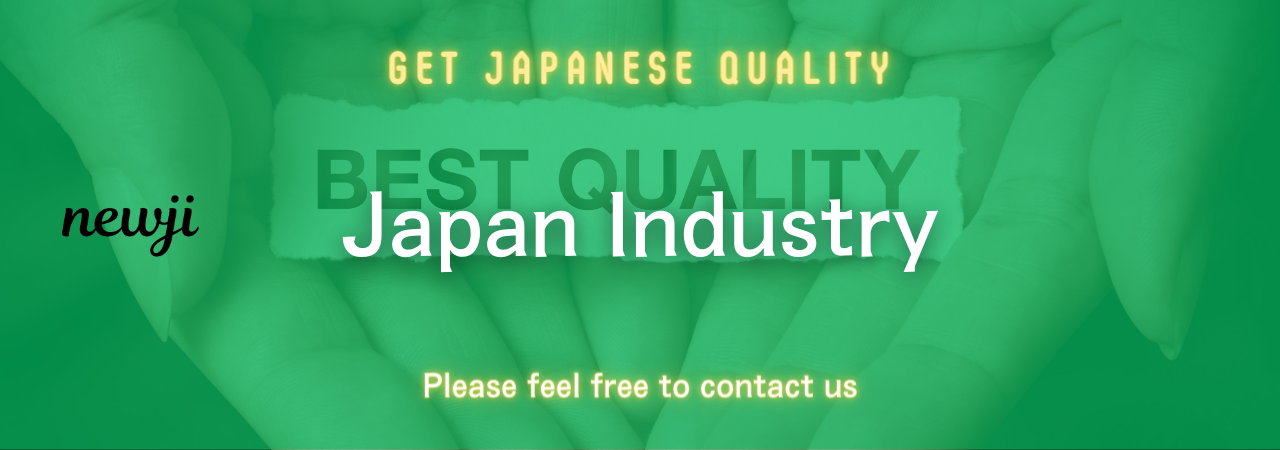
目次
Understanding Quality Function Deployment (QFD)
Quality Function Deployment, or QFD, is a systematic approach used in quality departments worldwide to transform user demands into design qualities and specifications.
It acts as a bridge between the voice of the customer and the technical requirements needed to address those needs effectively.
QFD is an essential methodology for any organization aiming to enhance product quality and customer satisfaction.
By structurally prioritizing and focusing on customer requirements, QFD ensures that products and services exceed consumer expectations.
The Origins of Quality Function Deployment
The concept of QFD originated in Japan in the late 1960s and gained significant traction in the automotive and consumer electronics industries.
Developed by Dr. Yoji Akao, QFD was initially intended to meet the rigorous demands of quality required in manufacturing.
The methodology quickly demonstrated its value, leading to widespread adoption across various industries including aerospace, telecommunications, software development, and more.
The Four Phases of QFD
QFD is typically broken down into four main phases, each crucial to the development process.
These phases are designed to ensure that customer needs are thoroughly analyzed and integrated into every step of product design and manufacturing.
1. Product Planning
The first phase is product planning, often referred to as the “House of Quality.”
It involves gathering customer requirements, translating them into technical descriptors, and prioritizing these descriptors based on customer importance and competitive analysis.
This phase serves as the foundation, ensuring that key customer needs are identified and addressed from the start.
2. Product Design
Once customer needs are identified, the next step is product design.
This involves translating the prioritized requirements into specific product concepts and components.
Here, the focus is on designing features and functionalities that meet both customer expectations and technical feasibility.
By ensuring alignment with customer needs, this phase helps minimize design flaws and customer dissatisfaction.
3. Process Planning
The third phase involves process planning.
This step outlines the processes required to manufacture the designed product.
It includes determining the necessary production procedures, equipment, and tools needed to ensure quality and efficiency.
Process planning ensures that the transition from design to production is seamless, keeping customer requirements at the forefront.
4. Production Planning
The final phase, production planning, focuses on establishing control measures to ensure that production consistently meets quality standards.
This includes setting up quality control checks, training staff, and implementing continuous improvement practices.
By maintaining rigorous adherence to customer requirements throughout production, this phase solidifies the quality of the final product.
Benefits of Implementing QFD
QFD offers numerous benefits to organizations aiming for high-quality products and customer satisfaction.
One significant advantage is improved communication and collaboration across departments.
By utilizing a structured approach to understand and address customer needs, teams can work more cohesively, minimizing misunderstandings and errors.
Moreover, QFD helps prioritize product features based on actual customer demand and importance.
This ensures that resources are focused on the most critical aspects, enhancing customer satisfaction and market success.
QFD also supports efficient resource allocation, reducing time-to-market and production costs by highlighting potential issues early in the process.
Challenges and Solutions in QFD Implementation
While QFD offers many benefits, implementing it can present challenges.
These may include resistance to change, resource limitations, and inadequate customer data.
However, with the right strategies, these challenges can be overcome effectively.
One common challenge is resistance from stakeholders unfamiliar with QFD methodology.
To address this, conducting comprehensive training sessions is crucial.
These sessions should clearly articulate the benefits of QFD and provide employees with the tools and knowledge needed for successful implementation.
Another challenge is collecting sufficient and accurate customer data.
Organizations can overcome this by using various data collection methods such as surveys, focus groups, and direct customer feedback.
Leveraging technology and data analytics can also enhance the accuracy and relevance of customer data.
Finally, resource limitations, both in terms of manpower and budget, can hinder QFD implementation.
By emphasizing the long-term benefits of QFD and encouraging pilot projects, organizations can demonstrate the positive impact on quality and cost savings, justifying the necessary resources.
Ensuring Successful QFD Implementation
For successful QFD implementation, it is crucial to involve cross-functional teams and foster a culture of continuous improvement.
Cross-functional teams, comprising members from design, engineering, marketing, and customer service, ensure that all perspectives are considered when developing a product.
This collaboration enriches the design process and ensures that products meet and exceed customer expectations.
Additionally, fostering a culture of continuous improvement is essential.
By encouraging regular reviews and updates to the QFD process, organizations can adapt to changing market demands and customer preferences effectively.
Continuous feedback loops help refine the approach, bolster employee engagement, and maintain high standards of quality and customer satisfaction.
Conclusion
Quality Function Deployment is an indispensable tool for quality departments focused on producing high-quality products that resonate with customer needs.
By translating customer requirements into actionable design and production plans, QFD ensures that organizations can deliver exceptional products and services.
Despite potential challenges, the benefits of QFD—including enhanced communication, better resource allocation, and increased customer satisfaction—far outweigh the hurdles, making it a vital methodology for any quality-driven organization.
資料ダウンロード
QCD管理受発注クラウド「newji」は、受発注部門で必要なQCD管理全てを備えた、現場特化型兼クラウド型の今世紀最高の受発注管理システムとなります。
ユーザー登録
受発注業務の効率化だけでなく、システムを導入することで、コスト削減や製品・資材のステータス可視化のほか、属人化していた受発注情報の共有化による内部不正防止や統制にも役立ちます。
NEWJI DX
製造業に特化したデジタルトランスフォーメーション(DX)の実現を目指す請負開発型のコンサルティングサービスです。AI、iPaaS、および先端の技術を駆使して、製造プロセスの効率化、業務効率化、チームワーク強化、コスト削減、品質向上を実現します。このサービスは、製造業の課題を深く理解し、それに対する最適なデジタルソリューションを提供することで、企業が持続的な成長とイノベーションを達成できるようサポートします。
製造業ニュース解説
製造業、主に購買・調達部門にお勤めの方々に向けた情報を配信しております。
新任の方やベテランの方、管理職を対象とした幅広いコンテンツをご用意しております。
お問い合わせ
コストダウンが利益に直結する術だと理解していても、なかなか前に進めることができない状況。そんな時は、newjiのコストダウン自動化機能で大きく利益貢献しよう!
(β版非公開)