- お役立ち記事
- A process that aims to improve quality and reduce costs through collaboration between purchasing and production departments.
月間76,176名の
製造業ご担当者様が閲覧しています*
*2025年3月31日現在のGoogle Analyticsのデータより
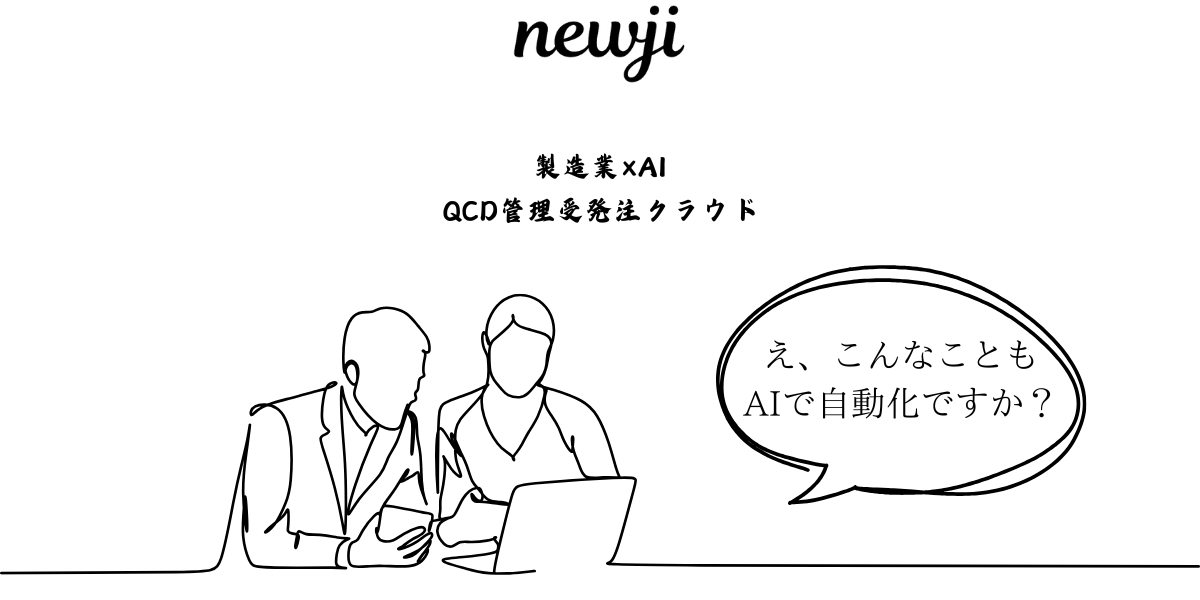
A process that aims to improve quality and reduce costs through collaboration between purchasing and production departments.
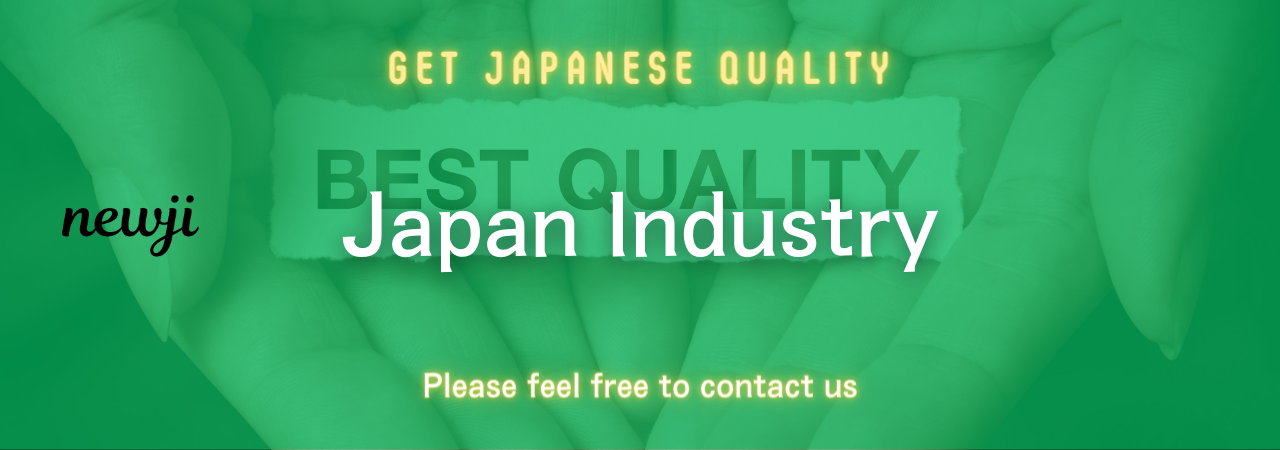
目次
Introduction
In today’s competitive business landscape, companies continuously search for strategies to enhance quality while minimizing costs.
One effective approach to achieving these goals is through seamless collaboration between the purchasing and production departments.
By working together, these departments can create a more efficient supply chain, streamline operations, and ultimately deliver better products at lower costs.
This article explores the process and benefits of collaboration between purchasing and production teams, shedding light on how it can lead to success.
The Role of the Purchasing Department
The purchasing department plays a vital role in a company by sourcing and acquiring the necessary materials and services needed for production.
This involves researching suppliers, negotiating contracts, and ensuring timely delivery of quality components.
The purchasing team is responsible for managing the supply chain, controlling costs, and maintaining strong relationships with vendors.
Their primary goal is to procure materials that meet production requirements while staying within budget constraints.
Supplier Relationship Management
A key element of the purchasing department’s role is to manage relationships with suppliers.
By building strong partnerships, the team can negotiate better terms, secure reliable supply chains, and gain access to innovations that could benefit production.
Effective supplier relationship management can lead to reduced lead times, improved material quality, and cost savings.
It also enables the company to quickly respond to changes in market demand or production requirements.
Cost Control
Cost control is a critical function of the purchasing department.
By optimizing procurement processes and negotiating favorable terms, the team can help reduce overall expenses.
This involves identifying cost-saving opportunities, such as bulk purchasing or selecting alternative materials that offer similar benefits at a lower price.
By keeping costs in check, the purchasing department contributes to the company’s financial health and competitiveness.
The Role of the Production Department
The production department is responsible for transforming raw materials into finished products that meet quality and efficiency standards.
Their primary goal is to ensure production processes run smoothly, efficiently, and consistently.
This involves managing equipment, schedules, and workforce to optimize throughput while maintaining product quality.
Quality Assurance
In the production department, quality assurance is paramount.
Ensuring that products meet customer expectations and comply with industry standards is crucial for maintaining brand reputation and customer satisfaction.
Quality assurance involves regular testing, process evaluations, and continuous improvement initiatives.
Collaboration with the purchasing department is essential here, as the quality of materials directly impacts the quality of the final product.
Process Efficiency
Achieving process efficiency is another critical responsibility of the production team.
By analyzing current workflows and identifying areas for improvement, the department can increase productivity and reduce waste.
Lean manufacturing principles and other process optimization techniques can be employed to streamline operations and enhance output.
Close collaboration with the purchasing team can help ensure that materials arrive on time and meet the exact specifications needed for efficient production.
Benefits of Collaboration Between Purchasing and Production
Collaboration between purchasing and production departments can lead to numerous benefits, including improved quality, reduced costs, and enhanced organizational efficiency.
Enhanced Communication
When purchasing and production departments work closely together, communication improves significantly.
Regular meetings and shared goals ensure that both teams understand each other’s needs and constraints.
This alignment allows for better decision-making and helps identify potential issues before they become problematic.
Streamlined Processes
Collaboration leads to more streamlined processes by aligning procurement with production schedules and requirements.
This alignment minimizes delays and reduces the risk of material shortages or overstock situations.
It ensures that the right materials are available when needed, contributing to smoother operations and less downtime.
Improved Quality and Reduced Defects
By working in tandem, purchasing and production departments can enhance overall product quality.
Close collaboration allows for better monitoring of material quality and production processes, reducing the likelihood of defects and rework.
Improved quality control leads to higher customer satisfaction and fewer warranty claims, benefiting the company’s bottom line.
Cost Savings
Joint efforts between purchasing and production departments can yield significant cost savings.
By optimizing procurement practices and production methods, the company can lower material costs and reduce waste.
Efficiency gains can also result in lower operational expenses, enhancing profitability.
Implementing a Collaborative Approach
To achieve successful collaboration between purchasing and production, companies should consider the following strategies:
Fostering a Collaborative Culture
Creating a company culture that emphasizes collaboration between departments is essential.
Encouraging open communication, teamwork, and shared goals can help break down silos and prompt departments to work together productively.
Investing in Technology
Implementing advanced technology, such as integrated systems and data analytics, can facilitate collaboration.
These tools provide real-time visibility into supply chain activities, inventory levels, and production schedules, enabling better coordination and decision-making.
Regular Cross-Functional Meetings
Regular cross-functional meetings between purchasing and production teams help maintain alignment and address issues promptly.
These meetings provide a forum for sharing information, discussing challenges, and developing solutions that benefit the entire organization.
Continuous Improvement Programs
Adopting continuous improvement programs can enhance collaboration efforts.
These initiatives encourage both departments to identify areas for improvement and work together on implementing changes that drive efficiency and quality.
Conclusion
In conclusion, collaboration between purchasing and production departments is a powerful strategy for improving quality and reducing costs.
By aligning goals, sharing information, and leveraging their respective strengths, these teams can drive efficiency, enhance product quality, and deliver value to customers.
Implementing a collaborative approach requires commitment, technology, and a culture that supports teamwork.
However, the benefits are substantial and can contribute to a company’s long-term success in the marketplace.
資料ダウンロード
QCD管理受発注クラウド「newji」は、受発注部門で必要なQCD管理全てを備えた、現場特化型兼クラウド型の今世紀最高の受発注管理システムとなります。
ユーザー登録
受発注業務の効率化だけでなく、システムを導入することで、コスト削減や製品・資材のステータス可視化のほか、属人化していた受発注情報の共有化による内部不正防止や統制にも役立ちます。
NEWJI DX
製造業に特化したデジタルトランスフォーメーション(DX)の実現を目指す請負開発型のコンサルティングサービスです。AI、iPaaS、および先端の技術を駆使して、製造プロセスの効率化、業務効率化、チームワーク強化、コスト削減、品質向上を実現します。このサービスは、製造業の課題を深く理解し、それに対する最適なデジタルソリューションを提供することで、企業が持続的な成長とイノベーションを達成できるようサポートします。
製造業ニュース解説
製造業、主に購買・調達部門にお勤めの方々に向けた情報を配信しております。
新任の方やベテランの方、管理職を対象とした幅広いコンテンツをご用意しております。
お問い合わせ
コストダウンが利益に直結する術だと理解していても、なかなか前に進めることができない状況。そんな時は、newjiのコストダウン自動化機能で大きく利益貢献しよう!
(β版非公開)