- お役立ち記事
- A process that aims to improve quality and reduce costs through collaboration between purchasing and production departments.
月間76,176名の
製造業ご担当者様が閲覧しています*
*2025年3月31日現在のGoogle Analyticsのデータより
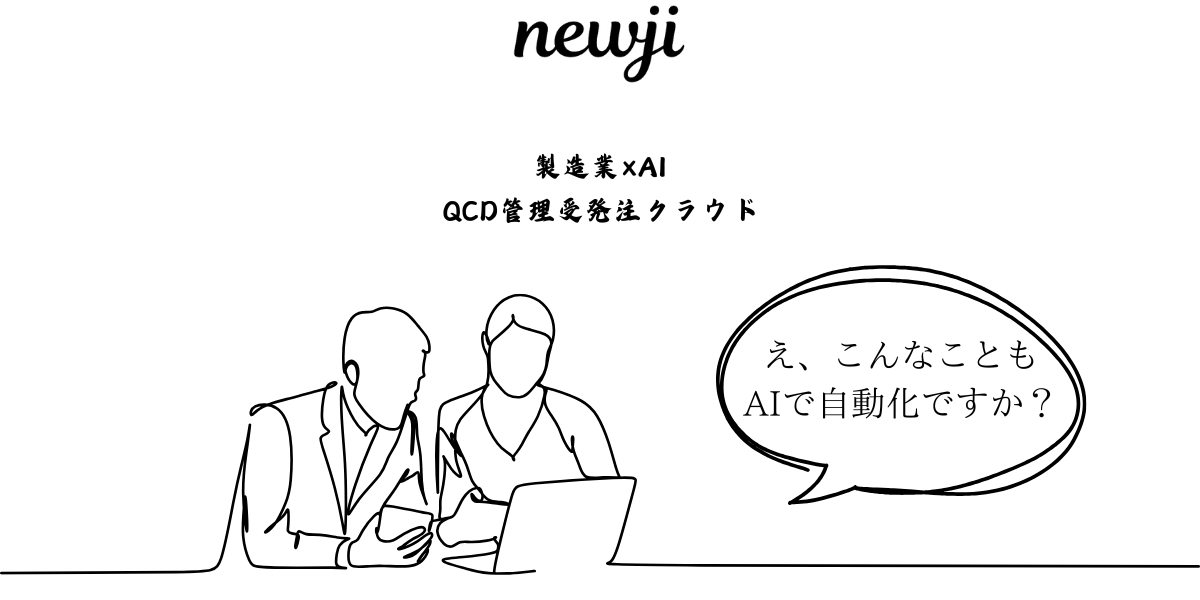
A process that aims to improve quality and reduce costs through collaboration between purchasing and production departments.
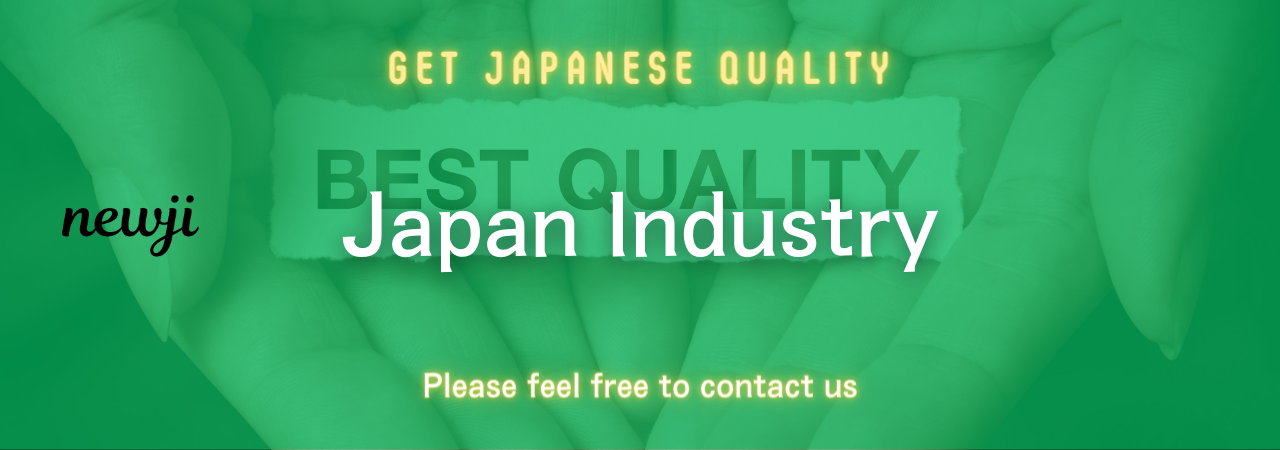
目次
Understanding the Role of Purchasing and Production Departments
When it comes to manufacturing, purchasing and production departments play critical roles in the lifecycle of a product.
The purchasing department is responsible for acquiring raw materials, components, and services needed to produce goods.
Their primary aim is to procure these at the best possible quality and cost.
On the other hand, the production department takes charge of transforming these inputs into finished products.
Their focus is on optimizing efficiency and maintaining quality standards throughout the production process.
These two departments have distinct responsibilities but must work closely to ensure that production runs smoothly.
Collaboration between purchasing and production is crucial for the success of a manufacturing business.
Together, they can directly impact the company’s bottom line by enhancing product quality while reducing costs.
Importance of Quality and Cost Management
In any manufacturing setup, maintaining high-quality standards while keeping costs in check is vital.
Consumers today are more quality-conscious, and they expect products that meet their standards at reasonable prices.
Simultaneously, companies are under constant pressure to keep their manufacturing expenses low to stay competitive.
Quality management involves ensuring that the products meet pre-established standards, which minimizes defects and enhances customer satisfaction.
When products are of high quality, companies spend less on returns and rework, thereby saving on costs.
Cost management, on the other hand, is about controlling expenses to maximize profit margins.
By sourcing materials at a lower cost without compromising on quality, businesses can improve their profitability.
Hence, both quality and cost management require strategic approaches from both purchasing and production departments.
The Need for Collaborative Processes
For many businesses, achieving exceptional quality and cost-effectiveness remains a challenging pursuit.
This is where collaboration becomes essential.
When purchasing and production departments operate in silos, it may lead to discrepancies in expectations and outcomes.
Shared goals between these departments can lead to processes that are both efficient and effective.
A collaborative approach enables companies to leverage the strengths of both teams, resulting in better resource utilization and improved performance.
Improving communication between purchasing and production helps in aligning objectives and maintaining consistency.
This collaboration aids in the development of integrated strategies that can tackle quality issues and cost constraints concurrently.
Benefits of Collaborative Processes
1. **Improved Supplier Relationships:** By working together, purchasing and production can establish stronger connections with suppliers, ensuring that they consistently provide quality materials at reasonable prices.
2. **Optimized Inventory Levels:** Collaboration ensures that production schedules and raw material purchases are harmonized, preventing overstocking and stockouts.
3. **Reduced Waste:** With closely aligned processes, both departments can identify areas to reduce waste, leading to cost savings and environmental benefits.
4. **Enhanced Problem Solving:** A united team can effectively identify bottlenecks and find solutions faster, improving overall operational efficiency.
Steps to Foster Collaboration
Building a collaborative culture between purchasing and production departments requires strategic planning and effort from both sides.
Here are some steps to get started:
1. Establish Clear Communication Channels
Encourage open and consistent communication between both departments.
Regular meetings and updates can help share insights and address any issues promptly.
Use collaborative tools and technology to facilitate information sharing and decision-making.
2. Align Objectives and Goals
Ensure that both departments understand and align with the broader organizational goals.
Setting common objectives helps in creating shared accountability and focus.
Collaborative goal-setting can motivate teams to work seamlessly towards shared success.
3. Integrate Technologies
Adopt technologies that foster collaboration, such as enterprise resource planning (ERP) systems.
Such tools can provide real-time data and feedback, enabling departments to adjust their strategies as needed.
Technology integration helps streamline processes and improve transparency.
4. Encourage Cross-Training
Encourage employees to learn aspects of each other’s roles.
This knowledge sharing enhances mutual understanding and respect among team members.
Cross-training can also improve workforce flexibility, ensuring operations run smoothly even when facing personnel shortages.
5. Track and Evaluate Performance
Establish key performance indicators (KPIs) to track the progress of collaborative efforts.
Regular evaluation helps in identifying areas of improvement and celebrating successes.
Feedback loops should be created to constantly refine processes and strategies.
Overcoming Challenges in Collaboration
While the benefits of collaboration are numerous, there are challenges that must be addressed:
Resistance to change is common as individuals may be accustomed to existing processes.
Structural changes to warranties may also involve time and monetary investment.
To overcome these challenges, it’s important to involve both departments early in the process of change.
Empower team members with the necessary tools, training, and support to adapt to new ways of working.
Additionally, fostering a culture of collaboration, where teamwork and cooperation are valued, is essential for long-term success.
Conclusion
In the dynamic landscape of manufacturing, the collaboration between the purchasing and production departments is vital for improving quality and reducing costs.
By working together towards common goals, businesses can optimize their operations, reduce waste, and achieve higher efficiency.
The journey of collaboration may require time and resources, but the rewards of enhanced product quality, cost savings, and competitive advantage make it a worthwhile endeavor.
資料ダウンロード
QCD管理受発注クラウド「newji」は、受発注部門で必要なQCD管理全てを備えた、現場特化型兼クラウド型の今世紀最高の受発注管理システムとなります。
ユーザー登録
受発注業務の効率化だけでなく、システムを導入することで、コスト削減や製品・資材のステータス可視化のほか、属人化していた受発注情報の共有化による内部不正防止や統制にも役立ちます。
NEWJI DX
製造業に特化したデジタルトランスフォーメーション(DX)の実現を目指す請負開発型のコンサルティングサービスです。AI、iPaaS、および先端の技術を駆使して、製造プロセスの効率化、業務効率化、チームワーク強化、コスト削減、品質向上を実現します。このサービスは、製造業の課題を深く理解し、それに対する最適なデジタルソリューションを提供することで、企業が持続的な成長とイノベーションを達成できるようサポートします。
製造業ニュース解説
製造業、主に購買・調達部門にお勤めの方々に向けた情報を配信しております。
新任の方やベテランの方、管理職を対象とした幅広いコンテンツをご用意しております。
お問い合わせ
コストダウンが利益に直結する術だと理解していても、なかなか前に進めることができない状況。そんな時は、newjiのコストダウン自動化機能で大きく利益貢献しよう!
(β版非公開)