- お役立ち記事
- A project to strengthen the quality control system led by the purchasing department
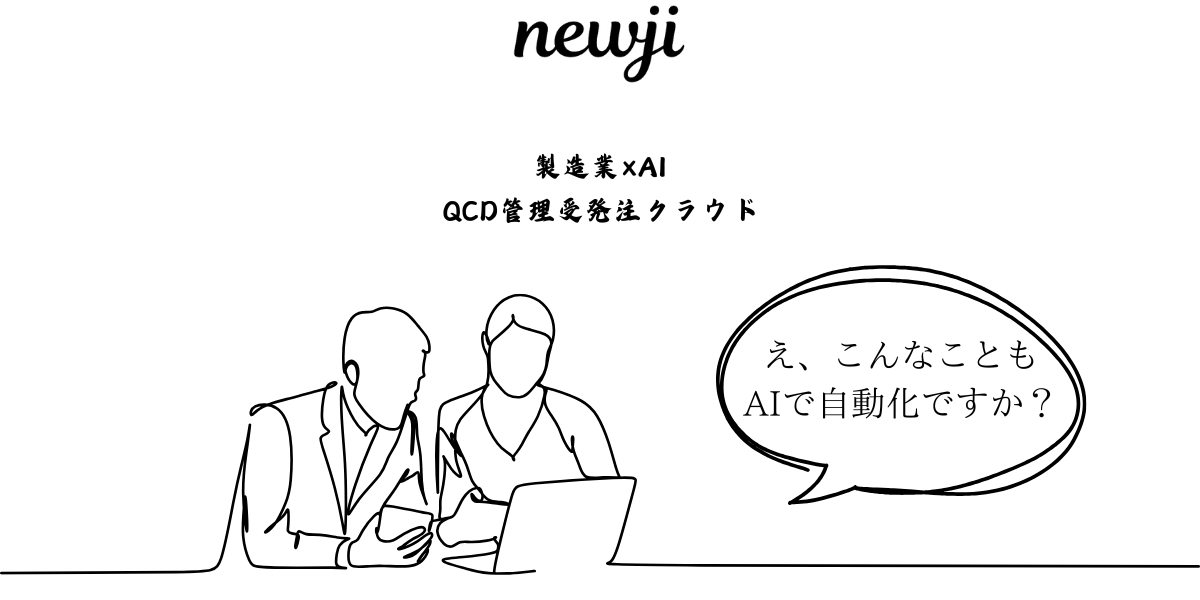
A project to strengthen the quality control system led by the purchasing department
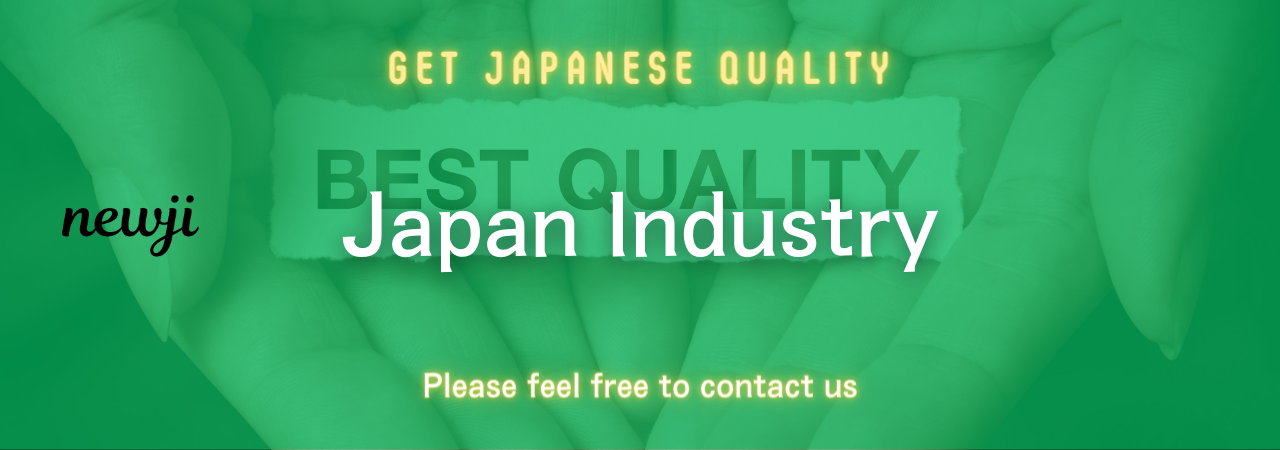
目次
Introduction to Quality Control in Purchasing
The quality control system within an organization is crucial for maintaining the standard of products and services offered to customers.
When it comes to the purchasing department, quality control plays an equally significant role.
This department is responsible for acquiring products and materials, which are then used in the production process.
If the quality of these purchased goods is compromised, it can result in defects and a decline in overall product quality.
Taking the initiative to enhance quality control, especially within the purchasing department, can yield remarkable benefits for any organization.
It not only ensures the integrity and reliability of goods but also enhances customer satisfaction and loyalty.
Moreover, a robust quality control system can lead to cost savings by reducing waste and minimizing returns and rework.
The Role of the Purchasing Department
The purchasing department is more than just an administrative unit that handles orders and payments.
It plays a strategic role in ensuring the supply chain is efficient and cost-effective.
The department is tasked with finding reliable suppliers, negotiating favorable terms, and ensuring timely deliveries.
Quality control within the purchasing department helps ensure that the materials and products purchased meet the required standards.
This involves setting strict criteria for supplier selection, implementing regular quality checks, and fostering continuous communication with suppliers.
By taking a proactive approach, the purchasing team can prevent poor quality products from entering the production line, thereby maintaining the overall quality of the final product.
Developing a Robust Quality Control System
Creating a comprehensive quality control system in the purchasing department requires careful planning and execution.
One of the first steps is to develop clear and concise quality standards that align with the company’s objectives.
These standards should define what is acceptable and what is not, ensuring everyone involved in the purchasing process understands the expectations.
Once the standards are set, it is essential to establish procedures for supplier evaluation and selection.
This process includes assessing potential suppliers based on their ability to deliver quality products consistently.
Conducting audits, requesting samples, and seeking references are effective ways to ensure adherence to quality standards.
Furthermore, implementing a system for continuous monitoring and evaluation is vital.
Regular inspections and assessments should be conducted to maintain quality control.
This repetitive practice ensures any deviations from the standard are detected early, preventing potential supply chain issues.
Training and Communication
To strengthen the quality control system, thorough training is imperative.
Personnel involved in the purchasing process should be well-versed in the quality standards and procedures set by the organization.
Training programs can cover topics such as identifying quality indicators, performing audits, and maintaining good supplier relationships.
Effective communication is another key aspect of improving quality control.
Regular meetings and updates between the purchasing team and suppliers help foster transparency and collaborative problem-solving.
Communication should not be one-sided but rather involve feedback from both sides to develop improved practices and solutions.
Leveraging Technology for Quality Control
In the digital age, technology offers valuable tools for enhancing quality control in the purchasing department.
Automating processes can streamline operations and reduce errors.
For example, using software to manage supplier information efficiently allows for quick access to data and helps in tracking performance over time.
Additionally, integrating technology such as electronic data interchange (EDI) systems can improve accuracy and speed in processing orders.
Technology also facilitates real-time reporting and monitoring, allowing the purchasing team to address any issues promptly.
Challenges and Solutions
Like any improvement initiative, there are challenges in developing an effective quality control system.
Resistance to change, limited resources, and the complexity of integrating new processes are common hurdles.
Addressing these challenges requires careful planning and involvement of all stakeholders.
Leadership support is crucial in overcoming resistance to change.
Managers should communicate the benefits of a robust quality control system and incentivize employees to adopt new practices.
Allocating sufficient resources to train staff and invest in technology is also critical for successful implementation.
Finally, starting with a phased approach can ease the transition.
By rolling out new processes gradually, the organization can manage risks and refine procedures based on feedback and real-world experiences.
Conclusion
Improving the quality control system led by the purchasing department is an initiative that can bring substantial benefits to an organization.
With the right strategies and practices in place, the purchasing department can ensure the materials and products acquired meet high standards of quality.
This not only enhances the product’s reliability but also strengthens the brand’s reputation in the market.
From setting clear standards to leveraging technology, strengthening the quality control system requires a comprehensive approach involving all stakeholders.
By committing to continuous improvement and adaptability, the purchasing department can play a vital role in delivering excellence and ensuring long-term success for the organization.
資料ダウンロード
QCD調達購買管理クラウド「newji」は、調達購買部門で必要なQCD管理全てを備えた、現場特化型兼クラウド型の今世紀最高の購買管理システムとなります。
ユーザー登録
調達購買業務の効率化だけでなく、システムを導入することで、コスト削減や製品・資材のステータス可視化のほか、属人化していた購買情報の共有化による内部不正防止や統制にも役立ちます。
NEWJI DX
製造業に特化したデジタルトランスフォーメーション(DX)の実現を目指す請負開発型のコンサルティングサービスです。AI、iPaaS、および先端の技術を駆使して、製造プロセスの効率化、業務効率化、チームワーク強化、コスト削減、品質向上を実現します。このサービスは、製造業の課題を深く理解し、それに対する最適なデジタルソリューションを提供することで、企業が持続的な成長とイノベーションを達成できるようサポートします。
オンライン講座
製造業、主に購買・調達部門にお勤めの方々に向けた情報を配信しております。
新任の方やベテランの方、管理職を対象とした幅広いコンテンツをご用意しております。
お問い合わせ
コストダウンが利益に直結する術だと理解していても、なかなか前に進めることができない状況。そんな時は、newjiのコストダウン自動化機能で大きく利益貢献しよう!
(Β版非公開)