- お役立ち記事
- A quality assurance department is essential! A step-by-step guide to effective 5-5 analysis
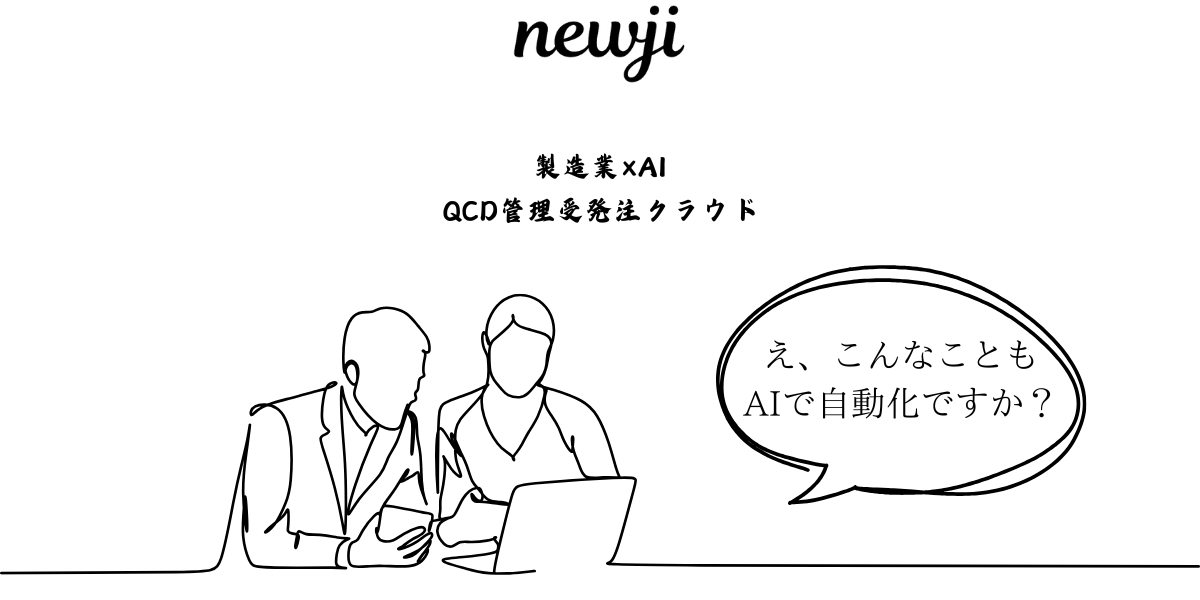
A quality assurance department is essential! A step-by-step guide to effective 5-5 analysis
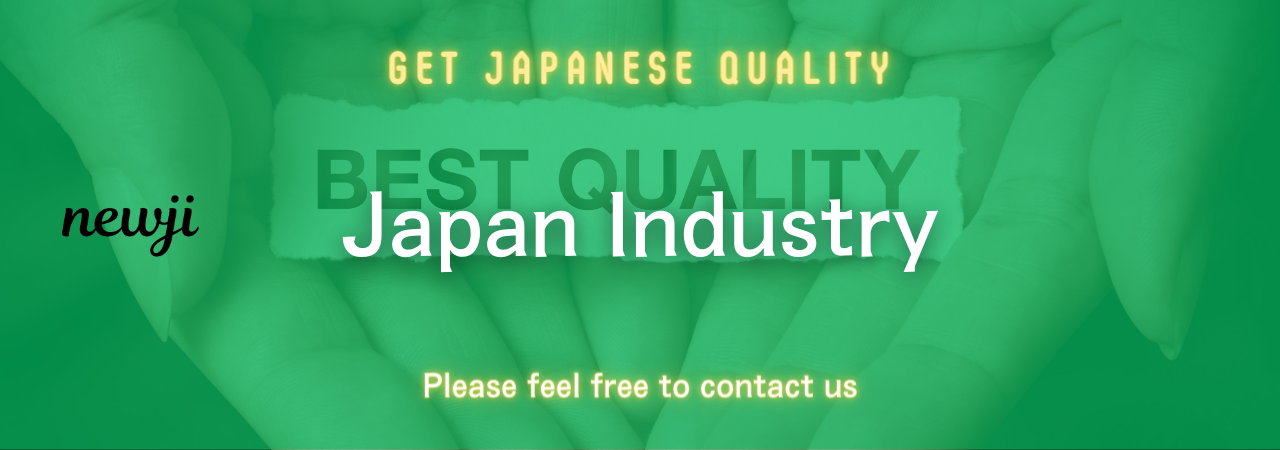
目次
Understanding 5-5 Analysis
Quality assurance plays a crucial role in ensuring products and services meet the set standards before they reach consumers.
One method that stands out for implementing this process is the 5-5 analysis, a systematic approach used by quality assurance departments.
Before diving into the step-by-step guide, it’s essential to understand what 5-5 analysis means.
5-5 analysis is a problem-solving tool that helps identify the root cause of a problem by asking “why” five times and “what” five times.
This technique provides a comprehensive understanding by exploring both the underlying cause and potential solutions.
The idea is that, by the time you have asked “why” five times, you will uncover the root cause of the issue.
Similarly, by exploring “what” questions, you offer a way to effectively address these issues.
Step 1: Identify the Problem
The first step in the 5-5 analysis is to clearly define the problem that needs to be addressed.
Having a specific problem definition is crucial for diving deeper into its root causes and finding appropriate solutions.
Start by gathering all necessary information related to the problem.
This includes data, documentation, testimonials, and any other relevant insights.
Be sure to precisely describe the issue to avoid confusion during subsequent analysis.
Step 2: Assemble the Right Team
A successful 5-5 analysis relies on gathering a team of individuals with diverse expertise and knowledge related to the problem.
Team members should come from various departments to provide different perspectives.
Having diverse views helps in comprehensively analyzing the problem and minimizes the risk of overlooking critical details.
Communicate the purpose of the meeting and encourage open dialogue to ensure that every team member is actively contributing to the analysis process.
Step 3: Conduct the First 5 Whys
Begin the 5-5 analysis by addressing the first half, which involves asking “why” five times.
Let’s break down this process:
1. **Ask the First Why**: Start by asking why the problem occurred.
Identify immediate causes and document the responses.
2. **Ask the Second Why**: Take the answer from the first why and ask why that situation happened.
Continue digging deeper into the underlying cause.
3. **Ask the Third Why**: By this stage, you’re uncovering deeper structural issues.
Continue asking why the problem persisted.
4. **Ask the Fourth Why**: This should lead you closer to the root cause.
Deepen the investigation and use insights from team members to gather different viewpoints.
5. **Ask the Fifth Why**: At the last why, aim to reveal the core of the problem.
This should present a clear and actionable root cause.
Remember, the goal is to reach a fundamental understanding of why a problem exists, not to place blame.
Step 4: Conduct the 5 Whats
Once the root cause is revealed, proceed to ask “what” five times to find solutions and ensure long-term resolution:
1. **Ask the First What**: Consider what actions can be taken immediately to address the root cause.
Start brainstorming potential solutions.
2. **Ask the Second What**: Ask what resources or tools are needed to implement the initial solutions.
Consider investments in technology or additional training where necessary.
3. **Ask the Third What**: Identify what changes to processes or systems are needed to prevent recurrence.
Assess the viability of proposed solutions.
4. **Ask the Fourth What**: Determine what metrics can be used to measure progress and success.
Make sure to have clear indicators for monitoring improvements.
5. **Ask the Fifth What**: Finally, establish what ongoing support is required for sustained improvements.
This step ensures the solution becomes integral to your processes.
Step 5: Implement and Review
Implementation is a critical phase where outlined solutions are put into practice.
Formulate a detailed action plan that includes priorities, timelines, and roles.
Communicate plans effectively across all involved teams, ensuring everyone is aligned.
After implementation, conduct regular reviews to assess effectiveness.
This involves monitoring progress, gathering feedback, and making necessary adjustments.
Remember, a solution is only as effective as its execution and follow-through.
Step 6: Document and Share Learnings
Documentation is vital for ongoing improvements and future reference.
Record all steps taken during the 5-5 analysis and the solutions implemented.
Sharing your findings with the broader organization can drive a culture of continuous improvement.
Allow others to learn from your experiences, which could help in preventing similar issues elsewhere.
Encouraging a collaborative atmosphere facilitates knowledge sharing and innovation.
The Benefits of 5-5 Analysis
The 5-5 analysis is invaluable for quality assurance departments, offering several benefits:
– It promotes an in-depth understanding of the root causes of problems, leading to more effective solutions.
– Encourages collaboration among team members, fostering a culture of problem-solving.
– Helps in creating detailed documentation that serves as a resource for ongoing learning and improvement.
– Promotes proactive management by identifying potential issues before they escalate.
Using this approach, quality assurance departments can better manage processes, reduce waste, and maintain high standards.
By following this guide, you can implement an effective 5-5 analysis within your quality assurance department.
It’s a powerful tool for driving improvements and ensuring the excellence of your products and services.
資料ダウンロード
QCD調達購買管理クラウド「newji」は、調達購買部門で必要なQCD管理全てを備えた、現場特化型兼クラウド型の今世紀最高の購買管理システムとなります。
ユーザー登録
調達購買業務の効率化だけでなく、システムを導入することで、コスト削減や製品・資材のステータス可視化のほか、属人化していた購買情報の共有化による内部不正防止や統制にも役立ちます。
NEWJI DX
製造業に特化したデジタルトランスフォーメーション(DX)の実現を目指す請負開発型のコンサルティングサービスです。AI、iPaaS、および先端の技術を駆使して、製造プロセスの効率化、業務効率化、チームワーク強化、コスト削減、品質向上を実現します。このサービスは、製造業の課題を深く理解し、それに対する最適なデジタルソリューションを提供することで、企業が持続的な成長とイノベーションを達成できるようサポートします。
オンライン講座
製造業、主に購買・調達部門にお勤めの方々に向けた情報を配信しております。
新任の方やベテランの方、管理職を対象とした幅広いコンテンツをご用意しております。
お問い合わせ
コストダウンが利益に直結する術だと理解していても、なかなか前に進めることができない状況。そんな時は、newjiのコストダウン自動化機能で大きく利益貢献しよう!
(Β版非公開)