- お役立ち記事
- A strategy for the purchasing department to pursue the optimal balance between cost and quality.
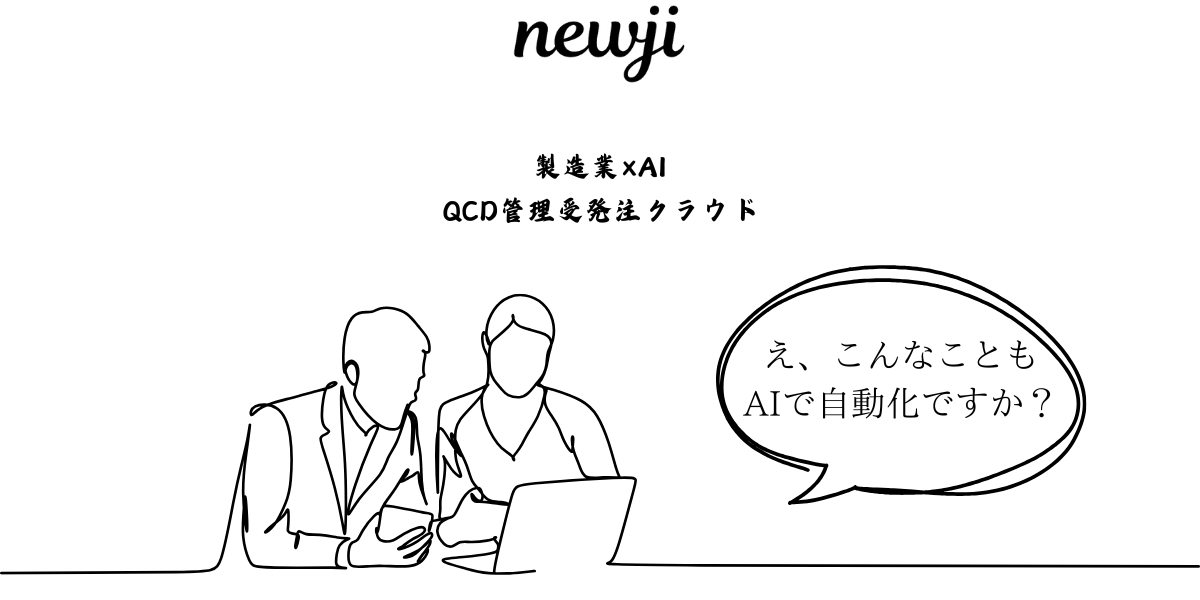
A strategy for the purchasing department to pursue the optimal balance between cost and quality.
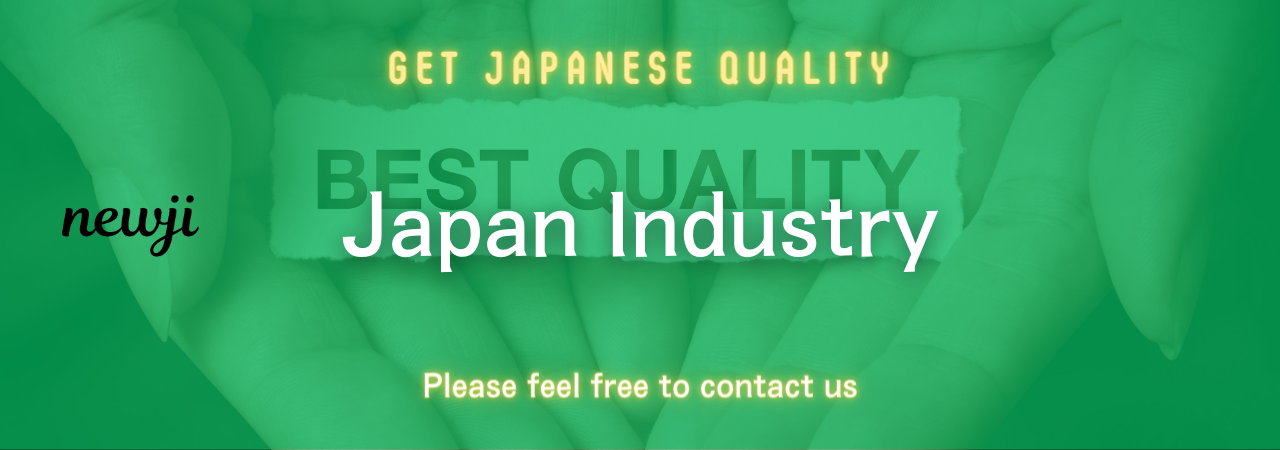
目次
Understanding the Role of the Purchasing Department
In any organization, the purchasing department plays a vital role in ensuring the company obtains the goods and services needed for operations.
Its primary responsibility is to source products and services at competitive prices while ensuring the quality meets organizational standards.
Balancing cost and quality is a constant challenge that requires effective strategies and foresight.
The key to this balance is understanding the organization’s needs and finding suitable suppliers who can meet those demands.
Assessing and Prioritizing Quality
One of the first steps in maintaining a balance between cost and quality is to establish clear criteria for quality.
This involves setting standards and specifications for materials or services needed.
Quality needs may vary from project to project, so it’s essential for the purchasing department to identify what aspects of quality are non-negotiable and what aspects can be adjusted according to the budget.
Regular feedback from product users can provide valuable insights into quality standards.
The purchasing department should frequently collaborate with end-users to understand their needs better and adjust the quality standards accordingly.
This ensures that the purchased goods or services are of a quality that satisfies internal and external customers, ultimately contributing to the company’s success.
Conducting Market Research
A thorough understanding of the market is crucial for finding the right balance between cost and quality.
Market research helps the purchasing team identify potential suppliers and get insights into current market prices, trends, and innovations.
By staying informed about the market landscape, the purchasing department can negotiate better deals and avoid overpaying for goods and services.
Competitive analysis also enables purchasers to benchmark their suppliers against industry standards.
This can be instrumental in determining if they are achieving the right balance between quality and cost and can initiate conversations with suppliers for possible improvements or discounts.
Supplier Selection and Management
Choosing the right suppliers is a critical step in balancing cost and quality.
Before making supplier selections, companies should perform a comprehensive evaluation of potential suppliers.
Factors such as reliability, delivery performance, post-purchase support, and overall flexibility need to be considered alongside cost and quality.
Once a supplier is selected, building a strong and transparent relationship is crucial.
Open communication helps in managing expectations and addressing any issues related to quality and cost effectively.
Regular audits and performance reviews can keep suppliers accountable and motivate them to maintain high standards.
Negotiating Contracts
Effective negotiation is key to achieving a balance between cost and quality.
The purchasing department should approach negotiations with a clear understanding of what the company is willing to compromise on and what is non-negotiable.
Well-prepared negotiation tactics can lead to mutually beneficial agreements, where the cost is optimized, and quality requirements are satisfied.
Purchasing professionals should also be knowledgeable about different contract types, such as fixed price, cost-reimbursable, and time and material contracts.
Choosing the right contract type based on the nature of the product or service can offer better control over cost without sacrificing quality.
Implementing Cost Control Measures
Cost control measures can help maintain a healthy balance between quality and expenditure.
These measures may include setting budgets, monitoring spend against forecasts, and regularly reviewing purchase requisitions.
Enabling competitive bidding among suppliers can also encourage them to offer the best prices without compromising on quality.
Purchasing departments can also look into alternative solutions such as bulk buying, long-term supplier contracts, and forming purchasing alliances.
Such strategies can lead to significant cost savings while ensuring the quality requirements are met.
Embracing Technology and Automation
Modern technology offers tools that can support the purchasing department in balancing cost and quality effectively.
Procurement software can streamline processes, reduce errors, and provide data analytics, which are essential for making informed purchasing decisions.
Automation can also enhance efficiency in tracking and managing supplier performance, enabling faster response times to quality concerns.
Through technology, purchasing departments can drive strategic sourcing decisions that are data-driven and aligned with organizational objectives.
Continuous Improvement and Feedback Loops
An ongoing process of improvement is necessary for the purchasing department to adapt to ever-changing market conditions and company needs.
By implementing feedback loops, the department can continuously assess the effectiveness of their purchasing strategies.
Feedback from suppliers, internal departments, and end-users should be analyzed to identify areas of improvement.
This will help the department to refine their approach towards achieving the optimal balance between cost and quality consistently.
Conclusion
Balancing cost and quality is an ongoing challenge that requires careful planning and execution by the purchasing department.
By understanding market trends, choosing the right suppliers, leveraging technology, and focusing on continuous improvement, organizations can achieve an optimal balance that supports their strategic goals.
Striving for this balance not only contributes to financial efficiency but also enhances overall business effectiveness and competitive advantage.
資料ダウンロード
QCD調達購買管理クラウド「newji」は、調達購買部門で必要なQCD管理全てを備えた、現場特化型兼クラウド型の今世紀最高の購買管理システムとなります。
ユーザー登録
調達購買業務の効率化だけでなく、システムを導入することで、コスト削減や製品・資材のステータス可視化のほか、属人化していた購買情報の共有化による内部不正防止や統制にも役立ちます。
NEWJI DX
製造業に特化したデジタルトランスフォーメーション(DX)の実現を目指す請負開発型のコンサルティングサービスです。AI、iPaaS、および先端の技術を駆使して、製造プロセスの効率化、業務効率化、チームワーク強化、コスト削減、品質向上を実現します。このサービスは、製造業の課題を深く理解し、それに対する最適なデジタルソリューションを提供することで、企業が持続的な成長とイノベーションを達成できるようサポートします。
オンライン講座
製造業、主に購買・調達部門にお勤めの方々に向けた情報を配信しております。
新任の方やベテランの方、管理職を対象とした幅広いコンテンツをご用意しております。
お問い合わせ
コストダウンが利益に直結する術だと理解していても、なかなか前に進めることができない状況。そんな時は、newjiのコストダウン自動化機能で大きく利益貢献しよう!
(Β版非公開)