- お役立ち記事
- A Technical Guide to Improving Product Quality and Precision Through Filling Time Management
月間76,176名の
製造業ご担当者様が閲覧しています*
*2025年3月31日現在のGoogle Analyticsのデータより
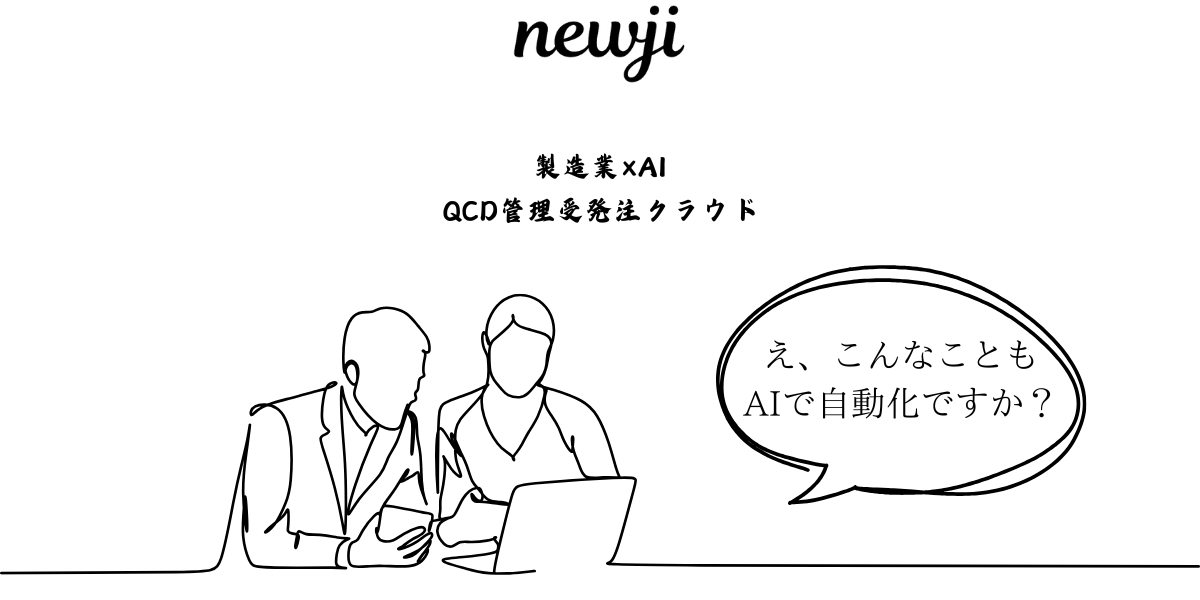
A Technical Guide to Improving Product Quality and Precision Through Filling Time Management
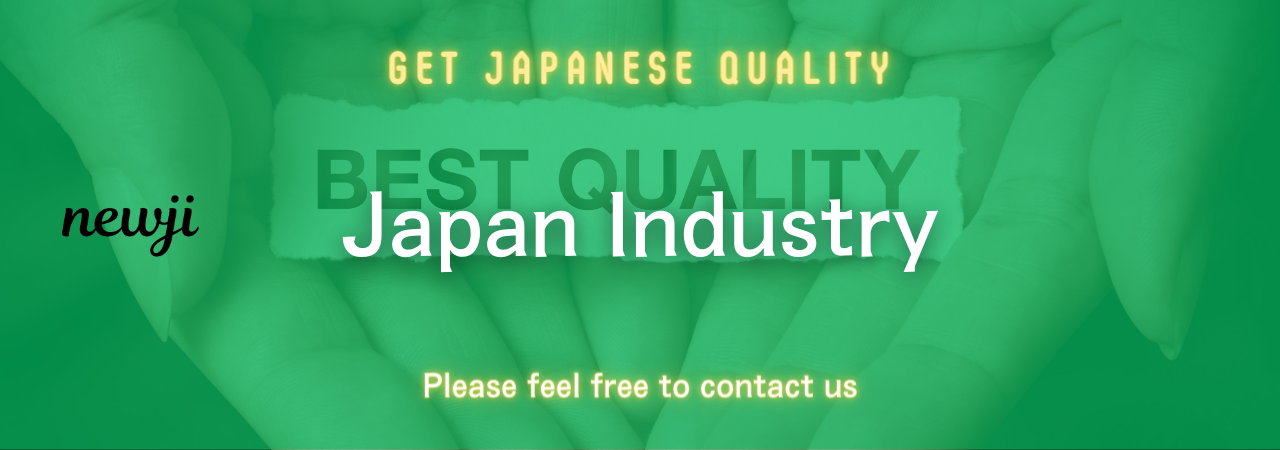
目次
Understanding Filling Time in Manufacturing
Filling time refers to the duration it takes to fill a product into its container or package during manufacturing.
This process is crucial in industries such as food and beverage, pharmaceuticals, and cosmetics.
The accurate management of filling time is essential to ensure not only the efficiency of production but also the quality and precision of the product.
Manufacturers rely on precise filling time as it affects both the quantity and the quality of the end product.
Even slight variations in filling times can lead to inconsistencies, material waste, or defects in the final product.
Understanding the dynamics of filling time can help companies streamline operations and enhance product quality.
The Impact of Filling Time on Product Quality
Proper filling time management can significantly enhance product quality, as it requires precise control mechanisms that align with production standards.
When filling time is optimized, it minimizes errors and discrepancies that affect the product’s integrity.
For instance, in pharmaceutical manufacturing, incorrect filling times can skew the dosage of a drug, affecting its efficacy and safety.
In food production, too much or too little filling can lead to spoiled products, impacting overall consumer satisfaction.
The demands of modern consumers have increased the stakes for maintaining high product quality.
Thus, understanding and controlling filling time can lead to improved customer trust and brand reputation.
The Effects of Filling Time Precision on Efficiency
Efficiency in filling processes is directly linked to the precision of timing.
A well-calibrated system ensures that resources are utilized optimally, reducing downtime and maximizing throughput.
By managing filling time precisely, companies can avoid frequent adjustments and repairs, leading to smoother operations.
In a competitive market, the efficiency of the filling process can be a differentiating factor.
Companies that manage their filling time with precision can handle larger volumes and adjust quickly to market demand fluctuations.
This capability provides a competitive edge, reducing costs and enhancing profitability.
Factors Affecting Filling Time
Numerous factors can impact filling time, requiring manufacturers to undertake careful analysis and adjustments.
1. **Type of Product**: Viscosity and consistency of the product can affect the speed and accuracy of the fill.
Thicker substances may require longer filling times and specialized equipment.
2. **Container Design**: The size and shape of the container influence filling operations.
Complex designs may challenge efficient filling, requiring customized solutions.
3. **Filling Equipment**: The technology and condition of the filling equipment are critical.
Outdated or poorly maintained machines can lead to inconsistent fills and longer filling times.
4. **External Conditions**: Temperature and humidity in the production environment can affect both the product and the machinery’s performance.
Adaptations in the filling process may be necessary to accommodate these variables.
Strategies for Optimizing Filling Time
To improve filling time management, businesses must consider strategic interventions that include technology upgrades and process improvements.
Implementation of Automated Systems
Automated filling machinery offers precision and consistency, reducing human errors and variability.
By integrating automation, companies can enhance the accuracy of filling times, ensuring reliable output.
Regular Calibration and Maintenance
Machines that are regularly serviced and calibrated are less likely to malfunction, leading to a more consistent filling process.
Scheduled maintenance can prevent unexpected breakdowns, ensuring uninterrupted operations.
Employee Training and Process Standardization
Well-trained employees can adeptly handle machinery and swiftly address issues, reducing downtime caused by human error.
Standardized procedures ensure that every shift operates under the same guidelines, minimizing variability.
Real-time Monitoring and Data Analysis
Installing sensors and monitoring systems can provide real-time insight into filling time performance.
These data analytics tools enable quick detection and correction of anomalies, further refining the filling process.
The Role of Technology in Filling Time Management
Advancements in technology play a pivotal role in the evolution of filling time management.
IoT and Smart Manufacturing
The integration of the Internet of Things (IoT) allows for interconnected systems where data from various equipment can be centralized and analyzed.
This connectivity helps in maintaining optimal filling times and predicting potential issues before they arise.
AI and Machine Learning
Artificial Intelligence and machine learning algorithms can analyze vast amounts of production data to identify patterns and optimize filling times.
These technologies can suggest adjustments that might lead to significant improvements in efficiency and precision.
Predictive Maintenance
Using predictive maintenance systems, manufacturers can foresee machinery failures and schedule maintenance before they cause downtime.
This precaution ensures continuous production flow and consistent filling times.
Concluding Insights
Efficient filling time management is a cornerstone of product quality and precision in the manufacturing industry.
By understanding the key factors influencing filling time and adopting modern technological solutions, companies can significantly enhance their production processes.
Adapting to new technologies and committing to continuous improvement can lead to substantial gains in productivity, customer satisfaction, and competitive advantage.
As the industry evolves, the emphasis on precision and quality will only intensify, making filling time management an essential focus for forward-thinking organizations.
資料ダウンロード
QCD管理受発注クラウド「newji」は、受発注部門で必要なQCD管理全てを備えた、現場特化型兼クラウド型の今世紀最高の受発注管理システムとなります。
ユーザー登録
受発注業務の効率化だけでなく、システムを導入することで、コスト削減や製品・資材のステータス可視化のほか、属人化していた受発注情報の共有化による内部不正防止や統制にも役立ちます。
NEWJI DX
製造業に特化したデジタルトランスフォーメーション(DX)の実現を目指す請負開発型のコンサルティングサービスです。AI、iPaaS、および先端の技術を駆使して、製造プロセスの効率化、業務効率化、チームワーク強化、コスト削減、品質向上を実現します。このサービスは、製造業の課題を深く理解し、それに対する最適なデジタルソリューションを提供することで、企業が持続的な成長とイノベーションを達成できるようサポートします。
製造業ニュース解説
製造業、主に購買・調達部門にお勤めの方々に向けた情報を配信しております。
新任の方やベテランの方、管理職を対象とした幅広いコンテンツをご用意しております。
お問い合わせ
コストダウンが利益に直結する術だと理解していても、なかなか前に進めることができない状況。そんな時は、newjiのコストダウン自動化機能で大きく利益貢献しよう!
(β版非公開)