- お役立ち記事
- A Technical Guide to Preventing Molding Defects by Adjusting Molding Cycle Times
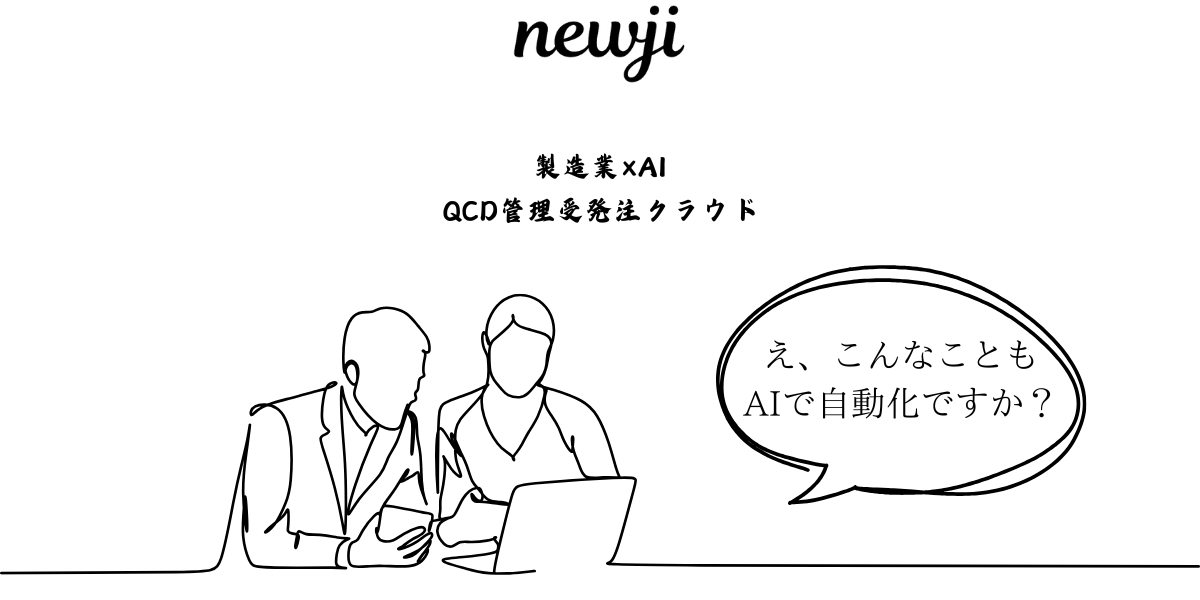
A Technical Guide to Preventing Molding Defects by Adjusting Molding Cycle Times
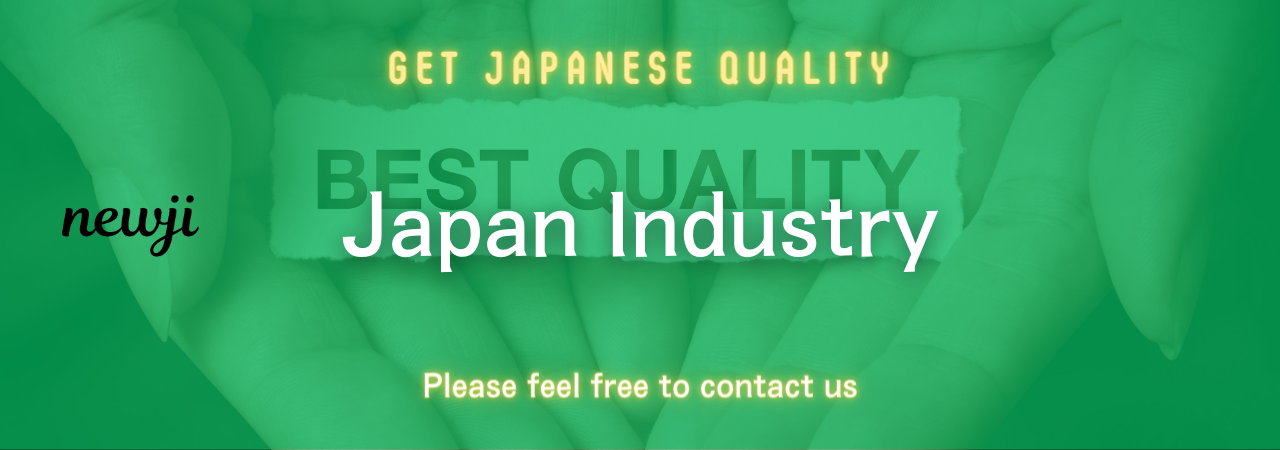
目次
Understanding Molding Cycle Times
Molding cycle times are crucial in manufacturing processes, particularly in plastic injection molding.
The cycle time refers to the period needed to complete one production cycle, which includes filling, cooling, and ejection of the mold.
Adjusting these times correctly can lead to higher quality products and fewer defects.
Failure to optimize this can result in imperfections like warping, sink marks, or incomplete filling.
Importance of Molding Cycle Times
Cycle times directly impact the productivity and quality of manufactured parts.
Short cycle times can enhance efficiency but may cause defects if not managed properly.
On the opposite end, longer cycle times might improve quality but reduce productivity.
Striking a balance is essential and can greatly affect the bottom line and customer satisfaction.
Common Molding Defects Related to Cycle Times
Molding defects can occur for various reasons, often linked to incorrect cycle times.
Three of the common defects include:
1. Warping
Warping happens when different areas of a molded part cool at different rates, leading to uneven shrinkage.
This can cause parts to distort and not fit together properly.
2. Sink Marks
Sink marks occur when the outer layer of a part solidifies faster than the inner material.
The contraction can create small depressions on the surface.
3. Short Shots
Short shots happen when the mold isn’t filled completely, usually caused by a mismatch in the cycle times.
This defect can result in incomplete parts that are not usable.
Adjusting Molding Cycle Times to Prevent Defects
Carefully adjusting the cycle times is essential in minimizing these defects.
Below are some techniques to optimize cycle times:
Fill Time Optimization
Filling time is critical as it determines how fast the molten material enters the mold.
Adjust this time based on the material type and mold design.
Too fast filling can lead to defects like flash, while too slow can cause short shots.
Cooling Time Adjustment
Cooling time allows the part to solidify within the mold before ejection.
Longer cooling times can help prevent warping but reduce output.
Consider the thermal properties of the mold material and the polymer to decide the appropriate cooling time.
Ejection Time Control
Ejecting too early can cause the part to be deformed, while delays can slow down the production rate.
Ensure that the part has sufficiently cooled and solidified before ejection.
Use temperature sensors to monitor part solidification for precision.
Tools and Technologies for Cycle Time Optimization
Advancements in technology provide tools that aid in fine-tuning cycle times.
Simulation Software
Injection molding simulation software can model and predict flow patterns and potential defects.
These simulations help in determining optimal cycle times without extensive physical trials.
Real-time Monitoring Systems
Install sensors that offer real-time data on temperature and pressure within the mold.
This data helps in making quick adjustments, ensuring consistent quality without delays.
Molding Automation
Automated systems can enhance precision in controlling cycle times by responding dynamically to changes in production conditions.
Automation reduces human error and increases production efficiency.
The Role of Materials and Design in Cycle Times
The materials and design also play a significant role in determining the optimal cycle times.
Material Selection
Different materials have varying cooling and solidifying times.
Consult material specifications to adjust cycle times appropriately.
Mold Design
The design should facilitate even flow and heat dissipation.
Complex designs might require longer cycle times to ensure complete filling and cooling.
Conclusion
Preventing molding defects involves a clear understanding of cycle times and their impact on the final product.
By optimizing fill, cooling, and ejection times, manufacturers can significantly reduce common defects like warping, sink marks, and short shots.
Utilizing modern tools and technologies, coupled with careful consideration of materials and design, can lead to more efficient production and higher quality parts.
Continually assess and adjust cycle times to adapt to new conditions, keeping productivity high and defect rates low.
資料ダウンロード
QCD調達購買管理クラウド「newji」は、調達購買部門で必要なQCD管理全てを備えた、現場特化型兼クラウド型の今世紀最高の購買管理システムとなります。
ユーザー登録
調達購買業務の効率化だけでなく、システムを導入することで、コスト削減や製品・資材のステータス可視化のほか、属人化していた購買情報の共有化による内部不正防止や統制にも役立ちます。
NEWJI DX
製造業に特化したデジタルトランスフォーメーション(DX)の実現を目指す請負開発型のコンサルティングサービスです。AI、iPaaS、および先端の技術を駆使して、製造プロセスの効率化、業務効率化、チームワーク強化、コスト削減、品質向上を実現します。このサービスは、製造業の課題を深く理解し、それに対する最適なデジタルソリューションを提供することで、企業が持続的な成長とイノベーションを達成できるようサポートします。
オンライン講座
製造業、主に購買・調達部門にお勤めの方々に向けた情報を配信しております。
新任の方やベテランの方、管理職を対象とした幅広いコンテンツをご用意しております。
お問い合わせ
コストダウンが利益に直結する術だと理解していても、なかなか前に進めることができない状況。そんな時は、newjiのコストダウン自動化機能で大きく利益貢献しよう!
(Β版非公開)