- お役立ち記事
- A total cost management tool to improve purchasing efficiency in the manufacturing industry
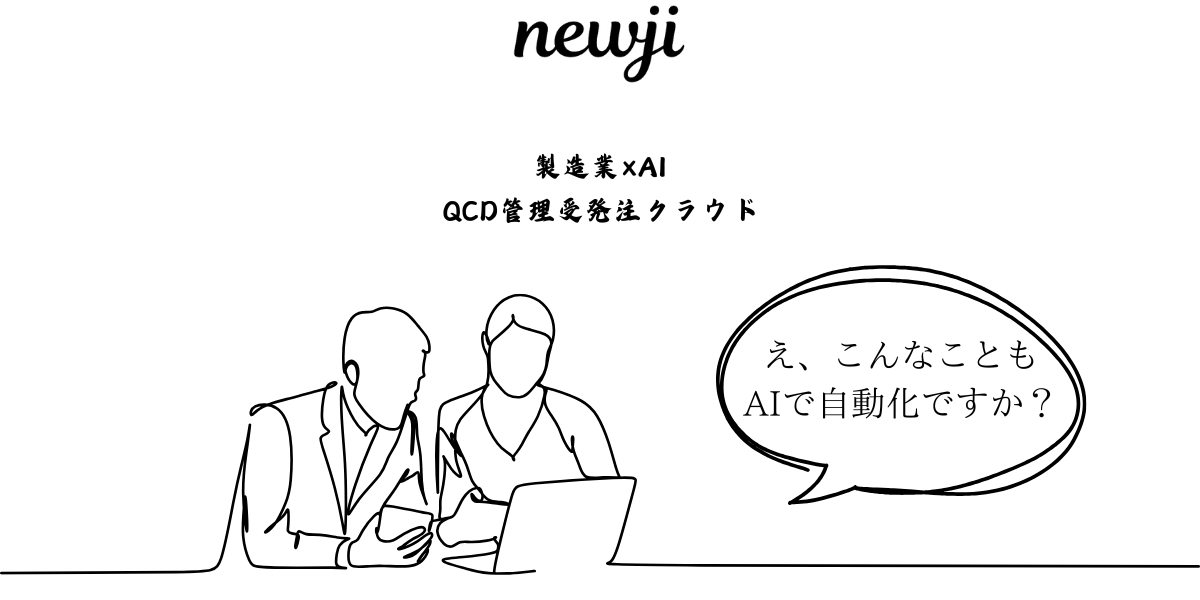
A total cost management tool to improve purchasing efficiency in the manufacturing industry
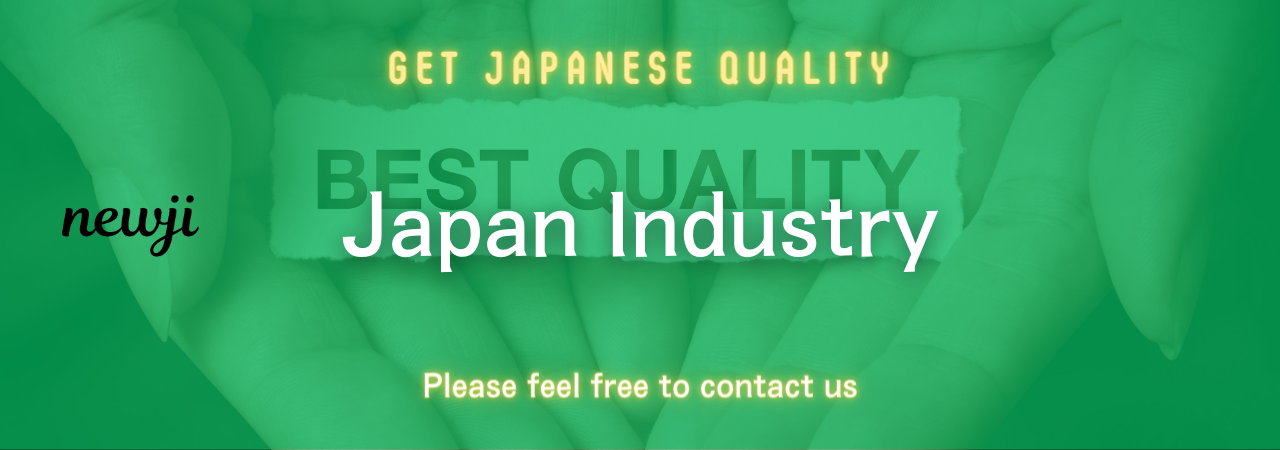
目次
Understanding Total Cost Management
In the manufacturing industry, purchasing efficiency can significantly impact a company’s overall profitability.
A Total Cost Management (TCM) tool is designed to streamline this process by offering comprehensive insights and strategies for managing costs across every stage of production.
By integrating a TCM tool, companies can gain a better understanding of their expenditure patterns and identify areas where efficiency can be improved.
TCM doesn’t focus solely on the price of purchasing materials.
Instead, it encompasses related expenses such as transportation, storage, and labor.
This broader perspective enables manufacturers to make more informed decisions regarding where to allocate resources most effectively.
The Importance of Purchasing Efficiency
Purchasing is a critical function in manufacturing, as it involves acquiring the necessary materials and services to produce a finished product.
Inefficient purchasing processes can lead to cost overruns, delays, and reduced product quality.
Thus, enhancing purchasing efficiency is essential for manufacturers aiming to maintain a competitive edge.
A well-implemented TCM tool helps manufacturers evaluate suppliers based on various criteria, including cost, reliability, and sustainability.
By doing so, manufacturers can establish strong relationships with suppliers who consistently deliver high-quality materials at competitive prices.
Key Features of a Total Cost Management Tool
Cost Analysis and Forecasting
One of the primary features of a TCM tool is its ability to analyze and forecast costs.
This includes evaluating past expenditures, predicting future trends, and identifying potential cost savings.
Accurate cost forecasting allows manufacturers to plan their budgets more effectively and avoid unexpected financial setbacks.
Supplier Management
Effective supplier management is crucial in maintaining purchasing efficiency.
A TCM tool enables manufacturers to evaluate supplier performance, track delivery times, and monitor the quality of materials provided.
By maintaining an up-to-date database of suppliers, manufacturers can quickly identify the best options for their needs.
Inventory Optimization
Managing inventory efficiently is another critical aspect of TCM.
A comprehensive tool helps manufacturers track inventory levels, monitor stock usage, and identify opportunities to reduce carrying costs.
Optimizing inventory ensures that manufacturers have the right materials at the right time, reducing the risk of production delays.
Process Automation
Automation is a vital feature of a TCM tool, as it streamlines repetitive tasks and reduces the likelihood of human error.
By automating processes such as ordering, invoicing, and data entry, manufacturers can save time and resources while improving accuracy.
Benefits of Implementing a Total Cost Management Tool
Implementing a TCM tool can bring numerous benefits to manufacturers, including improved purchasing efficiency and cost savings.
Some of the key advantages include:
Enhanced Decision-Making
With access to comprehensive data and analytics, manufacturers can make more informed decisions about their purchasing strategies.
This enables them to identify the most cost-effective options and minimize unnecessary expenditures.
Increased Cost Transparency
A TCM tool provides greater visibility into all aspects of the supply chain, helping manufacturers understand their total costs more clearly.
This transparency enables them to pinpoint areas where savings can be made and implement targeted cost-reduction strategies.
Improved Supplier Relationships
By evaluating and selecting suppliers based on performance metrics, manufacturers can foster stronger relationships with reliable partners.
This can lead to improved terms, better pricing, and overall enhanced collaboration.
Streamlined Operations
Automating routine tasks and optimizing inventory management through a TCM tool can result in significant operational efficiencies.
Manufacturers can allocate resources more effectively, minimize waste, and maximize productivity.
Overcoming Challenges in Implementing TCM Tools
While the benefits of a TCM tool are evident, implementing one can pose certain challenges.
Manufacturers must be prepared to address issues such as:
Integration with Existing Systems
Integrating a new tool with current systems can be complex and time-consuming.
Manufacturers should work closely with their IT teams to ensure seamless integration and minimize disruptions.
Training Employees
To maximize the effectiveness of a TCM tool, employees need to be trained on its functionalities and features.
Comprehensive training programs should be developed to help staff understand how to use the tool to its full potential.
Overcoming Resistance to Change
Introducing a new system can sometimes be met with resistance from employees.
To overcome this, manufacturers should communicate the benefits of the TCM tool clearly and involve staff in the implementation process to gain their support.
Conclusion
A Total Cost Management tool is an invaluable asset for manufacturers seeking to improve purchasing efficiency and reduce costs.
By offering comprehensive insights into cost analysis, supplier management, inventory optimization, and automation, a TCM tool enables manufacturers to make informed decisions that enhance overall business performance.
While challenges may arise during implementation, the long-term benefits of a TCM tool far outweigh initial hurdles.
Manufacturers willing to invest in this technology can look forward to enhanced purchasing processes, improved supplier relationships, and greater profitability.
資料ダウンロード
QCD調達購買管理クラウド「newji」は、調達購買部門で必要なQCD管理全てを備えた、現場特化型兼クラウド型の今世紀最高の購買管理システムとなります。
ユーザー登録
調達購買業務の効率化だけでなく、システムを導入することで、コスト削減や製品・資材のステータス可視化のほか、属人化していた購買情報の共有化による内部不正防止や統制にも役立ちます。
NEWJI DX
製造業に特化したデジタルトランスフォーメーション(DX)の実現を目指す請負開発型のコンサルティングサービスです。AI、iPaaS、および先端の技術を駆使して、製造プロセスの効率化、業務効率化、チームワーク強化、コスト削減、品質向上を実現します。このサービスは、製造業の課題を深く理解し、それに対する最適なデジタルソリューションを提供することで、企業が持続的な成長とイノベーションを達成できるようサポートします。
オンライン講座
製造業、主に購買・調達部門にお勤めの方々に向けた情報を配信しております。
新任の方やベテランの方、管理職を対象とした幅広いコンテンツをご用意しております。
お問い合わせ
コストダウンが利益に直結する術だと理解していても、なかなか前に進めることができない状況。そんな時は、newjiのコストダウン自動化機能で大きく利益貢献しよう!
(Β版非公開)