- お役立ち記事
- Accelerating Digitalization in Manufacturing with IT Infrastructure Development
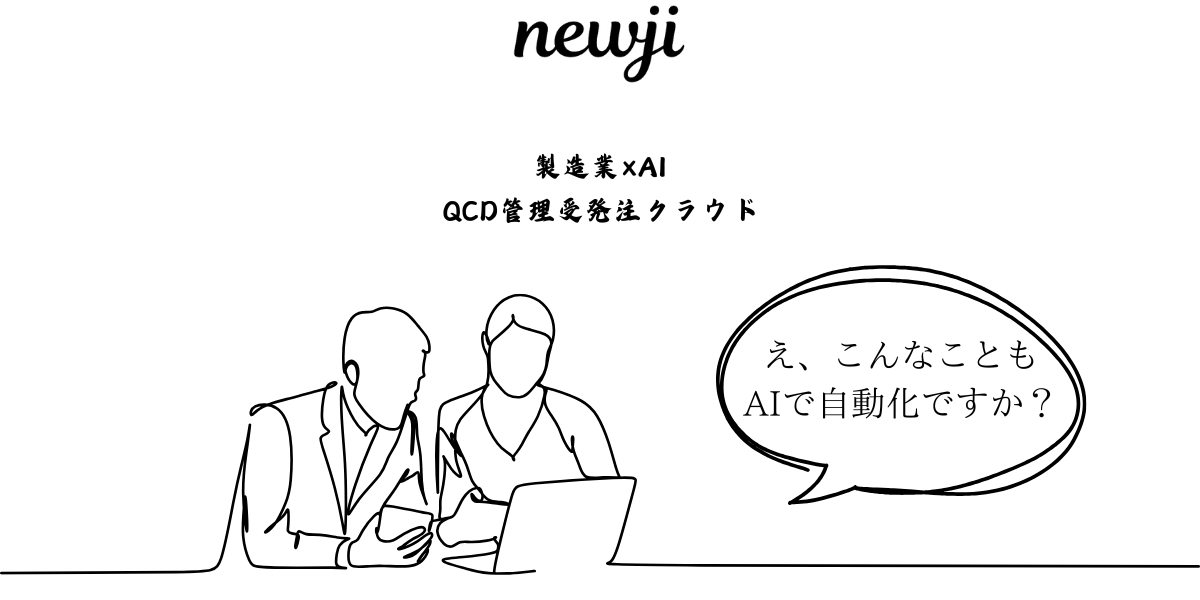
Accelerating Digitalization in Manufacturing with IT Infrastructure Development
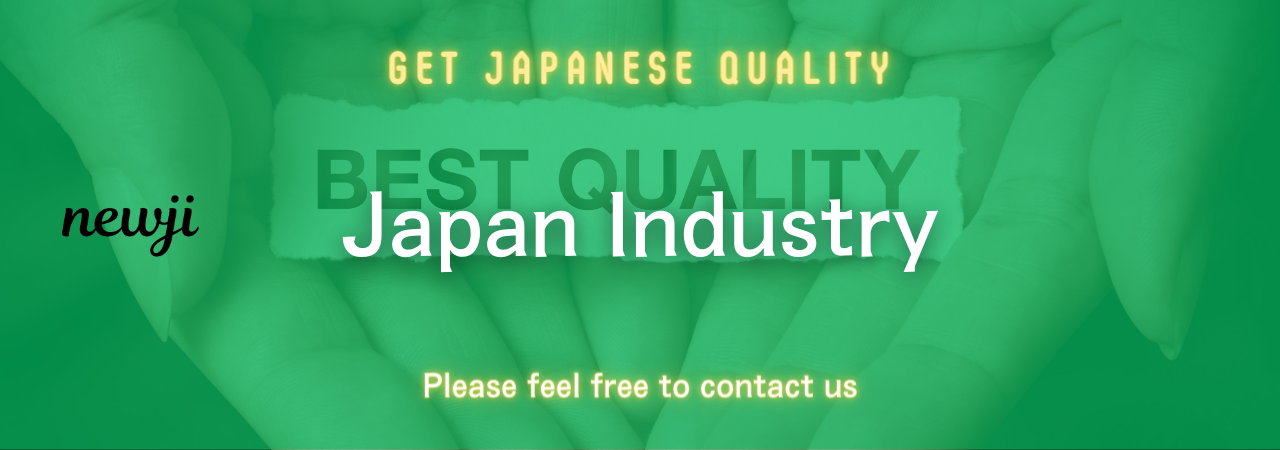
Digitalization is transforming the manufacturing industry, paving the way for more efficient, responsive, and versatile operations.
The rapid growth of technology demands robust IT infrastructure development to ensure the manufacturing sector keeps pace with these changes.
This article explores how IT infrastructure development is accelerating the digitalization of manufacturing and the benefits it brings.
目次
Understanding IT Infrastructure in Manufacturing
IT infrastructure refers to the composite hardware, software, network resources, and services required for the operation and management of an enterprise IT environment.
In manufacturing, a well-structured IT infrastructure is critical for supporting automation, data analytics, and connectivity.
The components of IT infrastructure in manufacturing include servers, data storage, networking equipment, and enterprise software.
The Role of IT Infrastructure in Digitalization
Digitalization leverages digital technologies to enhance business operations and outcomes.
In manufacturing, IT infrastructure plays a pivotal role in various digital transformation initiatives.
1. Enhancing Automation
Automation is a key aspect of digitalization in manufacturing.
With robust IT infrastructure, manufacturers can deploy advanced automation tools, such as robotic process automation (RPA) and industrial robots.
This improves efficiency, reduces errors, and enhances product quality.
2. Enabling Data Analytics
Data is at the heart of digital transformation.
IT infrastructure provides the necessary tools and platforms for collecting, storing, and analyzing vast amounts of data generated in manufacturing processes.
With analytics, manufacturers can gain insights into production bottlenecks, predictive maintenance, and supply chain optimization.
3. Improving Connectivity
The Industrial Internet of Things (IIoT) connects devices, machines, and systems within the manufacturing environment.
A strong IT infrastructure supports seamless connectivity, enabling real-time data exchange and remote monitoring.
This connectivity facilitates better decision-making and increases operational efficiency.
Benefits of IT Infrastructure Development
Investing in IT infrastructure development brings numerous benefits to the manufacturing sector.
1. Increased Productivity
With advanced IT infrastructure, manufacturers can automate repetitive tasks, streamline workflows, and optimize production schedules.
This leads to higher productivity and reduced operational costs.
2. Enhanced Flexibility
A well-developed IT infrastructure allows manufacturers to quickly adapt to market changes and customer demands.
It supports agile manufacturing practices, enabling rapid prototyping and customization.
3. Improved Quality Control
IT infrastructure supports real-time monitoring and quality control mechanisms.
Manufacturers can detect defects early, implement corrective actions swiftly, and ensure consistent product quality.
4. Better Supply Chain Management
With integrated IT systems, manufacturers can have better visibility and control over their supply chains.
This helps in demand forecasting, inventory management, and supplier collaboration.
5. Competitive Advantage
Companies that invest in IT infrastructure development are better positioned to leverage emerging technologies such as artificial intelligence (AI), machine learning, and blockchain.
These technologies can offer a significant competitive edge in terms of innovation and operational efficiency.
Challenges in IT Infrastructure Development
While the benefits are clear, developing robust IT infrastructure in manufacturing does come with challenges.
1. High Initial Costs
Building advanced IT infrastructure requires substantial upfront investment.
Many manufacturers, especially small and medium enterprises, may find it difficult to allocate the necessary resources.
2. Integration Issues
Integrating new IT systems with existing legacy systems can be complex and time-consuming.
Manufacturers must ensure interoperability and seamless data flow across all systems.
3. Cybersecurity Risks
As manufacturing operations become more dependent on digital technologies, they also become more vulnerable to cyberattacks.
Ensuring robust cybersecurity measures is essential to protect sensitive data and maintain operational integrity.
4. Skill Gaps
The rapid pace of technological advancement necessitates a workforce skilled in IT and digital tools.
Manufacturers need to invest in training and development to bridge the skill gap.
Future Trends in IT Infrastructure for Manufacturing
As technology continues to evolve, several trends are shaping the future of IT infrastructure in manufacturing.
1. Edge Computing
Edge computing involves processing data closer to the source of generation rather than relying on a central data center.
This reduces latency and allows for real-time decision-making, which is crucial in manufacturing.
2. 5G Connectivity
The adoption of 5G technology is set to revolutionize manufacturing by providing faster and more reliable communication networks.
It will support the deployment of IIoT devices and enhance overall connectivity.
3. Cloud Computing
Cloud computing offers scalable and flexible IT infrastructure solutions.
Manufacturers can leverage cloud platforms for data storage, analytics, and collaborative applications, reducing the need for on-premises hardware.
4. Artificial Intelligence and Machine Learning
AI and machine learning are driving innovations in predictive maintenance, quality control, and process optimization.
These technologies rely on a strong IT infrastructure to process and analyze large datasets efficiently.
5. Blockchain Technology
Blockchain can enhance transparency and security in supply chain management.
By providing a tamper-proof digital ledger, it ensures the authenticity and traceability of products.
Conclusion
The acceleration of digitalization in manufacturing hinges on the development of robust IT infrastructure.
While challenges exist, the benefits of increased productivity, enhanced flexibility, and improved quality control make it a worthwhile investment.
By staying abreast of emerging trends such as edge computing, 5G, and AI, manufacturers can continue to innovate and maintain a competitive edge in the industry.
Embracing IT infrastructure development is not just an option; it is a necessity for thriving in the digital age.
資料ダウンロード
QCD調達購買管理クラウド「newji」は、調達購買部門で必要なQCD管理全てを備えた、現場特化型兼クラウド型の今世紀最高の購買管理システムとなります。
ユーザー登録
調達購買業務の効率化だけでなく、システムを導入することで、コスト削減や製品・資材のステータス可視化のほか、属人化していた購買情報の共有化による内部不正防止や統制にも役立ちます。
NEWJI DX
製造業に特化したデジタルトランスフォーメーション(DX)の実現を目指す請負開発型のコンサルティングサービスです。AI、iPaaS、および先端の技術を駆使して、製造プロセスの効率化、業務効率化、チームワーク強化、コスト削減、品質向上を実現します。このサービスは、製造業の課題を深く理解し、それに対する最適なデジタルソリューションを提供することで、企業が持続的な成長とイノベーションを達成できるようサポートします。
オンライン講座
製造業、主に購買・調達部門にお勤めの方々に向けた情報を配信しております。
新任の方やベテランの方、管理職を対象とした幅広いコンテンツをご用意しております。
お問い合わせ
コストダウンが利益に直結する術だと理解していても、なかなか前に進めることができない状況。そんな時は、newjiのコストダウン自動化機能で大きく利益貢献しよう!
(Β版非公開)