- お役立ち記事
- Achieved both zero defects and improved productivity through DX of 100% inspection
Achieved both zero defects and improved productivity through DX of 100% inspection
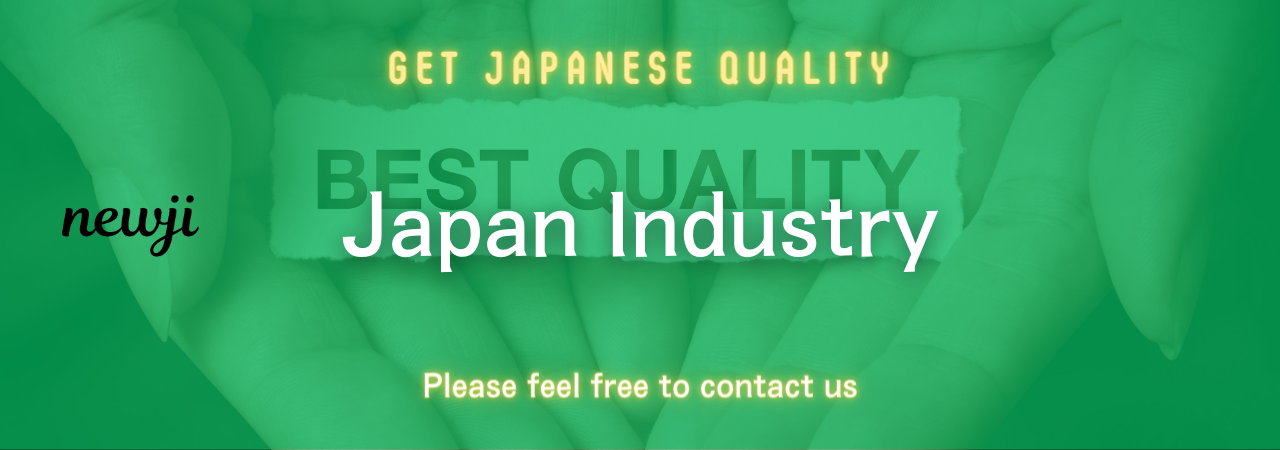
Digital transformation (DX) has become a buzzword in the manufacturing industry today.
One of the significant areas impacted by DX is the realm of quality control.
Traditional quality control methods often rely on sampling inspections that sometimes fail to catch defects, leading to costly recalls and damaged reputations.
This is where 100% inspection, powered by digital transformation, promises a breakthrough by ensuring zero defects while simultaneously boosting productivity.
目次
The Need for 100% Inspection
Manufacturers have always faced a trade-off between the extent of inspection and the associated costs.
A 100% inspection method intrinsically promises higher reliability since every product undergoes inspection.
However, manual 100% inspection has proven to be impractical and labor-intensive.
The advent of digital tools and technologies has reshaped this landscape.
Advanced software, artificial intelligence (AI), and robotic process automation (RPA) make it feasible to implement 100% inspection without the significantly increased labor cost and time.
Inherent Risks of Traditional Sampling
The fundamental flaw in traditional sampling inspections is the assumption that the sample represents the entire batch.
Any defect in unsampled units would go unnoticed, leading to sporadic quality issues.
For industries with stringent quality requirements—like pharmaceuticals, automotive, and aerospace—the costs of such oversights can be astronomical.
Thus, traditional sampling cannot guarantee the perfection that modern industries demand.
Leveraging Digital Transformation for 100% Inspection
Digital transformation allows companies to transition from outdated inspection protocols to real-time, automated, and comprehensive quality checks.
Let’s break down how DX achieves both zero defects and improved productivity through 100% inspection.
Integration of IoT Devices
The Internet of Things (IoT) has revolutionized how factories operate.
With IoT-enabled sensors strategically placed on production lines, real-time data can be collected and processed instantaneously.
These sensors are capable of monitoring various parameters such as temperature, dimensions, weight, and more.
Any deviation from the set standards can trigger automatic alarms, flagging the defect in real-time.
Thus, by integrating IoT devices, manufacturers can ensure that every product adheres to quality benchmarks.
Automation and Robotics
Incorporating robotics and automation into inspection processes turns the daunting task of 100% inspection into a streamlined, efficient protocol.
Automated robotic arms equipped with cameras and sensors can inspect every aspect of a product.
Moreover, these machines work tirelessly without experiencing the fatigue that human inspectors do.
The use of robotics for inspection reduces the scope for human error, ensuring higher consistency and quality.
Role of AI and Machine Learning
Artificial Intelligence (AI) and Machine Learning (ML) are game-changers in the inspection realm.
These technologies enable the creation of complex algorithms that can identify even the minutest defects.
Machine learning models can be trained with millions of images of both defective and non-defective items.
With this training, the model will start recognizing patterns that even the keenest human eye might miss.
AI-powered inspection systems can also learn and improve over time, becoming increasingly accurate and efficient.
Boosting Productivity Through DX
While ensuring zero defects is paramount, enhancing productivity is equally critical for manufacturers striving to maintain competitive advantages.
Digital transformation addresses this dual objective effortlessly.
Reduction in Downtime
One of the main productivity killers in traditional inspection processes is downtime.
Switching between batches, recalibrating machines, and fixing inspection errors consume substantial time.
With automated and digital inspection systems, these inefficiencies are minimized.
Machines equipped with AI and IoT capabilities can run continuous checks without requiring frequent shutdowns, thus maximizing operational uptime.
Streamlining Data Collection and Analysis
DX facilitates seamless data collection and analysis, vital for optimizing industrial processes.
Centralized data platforms can aggregate information from multiple inspection points.
Manufacturers can leverage data analytics tools to gain insights into defect trends, root causes, and areas needing improvement.
Prompt data availability allows for immediate interventions, reducing waste, and rework.
In addition, predictive analytics enabled by AI can foresee potential issues, allowing for preemptive corrections.
Inventory Management
Managing inventory efficiently is paramount for maintaining high productivity levels.
With DX and real-time quality data, manufacturers can optimize their inventory better.
Knowing which batches pass or fail inspections instantly informs inventory restocking decisions.
Just-in-time inventory systems benefit immensely from such immediate insights, reducing holding costs and improving turnover rates.
Case Studies: Digital Transformation in Action
Several industry leaders have already reaped the benefits of merging DX with 100% inspection.
Let’s delve into a few noteworthy examples.
Automobile Industry
Leading automakers have integrated AI and IoT to deploy automated inspection systems in assembly lines.
With continuous real-time monitoring, defects can be detected and rectified before the car leaves the factory, cutting down on recalls and repairs.
Pharmaceuticals
In the pharmaceutical industry, precision is unequivocally critical.
Digital transformation ensures that every pill, vial, and package undergo extensive scrutiny.
AI-powered inspection systems detect discrepancies in formulations, packaging, and labeling, ensuring that only flawless products reach consumers.
Electronics Manufacturing
Electronics manufacturing is another area immensely benefiting from DX.
Circuit boards, for instance, are subject to rigorous 100% inspection using machine vision systems.
These systems can identify microscopic defects, ensuring reliability and longevity in electronic devices.
Challenges and Future Directions
While the prospects of DX in achieving zero defects and increased productivity are promising, certain challenges remain.
Implementation Costs
The initial investment for setting up advanced digital inspection systems can be high.
However, manufacturers must consider this as a long-term investment, where the gains in quality, efficiency, and reduced waste outweigh the initial expenses.
Data Security
With increased reliance on interconnected systems, data security becomes paramount.
Manufacturers need robust cybersecurity measures to safeguard sensitive production data from potential breaches.
Continuous Improvement
Digital systems need continuous updates and improvements.
The rapidly evolving tech landscape means companies must constantly stay ahead of the curve, adopting new tools and techniques as they become available.
Workforce Training
Employees need to be adequately trained to handle new digital inspection tools.
Upskilling and reskilling of the workforce become vital components of successful DX implementation.
The journey towards achieving zero defects and improved productivity through digital transformation of 100% inspection is undoubtedly transformative.
As more manufacturers embrace this change, the industry will move closer to a future where perfection isn’t just an aspiration but a reality.
資料ダウンロード
QCD調達購買管理クラウド「newji」は、調達購買部門で必要なQCD管理全てを備えた、現場特化型兼クラウド型の今世紀最高の購買管理システムとなります。
ユーザー登録
調達購買業務の効率化だけでなく、システムを導入することで、コスト削減や製品・資材のステータス可視化のほか、属人化していた購買情報の共有化による内部不正防止や統制にも役立ちます。
NEWJI DX
製造業に特化したデジタルトランスフォーメーション(DX)の実現を目指す請負開発型のコンサルティングサービスです。AI、iPaaS、および先端の技術を駆使して、製造プロセスの効率化、業務効率化、チームワーク強化、コスト削減、品質向上を実現します。このサービスは、製造業の課題を深く理解し、それに対する最適なデジタルソリューションを提供することで、企業が持続的な成長とイノベーションを達成できるようサポートします。
オンライン講座
製造業、主に購買・調達部門にお勤めの方々に向けた情報を配信しております。
新任の方やベテランの方、管理職を対象とした幅広いコンテンツをご用意しております。
お問い合わせ
コストダウンが利益に直結する術だと理解していても、なかなか前に進めることができない状況。そんな時は、newjiのコストダウン自動化機能で大きく利益貢献しよう!
(Β版非公開)