- お役立ち記事
- Achieving a Production System That Prevents Defects
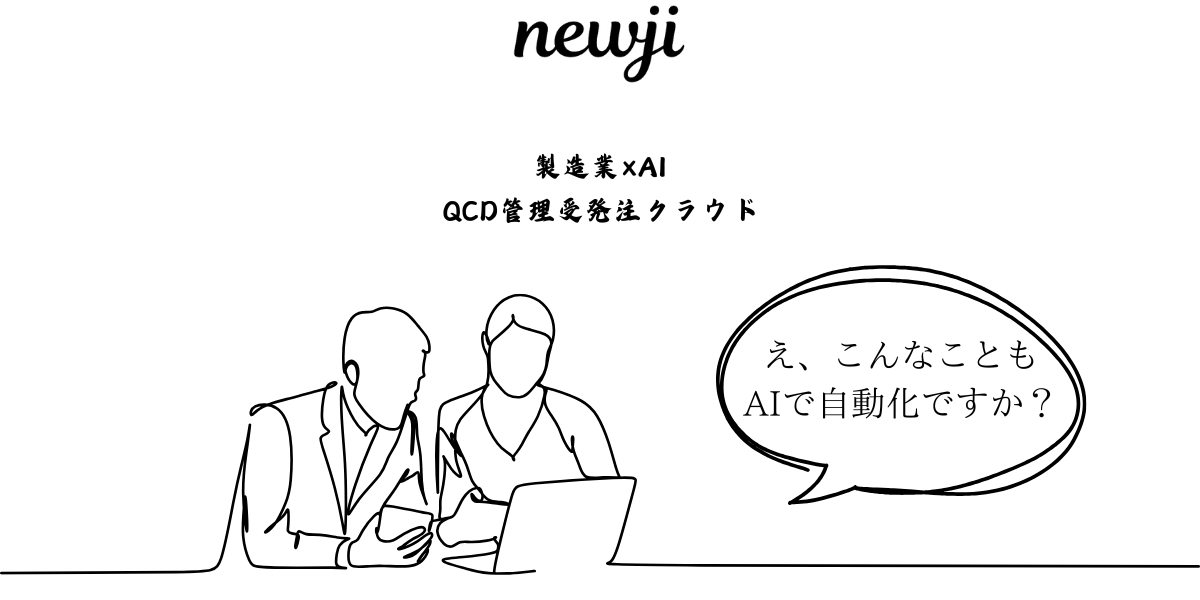
Achieving a Production System That Prevents Defects
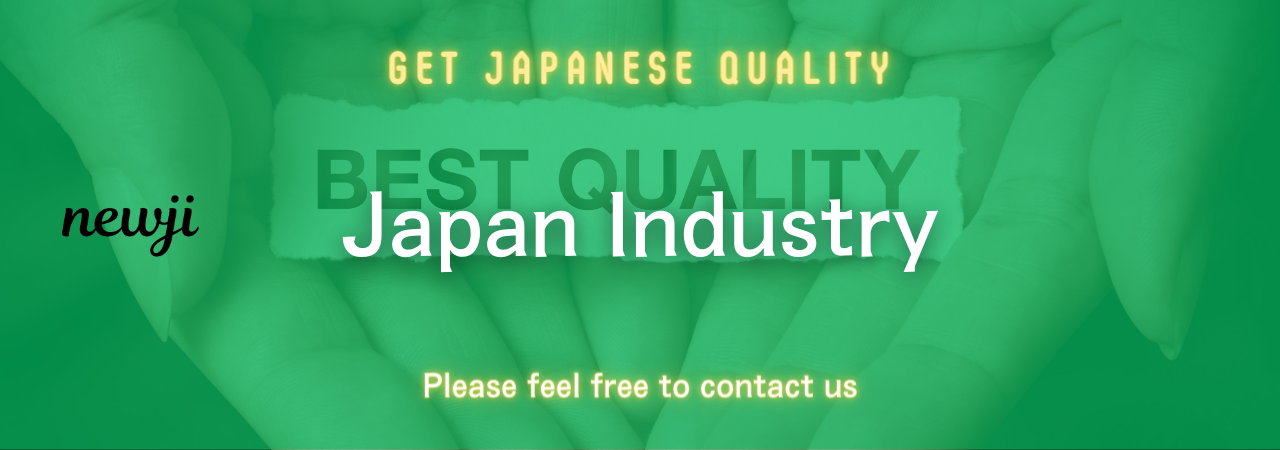
In the world of manufacturing, ensuring that products are free from defects is crucial for maintaining quality and customer satisfaction. Achieving a production system that prevents defects requires adopting specific strategies and technologies. This article delves into the vital components and practices necessary for creating an efficient defect-prevention system.
目次
Understanding the Importance of Defect Prevention
Defects in products can lead to increased costs, customer dissatisfaction, and reputational damage. Not only do businesses incur financial losses due to returns and rework, but they also risk losing customer trust. A production system that effectively prevents defects can save companies significant amounts of money and time. It also helps in maintaining a positive reputation in highly competitive markets.
Key Strategies for Preventing Defects
1. Implementing Quality Control Systems
Effective quality control systems are the backbone of defect-free production. These systems involve regular inspections, testing, and quality assessments throughout the manufacturing process. By closely monitoring each stage, companies can identify and address potential issues before they become defects.
2. Using Automated Testing Technologies
Incorporating automated testing technologies can significantly enhance the accuracy and efficiency of defect detection. Automated systems can quickly scan products for inconsistencies and deviations from quality standards. This rapid identification allows for immediate corrective actions, reducing the likelihood of defective products reaching the consumer market.
3. Employee Training and Awareness
Well-trained employees are crucial for maintaining product quality. Regular training sessions help workers understand the importance of quality and the specific steps they can take to prevent defects. Moreover, fostering a culture of quality awareness encourages employees to take personal responsibility for the products they handle, further reducing the chance of defects.
Technological Advancements in Defect Prevention
1. The Role of IoT (Internet of Things)
IoT technology has revolutionized defect prevention by enabling real-time monitoring of machinery and production processes. Sensors and interconnected devices can provide instant feedback on equipment performance and product quality, allowing for immediate adjustments. This real-time data helps in pinpointing potential issues before they escalate into significant problems.
2. Machine Learning and AI
Artificial Intelligence (AI) and machine learning algorithms can analyze vast amounts of production data to identify patterns and predict potential defects. These technologies can suggest optimal production parameters and highlight areas that need improvement. By continuously learning from the data, AI systems can enhance defect prevention measures over time.
Implementing a Holistic Approach
1. Integrating Lean Manufacturing Principles
Lean manufacturing focuses on minimizing waste and maximizing efficiency, which inherently supports defect prevention. By streamlining production processes and eliminating non-essential steps, companies can reduce the likelihood of errors and defects. Lean principles such as Six Sigma provide structured methodologies to identify and eliminate sources of variation and defects.
2. Continuous Improvement Practices
A commitment to continuous improvement is essential for a defect-free production system. Regularly reviewing and refining processes helps in staying ahead of potential issues. Tools such as Kaizen, which emphasizes incremental improvements, can be very effective in maintaining high quality standards and preventing defects.
3. Supplier Quality Management
Defect prevention doesn’t end within the factory’s walls. Ensuring that suppliers provide high-quality materials is equally important. Establishing rigorous supplier quality management programs allows companies to enforce high standards and consistent quality from the source. Regular audits and assessments of supplier performance are necessary to maintain these standards.
Benefits of a Defect-Free Production System
1. Cost Savings
Preventing defects at the production stage significantly reduces costs associated with returns, rework, and waste. By maintaining high-quality standards, companies can allocate resources more efficiently and focus on innovation and growth.
2. Enhanced Customer Satisfaction
Delivering defect-free products ensures that customers receive goods that meet their expectations. Enhanced customer satisfaction leads to repeat business, positive reviews, and strong word-of-mouth recommendations. This not only boosts sales but also cements a company’s reputation for reliability.
3. Improved Operational Efficiency
A production system focused on defect prevention operates more smoothly and efficiently. Fewer disruptions due to quality issues mean that production schedules are met more consistently. This reliability translates to better inventory management and more predictable supply chains.
4. Competitive Advantage
Companies that consistently produce high-quality, defect-free products gain a significant competitive edge. In markets where quality is a key differentiator, a strong reputation for reliability can attract new customers and retain existing ones. This advantage is crucial in building long-term business success.
Conclusion
Achieving a production system that prevents defects is a multifaceted endeavor that requires a combination of strategies, technologies, and a commitment to quality at all levels. By implementing robust quality control systems, leveraging advanced technologies like IoT and AI, and fostering a culture of continuous improvement, companies can significantly reduce defects.
These measures not only enhance customer satisfaction but also lead to substantial cost savings and operational efficiencies. In an increasingly competitive marketplace, the ability to consistently deliver defect-free products can set a company apart, ensuring its long-term success.
資料ダウンロード
QCD調達購買管理クラウド「newji」は、調達購買部門で必要なQCD管理全てを備えた、現場特化型兼クラウド型の今世紀最高の購買管理システムとなります。
ユーザー登録
調達購買業務の効率化だけでなく、システムを導入することで、コスト削減や製品・資材のステータス可視化のほか、属人化していた購買情報の共有化による内部不正防止や統制にも役立ちます。
NEWJI DX
製造業に特化したデジタルトランスフォーメーション(DX)の実現を目指す請負開発型のコンサルティングサービスです。AI、iPaaS、および先端の技術を駆使して、製造プロセスの効率化、業務効率化、チームワーク強化、コスト削減、品質向上を実現します。このサービスは、製造業の課題を深く理解し、それに対する最適なデジタルソリューションを提供することで、企業が持続的な成長とイノベーションを達成できるようサポートします。
オンライン講座
製造業、主に購買・調達部門にお勤めの方々に向けた情報を配信しております。
新任の方やベテランの方、管理職を対象とした幅広いコンテンツをご用意しております。
お問い合わせ
コストダウンが利益に直結する術だと理解していても、なかなか前に進めることができない状況。そんな時は、newjiのコストダウン自動化機能で大きく利益貢献しよう!
(Β版非公開)