- お役立ち記事
- Achieving an Efficient Manufacturing Line with Autonomous Mobile Robots (AMRs)
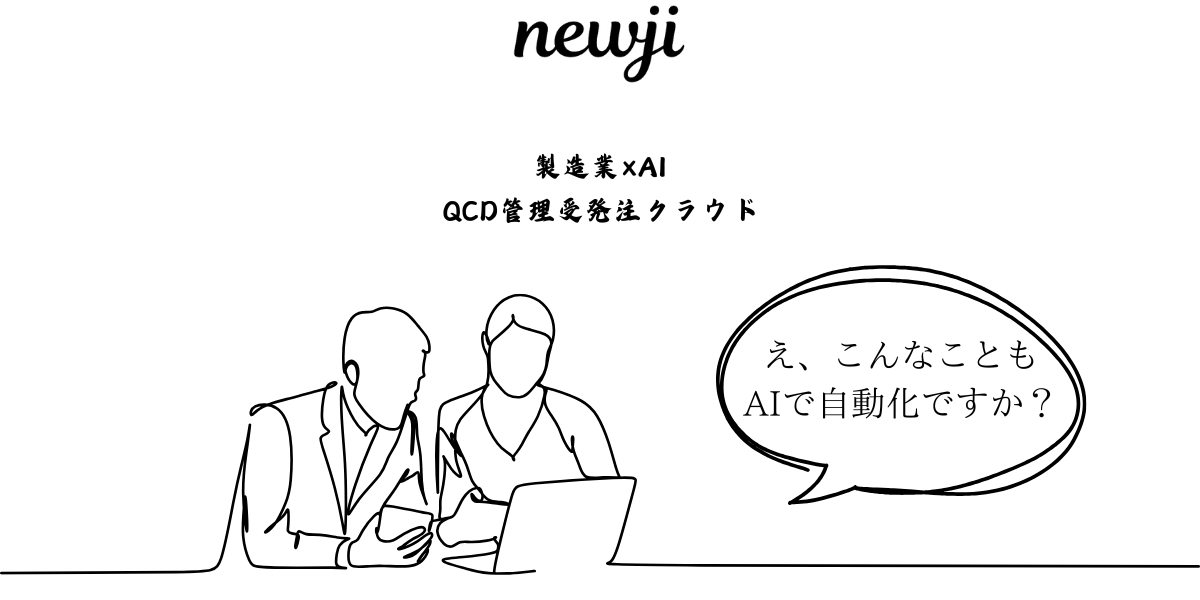
Achieving an Efficient Manufacturing Line with Autonomous Mobile Robots (AMRs)
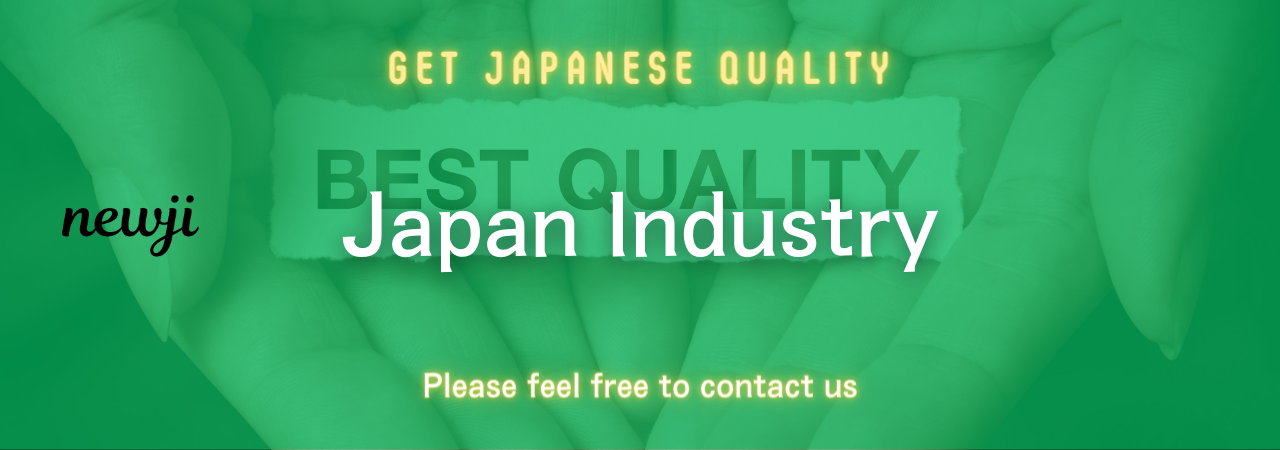
In today’s fast-paced world, manufacturing industries are constantly looking for ways to improve efficiency and reduce costs.
One of the most exciting advancements in recent years is the use of Autonomous Mobile Robots (AMRs) in manufacturing lines.
These innovative machines have the ability to revolutionize the way products are assembled, transported, and delivered within a factory.
目次
What Are Autonomous Mobile Robots (AMRs)?
AMRs are robots that can navigate through environments and perform tasks without direct human intervention.
Unlike traditional automated guided vehicles (AGVs), which rely on fixed paths like magnetic strips or wires, AMRs use sensors, cameras, and advanced software to understand their surroundings and move freely.
This flexibility allows them to adapt to changes in the environment and optimize their tasks in real-time.
The Advantages of Using AMRs in Manufacturing
The integration of AMRs in manufacturing offers several significant benefits.
Increased Efficiency
One of the primary advantages of AMRs is their ability to increase efficiency.
By automating repetitive and time-consuming tasks, these robots free up human workers to focus on more complex and value-added activities.
For example, instead of manually transporting materials across the factory floor, an AMR can handle this task seamlessly, reducing downtime and speeding up the production process.
Cost Savings
Although the initial investment in AMRs can be substantial, the long-term cost savings are considerable.
AMRs help reduce labor costs by taking over tasks that would otherwise require multiple workers.
Moreover, their precision and accuracy minimize errors and waste, leading to significant savings in the form of fewer defective products and less material usage.
Improved Safety
Safety is a top priority in manufacturing environments, and AMRs contribute to creating safer workplaces.
These robots are equipped with advanced sensors and algorithms that allow them to detect and avoid obstacles.
This reduces the risk of accidents and injuries that can occur with human workers performing manual tasks.
Additionally, AMRs can handle hazardous materials, further protecting human workers from potentially dangerous situations.
Flexibility and Scalability
AMRs offer a level of flexibility that traditional manufacturing systems cannot match.
They can be easily reprogrammed and reconfigured to handle different tasks, making them ideal for industries where production needs frequently change.
Additionally, scaling up or down is simpler with AMRs.
New robots can be added to the production line without the need for significant infrastructure changes, allowing manufacturers to respond quickly to market demands.
Applications of AMRs in Manufacturing
AMRs can be utilized in various stages of the manufacturing process.
Material Handling
One of the most common applications of AMRs is material handling.
These robots can transport raw materials, components, and finished products across the factory floor.
Their ability to navigate dynamic environments enables them to optimize delivery routes and reduce bottlenecks, ensuring a smooth flow of materials.
Assembly Line Support
AMRs can also play a crucial role in supporting assembly lines.
They can deliver components directly to workstations, ensuring that workers have the necessary parts to complete their tasks without interruption.
This not only boosts productivity but also reduces the chances of assembly errors due to missing or incorrect components.
Inspection and Quality Control
Ensuring the quality of products is essential in manufacturing.
AMRs equipped with cameras and sensors can inspect products for defects, measure dimensions, and verify assembly accuracy.
Their precision and consistency make them invaluable in maintaining high-quality standards.
Inventory Management
Efficient inventory management is critical for preventing production delays and overstocking.
AMRs can automate inventory checks by scanning barcodes or RFID tags, providing real-time data on stock levels.
This information helps manufacturers make informed decisions about ordering and storage, reducing the risk of shortages or excess inventory.
Challenges in Implementing AMRs
While the benefits of AMRs are substantial, there are challenges to consider during implementation.
High Initial Costs
The initial investment in AMRs can be high, including the cost of the robots, software, and potential modifications to the existing infrastructure.
However, the long-term savings in labor and material costs often justify the upfront expenses.
Complex Integration
Integrating AMRs into existing manufacturing processes can be complex.
It requires careful planning and coordination to ensure that the robots operate seamlessly with other systems and machinery.
This may involve customization of the software and hardware to meet the specific needs of the production line.
Training and Workforce Acceptance
Introducing AMRs into a manufacturing environment necessitates training for employees.
Workers need to understand how to operate and interact with the robots to maximize their efficiency.
Additionally, there may be resistance from employees who fear job displacement.
Addressing these concerns through communication and education is crucial for successful integration.
The Future of AMRs in Manufacturing
As technology continues to advance, the capabilities of AMRs will only improve.
Future AMRs are likely to be more intelligent, with enhanced problem-solving abilities and better integration with other smart factory technologies, such as the Internet of Things (IoT) and artificial intelligence (AI).
This will further boost efficiency and flexibility, making AMRs an indispensable part of modern manufacturing.
In conclusion, Autonomous Mobile Robots (AMRs) are reshaping the landscape of manufacturing.
Their ability to increase efficiency, reduce costs, and improve safety positions them as a valuable asset for factories looking to stay competitive in the global market.
Despite the challenges of implementation, the long-term benefits of AMRs make them a strategic investment for any forward-thinking manufacturing business.
資料ダウンロード
QCD調達購買管理クラウド「newji」は、調達購買部門で必要なQCD管理全てを備えた、現場特化型兼クラウド型の今世紀最高の購買管理システムとなります。
ユーザー登録
調達購買業務の効率化だけでなく、システムを導入することで、コスト削減や製品・資材のステータス可視化のほか、属人化していた購買情報の共有化による内部不正防止や統制にも役立ちます。
NEWJI DX
製造業に特化したデジタルトランスフォーメーション(DX)の実現を目指す請負開発型のコンサルティングサービスです。AI、iPaaS、および先端の技術を駆使して、製造プロセスの効率化、業務効率化、チームワーク強化、コスト削減、品質向上を実現します。このサービスは、製造業の課題を深く理解し、それに対する最適なデジタルソリューションを提供することで、企業が持続的な成長とイノベーションを達成できるようサポートします。
オンライン講座
製造業、主に購買・調達部門にお勤めの方々に向けた情報を配信しております。
新任の方やベテランの方、管理職を対象とした幅広いコンテンツをご用意しております。
お問い合わせ
コストダウンが利益に直結する術だと理解していても、なかなか前に進めることができない状況。そんな時は、newjiのコストダウン自動化機能で大きく利益貢献しよう!
(Β版非公開)