- お役立ち記事
- Achieving business improvements with a trading company’s supply strategy that solves parts processing issues in Rankoshi
月間77,185名の
製造業ご担当者様が閲覧しています*
*2025年2月28日現在のGoogle Analyticsのデータより
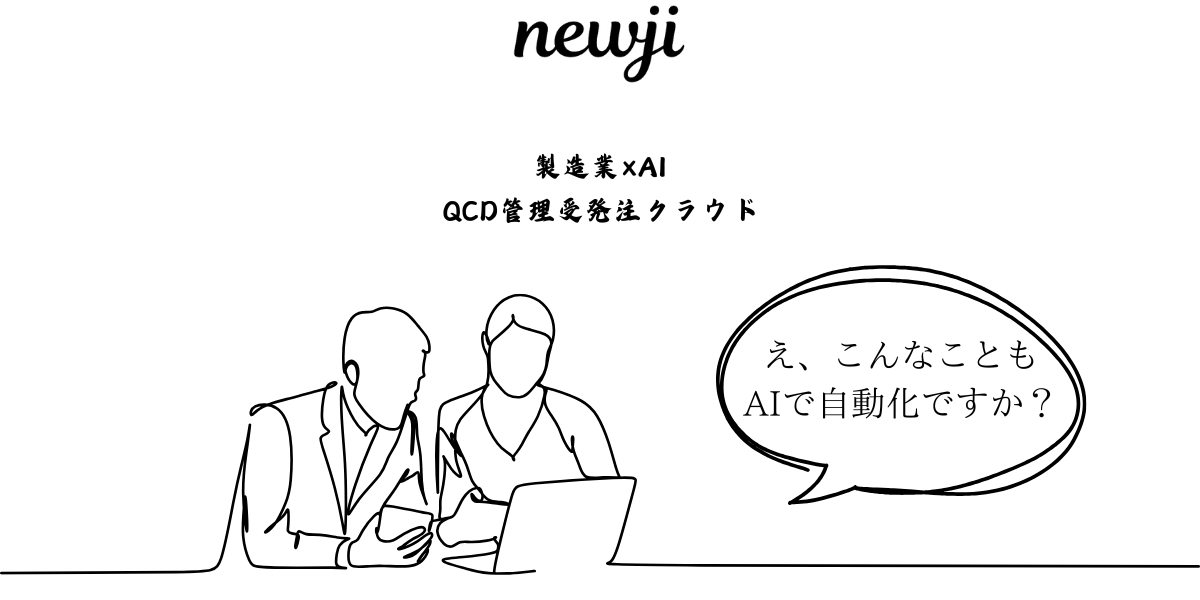
Achieving business improvements with a trading company’s supply strategy that solves parts processing issues in Rankoshi
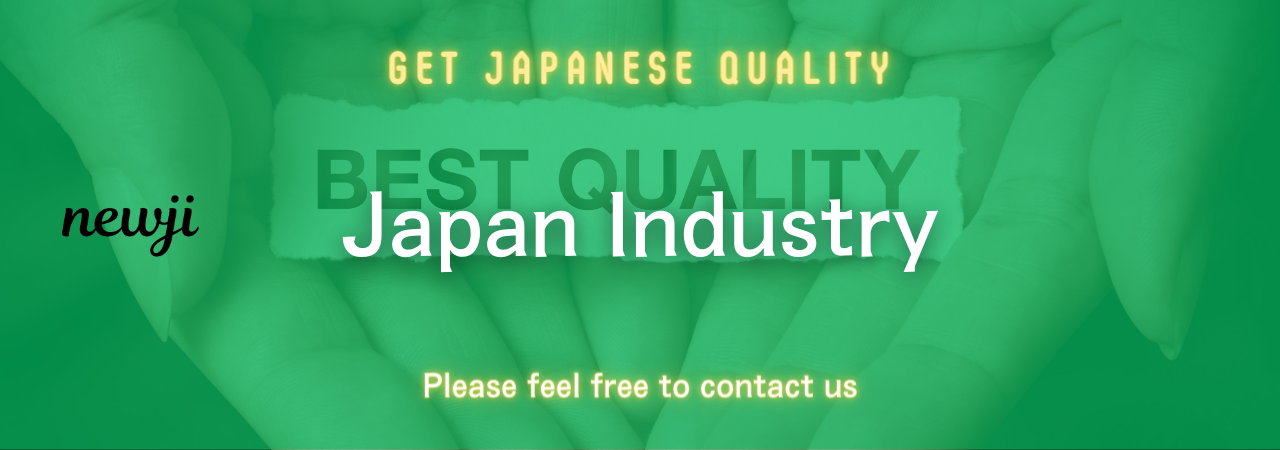
目次
Understanding the Importance of Supply Strategy
In the modern world, businesses need to be agile and efficient to stay competitive.
A key aspect of achieving this is having a robust supply strategy, especially for companies involved in the trading and processing of parts.
For trading companies in Rankoshi, addressing parts processing issues and improving supply strategies can lead to significant business improvements.
A well-engineered supply strategy can streamline operations, reduce costs, and enhance customer satisfaction, ultimately leading to business growth.
Identifying Parts Processing Challenges
Before implementing an improved supply strategy, it’s crucial to identify the parts processing challenges faced by trading companies in Rankoshi.
Common issues include delays in delivery, quality inconsistencies, and inefficiencies in the ordering process.
Such challenges can arise due to poor communication between suppliers and trading companies or inadequate inventory management systems.
Understanding these obstacles helps businesses design more effective solutions.
Common Issues in Parts Processing
One of the frequent issues is the delay in obtaining parts from suppliers.
This can occur due to logistical errors, inefficient transportation systems, or supplier shortages.
Other notable challenges include discrepancies in parts specifications which can lead to quality issues or mismatches in product requirements.
Additionally, customer expectations for faster turnarounds and lower costs exert continuous pressure on trading companies to optimize their processes.
Designing a Supply Strategy for Improvement
Developing a supply strategy that addresses these processing challenges can foster significant business improvements.
The first step is to establish clear communication channels between all parties involved.
Enhanced collaboration ensures that there is a mutual understanding of quality standards, delivery timelines, and other critical requirements.
This cooperation reduces the likelihood of misunderstandings and errors.
Incorporating Technology into Processes
Integrating technology into supply processes is a game-changer for trading companies.
Utilizing advanced inventory management systems can help companies maintain optimal stock levels and reduce wastage.
Automation tools can streamline ordering and shipping processes, resulting in faster turnaround times.
Moreover, using data analytics can provide valuable insights that help anticipate demand and supply trends, aiding in more accurate planning and decision-making.
Optimizing Supply Chain Operations
An optimized supply chain can dramatically improve a company’s efficiency and performance.
The goal is to create a seamless operation that minimizes disruptions and maximizes productivity.
By optimizing the supply chain, trading companies in Rankoshi can better manage their parts processing operations and meet client demands promptly.
Supplier Relationship Management
Building strong relationships with suppliers is a critical component of an optimized supply chain.
By fostering open communication and strong partnerships, trading companies can work closely with suppliers to ensure that they receive the best quality parts at competitive prices.
Strategic collaborations with suppliers can also help businesses navigate unforeseen challenges more effectively.
Furthermore, by prioritizing suppliers known for reliability and excellence, companies can strengthen their supply chain’s resilience.
Inventory Management Efficiency
Efficient inventory management is central to a successful supply strategy.
Companies should strive to implement just-in-time (JIT) inventory practices to reduce excess stock and minimize storage costs.
This approach requires precise forecasting to ensure that the company always has the right amount of stock available without over-committing resources.
Regular audits and technological upgrades can further enhance inventory management practices.
Impact of an Enhanced Supply Strategy
When a trading company in Rankoshi successfully addresses parts processing issues with a robust supply strategy, the impact on the business can be substantial.
Efficient supply strategies lead to reduced operational costs and increased profitability.
Moreover, the ability to meet customer demands promptly boosts customer satisfaction and loyalty, resulting in increased sales and a stronger market position.
Improved Customer Satisfaction
Providing reliable and fast service is critical in differentiating a company from its competitors.
With a well-orchestrated supply strategy, businesses can ensure timely delivery of quality products, fulfilling customer expectations and building lasting relationships.
Satisfied customers are more likely to return and recommend the company to others, contributing to growth.
Cost-Effectiveness and Revenue Growth
An improved supply chain reduces waste and inefficiencies, lowering operational costs.
Consequently, businesses can optimize their pricing strategies and offer competitive prices that attract more customers.
Revenue growth can be sustained because the company operates efficiently, maintains quality, and adapts to market changes swiftly.
Conclusion
A trading company’s ability to improve its business operations hinges on its supply strategy.
By addressing parts processing issues and optimizing their supply chain, Rankoshi-based companies can achieve significant business improvements.
The journey involves assessing current challenges, integrating technology, enhancing supplier relationships, and maintaining efficient inventory management.
The result is a more agile, responsive business that meets customer needs and fosters long-term growth.
資料ダウンロード
QCD管理受発注クラウド「newji」は、受発注部門で必要なQCD管理全てを備えた、現場特化型兼クラウド型の今世紀最高の受発注管理システムとなります。
ユーザー登録
受発注業務の効率化だけでなく、システムを導入することで、コスト削減や製品・資材のステータス可視化のほか、属人化していた受発注情報の共有化による内部不正防止や統制にも役立ちます。
NEWJI DX
製造業に特化したデジタルトランスフォーメーション(DX)の実現を目指す請負開発型のコンサルティングサービスです。AI、iPaaS、および先端の技術を駆使して、製造プロセスの効率化、業務効率化、チームワーク強化、コスト削減、品質向上を実現します。このサービスは、製造業の課題を深く理解し、それに対する最適なデジタルソリューションを提供することで、企業が持続的な成長とイノベーションを達成できるようサポートします。
製造業ニュース解説
製造業、主に購買・調達部門にお勤めの方々に向けた情報を配信しております。
新任の方やベテランの方、管理職を対象とした幅広いコンテンツをご用意しております。
お問い合わせ
コストダウンが利益に直結する術だと理解していても、なかなか前に進めることができない状況。そんな時は、newjiのコストダウン自動化機能で大きく利益貢献しよう!
(β版非公開)