- お役立ち記事
- Achieving Cost Reduction and Product Value Enhancement with VE/VA Implementation
月間76,176名の
製造業ご担当者様が閲覧しています*
*2025年3月31日現在のGoogle Analyticsのデータより
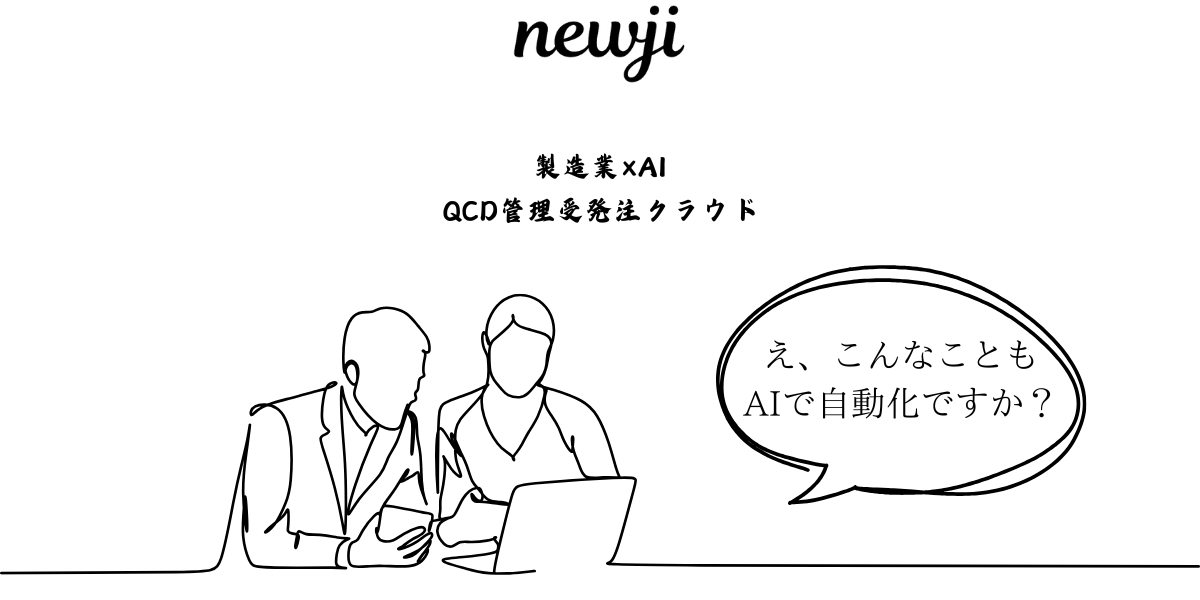
Achieving Cost Reduction and Product Value Enhancement with VE/VA Implementation
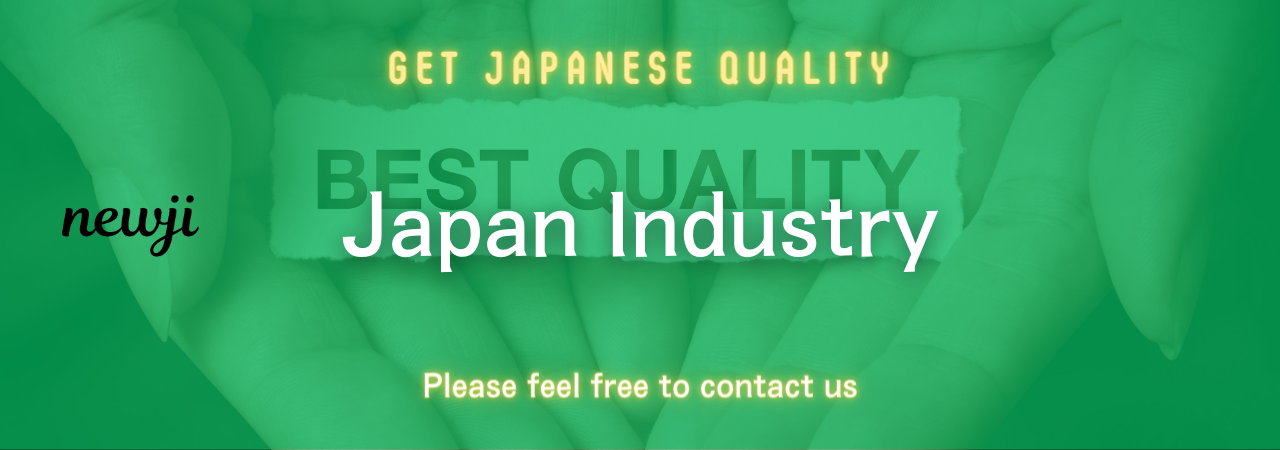
目次
Understanding VE/VA Methodologies
Value Engineering (VE) and Value Analysis (VA) are systematic approaches used by businesses to improve the value of a product or service by finding the perfect balance between necessary function, cost, and quality.
These methodologies aim to ensure that the final product meets customer needs at the lowest possible cost.
While VE is primarily applied during the product design phase, VA is often used to enhance existing products.
Both VE and VA involve a thorough evaluation process, where cost-saving opportunities and improvements are identified without compromising on functionality or quality.
The Importance of Cost Reduction
In today’s competitive market, cost reduction is a critical factor for businesses seeking to maximize profitability.
Implementing VE/VA methodologies can significantly help in reducing unnecessary costs by eliminating waste, optimizing resources, and utilizing alternative solutions.
Cost reduction not only enhances profit margins but also allows companies to offer more competitive pricing, thus attracting more customers.
Additionally, reduced costs can free up capital for reinvestment in other areas, such as innovation, marketing, or expanding product lines.
Enhancing Product Value
Product value is a combination of quality, functionality, and price.
Enhancing the value of a product means offering more benefits to customers, which can be achieved through the VE/VA processes.
VE/VA focuses on understanding customer needs and preferences, which allows businesses to tailor their products to better meet those needs.
Through value enhancement, companies can differentiate their products from competitors, leading to increased market share and customer loyalty.
Steps in Implementing VE/VA
The implementation of VE/VA involves several crucial steps.
These steps ensure that the methodologies are effectively applied to maximize savings and enhance product value.
1. Information Gathering
The first step is to gather all necessary information about the product or service.
This includes specifications, production processes, customer requirements, and cost data.
Understanding these factors is essential for identifying potential areas for improvement.
2. Functional Analysis
Functional analysis involves reviewing the various functions of a product to determine which are essential and which could be modified or eliminated.
By prioritizing essential functions, businesses can focus on optimizing costs related to these areas.
3. Creative Development
This step involves brainstorming and generating ideas for alternatives and improvements.
Involving a diverse team in this process can lead to innovative solutions that might not have been considered otherwise.
4. Evaluation and Selection
After generating ideas, the next step is to evaluate them based on feasibility, cost implications, and potential impact on product value.
Select the best options that align with the company’s strategic goals and customer needs.
5. Implementation
In this phase, the selected ideas are implemented into the product design or process.
This might involve redesigning components, altering production methods, or sourcing new materials.
6. Review and Appraisal
The final step is to review the implemented changes to assess their effectiveness.
This involves measuring cost savings, evaluating customer feedback, and determining any further adjustments needed to optimize the product.
Challenges and Considerations
Though VE/VA can offer significant benefits, there are challenges and considerations businesses should be aware of during implementation.
Stakeholder Buy-In
Getting buy-in from all stakeholders, including employees, suppliers, and management, is crucial for the success of VE/VA initiatives.
Stakeholders need to be convinced of the benefits and be willing to adapt to changes in processes or materials.
Resource Allocation
Implementing VE/VA requires time, personnel, and financial investment.
Allocating resources effectively can be challenging but is necessary for a successful outcome.
Companies need to ensure they have the right mix of skills and expertise within their teams to effectively carry out these methodologies.
Balancing Cost and Quality
Achieving cost savings without sacrificing quality is a delicate balance that businesses must maintain when implementing VE/VA.
The focus should remain on retaining essential functions and ensuring that any changes do not negatively impact the overall quality of the product or service.
Continuous Improvement
VE/VA should not be viewed as a one-time initiative but as an ongoing process of continuous improvement.
Even after initial cost reductions and value enhancements, continued evaluation and optimization should be a part of standard business practices.
Conclusion
VE/VA methodologies offer a powerful means for businesses to achieve cost reduction and enhance product value.
By systematically analyzing and improving product functions, companies can offer better value to customers while maintaining profitability.
Despite the challenges involved, with careful planning and execution, the benefits can significantly outweigh the costs, leading to long-term business success.
By prioritizing these strategies, organizations can ensure sustainable growth and a competitive edge in their respective industries.
資料ダウンロード
QCD管理受発注クラウド「newji」は、受発注部門で必要なQCD管理全てを備えた、現場特化型兼クラウド型の今世紀最高の受発注管理システムとなります。
ユーザー登録
受発注業務の効率化だけでなく、システムを導入することで、コスト削減や製品・資材のステータス可視化のほか、属人化していた受発注情報の共有化による内部不正防止や統制にも役立ちます。
NEWJI DX
製造業に特化したデジタルトランスフォーメーション(DX)の実現を目指す請負開発型のコンサルティングサービスです。AI、iPaaS、および先端の技術を駆使して、製造プロセスの効率化、業務効率化、チームワーク強化、コスト削減、品質向上を実現します。このサービスは、製造業の課題を深く理解し、それに対する最適なデジタルソリューションを提供することで、企業が持続的な成長とイノベーションを達成できるようサポートします。
製造業ニュース解説
製造業、主に購買・調達部門にお勤めの方々に向けた情報を配信しております。
新任の方やベテランの方、管理職を対象とした幅広いコンテンツをご用意しております。
お問い合わせ
コストダウンが利益に直結する術だと理解していても、なかなか前に進めることができない状況。そんな時は、newjiのコストダウン自動化機能で大きく利益貢献しよう!
(β版非公開)