- お役立ち記事
- Achieving Dramatic Precision Improvements with IDM Small Bore Internal Diameter Measurement Instruments
Achieving Dramatic Precision Improvements with IDM Small Bore Internal Diameter Measurement Instruments
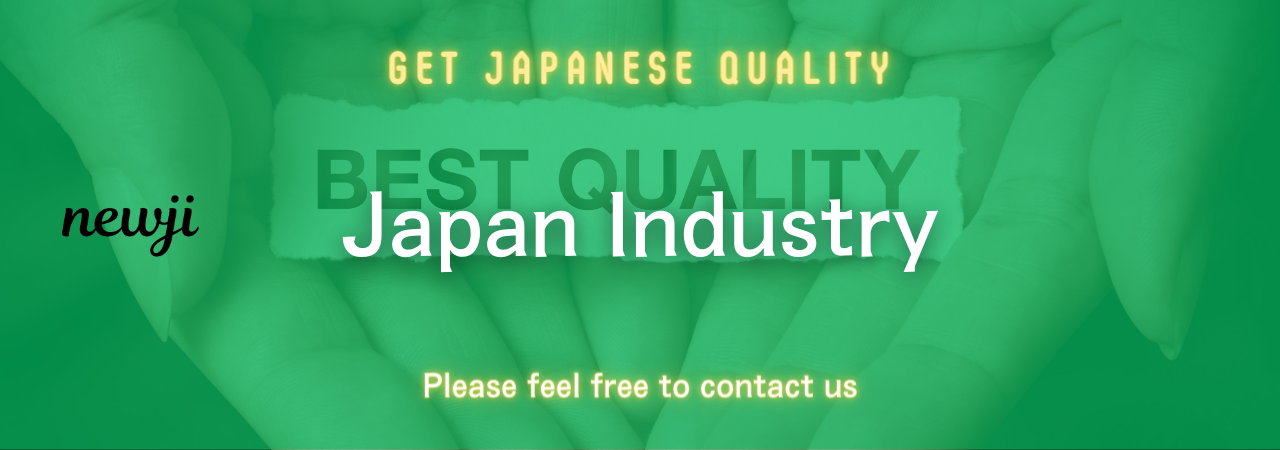
In the world of manufacturing and engineering, the need for precision is paramount.
A minor error can lead to significant issues, causing problems in the final product’s quality and functionality.
One of the critical aspects of ensuring accuracy is through precise measurement instruments.
This article delves into how IDM small bore internal diameter measurement instruments can dramatically improve precision.
目次
Understanding IDM Small Bore Internal Diameter Measurement Instruments
Before exploring the benefits, it’s essential to understand what IDM small bore internal diameter measurement instruments are.
IDM stands for Internal Diameter Measurement.
These instruments are specifically designed to measure the internal diameters of small bores or cavities with a high degree of accuracy.
They are crucial in various industries where precision is non-negotiable, including aerospace, automotive, and medical device manufacturing.
Types of IDM Instruments
There are several types of IDM instruments available, each designed to suit specific needs and applications.
Some common types include:
1. Indicating Micrometers
These are precision instruments used for measuring small internal diameters.
They provide digital readings and are known for their high accuracy.
Indicating micrometers are particularly useful in applications where the utmost precision is required.
2. Bore Gauges
Bore gauges are another popular type of IDM instrument.
They are designed with a measuring head that expands and contracts to fit the bore’s internal diameter.
Bore gauges offer quick and accurate measurements, making them ideal for production settings where speed and precision are essential.
3. Air Gauges
Air gauges use air pressure to measure the internal diameter of small bores.
They are non-contact devices, which means they can measure delicate or soft materials without causing any damage.
Why Precision Matters
In any manufacturing process, maintaining exact dimensions is crucial for several reasons.
Precision ensures that parts fit together correctly, which is vital for the proper functioning of the final product.
Inaccurate measurements can lead to faulty assemblies, resulting in product failure or compromised performance.
Moreover, precision is critical for maintaining quality and consistency in mass production.
Even a small deviation in dimensions can lead to significant variations in the final products, affecting the overall quality.
Benefits of Using IDM Small Bore Internal Diameter Measurement Instruments
Utilizing IDM instruments offers several advantages, primarily revolving around improved precision and efficiency.
Enhanced Accuracy
One of the most significant benefits of IDM instruments is their enhanced accuracy.
These tools are designed to provide precise measurements, often down to microns.
This level of accuracy ensures that even the smallest variations are detected and corrected, leading to better overall product quality.
Consistency in Production
IDM instruments offer consistent and repeatable measurements.
This consistency is crucial in production settings, where maintaining uniformity across batches is essential.
With IDM instruments, manufacturers can achieve a higher level of consistency, reducing the risk of errors and defects.
Time Efficiency
Measuring small bores with traditional methods can be time-consuming and labor-intensive.
IDM instruments streamline the process, offering quick and efficient measurements.
This time efficiency translates to increased productivity and reduced downtime in the production line.
Versatility
IDM instruments are versatile and can be used across various applications and industries.
Whether you are in automotive manufacturing or producing medical devices, these instruments can cater to your specific measurement needs.
Applications of IDM Small Bore Internal Diameter Measurement Instruments
IDM instruments are utilized in several industries, each benefiting from their unique capabilities.
Aerospace Industry
In aerospace, precision is crucial for ensuring the safety and reliability of aircraft components.
IDM instruments are used to measure the internal diameters of small bores in critical components such as fuel systems and hydraulic systems.
Accurate measurements help maintain the exacting standards required in this industry.
Automotive Industry
In the automotive sector, IDM instruments are used to measure engine components, transmission parts, and other critical elements.
Precision measurements ensure that these components fit together perfectly, contributing to the overall performance and efficiency of the vehicle.
Medical Device Manufacturing
The production of medical devices requires a high degree of precision to ensure that they function correctly and safely.
IDM instruments are used to measure the internal diameters of components such as syringes, catheters, and implants.
Accurate measurements are essential to meet stringent quality standards in this industry.
Choosing the Right IDM Instrument
Selecting the appropriate IDM instrument depends on several factors, including the specific application, the required level of precision, and the material being measured.
Here are some tips to help you choose the right IDM instrument:
Identify Your Needs
Determine the specific requirements of your application.
Consider factors such as the size of the bore, the material, and the required level of precision.
This will help you narrow down your options and choose an instrument that best suits your needs.
Consider the Environment
The working environment can impact the performance of IDM instruments.
For instance, air gauges may not perform well in dusty or humid conditions.
Consider the environmental factors and choose an instrument that can function optimally in your specific setting.
Check the Calibration and Maintenance Requirements
Ensure that the IDM instrument you choose can be easily calibrated and maintained.
Regular calibration is essential for maintaining accuracy, so opt for instruments that offer straightforward calibration procedures and minimal maintenance requirements.
Conclusion
Improving precision with IDM small bore internal diameter measurement instruments offers numerous advantages, from enhanced accuracy and consistency to increased time efficiency and versatility.
These instruments are invaluable in industries where precision is critical, ensuring that final products meet the exacting standards required.
By investing in the right IDM instruments and leveraging their capabilities, manufacturers can achieve dramatic improvements in precision, ultimately leading to better quality and more reliable products.
資料ダウンロード
QCD調達購買管理クラウド「newji」は、調達購買部門で必要なQCD管理全てを備えた、現場特化型兼クラウド型の今世紀最高の購買管理システムとなります。
ユーザー登録
調達購買業務の効率化だけでなく、システムを導入することで、コスト削減や製品・資材のステータス可視化のほか、属人化していた購買情報の共有化による内部不正防止や統制にも役立ちます。
NEWJI DX
製造業に特化したデジタルトランスフォーメーション(DX)の実現を目指す請負開発型のコンサルティングサービスです。AI、iPaaS、および先端の技術を駆使して、製造プロセスの効率化、業務効率化、チームワーク強化、コスト削減、品質向上を実現します。このサービスは、製造業の課題を深く理解し、それに対する最適なデジタルソリューションを提供することで、企業が持続的な成長とイノベーションを達成できるようサポートします。
オンライン講座
製造業、主に購買・調達部門にお勤めの方々に向けた情報を配信しております。
新任の方やベテランの方、管理職を対象とした幅広いコンテンツをご用意しております。
お問い合わせ
コストダウンが利益に直結する術だと理解していても、なかなか前に進めることができない状況。そんな時は、newjiのコストダウン自動化機能で大きく利益貢献しよう!
(Β版非公開)