- お役立ち記事
- Achieving High Stability with Clamp & Fastener OEM Manufacturing
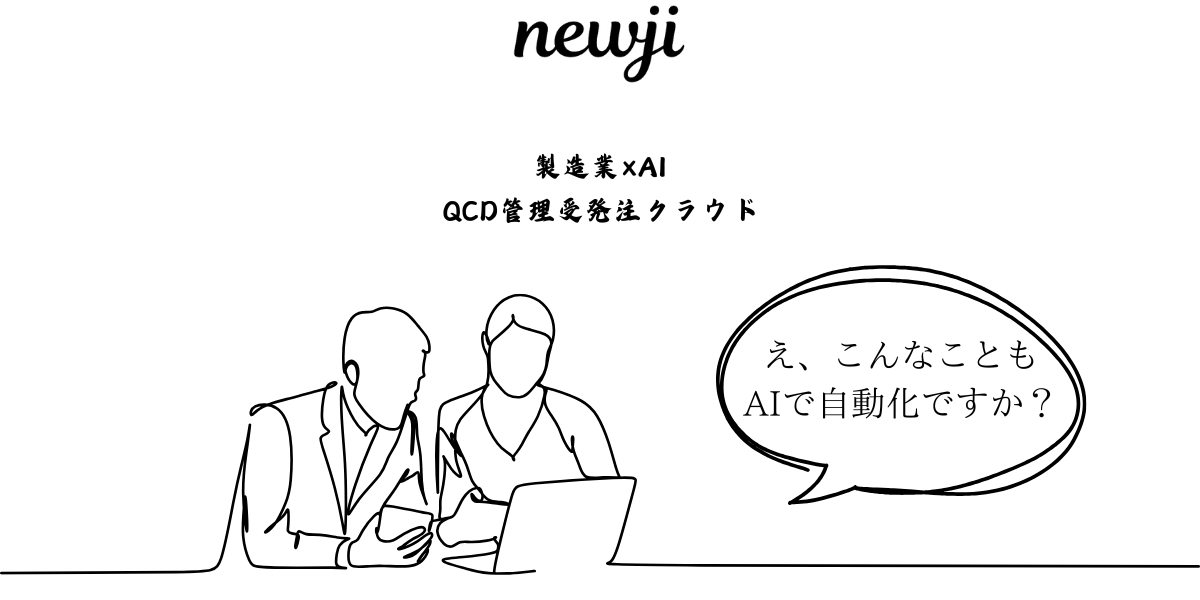
Achieving High Stability with Clamp & Fastener OEM Manufacturing
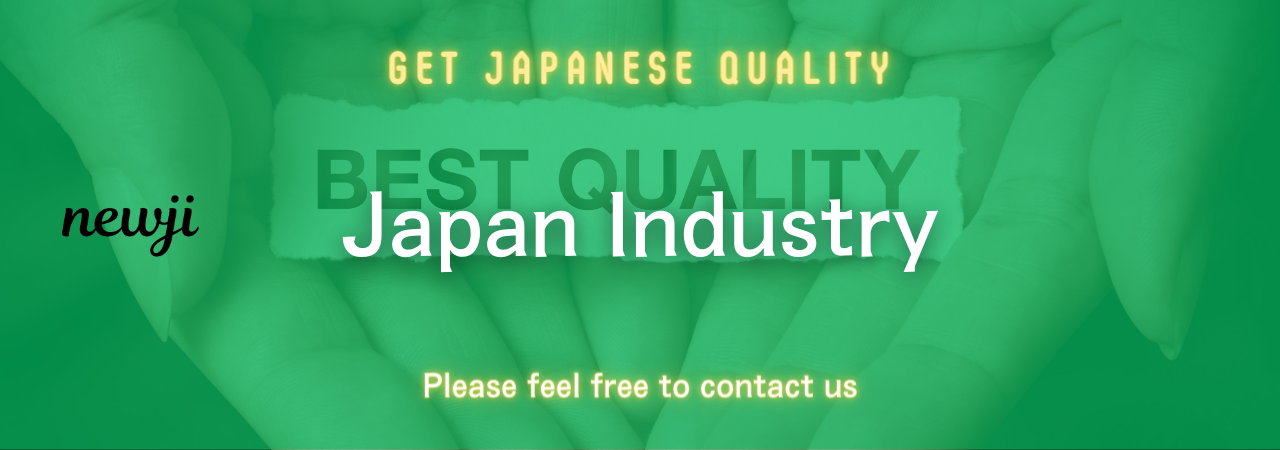
When it comes to securing components in various industrial settings, the reliability of clamps and fasteners cannot be overstated. These elements play a crucial role in maintaining the stability and safety of machinery, infrastructure, and countless other applications. Hence, investing in high-quality OEM (Original Equipment Manufacturer) manufacturing for clamps and fasteners is essential for achieving high stability. This article will delve into the key aspects of clamp and fastener OEM manufacturing, illustrating why they matter and how they can be optimized for maximum performance.
目次
Understanding the Importance of Clamps and Fasteners
Clamps and fasteners are more than just simple hardware. They are integral to the integrity of assemblies and structures, ensuring that every part holds together securely. These components are widely used in various industries, including automotive, aerospace, construction, and electronics, among others. A failure in any clamp or fastener could lead to catastrophic results, affecting both safety and functionality.
Types of Clamps and Fasteners
Various types of clamps and fasteners are designed to meet specific needs. Some common types include:
– **Bolts and nuts**: Frequently used in engines, machinery, and construction.
– **Screw clamps**: Ideal for applications requiring adjustable pressure.
– **Spring clamps**: Useful for quick and temporary securing needs.
– **Hose clamps**: Designed to secure hoses onto fittings, making them vital in plumbing and automotive applications.
Each type has its unique properties and uses, making it essential to select the right kind for a given application.
Why Choose OEM Manufacturing for Clamps and Fasteners?
OEM manufacturing offers several advantages that make it the preferred choice for producing clamps and fasteners.
Quality Assurance
OEM manufacturers adhere to stringent quality control measures. As a result, the clamps and fasteners produced under OEM guidelines are often of higher quality compared to generic alternatives. This ensures that they meet industry standards and perform reliably in demanding conditions.
Customization Options
OEM manufacturing allows for a high degree of customization. Companies can request specific materials, sizes, and designs tailored to their unique requirements. This flexibility ensures that the final product fits perfectly into its intended application, thereby enhancing stability and performance.
Cost-Effectiveness
Though OEM parts may come with a higher upfront cost, they often prove to be more economical in the long run. High-quality, reliable components can reduce the frequency of maintenance and replacements. This translates into less downtime and cost-savings over time.
Material Considerations in OEM Manufacturing
The choice of material is a critical factor in the effectiveness of clamps and fasteners. Different materials offer various strengths, weaknesses, and suitability for specific applications.
Common Materials
– **Steel**: Known for its strength and durability, making it ideal for heavy-duty applications.
– **Stainless Steel**: Offers excellent resistance to corrosion, suitable for environments where moisture or chemicals are present.
– **Aluminum**: Lightweight and easy to work with, commonly used in applications where weight is a concern.
– **Plastic**: Used for light-duty applications where corrosion resistance and non-conductivity are required.
Choosing the Right Material
Selecting the appropriate material depends on several factors, including the application’s load requirements, environmental conditions, and expected lifespan. Consulting with an experienced OEM manufacturer can help identify the best material for your specific needs, ensuring optimal performance and longevity.
Innovations in Clamp and Fastener Design
Advancements in technology have led to innovative designs that offer improved functionality and ease of use. Various design improvements aim to enhance the stability and efficiency of clamps and fasteners.
Ergonomic Designs
Modern clamps and fasteners often feature ergonomic designs that make them easier to handle and install. These designs not only minimize the risk of injury but also speed up the assembly process.
Self-Locking Mechanisms
Many modern fasteners now incorporate self-locking mechanisms. These designs ensure that the fasteners remain securely in place, reducing the risk of loosening over time and thereby maintaining long-term stability.
Quick-Release Features
Quick-release clamps and fasteners are designed for applications requiring frequent adjustments or disassembly. These features allow for fast and convenient changes without compromising on security.
Testing and Validation
OEM manufacturers often employ rigorous testing protocols to ensure the reliability of their products. These tests evaluate various aspects, including:
– **Load capacity**: Ensuring that the clamp or fastener can withstand the required forces.
– **Corrosion resistance**: Testing for durability in different environmental conditions.
– **Fatigue testing**: Assessing the longevity and performance under continuous use.
Such comprehensive testing ensures that the clamps and fasteners will perform as expected, providing peace of mind to the end-users.
Compliance with Standards
Compliance with industry standards is another significant benefit of opting for OEM manufacturing. These standards ensure that the products meet specific criteria for safety, quality, and performance. Common standards include:
– **ISO (International Organization for Standardization)**: Sets international standards across various industries.
– **ASTM (American Society for Testing and Materials)**: Provides voluntary consensus standards for materials and products.
Having clamps and fasteners that comply with these standards ensures compatibility and reliability across different applications and industries.
Working with a Reliable OEM Manufacturer
The importance of selecting a reliable OEM manufacturer cannot be overstated. A reputable manufacturer will offer not only high-quality products but also comprehensive support services, including design consultation, material selection, and after-sales support. When choosing a manufacturer, consider their track record, industry experience, and customer testimonials.
The Role of Customer Feedback
Customer feedback can provide valuable insights into the performance and reliability of OEM products. Manufacturers that prioritize customer satisfaction are more likely to produce high-quality clamps and fasteners that meet or exceed expectations.
Conclusion
Achieving high stability with clamps and fasteners requires careful consideration of several factors, including material selection, design, and manufacturing quality. OEM manufacturing stands out as the best approach for ensuring that these critical components meet stringent standards and deliver reliable performance. By partnering with a trusted OEM manufacturer, businesses can achieve enhanced stability, safety, and cost-effectiveness in their various applications.
資料ダウンロード
QCD調達購買管理クラウド「newji」は、調達購買部門で必要なQCD管理全てを備えた、現場特化型兼クラウド型の今世紀最高の購買管理システムとなります。
ユーザー登録
調達購買業務の効率化だけでなく、システムを導入することで、コスト削減や製品・資材のステータス可視化のほか、属人化していた購買情報の共有化による内部不正防止や統制にも役立ちます。
NEWJI DX
製造業に特化したデジタルトランスフォーメーション(DX)の実現を目指す請負開発型のコンサルティングサービスです。AI、iPaaS、および先端の技術を駆使して、製造プロセスの効率化、業務効率化、チームワーク強化、コスト削減、品質向上を実現します。このサービスは、製造業の課題を深く理解し、それに対する最適なデジタルソリューションを提供することで、企業が持続的な成長とイノベーションを達成できるようサポートします。
オンライン講座
製造業、主に購買・調達部門にお勤めの方々に向けた情報を配信しております。
新任の方やベテランの方、管理職を対象とした幅広いコンテンツをご用意しております。
お問い合わせ
コストダウンが利益に直結する術だと理解していても、なかなか前に進めることができない状況。そんな時は、newjiのコストダウン自動化機能で大きく利益貢献しよう!
(Β版非公開)