- お役立ち記事
- Achieving Precision in Guide Bush Design and Manufacturing
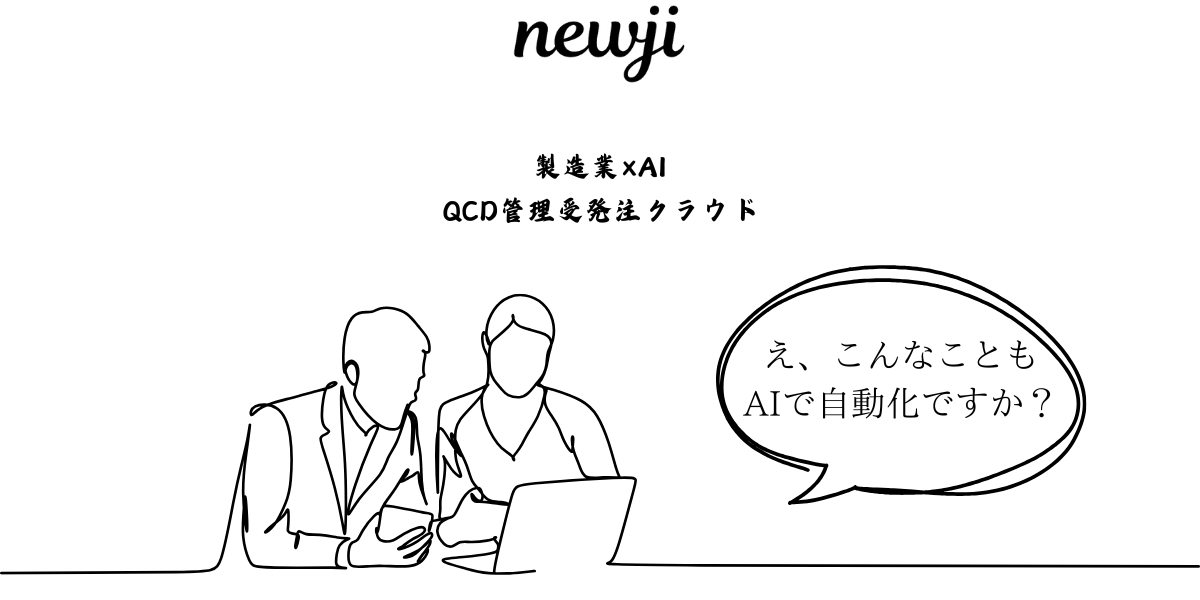
Achieving Precision in Guide Bush Design and Manufacturing
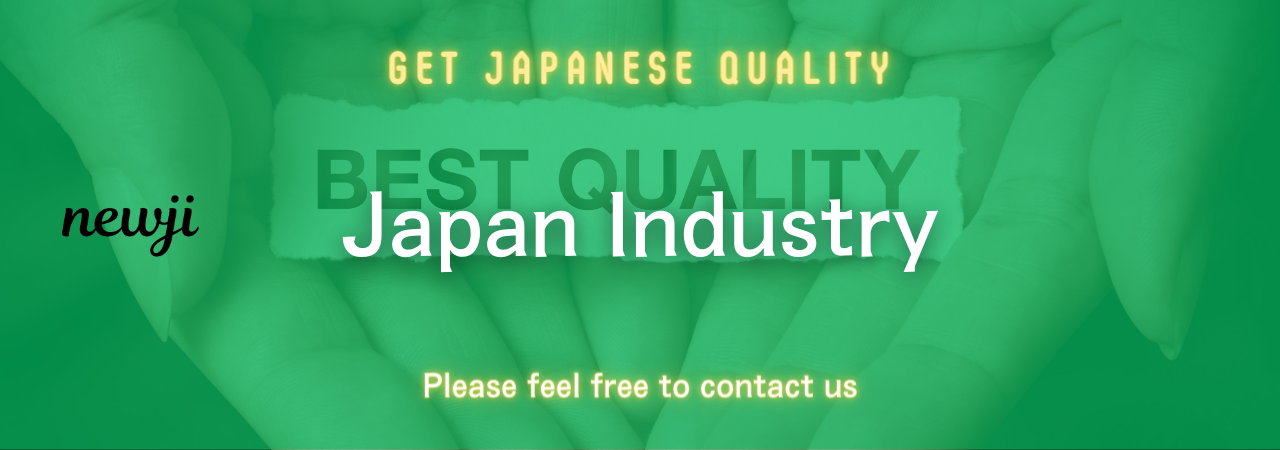
In the world of precision engineering, guide bushes play a crucial role. Their primary function is to guide and position workpieces, ensuring accuracy and efficiency in various machining processes. Achieving precision in guide bush design and manufacturing is essential to meet the stringent demands of modern industries. This article delves into the critical aspects of guide bush design and manufacturing, providing insights into achieving the highest precision levels.
目次
Understanding Guide Bushes
Guide bushes are components used to guide cutting tools or workpieces with high precision. They are commonly used in CNC machines, lathes, and other machining equipment. Guide bushes can be found in various industries, including automotive, aerospace, medical devices, and electronics. The primary objective of a guide bush is to ensure that the tool or workpiece moves in a predetermined path, reducing errors and ensuring consistent quality.
Materials for Guide Bushes
The choice of materials for guide bushes is critical for achieving precision and longevity. Various materials are used based on the application requirements, such as steel, carbide, and ceramic. Each material has its advantages and limitations.
Steel: Steel is a common choice due to its durability and machinability. Hardened and ground steel guide bushes offer excellent wear resistance and can withstand high loads and temperatures.
Carbide: Carbide guide bushes are known for their exceptional hardness and wear resistance. They are ideal for applications where high precision and durability are essential, such as in high-speed machining.
Ceramic: Ceramic guide bushes are used when exceptionally high temperatures and wear resistance are required. They are highly resistant to corrosion and can maintain precision even in challenging environments.
Key Design Considerations
Achieving precision in guide bush design requires careful consideration of several factors. These include tolerances, geometry, surface finish, and lubrication.
Tolerances
Tolerances are critical in guide bush design because they determine the accuracy and fit of the guide bush with other components. Tight tolerances are essential to minimize errors in positioning and guiding. Manufacturers often use advanced measuring equipment and techniques to ensure that tolerances are within the prescribed limits.
Geometry
The geometry of a guide bush influences its performance. The shape and size must be optimized to provide the desired guiding properties. Engineers must carefully consider factors such as the length-to-diameter ratio, angle of contact, and surface roughness. Proper geometry ensures that the guide bush maintains a stable and precise guiding path.
Surface Finish
The surface finish of a guide bush is crucial for minimizing friction and wear. A smooth surface finish reduces friction between the guide bush and the tool or workpiece, leading to improved accuracy and longer tool life. Polishing and grinding techniques are commonly used to achieve the desired surface finish.
Lubrication
Lubrication is essential to reduce friction and wear in guide bushes. Proper lubrication ensures smooth movement and minimizes the risk of overheating. Engineers must select the appropriate lubricant based on the operating conditions, such as temperature, speed, and load. Regular maintenance and inspection of lubrication systems are essential to ensure optimal performance.
Manufacturing Techniques
The manufacturing process for guide bushes involves several steps, each critical for achieving the desired precision. These steps include material selection, machining, heat treatment, grinding, and quality control.
Material Selection
Selecting the right material is the first step in manufacturing precise guide bushes. The material must meet the specific requirements of the application. Once the material is chosen, it undergoes various machining processes to achieve the desired shape and size.
Machining
Machining is a critical step in guide bush manufacturing. Precision machining techniques, such as turning, milling, and drilling, are used to create the initial shape and dimensions. CNC machines are often used for their high accuracy and repeatability.
Heat Treatment
Heat treatment is used to enhance the hardness and wear resistance of guide bushes. This process involves heating the material to a specific temperature and then cooling it at a controlled rate. Heat treatment improves the mechanical properties of the material, ensuring durability and precision.
Grinding
Grinding is a crucial step in achieving the final dimensional accuracy and surface finish of guide bushes. Precision grinding machines are used to achieve tight tolerances and smooth surfaces. This step is essential for ensuring that the guide bush meets the required specifications.
Quality Control
Quality control is a critical aspect of guide bush manufacturing. Advanced measuring equipment, such as coordinate measuring machines (CMMs) and optical comparators, is used to inspect the dimensions and surface finish. Quality control ensures that the guide bush meets the specified tolerances and performance requirements.
Applications of Guide Bushes
Guide bushes are used in a wide range of applications, where precision and reliability are paramount.
Automotive Industry
In the automotive industry, guide bushes are used in various machining processes, such as engine component manufacturing and transmission systems. They ensure accurate positioning and alignment, leading to high-quality products.
Aerospace Industry
The aerospace industry requires the highest levels of precision. Guide bushes are used in the machining of critical components, such as turbine blades and landing gear. They ensure that these components meet stringent quality and safety standards.
Medical Devices
In the medical device industry, guide bushes are used in the manufacturing of surgical instruments and implants. Precision is crucial to ensure the safety and effectiveness of these devices.
Electronics Industry
In the electronics industry, guide bushes are used in the production of components such as connectors and printed circuit boards (PCBs). They ensure accurate and consistent machining, leading to reliable electronic products.
Achieving precision in guide bush design and manufacturing is a complex process that requires careful consideration of materials, design factors, and manufacturing techniques.
By following best practices and using advanced technologies, manufacturers can produce guide bushes that meet the highest standards of accuracy and reliability.
Whether used in the automotive, aerospace, medical, or electronics industry, precision guide bushes play a vital role in ensuring the quality and performance of machined components.
資料ダウンロード
QCD調達購買管理クラウド「newji」は、調達購買部門で必要なQCD管理全てを備えた、現場特化型兼クラウド型の今世紀最高の購買管理システムとなります。
ユーザー登録
調達購買業務の効率化だけでなく、システムを導入することで、コスト削減や製品・資材のステータス可視化のほか、属人化していた購買情報の共有化による内部不正防止や統制にも役立ちます。
NEWJI DX
製造業に特化したデジタルトランスフォーメーション(DX)の実現を目指す請負開発型のコンサルティングサービスです。AI、iPaaS、および先端の技術を駆使して、製造プロセスの効率化、業務効率化、チームワーク強化、コスト削減、品質向上を実現します。このサービスは、製造業の課題を深く理解し、それに対する最適なデジタルソリューションを提供することで、企業が持続的な成長とイノベーションを達成できるようサポートします。
オンライン講座
製造業、主に購買・調達部門にお勤めの方々に向けた情報を配信しております。
新任の方やベテランの方、管理職を対象とした幅広いコンテンツをご用意しております。
お問い合わせ
コストダウンが利益に直結する術だと理解していても、なかなか前に進めることができない状況。そんな時は、newjiのコストダウン自動化機能で大きく利益貢献しよう!
(Β版非公開)