- お役立ち記事
- Achieving Precision Parts through OEM Wet Etching Processing
Achieving Precision Parts through OEM Wet Etching Processing
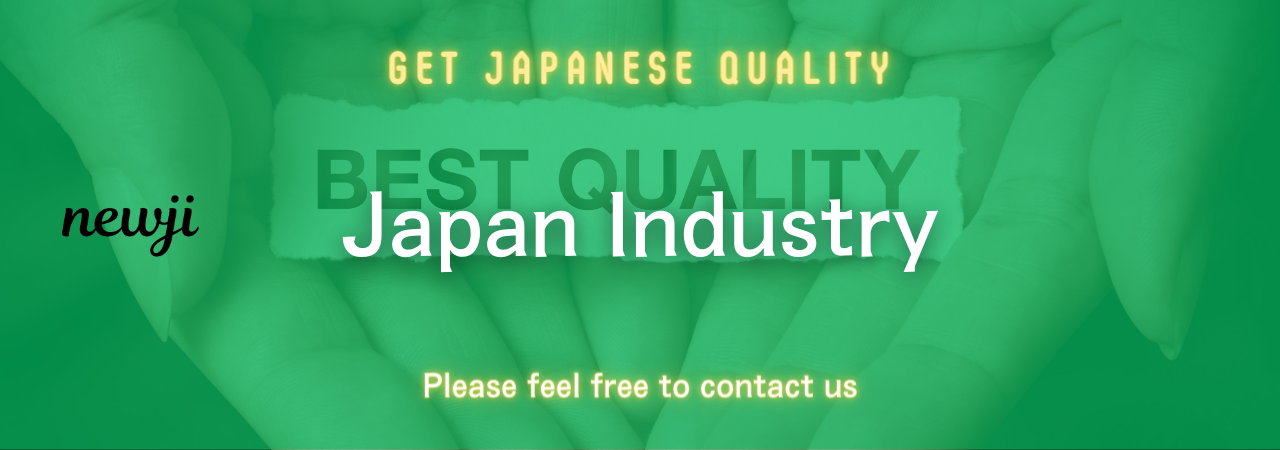
目次
Introduction to Wet Etching for Precision Parts
Manufacturing technology has evolved to produce precise and complex components that meet stringent requirements.
Wet etching, a process involving chemical solutions to remove material from a solid surface, has become a popular method in OEM (Original Equipment Manufacturer) production.
This technique is particularly beneficial for creating intricate designs in materials such as silicon, metal, and glass.
What is Wet Etching?
Wet etching involves immersing a material in a chemical solution that reacts with the surface to remove specific areas.
The etching solution, also known as the etchant, may vary depending on the material being etched.
For example, hydrofluoric acid (HF) is commonly used for etching silicon dioxide, while ferric chloride (FeCl3) is used for etching copper.
The process starts by coating the material with a protective layer called a resist.
This resist is patterned using photolithography techniques to create a mask that exposes certain areas for etching.
When the material is immersed in the etchant, only the exposed areas are affected, allowing for the controlled removal of material.
Advantages of OEM Wet Etching
OEM wet etching offers several advantages that make it suitable for precision part manufacturing:
High Precision
Wet etching can achieve high levels of precision, allowing for the creation of intricate designs and detailed features on a microscopic scale.
This is particularly beneficial for industries such as semiconductors, microelectronics, and MEMS (Micro-Electro-Mechanical Systems), where small and precise components are essential.
Cost-Effective
Compared to other fabrication methods, wet etching is relatively cost-effective.
The process requires less specialized equipment and can be performed at lower temperatures, reducing energy consumption and operational costs.
Additionally, the reusability of etchants further lowers production expenses.
Versatility
Wet etching is versatile and can be applied to a wide range of materials, including metals, semiconductors, and glass.
This flexibility allows OEM manufacturers to produce various components for different applications, from electronic circuits to optical devices.
Batch Processing
One of the significant advantages of wet etching is its ability to process multiple parts simultaneously.
Large batches of components can be etched in a single run, increasing production efficiency and output.
This is especially useful in high-volume manufacturing environments.
Applications of Wet Etching in OEM
Wet etching plays a crucial role in numerous industries, enabling the production of precision parts for various applications:
Semiconductor Manufacturing
In the semiconductor industry, wet etching is used to pattern silicon wafers, creating intricate circuits for microchips and integrated circuits (ICs).
The ability to etch features at the nanometer scale is essential for producing advanced semiconductor devices.
Microelectromechanical Systems (MEMS)
MEMS devices, such as sensors, actuators, and microstructures, rely on wet etching for precise fabrication.
The technique allows for the creation of complex 3D structures and fine features necessary for MEMS functionality.
Optical Devices
Wet etching is utilized in producing optical components, including lenses, waveguides, and photonic devices.
The process ensures high optical clarity and precise feature definition, crucial for optical performance.
Printed Circuit Boards (PCBs)
In PCB manufacturing, wet etching is employed to remove unwanted copper layers, creating the necessary circuit patterns.
The technique’s precision ensures reliable electrical connections and minimal signal interference in electronic devices.
Biomedical Devices
Wet etching is also applied in the production of biomedical devices, such as microfluidic chips and biosensors.
The ability to create intricate channels and structures enables the development of advanced diagnostic and therapeutic tools.
Challenges and Considerations
While wet etching offers numerous benefits, it also presents certain challenges that must be addressed to achieve optimal results:
Etch Rate Control
Achieving consistent etch rates is crucial for maintaining precision and uniformity across the material surface.
Factors such as etchant concentration, temperature, and agitation must be carefully controlled to ensure accurate results.
Etch Uniformity
Maintaining uniform etching across the entire surface can be challenging, especially for large or irregularly shaped components.
Proper agitation and etchant distribution techniques are essential to ensure even etching.
Material Compatibility
Different materials require specific etchants and conditions for effective etching.
Compatibility between the material and the etchant must be carefully considered to prevent unwanted reactions and damage.
Environmental and Safety Concerns
Some etchants used in wet etching processes are hazardous and require proper handling and disposal to ensure environmental and worker safety.
Strict adherence to safety protocols and regulations is necessary to mitigate risks.
Conclusion
OEM wet etching processing is a valuable technique for producing precision parts across various industries.
With its high precision, cost-effectiveness, and versatility, wet etching enables the fabrication of intricate components essential for modern technology.
By understanding the process, applications, and challenges associated with wet etching, manufacturers can leverage this technique to achieve superior quality and performance in their products.
As technology continues to advance, wet etching will remain a cornerstone of precision manufacturing, driving innovation and progress.
資料ダウンロード
QCD調達購買管理クラウド「newji」は、調達購買部門で必要なQCD管理全てを備えた、現場特化型兼クラウド型の今世紀最高の購買管理システムとなります。
ユーザー登録
調達購買業務の効率化だけでなく、システムを導入することで、コスト削減や製品・資材のステータス可視化のほか、属人化していた購買情報の共有化による内部不正防止や統制にも役立ちます。
NEWJI DX
製造業に特化したデジタルトランスフォーメーション(DX)の実現を目指す請負開発型のコンサルティングサービスです。AI、iPaaS、および先端の技術を駆使して、製造プロセスの効率化、業務効率化、チームワーク強化、コスト削減、品質向上を実現します。このサービスは、製造業の課題を深く理解し、それに対する最適なデジタルソリューションを提供することで、企業が持続的な成長とイノベーションを達成できるようサポートします。
オンライン講座
製造業、主に購買・調達部門にお勤めの方々に向けた情報を配信しております。
新任の方やベテランの方、管理職を対象とした幅広いコンテンツをご用意しております。
お問い合わせ
コストダウンが利益に直結する術だと理解していても、なかなか前に進めることができない状況。そんな時は、newjiのコストダウン自動化機能で大きく利益貢献しよう!
(Β版非公開)