- お役立ち記事
- Achieving Stable Production Line Operation through Equipment Maintenance and TPM Activities
月間76,176名の
製造業ご担当者様が閲覧しています*
*2025年3月31日現在のGoogle Analyticsのデータより
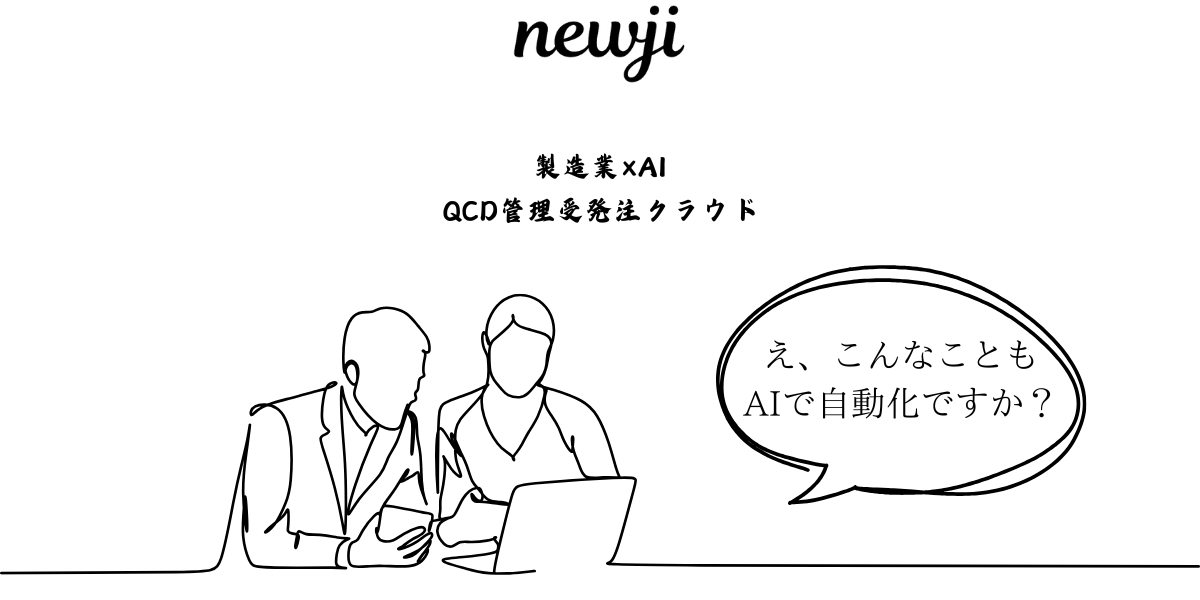
Achieving Stable Production Line Operation through Equipment Maintenance and TPM Activities
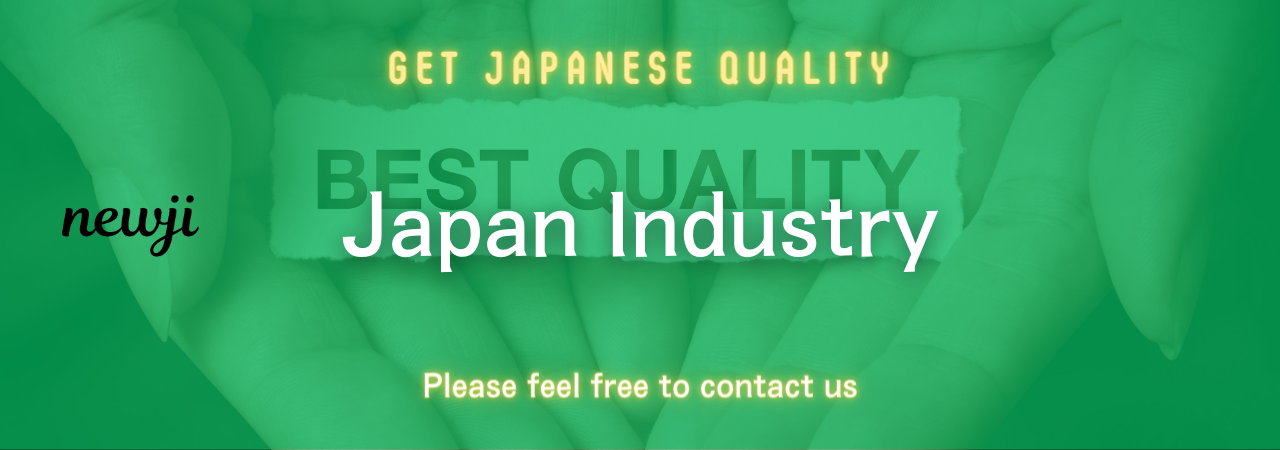
目次
Understanding Equipment Maintenance
Equipment maintenance is the practice of keeping machinery and industrial systems in optimal working condition.
It involves regular inspections, repairs, and updates to prevent any unforeseen breakdowns.
When a machine suddenly stops working, it can disrupt the entire production line, leading to costly delays and production losses.
Ensuring all equipment is well-maintained can avoid these issues, allowing for smoother operations.
Maintenance activities include cleaning, lubricating, checking for signs of wear and tear, replacing parts, and upgrading systems if necessary.
These tasks ensure that equipment is always running efficiently and effectively, ultimately saving both time and money in the long run.
The Role of TPM in Production
Total Productive Maintenance (TPM) is a proactive approach focused on improving the overall productivity of a production line.
By integrating maintenance strategies and procedures with everyday production activities, businesses can achieve superior results.
TPM emphasizes the shared responsibility of production and maintenance teams, promoting operational efficiency.
One critical aspect of TPM involves routine checks and early problem detection.
This helps to minimize disruptions due to unexpected equipment failures.
By establishing a schedule for routine maintenance, issues can be identified and resolved before they escalate into major problems.
The Pillars of TPM
TPM is structured around several key pillars, each contributing to more stable production line operations:
1. **Autonomous Maintenance**: Operators are trained to carry out basic maintenance tasks.
This empowers them to take an active role in the upkeep of machinery, leads to faster identification of potential problems, and reduces reliance on dedicated maintenance staff.
2. **Planned Maintenance**: Scheduling regular maintenance activities prevents equipment breakdowns.
By managing maintenance tasks ahead of time rather than waiting for issues to occur, downtime is minimized.
3. **Quality Maintenance**: Ensures that equipment functions at its best to produce high-quality goods.
Reducing defects and improving the quality of output leads to a more stable production line.
4. **Focused Improvement**: Teams come together to continually look for ways to improve machinery and operational processes.
This collaborative effort results in increased efficiency and productivity.
5. **Training and Development**: Employees receive the necessary training to perform maintenance tasks and operate equipment proficiently.
This skill development is vital to maintaining consistent production line operation.
Benefits of Effective Maintenance and TPM
Implementing robust equipment maintenance and TPM strategies can lead to numerous benefits for a production line:
– **Reduced Downtime**: Both strategies aim to minimize unexpected equipment failures, which significantly reduces production downtime.
Less downtime means more reliable operation and increased production output over time.
– **Cost Savings**: Regular maintenance prevents costly repairs and breakdowns.
It also minimizes production delays, thus saving both time and money.
– **Improved Safety**: Properly maintained equipment poses fewer risks to personnel, leading to a safer workplace and fewer accidents.
Employees who feel safe are more productive and engaged in their work.
– **Enhanced Product Quality**: When machines are operating efficiently, the quality of the products they produce improves.
This leads to higher customer satisfaction and repeat business.
– **Extended Equipment Life**: Consistent maintenance efforts prolong the life of machinery, allowing companies to get more out of their investments.
This reduces the need for frequent replacements.
Implementing TPM in Your Production Line
For companies looking to integrate TPM into their production processes, there are several steps to consider:
1. **Conduct an Initial Assessment**: Evaluate current maintenance practices and production processes to identify areas for improvement.
Understanding where inefficiencies lie is the first step to addressing them.
2. **Engage All Employees**: Successful TPM implementation requires participation from everyone, from upper management to line operators.
Engage employees by providing training and emphasizing their importance in achieving production goals.
3. **Establish Clear Goals**: Set specific and measurable objectives to guide the implementation process.
Whether it’s reducing downtime or increasing output, having clear goals will help track progress and ensure everyone is on the same page.
4. **Develop a Comprehensive Plan**: Create a detailed plan of action that outlines maintenance schedules, training programs, and improvement initiatives.
A well-structured plan provides a roadmap to achieving stable production line operations.
5. **Monitor and Adjust**: Continuously monitor the effects of TPM initiatives and make adjustments as necessary.
Regular reviews ensure that processes remain aligned with company objectives and that improvements are sustainable over the long term.
Conclusion
Effective equipment maintenance and the proactive methodologies of TPM are vital components in achieving stable production line operations.
By focusing on these areas, businesses can reduce downtime, lower costs, enhance safety, and improve product quality.
The integration of maintenance tasks into daily operations ensures that machinery runs smoothly, and empowers employees to contribute to the overall success of the production process.
Making TPM a core part of production strategy translates to long-term gains and sustainability for any manufacturing operation.
資料ダウンロード
QCD管理受発注クラウド「newji」は、受発注部門で必要なQCD管理全てを備えた、現場特化型兼クラウド型の今世紀最高の受発注管理システムとなります。
ユーザー登録
受発注業務の効率化だけでなく、システムを導入することで、コスト削減や製品・資材のステータス可視化のほか、属人化していた受発注情報の共有化による内部不正防止や統制にも役立ちます。
NEWJI DX
製造業に特化したデジタルトランスフォーメーション(DX)の実現を目指す請負開発型のコンサルティングサービスです。AI、iPaaS、および先端の技術を駆使して、製造プロセスの効率化、業務効率化、チームワーク強化、コスト削減、品質向上を実現します。このサービスは、製造業の課題を深く理解し、それに対する最適なデジタルソリューションを提供することで、企業が持続的な成長とイノベーションを達成できるようサポートします。
製造業ニュース解説
製造業、主に購買・調達部門にお勤めの方々に向けた情報を配信しております。
新任の方やベテランの方、管理職を対象とした幅広いコンテンツをご用意しております。
お問い合わせ
コストダウンが利益に直結する術だと理解していても、なかなか前に進めることができない状況。そんな時は、newjiのコストダウン自動化機能で大きく利益貢献しよう!
(β版非公開)