- お役立ち記事
- Adapting to the Times: Company-Wide Quality Management with Full Participation
Adapting to the Times: Company-Wide Quality Management with Full Participation
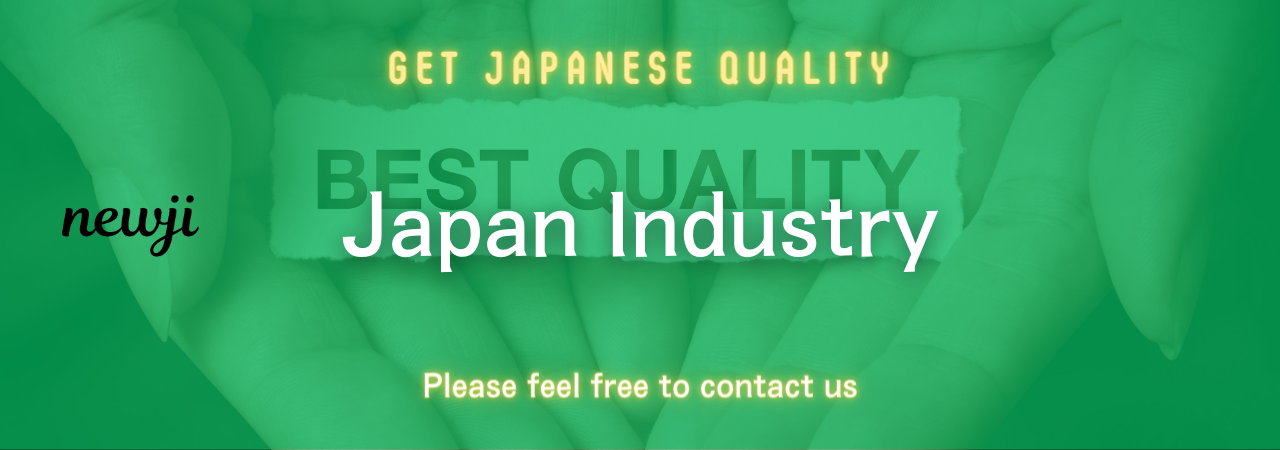
In today’s fast-paced business world, maintaining high-quality standards is paramount for any company aiming for long-term success.
One effective strategy to achieve this is through company-wide quality management with full participation.
By involving every employee in the quality management process, companies can ensure that they are meeting customer expectations, improving operational efficiencies, and fostering a culture of continuous improvement.
目次
The Importance of Quality Management
Quality management isn’t just about meeting the basic standards required for a product or service.
It’s about consistently exceeding expectations.
Quality management helps businesses to not only survive but thrive in an increasingly competitive market.
Companies can achieve higher customer satisfaction, improve operational efficiency, and build a strong reputation over time.
In the age of social media, where a single negative review can tarnish a company’s reputation, effective quality management is more crucial than ever.
Customer Satisfaction
When quality is the focus, customers notice.
Satisfied customers are more likely to return and recommend your services or products to others.
Word-of-mouth and positive reviews can significantly impact a business’s growth.
By ensuring your products or services meet high standards, you build customer trust and loyalty.
Operational Efficiency
Quality management processes can help identify inefficiencies and areas for improvement within a company.
Streamlining operations reduces waste and lowers costs.
Employees can focus on tasks that add value, rather than dealing with recurring issues or defects.
An efficient operation is not only more profitable but also more sustainable.
Reputation Building
A company known for its high-quality products and services naturally attracts more customers.
Brand reputation is a long-term asset that can differentiate a company in a crowded market.
Consistent quality helps build this reputation, ensuring that your company stands out.
Employee Involvement in Quality Management
For quality management to be effective, it requires the full participation of all employees.
Everyone in the organization, from top management to frontline workers, needs to be involved in the quality process.
This collective effort can transform a company’s culture, making quality a shared responsibility.
Training and Development
Employees need the right training and development to contribute effectively to quality management.
This includes understanding quality standards, learning how to use quality management tools, and knowing how to identify and report quality issues.
Regular training sessions can keep everyone updated on the latest practices and technologies in quality management.
Open Communication
For full employee participation, there must be open lines of communication within the organization.
Employees should feel comfortable reporting issues or suggesting improvements without fear of retribution.
A transparent communication culture helps in identifying problems early and finding effective solutions.
Empowerment and Accountability
Employees who feel empowered are more likely to take ownership of their work and its quality.
Empowering employees means giving them the authority to make decisions and take actions that improve quality.
Accountability ensures that everyone understands their role in maintaining quality standards.
Implementing Company-Wide Quality Management
Implementing company-wide quality management is not a one-time effort but an ongoing process.
Here are key steps to get started.
Setting Clear Objectives
The first step is to set clear, measurable objectives for quality management.
These objectives should align with the company’s overall goals and customer expectations.
Having clear objectives helps in tracking progress and making necessary adjustments.
Developing a Quality Management System (QMS)
A Quality Management System (QMS) is a formalized system that documents processes, procedures, and responsibilities for achieving quality objectives.
A well-designed QMS helps ensure that quality standards are consistently met and improved upon.
It serves as a roadmap for employees to follow.
Regular Audits and Reviews
Continuous assessment is vital to ensure that the quality management processes are effective.
Regular audits and reviews can help identify gaps and areas for improvement.
Feedback from these audits should be used to make necessary changes to the QMS.
Fostering a Quality Culture
Creating a culture that emphasizes quality is essential for the success of any quality management initiative.
Leaders should lead by example, demonstrating their commitment to quality in their actions and decisions.
Celebrating successes and recognizing employees’ contributions to quality can help reinforce this culture.
Tools and Techniques in Quality Management
Various tools and techniques can aid in effective quality management.
These tools help in monitoring, measuring, and improving quality throughout the organization.
Six Sigma
Six Sigma is a set of techniques and tools for process improvement.
It focuses on identifying and removing the causes of defects and minimizing variability in processes.
Six Sigma uses statistical methods to improve quality and efficiency.
Lean Management
Lean management aims to create more value for customers with fewer resources.
It focuses on reducing waste and improving processes.
Lean techniques help in creating efficient workflows and reducing costs, while still maintaining high quality.
Root Cause Analysis
Root Cause Analysis (RCA) helps in identifying the underlying causes of a problem.
By understanding the root cause, companies can implement effective solutions that prevent the problem from recurring.
RCA is essential for addressing quality issues at their source.
Quality Control Tools
Various quality control tools such as control charts, histograms, and Pareto charts can help monitor quality levels.
These tools provide visual representations of data, making it easier to identify trends and areas for improvement.
Overcoming Challenges in Quality Management
Implementing company-wide quality management with full participation comes with its challenges.
However, these challenges can be overcome with the right strategies.
Resistance to Change
Employees may resist changes to their usual ways of working.
Effective communication and training can help in overcoming this resistance.
It’s important to explain the benefits of quality management and how it contributes to the company’s success.
Resource Constraints
Implementing quality management processes requires time and resources.
Companies need to invest in training, tools, and systems.
Prioritizing quality and allocating adequate resources is essential for long-term success.
Sustaining Momentum
Maintaining the momentum of quality initiatives can be challenging.
Regular reviews, audits, and employee engagement activities can help keep the focus on quality.
Celebrating small wins and recognizing efforts can also boost morale and sustain momentum.
In conclusion, company-wide quality management with full participation is essential for businesses to adapt to the times.
By involving every employee in the quality process, companies can improve customer satisfaction, enhance operational efficiency, and build a strong reputation.
Implementing a robust quality management system, using effective tools, and overcoming challenges are crucial steps in this journey.
Ultimately, a commitment to quality can set a company apart in a competitive market, leading to long-term success.
資料ダウンロード
QCD調達購買管理クラウド「newji」は、調達購買部門で必要なQCD管理全てを備えた、現場特化型兼クラウド型の今世紀最高の購買管理システムとなります。
ユーザー登録
調達購買業務の効率化だけでなく、システムを導入することで、コスト削減や製品・資材のステータス可視化のほか、属人化していた購買情報の共有化による内部不正防止や統制にも役立ちます。
NEWJI DX
製造業に特化したデジタルトランスフォーメーション(DX)の実現を目指す請負開発型のコンサルティングサービスです。AI、iPaaS、および先端の技術を駆使して、製造プロセスの効率化、業務効率化、チームワーク強化、コスト削減、品質向上を実現します。このサービスは、製造業の課題を深く理解し、それに対する最適なデジタルソリューションを提供することで、企業が持続的な成長とイノベーションを達成できるようサポートします。
オンライン講座
製造業、主に購買・調達部門にお勤めの方々に向けた情報を配信しております。
新任の方やベテランの方、管理職を対象とした幅広いコンテンツをご用意しております。
お問い合わせ
コストダウンが利益に直結する術だと理解していても、なかなか前に進めることができない状況。そんな時は、newjiのコストダウン自動化機能で大きく利益貢献しよう!
(Β版非公開)