- お役立ち記事
- Adhesive joint design and analysis
月間77,185名の
製造業ご担当者様が閲覧しています*
*2025年2月28日現在のGoogle Analyticsのデータより
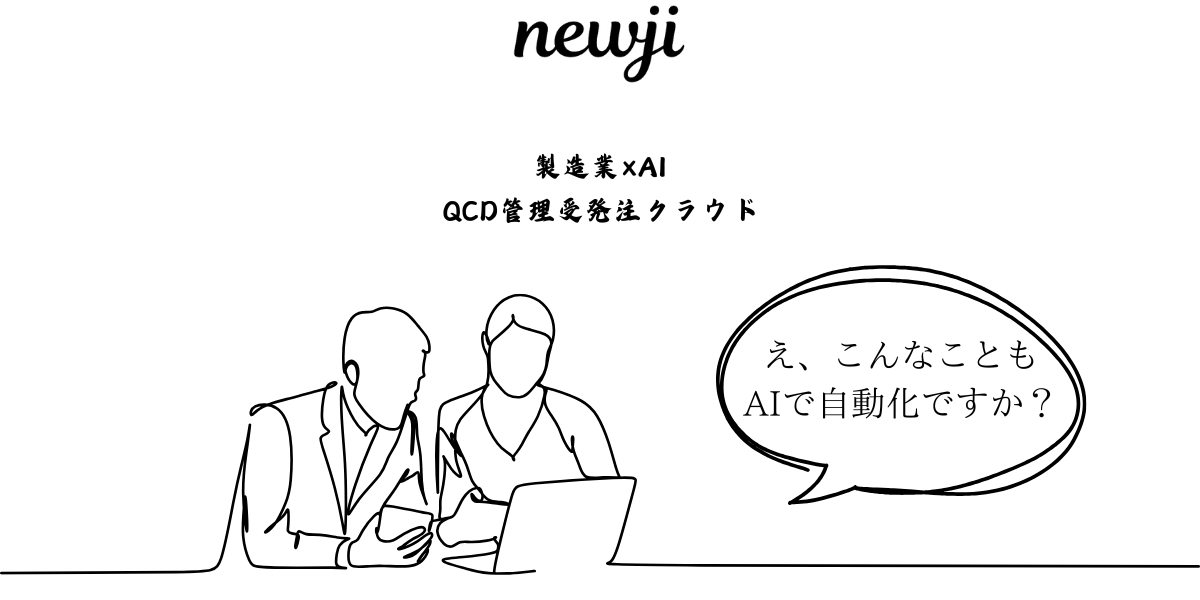
Adhesive joint design and analysis
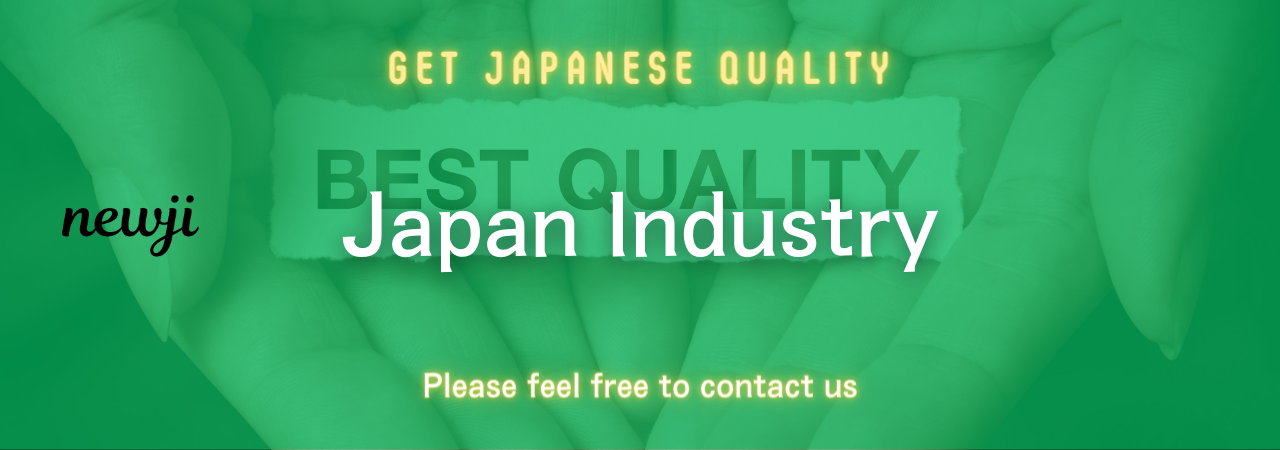
目次
Understanding Adhesive Joints
Adhesive joints play a vital role in modern manufacturing and construction industries.
They are used to bond materials together, offering flexibility, durability, and generally low production costs.
An adhesive joint is technically a form of bonding technology that involves joining two or more materials using a polymeric substance.
The importance of a well-designed adhesive joint cannot be overstated.
It ensures the structural integrity and long-term performance of the products involved.
From automotive and aerospace industries to simple everyday products, adhesive joints are indispensable.
Advantages of Adhesive Joints
One of the primary advantages of using adhesives is their ability to join dissimilar materials.
Adhesives can bond metals to plastics, ceramics to glass, and other combinations that would be challenging using traditional methods such as welding or bolting.
Adhesive joints also provide excellent stress distribution.
Unlike mechanical fasteners that create point stresses where they are applied, adhesives distribute the load evenly along the joint surface.
This capability reduces the risk of material failure.
Furthermore, adhesives contribute to weight reduction.
In industries like aerospace and automotive, reducing weight can lead to substantial fuel savings and increased efficiency.
Adhesives also offer aesthetic benefits by eliminating visible fasteners, resulting in a cleaner appearance.
Types of Adhesives Used in Joints
Different applications require different types of adhesives.
Some major categories include epoxies, acrylics, polyurethanes, and silicones.
Epoxy Adhesives
Epoxy adhesives are renowned for their high strength and durability.
They are often used in structural applications where a strong joint is crucial.
Epoxies can bond a wide range of materials, including metals, plastics, and ceramics.
Acrylic Adhesives
Acrylic adhesives cure rapidly and offer a strong bond, making them ideal for high-speed manufacturing processes.
These adhesives are often used in automotive and electronics industries.
Polyurethane Adhesives
Polyurethanes offer flexibility and are excellent for bonding materials prone to expansion and contraction.
They exhibit good impact resistance and are suitable for applications where vibration and movement are common.
Silicone Adhesives
Silicone adhesives are known for their temperature resistance and elasticity.
They are often used in electronics and automotive applications where heat exposure is a concern.
Designing an Effective Adhesive Joint
Successful adhesive joint design involves several critical factors that must be considered.
Surface Preparation
Proper surface preparation is crucial for ensuring a strong bond.
The surfaces to be bonded must be clean, dry, and free of contaminants such as oils, dust, or moisture.
This can involve processes like sanding, solvents, or priming.
Joint Configuration
The geometry of the adhesive joint plays a significant role in its performance.
Common configurations include lap joints, butt joints, and scarf joints.
Lap joints, where two surfaces overlap, are favorable due to increased surface area and stress distribution.
Material Compatibility
It is vital to consider the compatibility of the materials involved in the joint.
This includes their thermal expansion coefficients, surface energies, and potential chemical interactions with the adhesive.
The chosen adhesive should work well with the specific materials being joined.
Environmental Considerations
Adhesive joints can be affected by environmental factors such as temperature, humidity, and exposure to chemicals.
Designers must choose adhesives that can withstand the service environment without degrading.
Analyzing Adhesive Joints
Evaluating the performance of adhesive joints involves both physical testing and computational methods.
Experimental Testing
Physical testing of adhesive joints may include tensile, shear, and peel tests.
These tests measure the joint’s ability to withstand various loading conditions.
Destructive testing helps in understanding the joint’s failure modes.
Finite Element Analysis (FEA)
Finite Element Analysis is a computational tool used to simulate how an adhesive joint will react under different conditions.
FEA helps designers visualize stress distribution and identify potential failure points in the joint.
This analysis enables optimizations before physical prototypes are made.
Nondestructive Testing (NDT)
Nondestructive testing methods, such as ultrasound or infrared thermography, offer insight into the internal condition of adhesive joints without damaging them.
These methods are useful for quality control and ensuring long-term reliability.
Case Studies and Applications
The use of adhesive joints spans numerous industries, each benefiting from the specific advantages adhesives offer.
Automotive Industry
In the automotive industry, adhesive joints contribute to vehicle light-weighting, noise reduction, and improved crash performance.
Adhesives are used to bond components such as glass, plastics, and metal panels.
Aerospace Sector
The aerospace industry relies on adhesives for bonding lightweight composite materials.
Adhesive joints contribute to the integration of complex structures while maintaining structural integrity.
Electronics
Adhesive joints in electronics provide insulation, thermal management, and vibration damping.
They are critical in assembling circuit boards and encapsulating electronic components.
Future Trends in Adhesive Joint Design
The future of adhesive joint design is shaped by the development of smarter adhesives.
These innovative materials are being engineered with self-healing properties, allowing joints to repair minor damage autonomously.
Furthermore, advancements in nanotechnology enhance adhesive formulations, leading to stronger and more durable joints.
The integration of sensors into adhesive joints to monitor real-time performance is an emerging trend.
As industries continue to demand tailored solutions with higher performance, adhesive technology will remain an area of active research and development.
The journey towards improved design, testing, and analysis of adhesive joints will undoubtedly lead to more innovative and sustainable solutions.
資料ダウンロード
QCD管理受発注クラウド「newji」は、受発注部門で必要なQCD管理全てを備えた、現場特化型兼クラウド型の今世紀最高の受発注管理システムとなります。
ユーザー登録
受発注業務の効率化だけでなく、システムを導入することで、コスト削減や製品・資材のステータス可視化のほか、属人化していた受発注情報の共有化による内部不正防止や統制にも役立ちます。
NEWJI DX
製造業に特化したデジタルトランスフォーメーション(DX)の実現を目指す請負開発型のコンサルティングサービスです。AI、iPaaS、および先端の技術を駆使して、製造プロセスの効率化、業務効率化、チームワーク強化、コスト削減、品質向上を実現します。このサービスは、製造業の課題を深く理解し、それに対する最適なデジタルソリューションを提供することで、企業が持続的な成長とイノベーションを達成できるようサポートします。
製造業ニュース解説
製造業、主に購買・調達部門にお勤めの方々に向けた情報を配信しております。
新任の方やベテランの方、管理職を対象とした幅広いコンテンツをご用意しております。
お問い合わせ
コストダウンが利益に直結する術だと理解していても、なかなか前に進めることができない状況。そんな時は、newjiのコストダウン自動化機能で大きく利益貢献しよう!
(β版非公開)