- お役立ち記事
- Advancing Kaizen Activities in Manufacturing Quality Management: Approaches and Success Stories
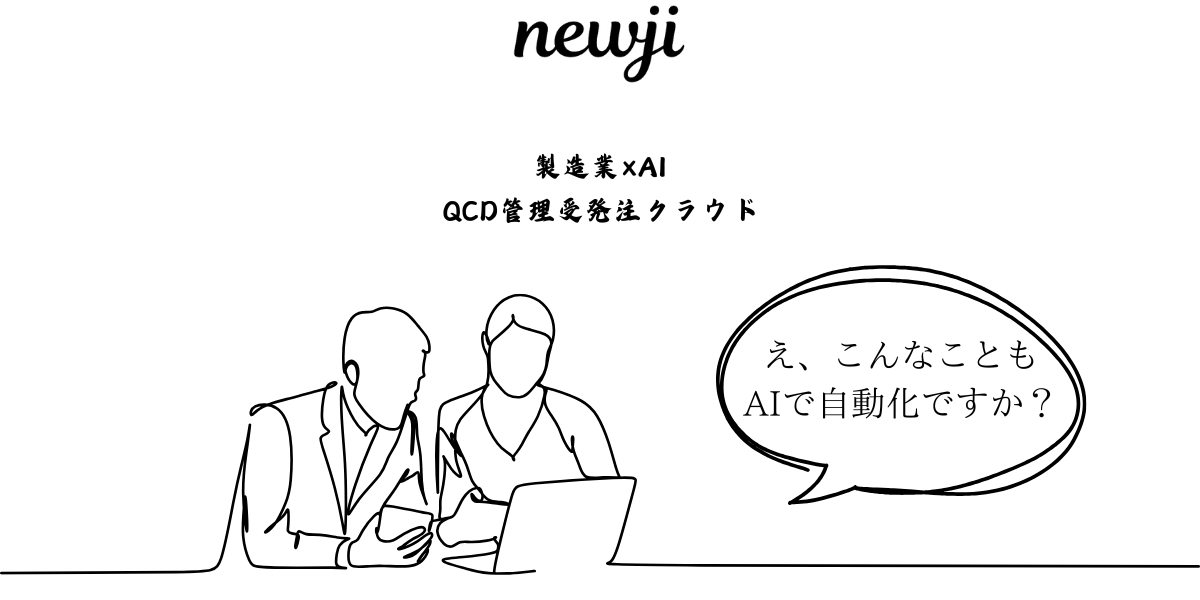
Advancing Kaizen Activities in Manufacturing Quality Management: Approaches and Success Stories
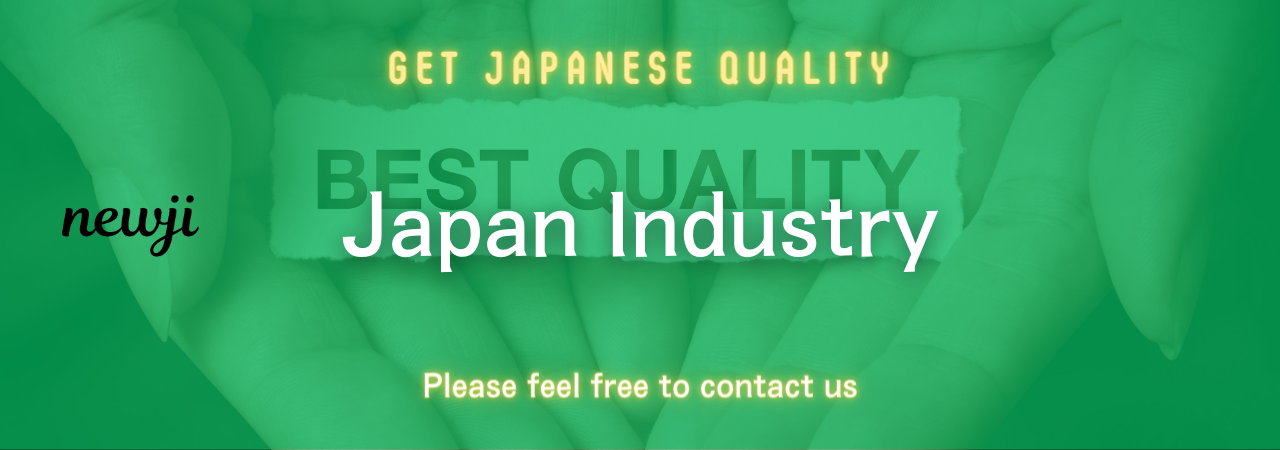
In the competitive world of manufacturing, consistent improvement is crucial.
This is where Kaizen, a Japanese term meaning “continuous improvement,” comes into play.
Adopting Kaizen activities in quality management offers numerous benefits, from enhanced efficiency to increased employee engagement.
In this article, we’ll explore the various approaches to advancing Kaizen activities and share some success stories to illustrate its impact.
目次
Understanding Kaizen in Manufacturing
Kaizen is a philosophy that focuses on small, incremental changes rather than large-scale transformations.
Originating in Japan, this approach prioritizes a culture of continuous improvement involving everyone from top management to frontline workers.
It encourages identifying inefficiencies and making step-by-step improvements.
In essence, Kaizen aims to enhance processes, and quality, and ultimately, customer satisfaction.
Core Principles of Kaizen
To implement Kaizen effectively, understanding its core principles is essential.
1. Focus on Process
Successful Kaizen activities prioritize the process rather than just the end results.
By focusing on how work is done, rather than purely on outcomes, companies can identify inefficiencies and areas for improvement.
2. Involve Everyone
One of the strengths of Kaizen lies in its inclusive nature.
From executives to workers on the shop floor, involving everyone encourages a shared responsibility for improvement.
3. Use Data and Facts
Decisions in Kaizen activities are driven by data and facts, ensuring that changes are evidence-based and more likely to yield desired results.
Approaches to Advancing Kaizen
Several effective approaches can help in advancing Kaizen activities in manufacturing quality management.
1. Establish a Kaizen Team
Forming a dedicated team to lead Kaizen activities can be extremely beneficial.
This team is responsible for training employees, leading improvement projects, and ensuring that the Kaizen philosophy is consistently applied.
2. Regular Training and Workshops
Training is a cornerstone of successful Kaizen implementation.
Regular workshops and training sessions help employees understand Kaizen principles and how to apply them in their daily tasks.
3. Implementing Small Changes
Rather than attempting large-scale changes, focus on small, manageable improvements.
Over time, these incremental changes can accumulate and lead to significant enhancements.
4. Continuous Feedback
Collecting and analyzing feedback from employees ensures that the implemented changes are effective.
Continuous feedback loops help in refining processes and sustaining improvements.
Kaizen Tools and Techniques
Several tools and techniques can aid in Kaizen activities, making the process more efficient and effective.
1. 5S Methodology
The 5S methodology (Sort, Set in order, Shine, Standardize, and Sustain) is among the most popular Kaizen tools.
It focuses on workplace organization and cleanliness, which can significantly improve efficiency and safety.
2. Value Stream Mapping
Value Stream Mapping (VSM) helps in identifying and eliminating waste in processes.
By visualizing the flow of materials and information, companies can pinpoint inefficiencies and areas for improvement.
3. Root Cause Analysis
Root Cause Analysis (RCA) techniques, like the “Five Whys,” help in identifying the underlying causes of problems.
Addressing these root causes is essential for sustainable improvements.
Success Stories in Kaizen
The true test of Kaizen lies in its practical application and results.
Let’s look at some success stories that highlight the power of Kaizen in manufacturing quality management.
Case Study 1: Toyota
Toyota is perhaps the most well-known example of successful Kaizen implementation.
By adopting Kaizen, Toyota has maintained high quality and efficiency standards.
The company’s commitment to continuous improvement has helped it remain a leader in the automotive industry.
Case Study 2: Bosch
Bosch, a multinational engineering and technology company, has also reaped the benefits of Kaizen.
By focusing on employee involvement and continuous improvement, Bosch has achieved impressive advancements in manufacturing efficiency and product quality.
Case Study 3: Nike
In an effort to enhance production efficiency and quality, Nike implemented Kaizen activities across its manufacturing plants.
The result has been a noticeable reduction in waste and improved product consistency, contributing to higher customer satisfaction.
Conclusion
Advancing Kaizen activities in manufacturing quality management is a surefire way to achieve continuous improvement.
By focusing on core principles, involving everyone, using data, and implementing effective tools, companies can see significant benefits.
The success stories of industry giants like Toyota, Bosch, and Nike underscore the transformative power of Kaizen.
By embracing this philosophy, manufacturing companies can look forward to enhanced efficiency, better product quality, and higher customer satisfaction.
資料ダウンロード
QCD調達購買管理クラウド「newji」は、調達購買部門で必要なQCD管理全てを備えた、現場特化型兼クラウド型の今世紀最高の購買管理システムとなります。
ユーザー登録
調達購買業務の効率化だけでなく、システムを導入することで、コスト削減や製品・資材のステータス可視化のほか、属人化していた購買情報の共有化による内部不正防止や統制にも役立ちます。
NEWJI DX
製造業に特化したデジタルトランスフォーメーション(DX)の実現を目指す請負開発型のコンサルティングサービスです。AI、iPaaS、および先端の技術を駆使して、製造プロセスの効率化、業務効率化、チームワーク強化、コスト削減、品質向上を実現します。このサービスは、製造業の課題を深く理解し、それに対する最適なデジタルソリューションを提供することで、企業が持続的な成長とイノベーションを達成できるようサポートします。
オンライン講座
製造業、主に購買・調達部門にお勤めの方々に向けた情報を配信しております。
新任の方やベテランの方、管理職を対象とした幅広いコンテンツをご用意しております。
お問い合わせ
コストダウンが利益に直結する術だと理解していても、なかなか前に進めることができない状況。そんな時は、newjiのコストダウン自動化機能で大きく利益貢献しよう!
(Β版非公開)