- お役立ち記事
- Advantages of Multi-Axis Control Using 5-Axis Machining in Production Equipment
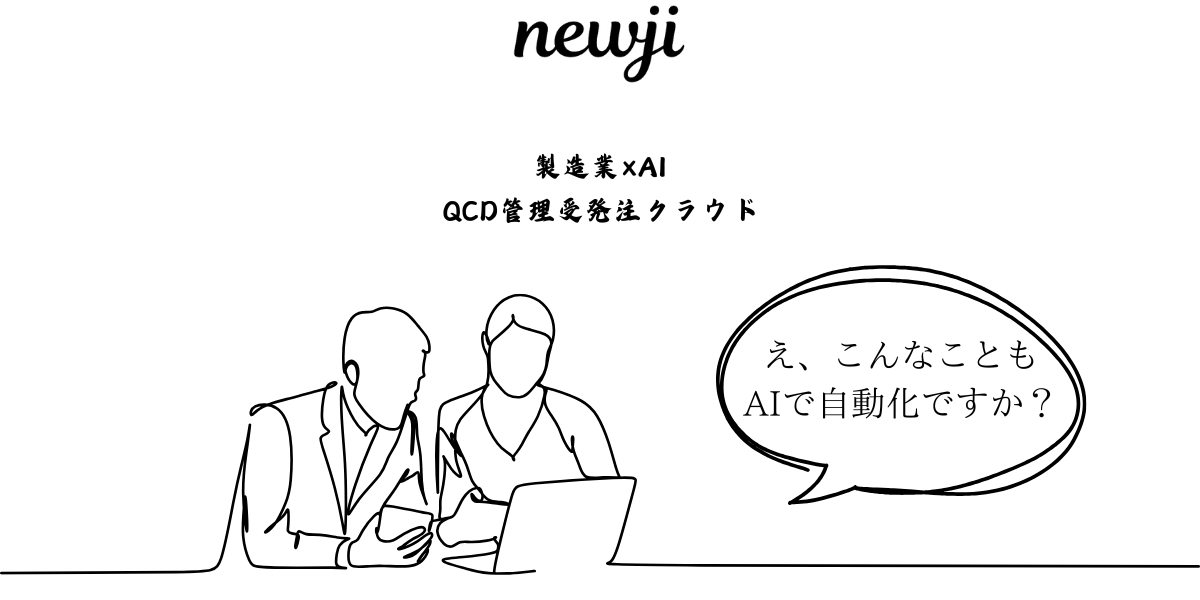
Advantages of Multi-Axis Control Using 5-Axis Machining in Production Equipment
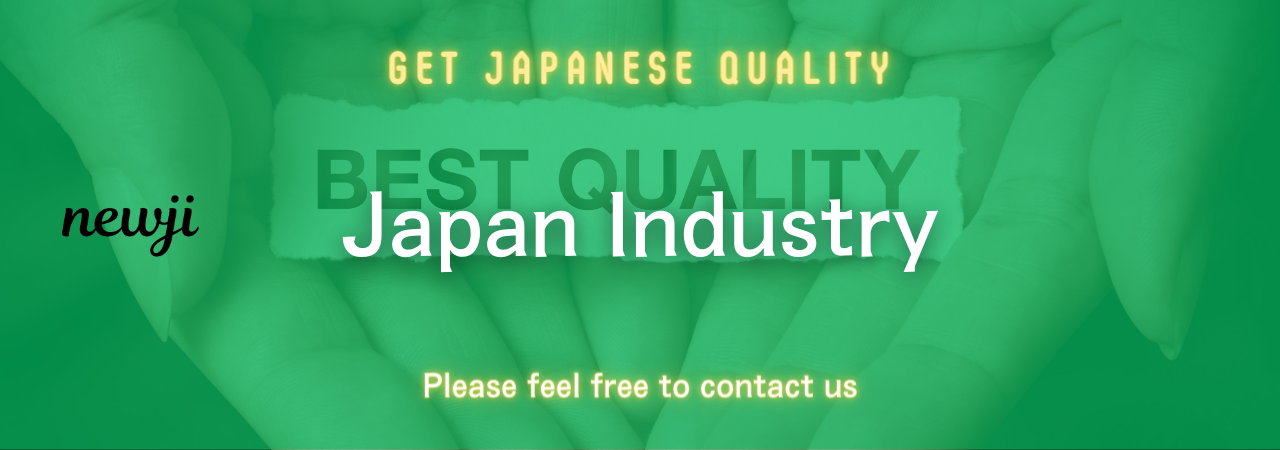
目次
Understanding 5-Axis Machining
5-axis machining is a technological advancement in the field of manufacturing that allows complex shapes to be produced with a higher degree of accuracy and efficiency.
Unlike the traditional 3-axis machining, which operates on three linear axes of motion (X, Y, and Z), the 5-axis machining adds two additional rotational axes.
These additional axes enable the machining tool to approach a part from various angles.
This results in reduced setup time and the need for multiple fixtures.
When it comes to multi-axis control, the benefits are numerous, and understanding these can significantly enhance production capabilities and output quality.
Enhancing Production Efficiency
One of the primary advantages of implementing 5-axis machining in production equipment is its ability to enhance efficiency.
By reducing the number of setups needed to achieve complex geometries, production time is cut down substantially.
In conventional 3-axis machining, a part often requires multiple setups and repositioning, each adding to the total machining time.
With 5-axis machining, the ability to machine complex features in a single setup means that manufacturers can improve throughput and minimize idle time.
The reduction in setup time not only improves efficiency but also enhances the overall workflow of the production process.
Improved Surface Finishes
Another significant advantage of 5-axis machining is the superior surface finish it can offer.
Since the machine can approach the part from different angles, the tool can maintain a constant cutting path that results in smoother surfaces.
With traditional machining, the inability to change angles easily often leads to stepped or scalloped finishes, which require additional finishing processes.
By allowing for continuous machining along complex contours and surfaces, 5-axis machining minimizes these issues, resulting in a better finish straight off the machine.
This improvement in surface finish can be a critical factor in industries where aesthetics and precision are vital, such as aerospace and automotive sectors.
Reducing Tool Wear
In 5-axis machining, tools can maintain the necessary angles and speeds for optimal cutting, reducing the strain on the tool itself.
As a result, tool wear is minimized, which not only extends the life of the cutting tools but also ensures consistent quality over the production run.
This reduction in tool wear contributes to lower production costs since the need for frequent tool changes is decreased and overall tooling expenses are reduced.
Complex Geometries and Procedures
5-axis machining allows for the creation of extremely complex geometries that would be impossible or incredibly time-consuming with other manufacturing techniques.
The ability to rotate both the part and the tool provides immense flexibility, enabling the production of intricate designs and unique structures.
This capability is particularly beneficial in industries such as aerospace, medical devices, and automotive, where components often feature intricate geometries that need precise manufacturing.
By enabling more complex and sophisticated designs, 5-axis machining opens up new possibilities for innovation and functionality in product development.
Cost-Effectiveness in Long Runs
Although the initial investment in 5-axis machining equipment can be substantial, the cost-effectiveness becomes evident over long production runs.
The ability to efficiently handle complex parts in a single setup reduces labor costs, tooling expenses, and time.
Moreover, the precision of 5-axis machines reduces the requirement for additional quality control checks and significantly lowers the risk of part rejection due to errors.
Over time, these savings accumulate, providing a substantial return on investment.
This long-term cost-effectiveness makes 5-axis machining an appealing choice for manufacturers considering high-volume production or dealing with high-value materials where waste must be minimized.
Boosting Flexibility and Versatility
Versatility is a hallmark of 5-axis machining, as it allows manufacturers to adapt to a variety of projects and materials.
The versatility of multi-axis control eliminates the need for multiple machines, reducing factory floor space and maintenance costs.
5-axis machines can be programmed to handle different parts with varying complexities, which is advantageous for production lines that require quick changeovers.
With the increasing demand for customized products, the flexibility offered by 5-axis machining enables manufacturers to quickly adapt their processes to meet the changing needs of customers.
Improved Accuracy and Consistency
The precision of 5-axis machines ensures that parts are produced with consistent accuracy, which is critical in industries where tolerances are tight.
With multi-axis control, there’s less risk of cumulative error through multiple setups, ensuring parts remain within tolerance throughout production.
This precision and repeatability translate into improved product quality and customer satisfaction.
Moreover, enhanced accuracy ensures that parts fit together correctly, reducing assembly time and potential rework costs.
Future of Manufacturing with 5-Axis Machining
The technological advances in 5-axis machining signify a shift towards more sophisticated manufacturing processes.
As industries continue to demand higher precision and efficiency, the role of 5-axis machining in production equipment will only continue to grow.
The development of even more advanced software and hardware solutions will likely make these machines more user-friendly and economically feasible for a broader range of manufacturers.
Embracing 5-axis machining today equips manufacturers not only to meet current demands but also to be poised for future challenges and innovations in the manufacturing landscape.
In conclusion, multi-axis control using 5-axis machining provides a myriad of advantages from enhancing efficiency and surface finish to improving flexibility and accuracy.
For manufacturers looking to remain competitive, adopting this technology can be a vital step forward in achieving production excellence.
資料ダウンロード
QCD調達購買管理クラウド「newji」は、調達購買部門で必要なQCD管理全てを備えた、現場特化型兼クラウド型の今世紀最高の購買管理システムとなります。
ユーザー登録
調達購買業務の効率化だけでなく、システムを導入することで、コスト削減や製品・資材のステータス可視化のほか、属人化していた購買情報の共有化による内部不正防止や統制にも役立ちます。
NEWJI DX
製造業に特化したデジタルトランスフォーメーション(DX)の実現を目指す請負開発型のコンサルティングサービスです。AI、iPaaS、および先端の技術を駆使して、製造プロセスの効率化、業務効率化、チームワーク強化、コスト削減、品質向上を実現します。このサービスは、製造業の課題を深く理解し、それに対する最適なデジタルソリューションを提供することで、企業が持続的な成長とイノベーションを達成できるようサポートします。
オンライン講座
製造業、主に購買・調達部門にお勤めの方々に向けた情報を配信しております。
新任の方やベテランの方、管理職を対象とした幅広いコンテンツをご用意しております。
お問い合わせ
コストダウンが利益に直結する術だと理解していても、なかなか前に進めることができない状況。そんな時は、newjiのコストダウン自動化機能で大きく利益貢献しよう!
(Β版非公開)