- お役立ち記事
- Advantages of multi-tier procurement system in manufacturing industry adopted by purchasing department
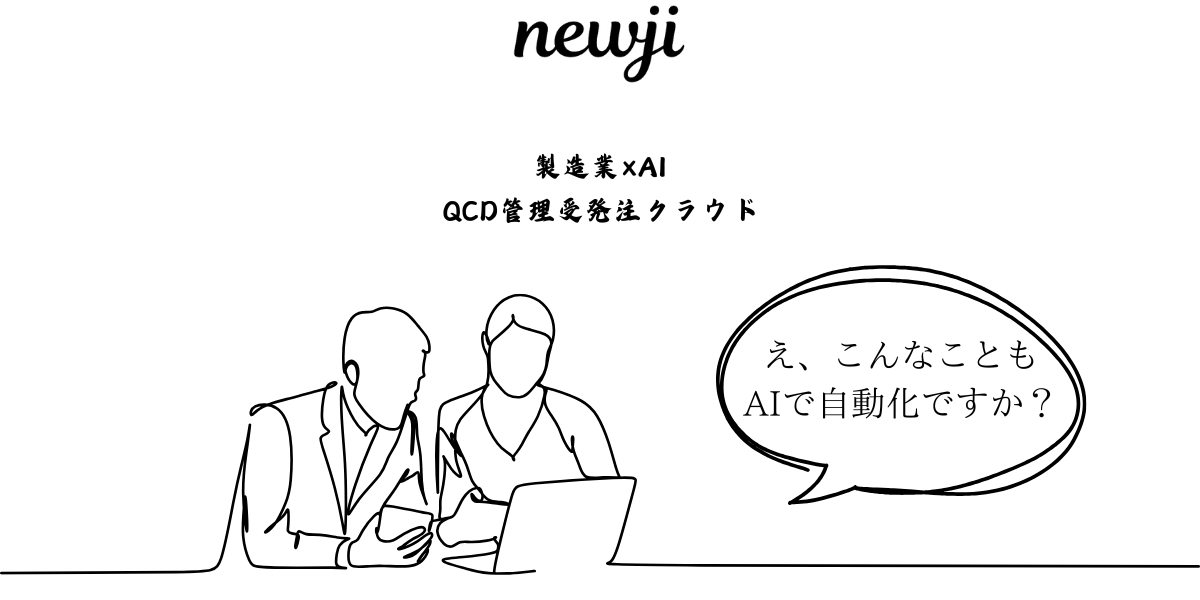
Advantages of multi-tier procurement system in manufacturing industry adopted by purchasing department
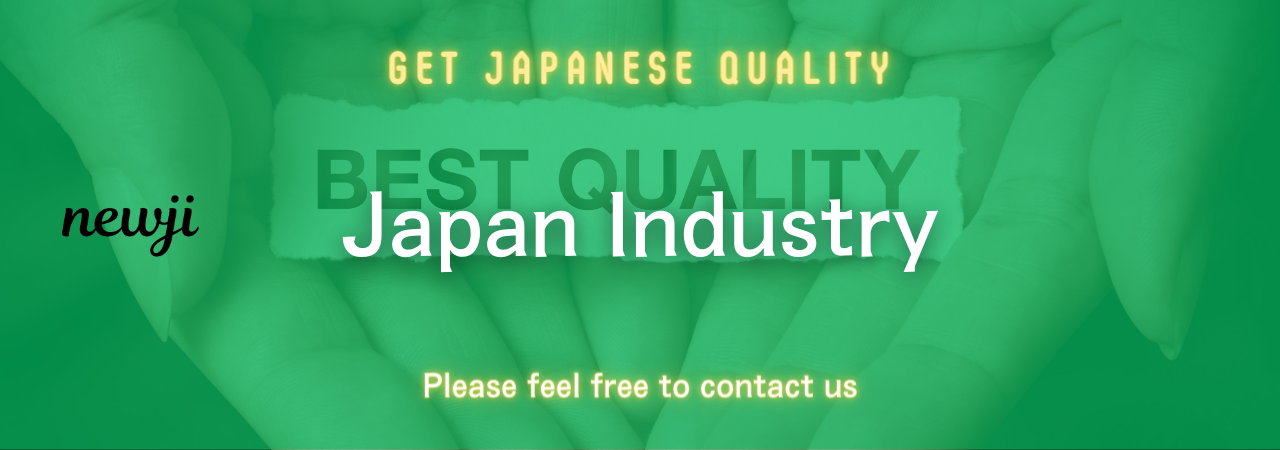
目次
Understanding Multi-Tier Procurement
The concept of a multi-tier procurement system is gaining traction in the manufacturing industry.
It involves the strategic management of suppliers at different levels to optimize purchasing processes.
This approach addresses challenges linked with a single-tier procurement system, whereby a company depends too heavily on direct suppliers.
In a multi-tier procurement system, companies manage and collaborate with both direct suppliers and their suppliers, hence creating a more comprehensive supply chain strategy.
This enhances flexibility and efficiency, providing manufacturers with numerous competitive advantages.
Increased Supply Chain Resilience
One significant advantage of a multi-tier procurement system is its ability to improve supply chain resilience.
By engaging with suppliers at multiple levels, companies can anticipate potential disruptions and address vulnerabilities before they escalate.
This proactive approach means the purchasing department can better manage risk by diversifying the supplier base and ensuring there’s always an alternative source available in case of unexpected events.
Resilience in supply chains is more important than ever given the global exposure to natural disasters, political instability, and economic fluctuations.
Having multiple tiers in procurement ensures manufacturers are less affected by these unforeseen disruptions, thereby avoiding costly downtimes and delays.
Enhanced Transparency and Communication
Multi-tier procurement also fosters better transparency and communication across the supply chain.
This structure provides manufacturers with deeper insights into the production processes at various levels, leading to enhanced oversight and control.
When dealing with suppliers beyond the immediate level, manufacturers gain valuable information about upstream supply chain processes.
This transparency helps identify and mitigate inefficiencies, leading to optimized manufacturing operations.
Furthermore, improved communication with second and third-tier suppliers can lead to innovations and efficiencies that might not have been possible when limiting interactions to first-tier suppliers alone.
Cost Efficiency and Competitive Pricing
Another significant advantage is the potential for cost savings.
With a clearer view of the entire supply chain, manufacturers can identify cost drivers and inefficiencies, allowing them to negotiate better prices and terms at various levels.
This ability to interact and negotiate further up the supply chain can lead to more competitive pricing, better payment terms, and reduced procurement costs overall.
Moreover, the increased competition among suppliers at different levels can lead to better pricing and service offerings, as suppliers are more motivated to provide greater value to remain a part of the supply network.
Innovation and Collaboration Opportunities
The collaborative nature of a multi-tier procurement system encourages innovation.
By working closely with suppliers throughout the tiers, manufacturing companies can foster partnerships that lead to co-development of new products or enhancements to existing ones.
These partnerships leverage the unique strengths and expertise of each supplier, accelerating innovation cycles and bringing advanced products to market more swiftly.
Collaboration at multiple levels of the supply chain can also lead to streamlined processes and adoption of best practices, thereby improving product quality and reducing time to market.
Improved Quality Assurance
Quality control is crucial in the manufacturing industry, and a multi-tier procurement system provides additional checks and balances.
With oversight extending to multiple levels of suppliers, manufacturers can ensure that quality standards are met consistently across the entire supply chain.
This approach minimizes the risk of substandard materials and components entering the production process, enhancing the overall quality of the final product.
By addressing quality issues at various stages, companies enhance their reputation, reduce the risk of recalls, and ultimately increase customer satisfaction.
Strategic Supplier Relationships
Building robust supplier relationships is a cornerstone of the multi-tier procurement strategy.
It goes beyond transactional interactions and focuses on strategic partnerships that create value for all parties involved.
Fostering long-term relationships with suppliers across tiers allows for better alignment of goals and objectives.
It encourages collaborative problem-solving and the sharing of information, leading to better decision-making.
Such relationships can be a source of competitive advantage, as they enhance reliability and flexibility, enabling companies to respond more effectively to market demands and changes.
Challenges and Considerations
While the advantages of a multi-tier procurement system are significant, there are challenges to consider.
Managing a complex network of suppliers requires advanced systems and expertise to ensure effective coordination.
It demands robust communication and data-sharing capabilities to maintain transparency and collaboration across different levels.
Moreover, establishing and nurturing relationships throughout the supply chain can be resource-intensive.
This approach requires strategic planning and a commitment to partner development to realize its full potential.
Companies must also be vigilant about data security and intellectual property protection, as interactions with multiple suppliers can increase exposure to risks.
Conclusion
The advantages of a multi-tier procurement system in the manufacturing industry are manifold.
It provides a robust framework for enhancing resilience, transparency, and cost efficiency, while fostering innovation and improving quality assurance.
When implemented effectively, it leads to stronger supplier relationships and a more competitive market position.
However, to fully benefit from this system, companies must be prepared to tackle the challenges and commit to building strategic partnerships throughout their supply chain.
By doing so, they can unlock significant value and gain a competitive edge in the market.
資料ダウンロード
QCD調達購買管理クラウド「newji」は、調達購買部門で必要なQCD管理全てを備えた、現場特化型兼クラウド型の今世紀最高の購買管理システムとなります。
ユーザー登録
調達購買業務の効率化だけでなく、システムを導入することで、コスト削減や製品・資材のステータス可視化のほか、属人化していた購買情報の共有化による内部不正防止や統制にも役立ちます。
NEWJI DX
製造業に特化したデジタルトランスフォーメーション(DX)の実現を目指す請負開発型のコンサルティングサービスです。AI、iPaaS、および先端の技術を駆使して、製造プロセスの効率化、業務効率化、チームワーク強化、コスト削減、品質向上を実現します。このサービスは、製造業の課題を深く理解し、それに対する最適なデジタルソリューションを提供することで、企業が持続的な成長とイノベーションを達成できるようサポートします。
オンライン講座
製造業、主に購買・調達部門にお勤めの方々に向けた情報を配信しております。
新任の方やベテランの方、管理職を対象とした幅広いコンテンツをご用意しております。
お問い合わせ
コストダウンが利益に直結する術だと理解していても、なかなか前に進めることができない状況。そんな時は、newjiのコストダウン自動化機能で大きく利益貢献しよう!
(Β版非公開)