- お役立ち記事
- Aerospace prototype manufacturing
月間77,185名の
製造業ご担当者様が閲覧しています*
*2025年2月28日現在のGoogle Analyticsのデータより
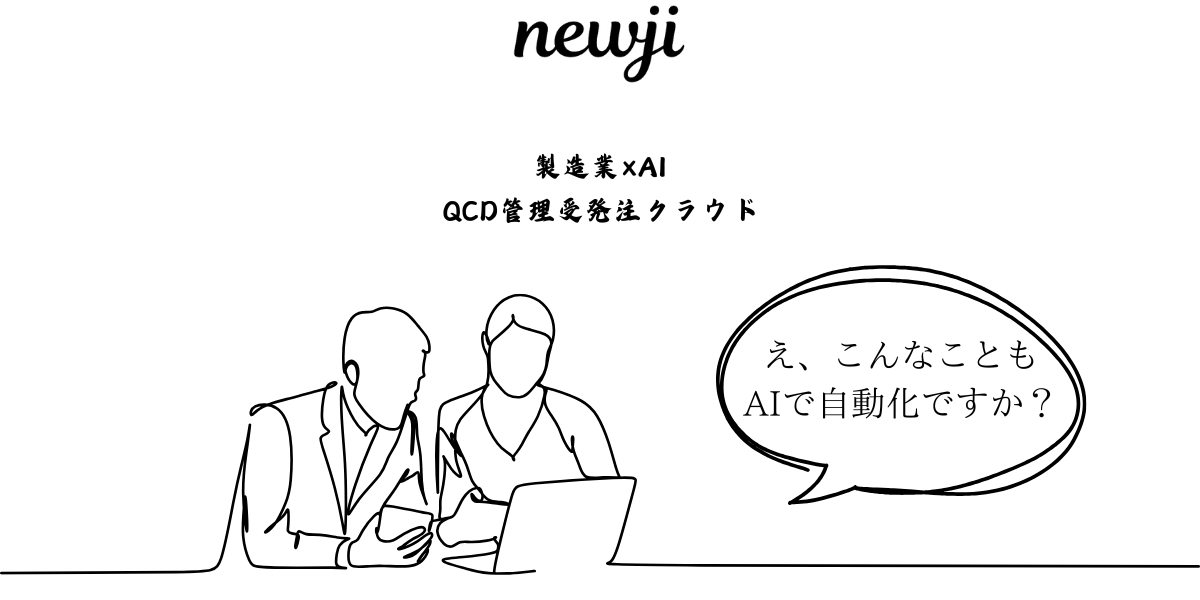
Aerospace prototype manufacturing
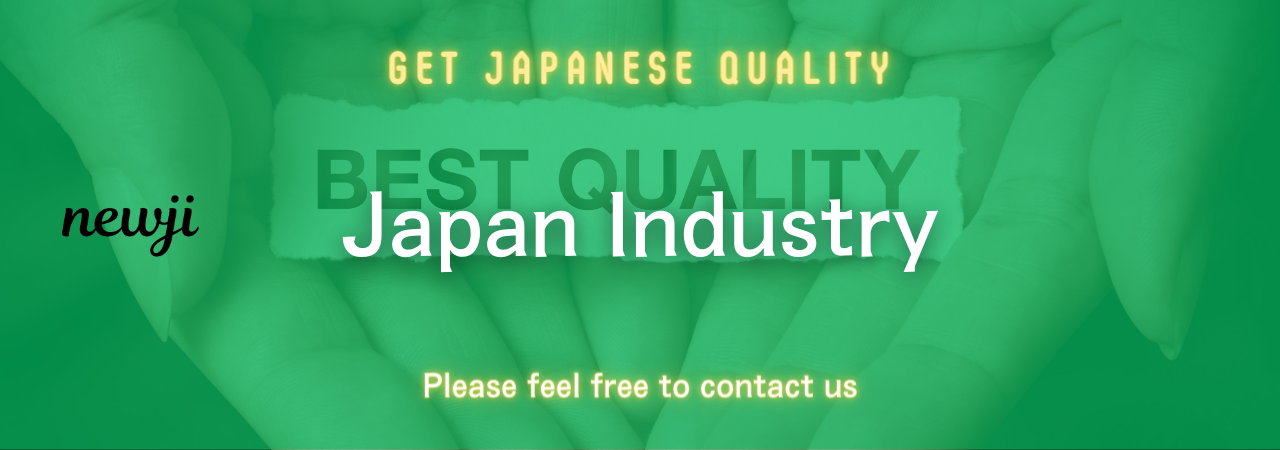
目次
Understanding Aerospace Prototype Manufacturing
Aerospace prototype manufacturing is an essential part of developing new aircraft and spacecraft.
It involves creating test versions of aircraft components or entire systems to evaluate their design and functionality before mass production.
This process helps engineers and designers identify potential issues and refine designs for optimal performance.
What is Aerospace Prototype Manufacturing?
In simple terms, aerospace prototype manufacturing is the creation of experimental models or prototypes of aerospace components.
These models are used to test and refine designs for new aircraft, spacecraft, or related systems.
Prototypes allow engineers to verify the capabilities and performance of their designs in real-world conditions.
The process involves several stages, including design, material selection, manufacturing, and testing.
Each stage is crucial in ensuring that the final product meets industry standards and performs effectively.
The Importance of Prototypes in Aerospace
Prototyping is vital in the aerospace industry for several reasons.
First, it allows for the identification and resolution of design flaws early in the development process.
By testing a prototype, engineers can observe how a design performs under various conditions and make necessary adjustments before full-scale production.
Second, creating a prototype helps streamline the production process by identifying optimal manufacturing techniques.
This can lead to cost savings and increased efficiency in producing the final product.
Finally, prototypes provide valuable data for regulatory compliance.
Aerospace components and systems are subject to stringent safety and performance standards.
Prototypes can help demonstrate compliance with these standards, ensuring the final product is safe and reliable.
Stages of Aerospace Prototype Manufacturing
The aerospace prototype manufacturing process can be broken down into several key stages:
Design and Conceptualization
The first stage involves developing a detailed design of the proposed aerospace component or system.
Engineers use advanced software tools to create 3D models and detailed drawings of the prototype.
These tools allow for precise calculations and simulations to evaluate the feasibility and performance of the design.
Material Selection
Once the design is finalized, the next step is selecting the appropriate materials.
Material selection is crucial in aerospace manufacturing, as components must withstand extreme conditions while maintaining low weight.
Engineers consider factors such as strength, temperature resistance, and weight when choosing materials for their prototypes.
Manufacturing
The manufacturing stage involves creating the physical prototype based on the design.
Various techniques, including 3D printing, CNC machining, and composite fabrication, may be used to produce the prototype.
Each technique offers unique advantages and is chosen based on the requirements of the specific component or system being manufactured.
Testing and Evaluation
Once the prototype is manufactured, it undergoes rigorous testing to assess its performance and identify any design flaws.
Tests may include structural, aerodynamic, thermal, and other evaluations to replicate the conditions the final product will face during operation.
Refinement
Based on the test results, engineers may need to refine the design further.
This stage can involve making changes to the design, material selection, or manufacturing process.
Refinement is crucial in ensuring the final product meets all necessary performance and safety standards.
Challenges in Aerospace Prototype Manufacturing
Despite its importance, aerospace prototype manufacturing presents several challenges.
One challenge is the high cost associated with creating aerospace prototypes.
Due to the complexity and precision required, manufacturing a prototype can be expensive, especially if multiple iterations are needed.
Another challenge is the time required to develop and test prototypes.
The process can be lengthy, with each stage taking considerable time to complete.
This can delay the overall time to market for new aerospace products.
Additionally, there is the challenge of ensuring that prototypes accurately represent the final product.
Any discrepancies between the prototype and the final product could result in performance issues or regulatory non-compliance.
Therefore, maintaining accuracy and consistency throughout the prototype manufacturing process is imperative.
Advancements in Aerospace Prototype Manufacturing
Recent advancements in technology have significantly impacted aerospace prototype manufacturing, helping to address some of its challenges.
3D printing, or additive manufacturing, has revolutionized the field by enabling faster and more cost-effective production of complex prototypes.
This technology allows engineers to quickly iterate designs and test prototypes without the same level of expense and time commitment traditional methods require.
Advanced simulation software has also improved the design and testing stages.
These tools allow for virtual testing and optimization, minimizing the need for costly physical prototypes.
Furthermore, the use of composite materials has enhanced the performance and capabilities of aerospace prototypes.
These materials offer increased strength-to-weight ratios, leading to more efficient and lightweight designs.
The Future of Aerospace Prototype Manufacturing
As technology continues to advance, the future of aerospace prototype manufacturing looks promising.
Emerging technologies such as artificial intelligence and machine learning are expected to play a significant role in design optimization and process automation.
The integration of digital twins — virtual replicas of physical systems — could further enhance prototype testing and evaluation.
This approach allows for real-time monitoring and analysis, facilitating more efficient and effective design iterations.
In conclusion, aerospace prototype manufacturing is a critical aspect of developing innovative and safe aerospace technologies.
Despite its challenges, advancements in technology continue to streamline the process, paving the way for more efficient and cost-effective production of prototypes.
With continued innovation, the future holds immense potential for the aerospace industry, ensuring that it can meet the ever-evolving demands of the 21st century.
資料ダウンロード
QCD管理受発注クラウド「newji」は、受発注部門で必要なQCD管理全てを備えた、現場特化型兼クラウド型の今世紀最高の受発注管理システムとなります。
ユーザー登録
受発注業務の効率化だけでなく、システムを導入することで、コスト削減や製品・資材のステータス可視化のほか、属人化していた受発注情報の共有化による内部不正防止や統制にも役立ちます。
NEWJI DX
製造業に特化したデジタルトランスフォーメーション(DX)の実現を目指す請負開発型のコンサルティングサービスです。AI、iPaaS、および先端の技術を駆使して、製造プロセスの効率化、業務効率化、チームワーク強化、コスト削減、品質向上を実現します。このサービスは、製造業の課題を深く理解し、それに対する最適なデジタルソリューションを提供することで、企業が持続的な成長とイノベーションを達成できるようサポートします。
製造業ニュース解説
製造業、主に購買・調達部門にお勤めの方々に向けた情報を配信しております。
新任の方やベテランの方、管理職を対象とした幅広いコンテンツをご用意しております。
お問い合わせ
コストダウンが利益に直結する術だと理解していても、なかなか前に進めることができない状況。そんな時は、newjiのコストダウン自動化機能で大きく利益貢献しよう!
(β版非公開)