- お役立ち記事
- AI automatic adjustment technology for printing presses and the future of productivity improvement
月間76,176名の
製造業ご担当者様が閲覧しています*
*2025年3月31日現在のGoogle Analyticsのデータより
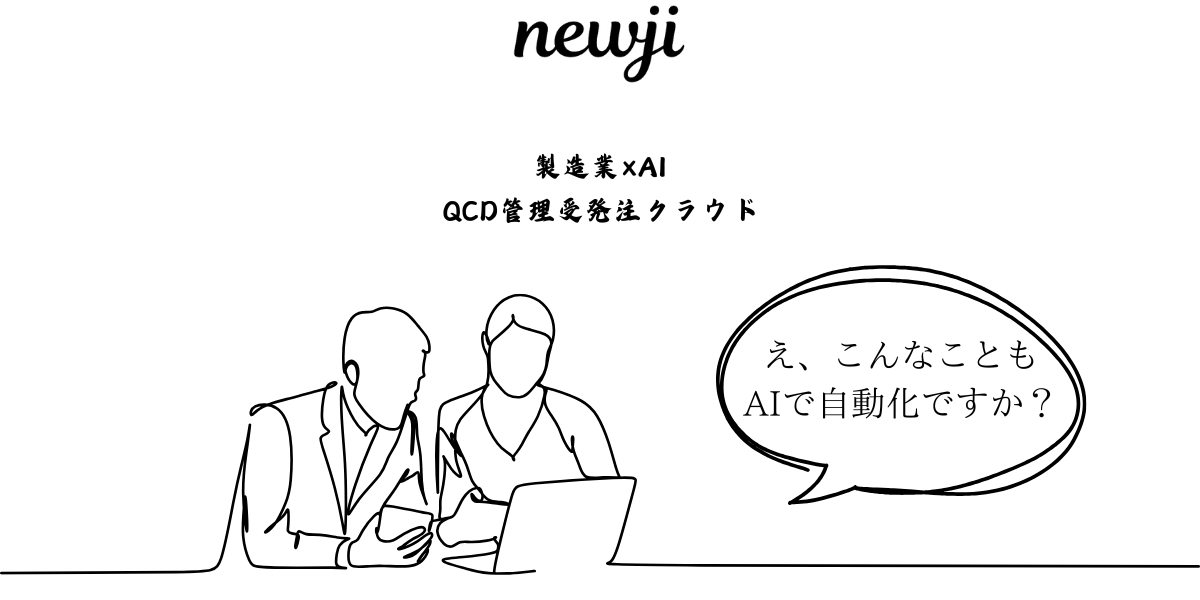
AI automatic adjustment technology for printing presses and the future of productivity improvement
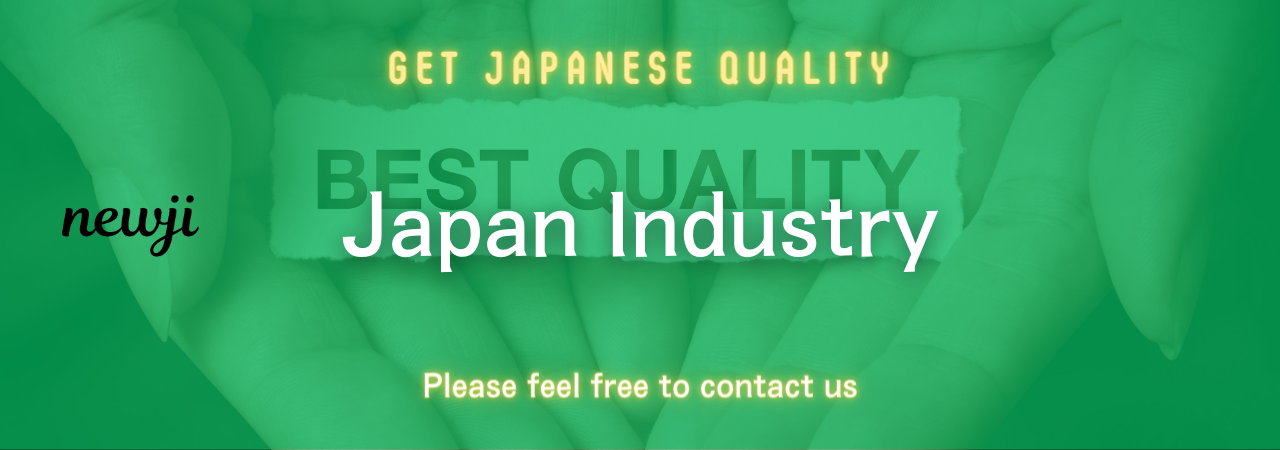
目次
Understanding AI in Printing Presses
Artificial Intelligence, or AI, has been revolutionizing various industries over the years, and the printing press is no exception.
The integration of AI into printing technology has paved the way for remarkable advancements in automation and efficiency.
From automating routine tasks to optimizing complex operations, AI is transforming the printing industry in unprecedented ways.
AI’s role in the printing press isn’t limited to just speeding up processes.
It is also about enhancing the overall productivity and quality of printed products.
By automating adjustments and configurations, AI ensures precision, reduces human error, and minimizes waste.
These improvements not only contribute to the efficiency of the operations but also significantly cut down costs.
How AI Automatic Adjustment Works
AI-driven automatic adjustment technology involves using sophisticated algorithms that enable machines to self-correct and optimize their operations without human intervention.
These algorithms process large volumes of data collected from the printing press machinery in real-time.
Through this data, AI systems can make precise adjustments to the machinery to ensure optimal performance.
For instance, during a print run, AI systems can identify any discrepancies in color or alignment and automatically adjust the settings to correct these issues.
This capability ensures that the quality of the output remains high without the need for continuous monitoring by human technicians.
Moreover, AI systems can predict potential issues before they arise.
By analyzing patterns from past data, AI can forecast machine maintenance needs and alert technicians ahead of time to prevent any downtime.
This proactive approach not only saves time but also enhances the lifespan of the machinery.
Impacts on Productivity
The biggest benefit AI brings to printing presses is the substantial improvement in productivity.
With AI automatic adjustment technology, printing presses can operate at higher speeds without sacrificing quality.
This capacity allows businesses to meet tight deadlines more efficiently and take on more projects, consequently boosting profitability.
Furthermore, by minimizing human intervention, AI allows operators to focus on more strategic decision-making processes rather than repetitive, mundane tasks.
This shift in focus leads to more innovative solutions and improvements in printing operations.
Overall, this harmonization of human and machine efforts results in increased output and a significant competitive edge in the marketplace.
AI and Waste Reduction
Waste reduction is a crucial aspect of any manufacturing process, and the printing industry is no different.
Traditional printing processes often involve a great deal of trial and error, which can lead to excessive waste.
AI technology addresses this issue by ensuring the first print is a perfect print.
The precision and efficiency of AI adjustment technology mean that fewer materials are wasted during production.
AI systems can determine the exact amount of ink and paper needed, reducing excess use and saving resources.
This environmental benefit also translates to financial savings, as less material waste equals lower operation costs.
Challenges in AI Implementation
Despite its advantages, implementing AI in printing presses is not without challenges.
The initial investment in AI technology can be high, making it difficult for smaller companies to adopt these advancements.
Additionally, training staff to work alongside AI systems requires time and resources.
There is also the concern of job displacement due to increased automation.
While AI automates routine tasks, the demand for skilled workers to oversee and manage the advanced systems remains.
Thus, it’s crucial for companies to invest in employee retraining programs to equip their workforce with the necessary skills to thrive in an AI-driven work environment.
The Future of Printing with AI
The future of printing presses with AI is promising.
As technology continues to evolve, AI systems are expected to become even more sophisticated, offering more precise and varied capabilities.
AI could soon manage entire printing operations, making real-time decisions faster and more accurately than human operators ever could.
Moreover, the integration of AI with other emerging technologies, such as the Internet of Things (IoT) and big data analytics, could lead to entirely new paradigms in the printing industry.
These advancements could unlock unprecedented levels of customization and efficiency, allowing businesses to cater to specific customer needs with remarkable agility and precision.
Conclusion
AI automatic adjustment technology is set to redefine productivity standards in the printing press industry.
By automating routine tasks, enhancing quality, and reducing waste, AI provides significant operational advantages.
Though the transition to AI-driven systems comes with challenges, the long-term benefits far outweigh the initial hurdles.
As AI technology becomes more accessible, its adoption is expected to accelerate, transforming how we view and utilize printing presses.
The future will likely see a harmonious blend of human expertise and AI efficiency, driving the printing industry to new heights of innovation and productivity.
資料ダウンロード
QCD管理受発注クラウド「newji」は、受発注部門で必要なQCD管理全てを備えた、現場特化型兼クラウド型の今世紀最高の受発注管理システムとなります。
ユーザー登録
受発注業務の効率化だけでなく、システムを導入することで、コスト削減や製品・資材のステータス可視化のほか、属人化していた受発注情報の共有化による内部不正防止や統制にも役立ちます。
NEWJI DX
製造業に特化したデジタルトランスフォーメーション(DX)の実現を目指す請負開発型のコンサルティングサービスです。AI、iPaaS、および先端の技術を駆使して、製造プロセスの効率化、業務効率化、チームワーク強化、コスト削減、品質向上を実現します。このサービスは、製造業の課題を深く理解し、それに対する最適なデジタルソリューションを提供することで、企業が持続的な成長とイノベーションを達成できるようサポートします。
製造業ニュース解説
製造業、主に購買・調達部門にお勤めの方々に向けた情報を配信しております。
新任の方やベテランの方、管理職を対象とした幅広いコンテンツをご用意しております。
お問い合わせ
コストダウンが利益に直結する術だと理解していても、なかなか前に進めることができない状況。そんな時は、newjiのコストダウン自動化機能で大きく利益貢献しよう!
(β版非公開)