- お役立ち記事
- AI Utilization in Manufacturing: Case Studies and Future Prospects
月間76,176名の
製造業ご担当者様が閲覧しています*
*2025年3月31日現在のGoogle Analyticsのデータより
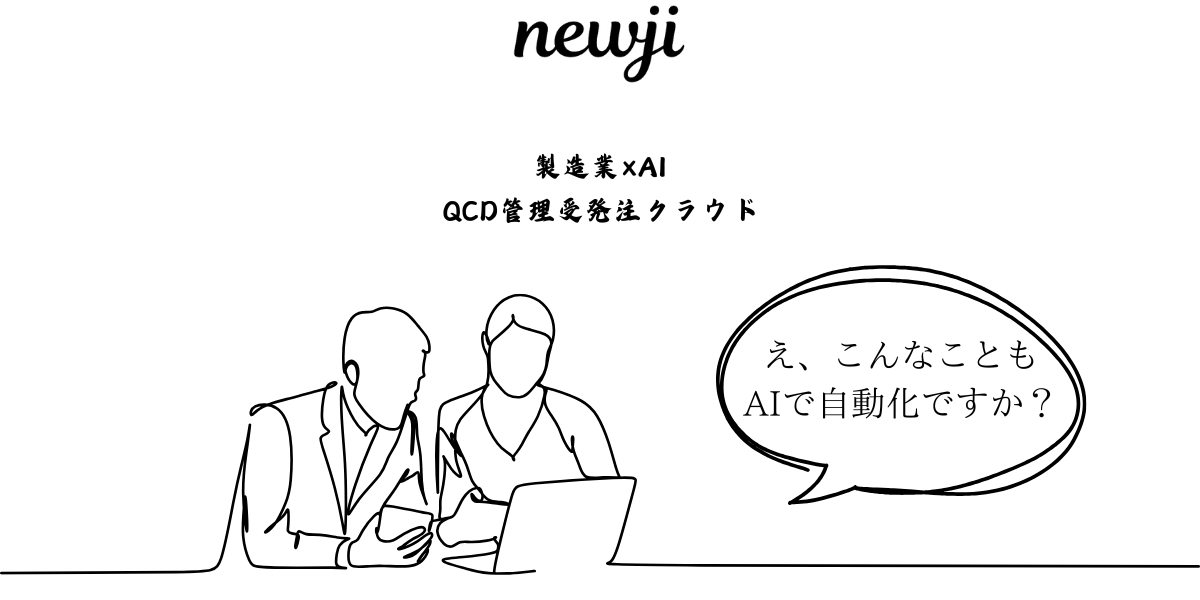
AI Utilization in Manufacturing: Case Studies and Future Prospects
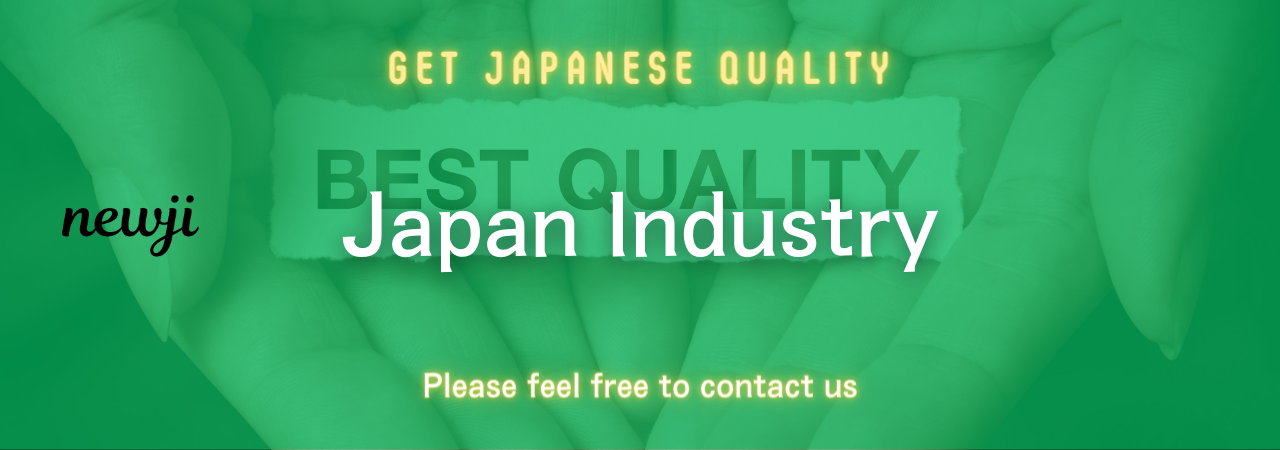
The manufacturing sector has consistently evolved with technological advancements, and artificial intelligence (AI) is the newest frontier.
The incorporation of AI in manufacturing brings a myriad of benefits, from enhancing efficiency to predicting equipment failures.
This article delves into practical case studies of AI utilization in manufacturing and what the future holds.
目次
Case Study 1: Predictive Maintenance at General Electric
General Electric (GE) is a prime example of how AI can revolutionize manufacturing through predictive maintenance.
By integrating AI algorithms into their systems, GE can forecast equipment failures before they occur.
Machine learning models analyze data from sensors installed on machinery, predicting when and where a failure might happen.
This preemptive approach drastically reduces downtime, saving significant costs and boosting productivity.
How GE Achieves Predictive Maintenance
GE leverages the Internet of Things (IoT) alongside AI technologies.
Sensors collect real-time data on machine operations, including temperature, vibration, and pressure.
This data is fed into AI algorithms that detect anomalies and forecast potential breakdowns.
Maintenance teams receive alerts, allowing them to address issues promptly and efficiently.
Case Study 2: Quality Control at BMW
BMW has embraced AI to enhance quality control in their manufacturing processes.
AI-driven computer vision systems analyze images of parts and products on the production line, identifying defects with high precision.
This real-time inspection ensures that only top-quality products reach customers.
Implementation Details of BMW’s AI System
BMW’s AI tool uses deep learning models trained on thousands of images to recognize defects.
Cameras installed along the production line capture continuous images.
The AI system compares these images to the ideal ones stored in its database.
Any discrepancies are flagged instantly, allowing human inspectors to intervene if necessary.
This system significantly reduces human error and improves the overall quality of the products.
Case Study 3: Supply Chain Optimization by Siemens
Siemens has implemented AI to optimize its supply chain management.
AI algorithms analyze vast amounts of data, including demand forecasts, supplier performance, and transportation logistics.
The result is a streamlined supply chain that can quickly adapt to changes and reduce costs.
How Siemens Transforms Supply Chain Management
Siemens utilizes AI-powered platforms to predict demand for products accurately.
These forecasts inform production schedules, ensuring that manufacturing processes align with market needs.
AI also helps in assessing supplier reliability and optimizing transportation routes.
This comprehensive approach ensures that Siemens maintains a fluid and cost-effective supply chain.
Future Prospects of AI in Manufacturing
AI’s role in manufacturing is poised to expand even further.
Future trends indicate even more integrated and intelligent systems.
Custom Manufacturing
The rise of AI could lead to more custom manufacturing.
AI can analyze customer preferences and design unique products tailored to individual needs.
This ability to offer personalized products could be a game-changer in competitive markets.
Augmented Workforce
AI will likely augment the manufacturing workforce rather than replace it.
By taking over repetitive and mundane tasks, AI allows human workers to focus on more complex and creative aspects of manufacturing.
This collaboration between humans and machines could lead to unprecedented levels of innovation and efficiency.
Enhanced Safety Measures
AI-driven safety measures could become more prevalent.
For instance, AI systems can monitor factory environments for hazardous conditions, alerting workers before accidents occur.
This proactive approach can significantly enhance workplace safety, potentially saving lives.
Sustainable Manufacturing
Sustainability is becoming a central focus in manufacturing.
AI can help manufacturers optimize resource usage, reducing waste and energy consumption.
Predictive algorithms can also suggest more sustainable materials and practices, aligning manufacturing processes with environmental goals.
Conclusion
AI is undeniably transforming manufacturing, bringing about efficiencies, cost savings, and product quality improvements.
Case studies from industry giants like General Electric, BMW, and Siemens showcase the tangible benefits of AI.
As AI technology continues to advance, its role in manufacturing will only grow, paving the way for a more intelligent and sustainable future.
Embracing AI now can position manufacturers at the forefront of this revolution, ensuring they remain competitive in an ever-evolving landscape.
資料ダウンロード
QCD管理受発注クラウド「newji」は、受発注部門で必要なQCD管理全てを備えた、現場特化型兼クラウド型の今世紀最高の受発注管理システムとなります。
ユーザー登録
受発注業務の効率化だけでなく、システムを導入することで、コスト削減や製品・資材のステータス可視化のほか、属人化していた受発注情報の共有化による内部不正防止や統制にも役立ちます。
NEWJI DX
製造業に特化したデジタルトランスフォーメーション(DX)の実現を目指す請負開発型のコンサルティングサービスです。AI、iPaaS、および先端の技術を駆使して、製造プロセスの効率化、業務効率化、チームワーク強化、コスト削減、品質向上を実現します。このサービスは、製造業の課題を深く理解し、それに対する最適なデジタルソリューションを提供することで、企業が持続的な成長とイノベーションを達成できるようサポートします。
製造業ニュース解説
製造業、主に購買・調達部門にお勤めの方々に向けた情報を配信しております。
新任の方やベテランの方、管理職を対象とした幅広いコンテンツをご用意しております。
お問い合わせ
コストダウンが利益に直結する術だと理解していても、なかなか前に進めることができない状況。そんな時は、newjiのコストダウン自動化機能で大きく利益貢献しよう!
(β版非公開)