- お役立ち記事
- Aiming to Improve Processing Quality: A New Quality Control System Proposal from Manufacturing Sales
Aiming to Improve Processing Quality: A New Quality Control System Proposal from Manufacturing Sales
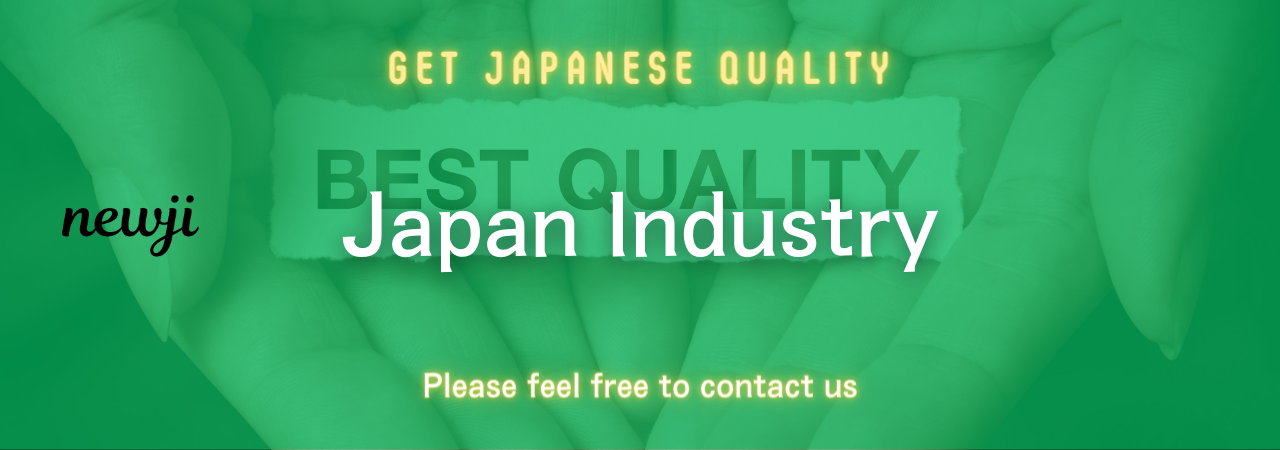
In the world of manufacturing, improving processing quality has always been a goal for companies striving for excellence. High standards in production not only ensure customer satisfaction but also help in maintaining a competitive edge in the market. To achieve this, a robust quality control system is essential, and today we are delving into a proposal for a new quality control system from the standpoint of manufacturing sales.
Quality control in manufacturing is a multifaceted process that encompasses various stages, from raw material inspection to final product testing. It’s a systematic approach that ensures each product meets the necessary standards and specifications. However, with advancements in technology and changing market demands, it’s necessary to continually refine and improve these systems.
The primary focus of this proposal is to integrate advanced technologies and innovative strategies into the existing quality control framework. By doing so, businesses can identify defects, reduce waste, and enhance overall efficiency.
目次
The Role of Technology in Quality Control
In recent years, technology has become a game-changer in manufacturing. With the advent of Industry 4.0, the integration of IoT (Internet of Things), AI (Artificial Intelligence), and machine learning has transformed traditional manufacturing processes.
1. IoT and Sensors
IoT devices and sensors play a crucial role in real-time monitoring and data collection. These devices can be placed at various checkpoints along the production line to continuously collect data on different parameters such as temperature, pressure, and humidity. This real-time data is invaluable for quality control as it helps in identifying discrepancies as soon as they occur, allowing for immediate corrective action.
2. AI and Machine Learning
AI and machine learning algorithms can analyze vast amounts of data to identify patterns and trends. By leveraging these technologies, manufacturers can predict potential quality issues before they occur. For instance, machine learning models can be trained to detect anomalies in the production process, which can then be flagged for further inspection.
3. Automation and Robotics
Automation and robotics are revolutionizing the manufacturing sector by enhancing precision and reducing human error. Automated inspection systems, equipped with high-resolution cameras and lasers, can perform detailed inspections that are often beyond the capabilities of human inspectors. These systems can analyze the dimensions, shape, and surface quality of products, ensuring that they meet the specified standards.
Implementing a New Quality Control System
To implement an effective quality control system, manufacturers need to follow a structured approach. Here’s a step-by-step outline:
1. Assessment of Current System
Before implementing a new system, it’s important to assess the current quality control framework. This assessment should identify the strengths and weaknesses of the existing system, providing a clear understanding of the areas that need improvement.
2. Setting Clear Objectives
Defining clear objectives is crucial for the success of any new system. These objectives should be aligned with the overall business goals and should focus on enhancing product quality, reducing defects, and increasing operational efficiency.
3. Technology Integration
Based on the assessment, manufacturers should identify the technologies that best suit their needs. Integrating IoT devices, AI, and automation into the production line can significantly enhance quality control measures. It’s also important to ensure that these technologies are compatible with existing systems to avoid disruptions.
4. Training and Development
Human resources play a critical role in the success of any quality control system. Training and development programs should be conducted to educate employees about the new technologies and processes. This will not only improve their skills but also foster a culture of quality within the organization.
5. Continuous Monitoring and Feedback
Once the new system is implemented, continuous monitoring is essential to ensure its effectiveness. Regular feedback from the production team and periodic audits can help in identifying any gaps or areas for further improvement.
Benefits of a Robust Quality Control System
Implementing a new quality control system offers several benefits:
1. Enhanced Product Quality
By leveraging advanced technologies, manufacturers can ensure that each product meets the highest quality standards. This leads to higher customer satisfaction and loyalty.
2. Reduced Defects and Waste
Early detection of quality issues helps in reducing defects and minimizing waste. This not only improves operational efficiency but also reduces production costs.
3. Competitive Advantage
A robust quality control system gives manufacturers a competitive edge by ensuring reliable and high-quality products. This can help in attracting new customers and retaining existing ones.
4. Regulatory Compliance
Adhering to quality standards is essential for regulatory compliance. An effective quality control system ensures that all products meet the necessary regulations, reducing the risk of penalties or legal issues.
Challenges and Solutions
While the benefits are significant, implementing a new quality control system also comes with challenges. Here are a few common challenges and their solutions:
1. High Initial Costs
Investing in new technologies can be expensive. However, the long-term benefits such as reduced defects and increased efficiency can outweigh the initial costs. Manufacturers can also explore different financing options or phased implementation to manage costs.
2. Resistance to Change
Employees may resist changes to their routine. To address this, it’s important to involve them in the process and provide adequate training. Communicating the benefits and offering incentives can also help in overcoming resistance.
3. Technical Issues
Integrating new technologies with existing systems can sometimes lead to technical issues. Working with experienced technology partners and conducting thorough testing can help in mitigating these risks.
As the manufacturing industry continues to evolve, staying ahead of the curve requires embracing new technologies and continually improving processes. By implementing a robust quality control system that leverages IoT, AI, and automation, manufacturers can enhance product quality, reduce defects, and maintain a competitive edge in the market.
資料ダウンロード
QCD調達購買管理クラウド「newji」は、調達購買部門で必要なQCD管理全てを備えた、現場特化型兼クラウド型の今世紀最高の購買管理システムとなります。
ユーザー登録
調達購買業務の効率化だけでなく、システムを導入することで、コスト削減や製品・資材のステータス可視化のほか、属人化していた購買情報の共有化による内部不正防止や統制にも役立ちます。
NEWJI DX
製造業に特化したデジタルトランスフォーメーション(DX)の実現を目指す請負開発型のコンサルティングサービスです。AI、iPaaS、および先端の技術を駆使して、製造プロセスの効率化、業務効率化、チームワーク強化、コスト削減、品質向上を実現します。このサービスは、製造業の課題を深く理解し、それに対する最適なデジタルソリューションを提供することで、企業が持続的な成長とイノベーションを達成できるようサポートします。
オンライン講座
製造業、主に購買・調達部門にお勤めの方々に向けた情報を配信しております。
新任の方やベテランの方、管理職を対象とした幅広いコンテンツをご用意しております。
お問い合わせ
コストダウンが利益に直結する術だと理解していても、なかなか前に進めることができない状況。そんな時は、newjiのコストダウン自動化機能で大きく利益貢献しよう!
(Β版非公開)