- お役立ち記事
- Aluminum alloy thin plate processing and its market utilization in the automobile industry
月間77,185名の
製造業ご担当者様が閲覧しています*
*2025年2月28日現在のGoogle Analyticsのデータより
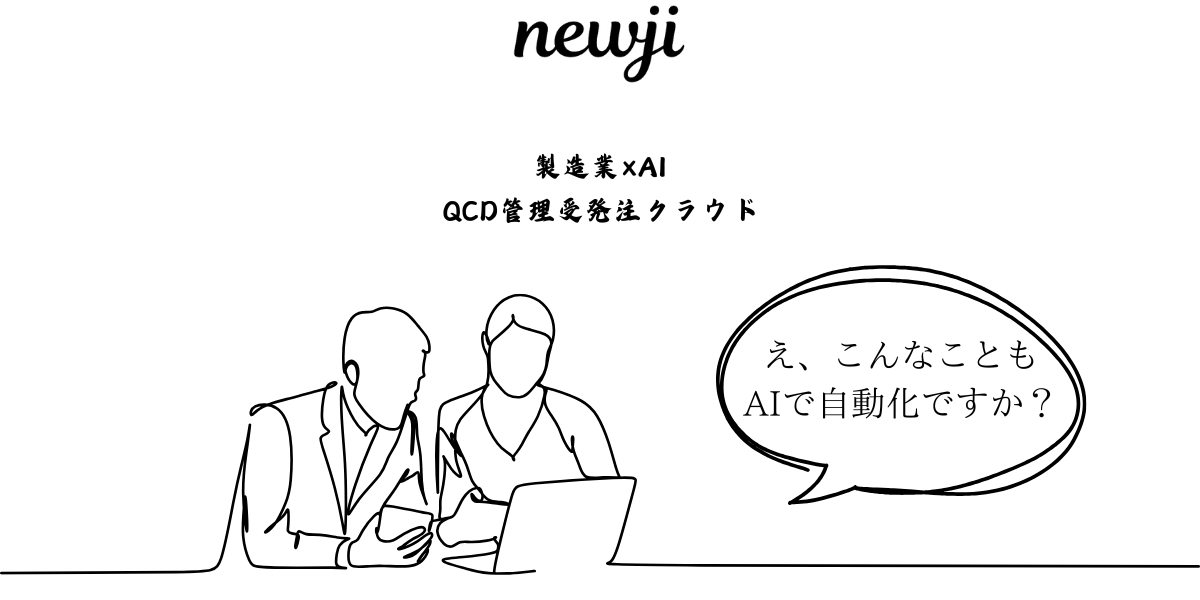
Aluminum alloy thin plate processing and its market utilization in the automobile industry
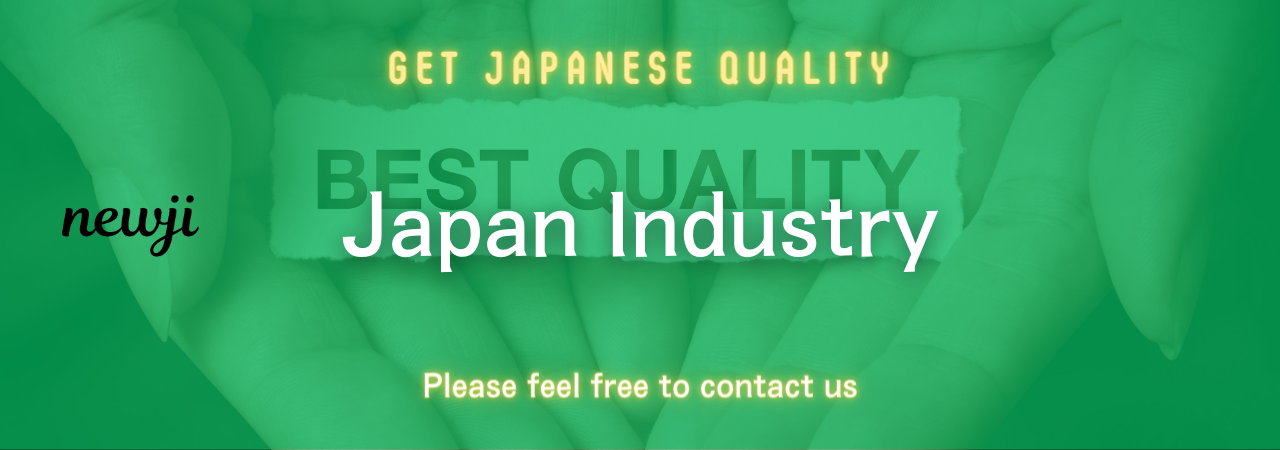
目次
Introduction to Aluminum Alloy Thin Plate Processing
Aluminum alloys have become an integral part of various industries owing to their light weight, strength, and exceptional corrosion resistance.
Among the many forms of aluminum alloy, thin plates are gaining popularity due to their versatility and ease of fabrication.
In recent years, the automobile industry has identified the manifold benefits of incorporating aluminum alloy thin plates into vehicle design and manufacturing.
This article delves into the process of aluminum alloy thin plate processing and explores its growing significance in the automobile sector.
Understanding Aluminum Alloy Thin Plates
Aluminum alloys are composed of aluminum mixed with other elements like copper, magnesium, and silicon to enhance specific properties.
These materials are processed into thin plates, which are then utilized in various applications.
Thin plates have a typical thickness ranging from 0.5mm to 6mm, making them ideal for lightweight structures without compromising strength.
Through careful alloy selection and processing, manufacturers can tailor the characteristics of aluminum thin plates to meet precise requirements of specific applications.
Processing Techniques for Aluminum Alloy Thin Plates
The production of aluminum alloy thin plates involves a series of complex processes.
One of the initial steps in processing is casting, where liquid aluminum alloy is poured into molds to form ingots.
These ingots are then subjected to rolling, a procedure that reduces thickness while simultaneously increasing the length.
Depending on desired features, rolling can be accomplished through hot rolling or cold rolling techniques.
Hot rolling generally occurs at temperatures above the material’s recrystallization point, resulting in a more ductile and workable product.
Cold rolling, on the other hand, is performed at or near room temperature, allowing for a superior surface finish and closer control of thickness.
Subsequent processes include annealing, which softens the metal, thereby enhancing formability.
Post-rolling, aluminum thin plates undergo surface treatments such as anodizing or painting to improve durability and aesthetics.
Benefits of Using Aluminum Alloy Thin Plates in the Automobile Industry
The use of aluminum alloy thin plates in automobiles is primarily driven by the need for weight reduction—a crucial factor in enhancing fuel efficiency.
Aluminum is roughly one-third the weight of steel, enabling manufacturers to produce lighter vehicles without sacrificing performance or safety.
Apart from weight reduction, aluminum alloys offer superior corrosion resistance.
This characteristic makes them particularly useful for vehicle components exposed to environmental elements, such as body panels and chassis parts.
Furthermore, aluminum alloys have an excellent strength-to-weight ratio, which ensures that the durability of the vehicle is maintained.
The recyclability of aluminum is another significant benefit.
Automakers are increasingly focusing on sustainability, and aluminum can be recycled without loss in quality, making it an environmentally friendly material choice.
Market Utilization of Aluminum Alloy Thin Plates in the Automobile Industry
The demand for aluminum alloy thin plates in the automobile industry is on the rise due to the ongoing quest for improved energy efficiency and reduced emissions.
As governments around the world set stringent fuel economy standards, car manufacturers are turning to lightweight materials like aluminum to comply with these regulations.
Luxury car brands were some of the first to integrate aluminum alloy thin plates into their designs.
However, the trend has rapidly permeated mass market models as well.
Manufacturers now utilize these thin plates for producing roofs, doors, hoods, and other critical vehicle parts.
Electric vehicles (EVs) have also significantly bolstered the demand for aluminum alloy thin plates.
Due to limited battery range constraints, EV manufacturers are prioritizing weight reduction as a means to extend driving range.
Additionally, advancements in joining technologies, like friction stir welding, have facilitated the incorporation of aluminum alloy thin plates in assembly lines.
These techniques allow for the reliable fusion of aluminum with other metals, ensuring seamless integration into complex vehicle structures.
Challenges and Future Prospects
While aluminum alloy thin plates offer significant advantages, their adoption does not come without challenges.
One major hurdle is the higher cost associated with aluminum compared to traditional steel.
Nonetheless, these costs are often offset by savings realized through improved fuel efficiency and the long-term durability of aluminum structures.
Another challenge is the requirement for specialized equipment and skills to process and weld aluminum alloys, which may necessitate substantial investment by manufacturers.
However, ongoing technological advancements are expected to make these processes more efficient and cost-effective.
Looking ahead, the future of aluminum alloy thin plate processing appears promising.
Ongoing research and development efforts aim to optimize both the processing techniques and the alloy compositions to further enhance performance.
In parallel, increasing emphasis on sustainability will likely continue driving the adoption of lightweight materials like aluminum in automotive applications.
Conclusion
Aluminum alloy thin plates are a game-changer in the automobile industry, offering a blend of strength, weight reduction, and resistance to corrosion.
Through sophisticated processing techniques, these plates are becoming increasingly prevalent in vehicle manufacturing.
Despite some challenges, the market utilization of aluminum alloy thin plates is set to grow as automakers strive to meet future energy and environmental targets.
As technology evolves, aluminum is poised to play a pivotal role in the production of next-generation vehicles.
資料ダウンロード
QCD管理受発注クラウド「newji」は、受発注部門で必要なQCD管理全てを備えた、現場特化型兼クラウド型の今世紀最高の受発注管理システムとなります。
ユーザー登録
受発注業務の効率化だけでなく、システムを導入することで、コスト削減や製品・資材のステータス可視化のほか、属人化していた受発注情報の共有化による内部不正防止や統制にも役立ちます。
NEWJI DX
製造業に特化したデジタルトランスフォーメーション(DX)の実現を目指す請負開発型のコンサルティングサービスです。AI、iPaaS、および先端の技術を駆使して、製造プロセスの効率化、業務効率化、チームワーク強化、コスト削減、品質向上を実現します。このサービスは、製造業の課題を深く理解し、それに対する最適なデジタルソリューションを提供することで、企業が持続的な成長とイノベーションを達成できるようサポートします。
製造業ニュース解説
製造業、主に購買・調達部門にお勤めの方々に向けた情報を配信しております。
新任の方やベテランの方、管理職を対象とした幅広いコンテンツをご用意しております。
お問い合わせ
コストダウンが利益に直結する術だと理解していても、なかなか前に進めることができない状況。そんな時は、newjiのコストダウン自動化機能で大きく利益貢献しよう!
(β版非公開)