- お役立ち記事
- Aluminum forming technology, new construction methods, and application to reducing the weight of automobiles
月間77,185名の
製造業ご担当者様が閲覧しています*
*2025年2月28日現在のGoogle Analyticsのデータより
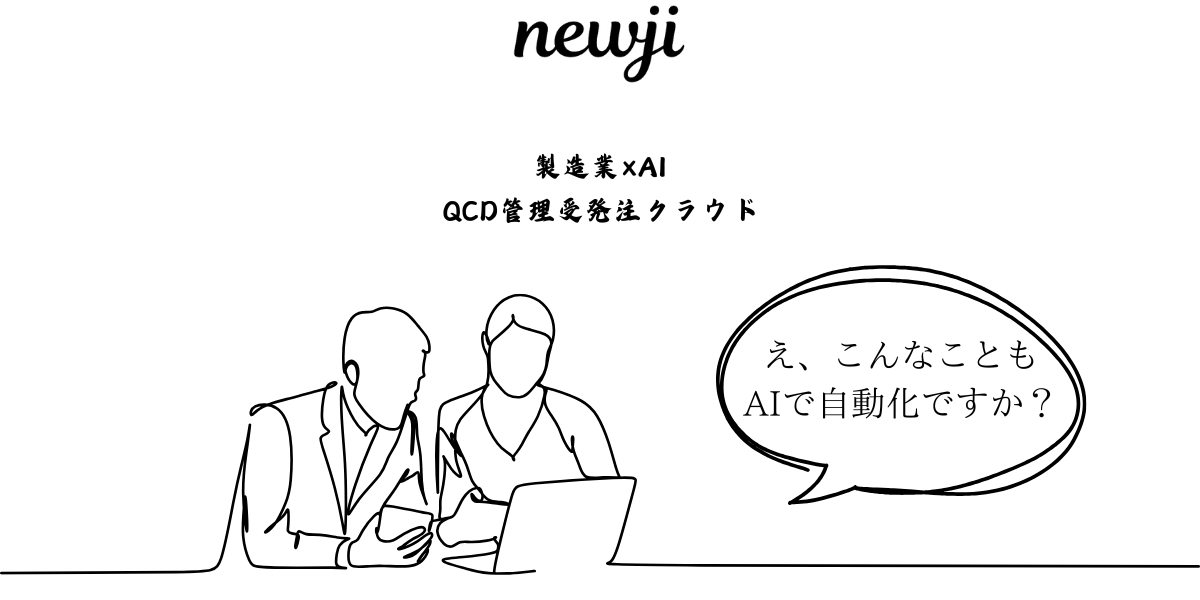
Aluminum forming technology, new construction methods, and application to reducing the weight of automobiles
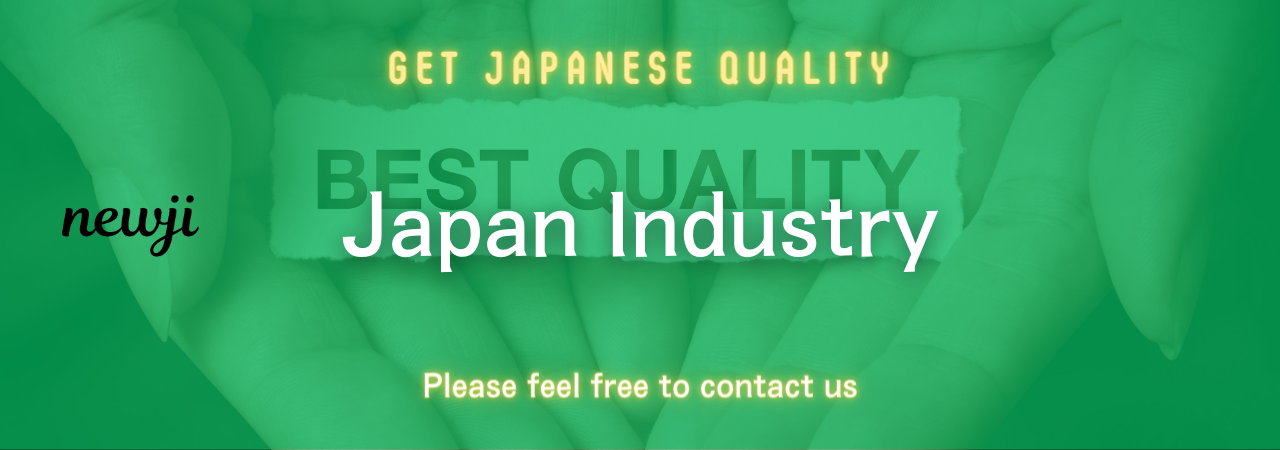
目次
Introduction to Aluminum Forming Technology
Aluminum forming technology is revolutionizing various industries, particularly automotive manufacturing.
This technology offers a sustainable and efficient way to create lightweight, durable components, ultimately enhancing vehicle performance and fuel efficiency.
As automotive companies strive to produce lighter vehicles to meet environmental standards and customer demand for better mileage, aluminum’s role becomes increasingly important.
But what is aluminum forming, and how is it transforming automotive manufacturing?
Let’s explore.
The Basics of Aluminum Forming
Aluminum forming involves shaping aluminum into desired forms and structures.
The process includes various techniques such as casting, rolling, forging, and extrusion.
Each method serves different purposes, offering unique benefits and meeting specific project requirements.
Casting involves pouring liquid aluminum into a mold to obtain complex shapes, ideal for parts with intricate designs.
Extrusion pushes aluminum through a die to create elongated shapes like rods and channels, frequently used in vehicle frames and panels.
Rolling and forging work aluminum into sheets or more dense parts, providing impressive strength-to-weight ratios.
These processes collectively contribute to the adaptability and versatility of aluminum in automotive applications.
Advantages of Aluminum in Automotive Manufacturing
Aluminum forms a pinnacle of engineering advantages that appeal to car manufacturers.
Firstly, aluminum is significantly lighter than other metals like steel.
A lighter vehicle means fewer emissions and better fuel efficiency, meeting stringent regulatory demands.
Moreover, aluminum is incredibly durable and corrosion-resistant, adding to the vehicle’s longevity and safety.
Crafting parts from aluminum can result in more affordable maintenance and repairs, benefiting drivers in the long run.
Recyclability is another standout feature, as aluminum can be reused without degrading quality, further enhancing sustainability efforts.
As a conductor of energy, aluminum improves electric vehicle efficiency by effectively distributing power, aiding in the pursuit of greener transportation solutions.
New Construction Methods in Aluminum Forming
The technology behind aluminum forming never ceases to evolve, giving rise to innovative construction methods.
These groundbreaking techniques not only boost production speed and efficiency but also lead to further weight reduction in automobile manufacturing.
Let’s delve into some of these methods.
Advanced Manufacturing Techniques
Today, manufacturers leverage advanced methods like hydroforming, which uses pressurized fluid to shape aluminum sheets into intricate geometries with high precision.
This technique minimizes material waste and allows designers to produce sophisticated, aerodynamic shapes.
Another breakthrough is additive manufacturing or 3D printing, where aluminum alloys can be effectively used to make complex structures that were once impossible with traditional methods.
The layer-by-layer construction can result in components that are not only lighter but also more robust.
Resonating welding introduces a new way to join aluminum parts with enhanced uniformity and reduced distortion, improving the longevity and reliability of assembled parts.
Automation and Robotics
The integration of robotics and automation in aluminum forming processes has enabled the scaling of production and enhanced quality assurance.
By employing robots, manufacturers can achieve high repeatability and accuracy in forming parts, ensuring consistency across production batches.
Automation reduces human error, accelerates production timelines, and allows the workforce to concentrate on more complex and creative tasks.
As a result, the efficiency and effectiveness of the entire manufacturing process are elevated, driving down production costs and enabling faster vehicle development.
Application in Reducing Vehicle Weight
Incorporating aluminum has become a critical factor in reducing the overall weight of vehicles.
Manufacturers strategically use aluminum in key vehicle components such as the chassis, engine blocks, and body panels.
By doing so, they maintain structural integrity while significantly lowering weight.
This shift not only benefits performance but also profoundly impacts fuel efficiency.
Lighter vehicles require less energy to move, translating directly into better fuel consumption and reduced emissions, which are crucial for meeting existing and future environmental regulations.
Electric vehicles, in particular, benefit from aluminum’s use by extending range and enhancing battery performance due to less burden on power systems.
Case Studies in Automotive Innovation
Several automotive giants have already embraced aluminum to revolutionary effect.
For instance, Ford used high-strength aluminum alloys in their popular F-150 model, resulting in improved fuel efficiency and payload capabilities without compromising safety.
Tesla incorporates aluminum throughout its electric vehicle lineup to maximize performance and range, demonstrating the material’s adaptability to cutting-edge designs and technology.
These case studies emphasize that aluminum forming technology is not limited to luxury or high-end vehicles.
It’s driving a broader shift across the industry towards more sustainable and efficient automotive manufacturing.
Conclusion
Aluminum forming technology is at the forefront of innovation in automobile manufacturing.
Through a combination of advanced techniques and new construction methods, automakers are achieving unprecedented levels of weight reduction, leading to more fuel-efficient and environmentally friendly vehicles.
The ongoing advancements in this field suggest a promising future where the automotive sector can continue evolving toward sustainability and performance without sacrificing quality or safety.
By embracing these new technologies, the automotive industry not only meets regulatory requirements but also aligns itself with consumer expectations for greener and more efficient vehicles.
As these methods and applications continue to improve, the role of aluminum in shaping the future of transportation becomes ever more integral.
資料ダウンロード
QCD管理受発注クラウド「newji」は、受発注部門で必要なQCD管理全てを備えた、現場特化型兼クラウド型の今世紀最高の受発注管理システムとなります。
ユーザー登録
受発注業務の効率化だけでなく、システムを導入することで、コスト削減や製品・資材のステータス可視化のほか、属人化していた受発注情報の共有化による内部不正防止や統制にも役立ちます。
NEWJI DX
製造業に特化したデジタルトランスフォーメーション(DX)の実現を目指す請負開発型のコンサルティングサービスです。AI、iPaaS、および先端の技術を駆使して、製造プロセスの効率化、業務効率化、チームワーク強化、コスト削減、品質向上を実現します。このサービスは、製造業の課題を深く理解し、それに対する最適なデジタルソリューションを提供することで、企業が持続的な成長とイノベーションを達成できるようサポートします。
製造業ニュース解説
製造業、主に購買・調達部門にお勤めの方々に向けた情報を配信しております。
新任の方やベテランの方、管理職を対象とした幅広いコンテンツをご用意しております。
お問い合わせ
コストダウンが利益に直結する術だと理解していても、なかなか前に進めることができない状況。そんな時は、newjiのコストダウン自動化機能で大きく利益貢献しよう!
(β版非公開)