- お役立ち記事
- Alumite Processing Technology and Its Applications
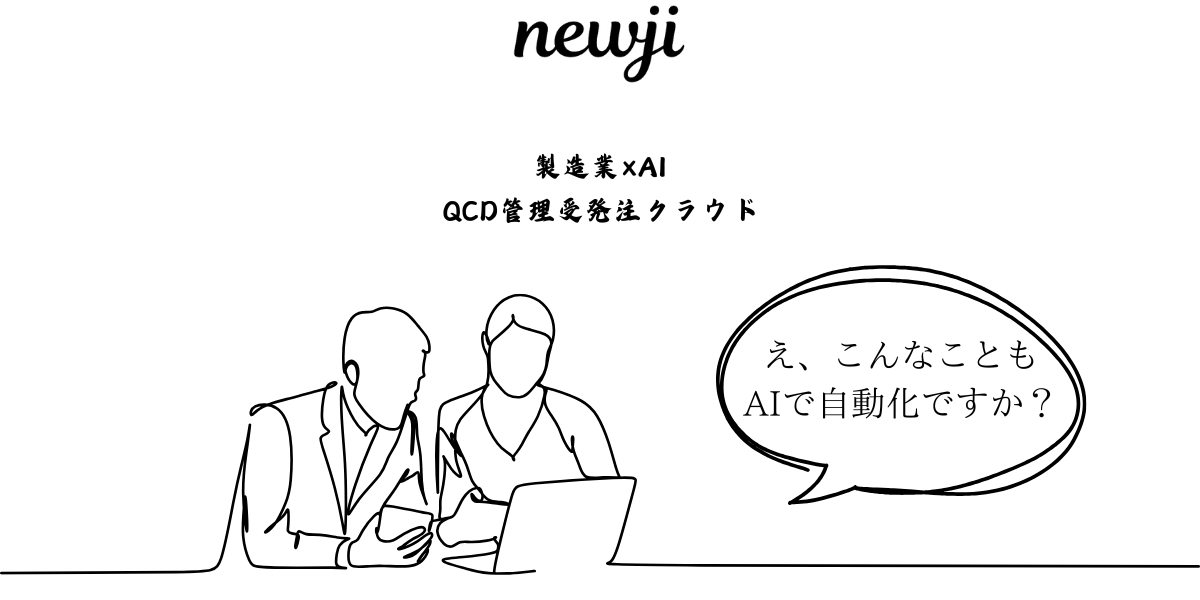
Alumite Processing Technology and Its Applications
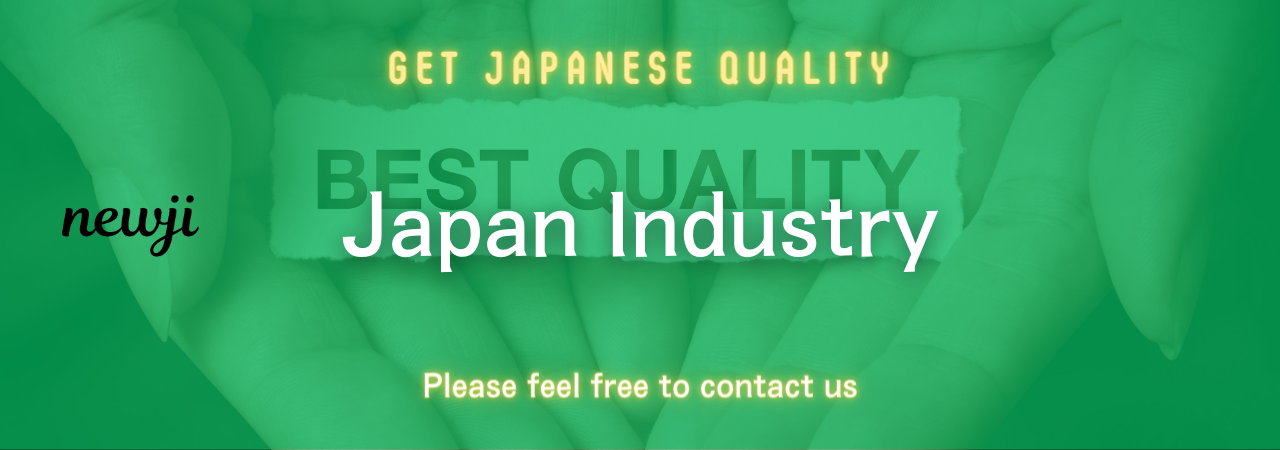
Alumite processing technology has become an integral part of various industries due to its versatility and durability. This process, often referred to as anodizing aluminum, enhances the natural oxide layer on aluminum’s surface, making it more resistant to corrosion and wear. The applications of alumite processing technology are numerous, ranging from automotive parts to everyday household items.
目次
What is Alumite Processing?
Alumite processing, or anodizing, is a surface treatment technique used primarily on aluminum and its alloys. This process involves the electrolytic passivation of aluminum to form a robust and thick oxide layer.
Unlike painting or coating, anodizing permanently alters the aluminum surface, providing several intrinsic properties that are highly desirable in industrial applications.
How Does Alumite Processing Work?
The process begins by immersing aluminum parts into an acid electrolyte bath and passing an electric current through the medium.
This causes the aluminum surface to oxidize, creating a thicker-than-normal oxide layer.
The result is a metal surface that is highly durable and resistant to scratches, corrosion, and other forms of wear and tear.
Benefits of Alumite Processing
The benefits of alumite processing extend beyond mere aesthetics.
The robustness and enhanced properties make it a preferred choice for various fields.
Enhanced Durability
One of the most noticeable benefits of alumite processing is improved durability.
The thick oxide layer created through anodizing is much harder than the untreated aluminum, making the metal more resistant to physical wear and corrosion.
Corrosion Resistance
Aluminum naturally forms an oxide layer when exposed to air, which provides some level of corrosion resistance.
Anodizing enhances this natural property significantly by creating a much thicker and more uniform oxide layer. This is especially beneficial in marine and industrial environments where corrosion can be a significant issue.
Improved Aesthetics
Anodizing allows for the addition of various colors and finishes to aluminum parts.
Dyes can be introduced during the anodizing process to achieve a wide range of colors, making the metal more aesthetically pleasing for consumer products and architectural applications.
Electrical Insulation
The oxide layer formed during anodizing is also an excellent electrical insulator.
This property is particularly useful in electronic applications where insulating properties are required.
Applications of Alumite Processing Technology
The extensive benefits of alumite processing technology make it suitable for a wide range of applications.
Whether it’s for functional or decorative purposes, anodized aluminum is found in almost every industry.
Automotive Industry
In the automotive industry, alumite-processed aluminum is used for various components like engine parts, trim, and body panels.
The enhanced durability and corrosion resistance ensure that these parts last longer and require less maintenance.
Aerospace Industry
The aerospace industry extensively uses anodized aluminum for aircraft components because of its lightweight nature and excellent durability.
Anodized parts are found in everything from exterior panels to interior fixtures.
Consumer Electronics
Many consumer electronics, including smartphones, laptops, and cameras, utilize anodized aluminum for their outer casing.
The process not only improves the durability of these devices but also allows for sleek, colorful finishes that appeal to consumers.
Architectural Applications
In architecture, anodized aluminum is used for window frames, curtain walls, and exterior facades.
The process enables designers to achieve a distinctive look while ensuring that the material can withstand the elements.
Marine Applications
Given its superior resistance to corrosion, anodized aluminum is ideal for marine applications.
It is commonly used in boat fittings, railings, and other hardware exposed to saltwater environments.
Types of Anodizing Processes
There are several types of anodizing processes, each suited for different applications and desired outcomes.
Type I: Chromic Acid Anodizing
Type I anodizing uses chromic acid and is generally used for parts that require a thinner oxide layer.
This type is less aggressive and is commonly used for aerospace components and military applications.
Type II: Sulfuric Acid Anodizing
Type II anodizing employs sulfuric acid and is one of the most common anodizing types.
It creates a moderately thick oxide layer and is used for a broad range of applications, including architectural and consumer products.
Type III: Hard Anodizing
Type III, also known as hard anodizing, uses a similar process to Type II but with different parameters to create a much thicker and harder oxide layer.
This type is used in applications that require maximum abrasion and corrosion resistance, such as heavy machinery and automotive components.
Environmental Considerations
While alumite processing offers numerous benefits, it is essential to consider the environmental impact.
The anodizing process involves chemicals like sulfuric and chromic acids, which need to be handled and disposed of properly to minimize environmental damage.
However, anodized aluminum is highly recyclable, contributing to reduced waste and resource conservation.
Recycling
Aluminum is one of the most recyclable materials available.
The anodizing process does not affect the metal’s recyclability, making it an eco-friendly choice for various applications.
Waste Management
Responsible management of the waste products from the anodizing process is crucial.
Many companies have adopted stringent waste treatment measures to ensure minimal environmental impact.
In conclusion, alumite processing technology provides numerous advantages, making it a popular choice across various industries.
Its benefits, ranging from enhanced durability and corrosion resistance to improved aesthetics and electrical insulation, contribute to its widespread use.
As industries continue to evolve, the demand for robust and sustainable materials like anodized aluminum is likely to grow, further cementing the importance of alumite processing technology.
資料ダウンロード
QCD調達購買管理クラウド「newji」は、調達購買部門で必要なQCD管理全てを備えた、現場特化型兼クラウド型の今世紀最高の購買管理システムとなります。
ユーザー登録
調達購買業務の効率化だけでなく、システムを導入することで、コスト削減や製品・資材のステータス可視化のほか、属人化していた購買情報の共有化による内部不正防止や統制にも役立ちます。
NEWJI DX
製造業に特化したデジタルトランスフォーメーション(DX)の実現を目指す請負開発型のコンサルティングサービスです。AI、iPaaS、および先端の技術を駆使して、製造プロセスの効率化、業務効率化、チームワーク強化、コスト削減、品質向上を実現します。このサービスは、製造業の課題を深く理解し、それに対する最適なデジタルソリューションを提供することで、企業が持続的な成長とイノベーションを達成できるようサポートします。
オンライン講座
製造業、主に購買・調達部門にお勤めの方々に向けた情報を配信しております。
新任の方やベテランの方、管理職を対象とした幅広いコンテンツをご用意しております。
お問い合わせ
コストダウンが利益に直結する術だと理解していても、なかなか前に進めることができない状況。そんな時は、newjiのコストダウン自動化機能で大きく利益貢献しよう!
(Β版非公開)