- お役立ち記事
- An integrated approach to quality assurance and procurement cost reduction promoted by the purchasing department
An integrated approach to quality assurance and procurement cost reduction promoted by the purchasing department
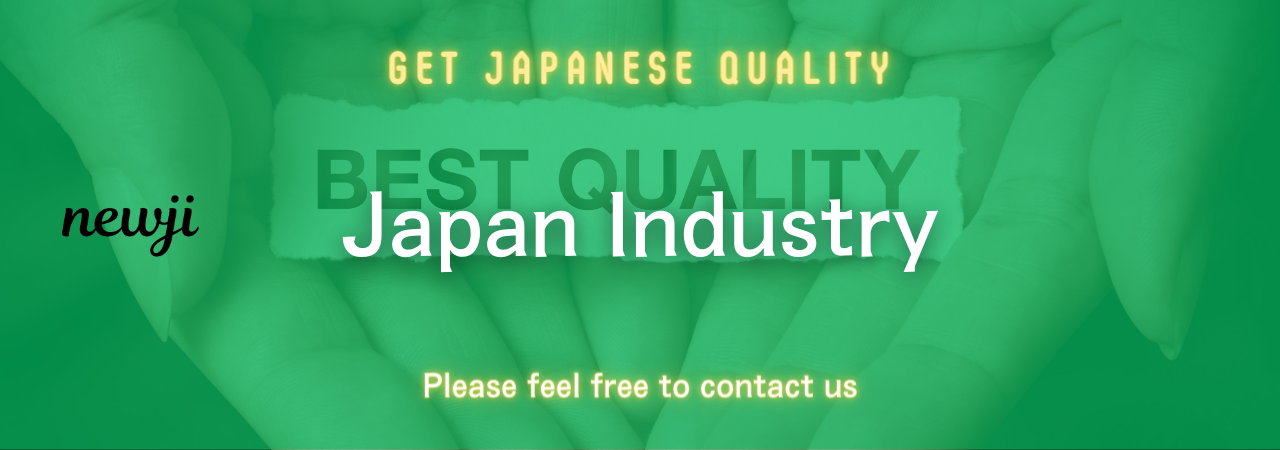
目次
Introduction to Quality Assurance and Procurement Cost Reduction
In today’s competitive business environment, companies are continuously seeking ways to enhance their operations while minimizing costs.
One effective strategy is implementing an integrated approach to quality assurance and procurement cost reduction.
This holistic method, primarily driven by the purchasing department, can lead to improved product quality, increased efficiencies, and substantial cost savings.
The Role of the Purchasing Department
The purchasing department plays a pivotal role in the integration of quality assurance and cost reduction strategies.
They are responsible for selecting suppliers, negotiating contracts, and ensuring the materials procured meet quality standards.
By focusing on these key areas, procurement professionals can significantly impact the overall cost structure of the company and the quality of its products or services.
Selecting Reliable Suppliers
A fundamental aspect of procurement is selecting suppliers who consistently provide quality materials at competitive prices.
The purchasing department must conduct thorough supplier evaluations, considering factors such as reliability, product quality, and financial stability.
By fostering strong relationships with trustworthy suppliers, the department can secure better prices and ensure a steady flow of high-quality materials.
Implementing Strategic Sourcing
Strategic sourcing involves analyzing an organization’s spending patterns and consolidating purchasing activities to leverage better pricing and contract terms.
The purchasing department should use data analytics tools to identify high-spend areas and potential cost-saving opportunities.
By consolidating orders and working with fewer suppliers, companies can benefit from volume discounts and reduced administrative costs.
Collaborating with Quality Assurance Teams
To effectively merge procurement cost reduction with quality assurance, collaboration between the purchasing and quality assurance teams is essential.
This partnership ensures that cost-saving measures do not compromise product quality.
Setting Quality Standards
Quality standards set by the quality assurance team must be communicated clearly to the purchasing department.
These standards should be integrated into supplier contracts and purchase orders, ensuring that suppliers are aware of and adhere to the required specifications.
This alignment helps maintain consistent product quality and reduces the risk of defects and returns.
Conducting Supplier Audits
Regular supplier audits are an effective way to monitor supplier compliance with quality standards.
The purchasing and quality assurance teams can collaborate to conduct these audits, identifying areas for improvement and ensuring that suppliers meet their contractual obligations.
This proactive approach can prevent quality issues that might arise from substandard materials, ultimately saving costs related to defects and repairs.
Adopting Lean Procurement Practices
Lean procurement focuses on eliminating waste and inefficiencies in the procurement process, directly contributing to cost reductions without compromising quality.
Optimizing Inventory Management
Effective inventory management is crucial for minimizing procurement costs.
By adopting just-in-time (JIT) inventory practices, companies can reduce excess stock and associated carrying costs.
The purchasing department should work closely with suppliers to ensure timely delivery of materials, preventing overstocking and minimizing waste.
Standardizing Purchase Orders
Standardizing purchase orders across the organization simplifies the procurement process and reduces administrative costs.
The purchasing department can develop templates and automated systems for purchase orders, making it easier to implement consistent procedures and track spending effectively.
This standardization can lead to improved accuracy and faster processing times.
Leveraging Technology in Procurement
Technology plays an integral role in facilitating an integrated approach to quality assurance and procurement cost reduction.
Utilizing E-Procurement Solutions
E-procurement platforms streamline the purchasing process, providing a centralized system for managing supplier relationships, contracts, and purchase orders.
These solutions allow the purchasing department to automate routine tasks, such as order processing and invoicing, freeing up time to focus on strategic initiatives.
E-procurement also provides real-time data analytics, aiding decision-making and identifying cost-saving opportunities.
Implementing Supplier Relationship Management Systems
Supplier relationship management (SRM) systems enable companies to build stronger relationships with their suppliers.
These systems facilitate communication, performance tracking, and collaboration, ensuring suppliers meet quality and delivery standards.
By leveraging SRM, the purchasing department can drive improvements in supplier performance, leading to cost reductions and enhanced product quality.
Conclusion: The Benefits of Integrated Quality Assurance and Procurement Cost Reduction
An integrated approach to quality assurance and procurement cost reduction, championed by the purchasing department, offers numerous benefits.
This strategy leads to improved product quality, increased efficiencies, and significant cost savings.
By selecting reliable suppliers, collaborating with quality assurance teams, adopting lean procurement practices, and leveraging technology, companies can achieve their quality and cost objectives effectively.
In an increasingly competitive market, this holistic approach not only enhances the organization’s performance but also strengthens its position within the industry.
資料ダウンロード
QCD調達購買管理クラウド「newji」は、調達購買部門で必要なQCD管理全てを備えた、現場特化型兼クラウド型の今世紀最高の購買管理システムとなります。
ユーザー登録
調達購買業務の効率化だけでなく、システムを導入することで、コスト削減や製品・資材のステータス可視化のほか、属人化していた購買情報の共有化による内部不正防止や統制にも役立ちます。
NEWJI DX
製造業に特化したデジタルトランスフォーメーション(DX)の実現を目指す請負開発型のコンサルティングサービスです。AI、iPaaS、および先端の技術を駆使して、製造プロセスの効率化、業務効率化、チームワーク強化、コスト削減、品質向上を実現します。このサービスは、製造業の課題を深く理解し、それに対する最適なデジタルソリューションを提供することで、企業が持続的な成長とイノベーションを達成できるようサポートします。
オンライン講座
製造業、主に購買・調達部門にお勤めの方々に向けた情報を配信しております。
新任の方やベテランの方、管理職を対象とした幅広いコンテンツをご用意しております。
お問い合わせ
コストダウンが利益に直結する術だと理解していても、なかなか前に進めることができない状況。そんな時は、newjiのコストダウン自動化機能で大きく利益貢献しよう!
(Β版非公開)